मशीनों द्वारा मृदा संघनन की प्रक्रिया का भौतिक आधार। मिट्टी की सतह संघनन की भौतिक विधियाँ
दोलन के आयाम और आवृत्ति का प्रभाव
कणों की कंपन आवृत्ति और उनके आयाम परस्पर जुड़े हुए हैं, जो औद्योगिक परिस्थितियों में विभिन्न स्थिरताओं के मिश्रण के लिए विभिन्न कंपन मोड का उपयोग करना संभव बनाता है। मोटे दाने वाले समग्र अंश वाले मिश्रण अपेक्षाकृत कम आवृत्ति (3000-6000 कंपन प्रति मिनट) पर कंपन करते हैं, लेकिन काफी बड़े आयाम के साथ, जबकि बारीक दाने वाले मिश्रण को कंपन करते समय, उच्च आवृत्ति कंपन का उपयोग किया जाता है - प्रति 20,000 कंपन तक मिनट, लेकिन कम आयाम के साथ।
कंक्रीट संघनन विकल्पों की योजना: ए) डीप वाइब्रेटर; बी) गहरे वाइब्रेटर का एक पैकेज; ग) लचीले शाफ्ट वाला वाइब्रेटर; घ) सतह थरथानेवाला; ई) बाहरी वाइब्रेटर; च) संघनन के समय के आधार पर कंक्रीट की ताकत में परिवर्तन।
आयाम और आवृत्ति जैसे कंपन तंत्र के ऐसे ऑपरेटिंग मापदंडों के अलावा, कंपन के परिणामस्वरूप संघनन की गुणवत्ता भी प्रक्रिया की अवधि से प्रभावित होती है। सभी प्रकार के कंक्रीट मिश्रणों के लिए, उनकी तरलता के आधार पर, कंपन संघनन के लिए एक इष्टतम समय होता है, जिसके दौरान मिश्रण प्रभावी ढंग से संकुचित होता है और जिसके बाद ऊर्जा लागत आगे संघनन की प्रभावशीलता के अनुपात में नहीं होती है। चूंकि इस समय के बाद भी संघनन जारी रहता है, इसलिए घनत्व में कोई वृद्धि आम तौर पर नहीं देखी जाती है। इसके अलावा, एक जोखिम है कि कंक्रीट मिश्रण उनके गुणों के आधार पर अलग-अलग घटकों में अलग होना शुरू हो जाएगा - उदाहरण के लिए, मोटे समुच्चय अंश और सीमेंट मोर्टार। परिणामस्वरूप, इसके भागों के कुछ हिस्सों में घनत्व के असमान वितरण और कम ताकत के कारण अंतिम कंक्रीट उत्पाद की गुणवत्ता कम हो जाएगी।
दीर्घकालिक कंपन आर्थिक रूप से लाभहीन है, क्योंकि यह उच्च ऊर्जा लागत और पूरी प्रक्रिया की श्रम तीव्रता से जुड़ा है, जिसके कारण मोल्डिंग लाइन की उत्पादकता काफी कम हो जाती है।
कंपन कम्पेक्टर के मजबूर कंपन की आवृत्ति के साथ समाधान कणों के प्राकृतिक कंपन की आवृत्ति के संयोग से संघनन दक्षता पर सकारात्मक प्रभाव पड़ता है। लेकिन यहां आपको इस तथ्य को ध्यान में रखना होगा कि मिश्रण विभिन्न कण आकारों के साथ विभिन्न अंशों का संयोजन है - सीमेंट मोर्टार के लिए माइक्रोमीटर से लेकर मोटे कंक्रीट समुच्चय के लिए कई सेंटीमीटर तक। तदनुसार, सबसे प्रभावी संघनन तकनीक विभिन्न आवृत्तियों का उपयोग होगी - तथाकथित पॉलीफ़्रीक्वेंसी संघनन, क्योंकि विभिन्न आकार और द्रव्यमान के कणों के लिए कंपन की प्राकृतिक आवृत्ति अलग-अलग होगी।
तकनीकी और आर्थिक मूल्यांकन करते समय, उपरोक्त को ध्यान में रखना आवश्यक है - बढ़ती संघनन ऊर्जा के साथ, संघनन दक्षता बढ़ती है, जिससे प्रक्रिया की अवधि भी कम हो जाती है और लाभप्रदता बढ़ जाती है।
कंपन मशीनें और कंपन प्लेटफार्म
कंक्रीट मोर्टार का कंपन संघनन स्थिर और पोर्टेबल दोनों साधनों का उपयोग करके किया जाता है। प्रीकास्ट कंक्रीट के लिए संघनन तकनीक में पोर्टेबल साधनों का उपयोग काफी सीमित है। उनका औद्योगिक उपयोग मुख्य रूप से बड़े, भारी उत्पादों की बेंच मोल्डिंग तक ही सीमित है।
कंपन प्लेटफार्मों का उपयोग उन प्रकार के संयंत्रों में पूर्वनिर्मित प्रबलित कंक्रीट के कारखाने के उत्पादन में किया जाता है जो कन्वेयर और प्रवाह-इकाई योजनाओं पर काम करते हैं। कंपन प्लेटफार्मों की डिज़ाइन सुविधाओं और प्रकारों की एक विस्तृत विविधता है - विद्युत चुम्बकीय, विद्युत यांत्रिक, वायवीय। कंपन की प्रकृति टक्कर, हार्मोनिक, संयुक्त है। कम्पनों का आकार गोलाकार, दिशात्मक, क्षैतिज, ऊर्ध्वाधर होता है। तालिका की डिज़ाइन योजनाओं के अनुसार, एक ठोस ऊपरी फ्रेम होता है जो एक या अधिक कंपन शाफ्ट के साथ एक तालिका बनाता है या अलग-अलग कंपन ब्लॉकों से इकट्ठा किया जाता है, जो सामान्य रूप से एक कंपन सतह का प्रतिनिधित्व करता है, जिस पर एक मिश्रण स्थित होता है। समाधान के साथ फॉर्म को मजबूती से सुरक्षित करने के लिए, प्लेटफ़ॉर्म टेबल पर वायवीय इलेक्ट्रोमैग्नेट या मैकेनिकल क्लैंप प्रदान किए जाते हैं।
आयामों के साथ कंपन तालिका आरेख
कंपन मंच एक सपाट मेज के रूप में बनाया गया है, जो बिस्तर (फ्रेम) पर या स्थिर समर्थन पर स्प्रिंग समर्थन द्वारा समर्थित है। स्प्रिंग्स का उद्देश्य टेबल की दोलन संबंधी गतिविधियों को कम करना है, इस प्रकार उन्हें समर्थन को प्रभावित करने से रोकना है, जो अनिवार्य रूप से विनाश का कारण बनेगा। निचले हिस्से में, इसकी सतह पर स्थित एक्सेन्ट्रिक्स के साथ एक कंपन शाफ्ट डिवाइस से जुड़ा हुआ है। शाफ्ट एक इलेक्ट्रिक मोटर द्वारा संचालित होता है, एक्सेन्ट्रिक्स की गति से टेबल में कंपन होता है, जो फिर कंक्रीट के द्रव्यमान में संचारित होता है और कंक्रीट मिश्रण के संघनन का कारण बनता है। एक कंपन प्लेटफ़ॉर्म की शक्ति को उसकी भार क्षमता से मापा जाता है - फॉर्म के साथ कंक्रीट उत्पाद का द्रव्यमान - और 2 से 30 टन तक होता है।
प्रीकास्ट प्रबलित कंक्रीट का उत्पादन करने वाली फैक्ट्रियां आमतौर पर 0.3-0.6 मिमी के कंपन आयाम और 3000 कंपन प्रति मिनट की आवृत्ति के साथ मानकीकृत कंपन प्लेटफार्मों से सुसज्जित होती हैं। ऐसे प्लेटफ़ॉर्म 18 मीटर तक की लंबाई और 3.5 मीटर तक की चौड़ाई वाली संरचनाओं के लिए संघनन का अच्छी तरह से सामना करते हैं।
कंपन प्लेटफार्मों पर उत्पाद बनाते समय, खासकर यदि कठोर, छिद्रपूर्ण समुच्चय का उपयोग किया जाता है, तो वजन का उपयोग आमतौर पर कंक्रीट की संरचना में सुधार के लिए किया जाता है।
यदि किसी निश्चित साँचे का उपयोग करके उत्पाद बनाना आवश्यक है, तो कंक्रीट मिश्रण को साँचे से जुड़े सतह, गहरे और लगे हुए वाइब्रेटर का उपयोग करके संकुचित किया जाता है। क्षैतिज रूपों का उपयोग करके उत्पादों का निर्माण करते समय, कठोर कंक्रीट मिश्रण या कम तरलता वाले मिश्रण का उपयोग किया जाता है; ऊर्ध्वाधर रूपों (कैसेट) में - उच्च तरलता और 80-100 मिमी के शंकु ड्राफ्ट के साथ मिश्रण।
दबाने की प्रक्रिया
प्रबलित कंक्रीट उत्पादों के निर्माण में संघनन की एक विधि के रूप में दबाने का उपयोग शायद ही कभी किया जाता है, इस तथ्य के बावजूद कि तकनीकी संकेतों के अनुसार यह बहुत प्रभावी है, क्योंकि यह बहुत कम सीमेंट खपत (100) के साथ उच्च घनत्व के साथ उच्च शक्ति कंक्रीट प्राप्त करने की अनुमति देता है। -150 किग्रा/मीटर 3 कंक्रीट)। इस पद्धति के प्रसार को रोकने वाले कारण पूर्णतः आर्थिक प्रकृति के हैं। जिस दबाव पर कंक्रीट को प्रभावी ढंग से संकुचित किया जाता है वह 10-15 एमपीए या उससे अधिक होता है, अर्थात, कंक्रीट उत्पाद को संकुचित करने के लिए, प्रत्येक 1 एम2 के लिए 10-15 एमएन (मिलियन न्यूटन) का बल लगाया जाना चाहिए। ऐसी शक्ति वाले प्रेस का उपयोग केवल जहाज निर्माण में जहाज के पतवारों को दबाने के लिए किया जाता है, और उनकी लागत इतनी अधिक होती है कि यह उपयोग की आर्थिक लाभप्रदता को पूरी तरह से बाहर कर देती है।
केन्द्रापसारण
सेंट्रीफ्यूजेशन के दौरान, घूमने वाला मिश्रण साँचे की आंतरिक सतह के संपर्क के कारण संकुचित हो जाता है। सेंट्रीफ्यूजेशन प्रक्रिया के परिणामस्वरूप, कंक्रीट घोल के घटकों और उसमें मौजूद पानी के अलग-अलग घनत्व के कारण, इसमें से 20-30% तक तरल निकाल दिया जाता है, जिसके परिणामस्वरूप उच्च शक्ति वाला कंक्रीट बनता है।
सेंट्रीफ्यूजेशन से उच्च घनत्व, मजबूती (40-60 एमपीए) और स्थायित्व वाले कंक्रीट उत्पाद प्राप्त करना आसान हो जाता है। इस विधि में काफी मात्रा में सीमेंट की आवश्यकता होती है ताकि अंतिम कंक्रीट मिश्रण में उच्च सामंजस्य (400-450 किग्रा/एम3) हो। अन्यथा, केन्द्रापसारक बल के प्रभाव में, कई परतों में अलगाव हो जाएगा, क्योंकि बड़े आकार और द्रव्यमान के अनाज छोटे आकार के अनाज की तुलना में अपकेंद्रित्र मोल्ड के किनारे पर अधिक दबाव डालेंगे। इस तकनीक का उपयोग करके लैंप, पावर लाइन सपोर्ट या पाइप के लिए स्टैंड बनाए जाते हैं।
समाधान की निकासी
वैक्यूम विधि का उपयोग करते समय, 0.07-0.08 एमपीए के दबाव में हवा का एक वैक्यूम बनाया जाता है, जिसके कारण समाधान में शामिल अतिरिक्त हवा और दबाव अंतर के प्रभाव में अतिरिक्त पानी हटा दिया जाता है। इससे खाली हुई जगह को कंक्रीट घेर लेता है, जिससे मिश्रण का घनत्व बढ़ जाता है। निर्वात की उपस्थिति का कंक्रीट द्रव्यमान पर भी दबाव प्रभाव पड़ता है; इस प्रभाव का परिमाण निर्वात दबाव और वायुमंडलीय दबाव के बीच के अंतर के बराबर है। इस प्रभाव के कारण, मिश्रण और अधिक सघन हो जाता है।
वैक्यूमिंग और कंपन का संयोजन
वे वैक्यूम प्रक्रिया को कंपन के साथ जोड़ना पसंद करते हैं। निर्वात के अधीन कंक्रीट घोल के कंपन के दौरान, मिश्रण के ठोस घटक हवा के बुलबुले और पानी की बूंदों के स्थान पर बने छिद्रों को तीव्रता से भर देते हैं। हालाँकि, तकनीकी पहलू में, वैक्यूमिंग का एक महत्वपूर्ण तकनीकी और आर्थिक नुकसान है - प्रक्रिया की लंबी अवधि, जो कट के आकार के आधार पर, प्रत्येक 1 सेमी मोटाई के लिए लगभग 1-2 मिनट लेती है।
जिस परत को वैक्यूम किया जा सकता है उसकी मोटाई 12-15 सेमी से अधिक नहीं होती है। इस कारण से, बड़ी संरचनाओं को मुख्य रूप से उनकी सतह परत को अधिक घनत्व देने के लिए वैक्यूम किया जाता है।
कोवर्ग:
मृदा संघनन मशीनें
मशीनों द्वारा मृदा संघनन की प्रक्रिया का भौतिक आधार
मिट्टी का संघनन सड़कों, रेलवे, बांधों आदि के निर्माण की तकनीकी प्रक्रिया के सबसे महत्वपूर्ण तत्वों में से एक है। उनकी आगे की सेवा इस प्रक्रिया की गुणवत्ता पर निर्भर करती है। पर्याप्त स्थिरता प्राप्त करने के लिए, इनमें से प्रत्येक संरचना के लिए उनकी मिट्टी के घनत्व की आवश्यकताएं स्थापित की जाती हैं। साथ ही, संघनन की डिग्री का आकलन करने का आधार मानक संघनन विधि है, और इसलिए मिट्टी के घनत्व की आवश्यकताओं को आमतौर पर संघनन गुणांक के रूप में व्यक्त किया जाता है, अर्थात, अधिकतम मानक घनत्व (बीएमएक्स) के अंशों में। राजमार्ग उपनगरों की ऊपरी मिट्टी की परतों के लिए, घनत्व की आवश्यकताएं अधिक हैं - यहां मिट्टी का घनत्व (0.98-1.0) btah से कम नहीं होना चाहिए। तटबंधों की निचली परतों के लिए इसे घटाकर अधिकतम 0.956 किया जा सकता है। रेलवे तटबंधों की मिट्टी का घनत्व, तटबंधों में विचाराधीन परत के स्थान के आधार पर, (0.90h-0.98) 6 हेक्टेयर की सीमा के भीतर होना चाहिए, और बांध की मिट्टी का घनत्व प्रत्येक विशिष्ट मामले में स्थापित किया जाता है। यह ध्यान दिया जाना चाहिए कि (0.98h-1.0)bmax जैसे उच्च घनत्व को प्राप्त करना महत्वपूर्ण कठिनाइयों से जुड़ा है और इसे केवल उपयोग की जाने वाली मशीनों के मापदंडों और उनके ऑपरेटिंग मोड दोनों के सही विकल्प के साथ ही प्राप्त किया जा सकता है। मिट्टी का संघनन केवल इस उद्देश्य के लिए डिज़ाइन की गई विशेष मशीनों से ही किया जाना चाहिए। इसके लिए अर्थमूविंग और परिवहन मशीनों का उपयोग करने और इस प्रक्रिया को तटबंधों को हटाने के साथ संयोजित करने के प्रयास से पता चला कि मिट्टी का घनत्व अपर्याप्त है और संघनन असमान है और इसलिए यह विधि केवल प्रारंभिक मिट्टी संघनन के लिए काम कर सकती है, जो निश्चित रूप से सुविधा प्रदान करती है। मुख्य मशीनों का कार्य.
संघनन के दौरान मिट्टी की नमी का बहुत महत्व है। मिट्टी पर कार्य करने वाले प्रत्येक भार की अपनी इष्टतम आर्द्रता होती है, जिस पर न्यूनतम मात्रा में यांत्रिक कार्य के साथ आवश्यक घनत्व प्राप्त किया जा सकता है। अपर्याप्त आर्द्रता के मामले में, आवश्यक घनत्व प्राप्त करने के लिए, कई उपायों को लागू करना आवश्यक है, जिसमें, उदाहरण के लिए, संकुचित परत की मोटाई को कम करना शामिल है। यह ध्यान दिया जाना चाहिए कि बहुत शुष्क मिट्टी को आम तौर पर आवश्यक घनत्व में नहीं लाया जा सकता है। इष्टतम मिट्टी की नमी W0, जो मानक संघनन विधि द्वारा निर्धारित की जाती है, औसत मशीनों के संचालन से मेल खाती है।
मिट्टी को रोलिंग, कॉम्पेक्टिंग, कंपन और वाइब्रोटेम्पिंग द्वारा संकुचित किया जाता है।
लुढ़कते समय एक ड्रम या पहिया जमीन पर लुढ़कता है, जिसके जमीन के संपर्क में आने वाली सतह पर कुछ विशिष्ट दबाव (तनाव) पड़ता है, जिससे मिट्टी में अपरिवर्तनीय विकृति विकसित हो जाती है। सभी रोलर्स का कार्य इसी सिद्धांत पर आधारित है। संघनन करते समय, मिट्टी एक गिरते हुए द्रव्यमान द्वारा संकुचित होती है, जिसे पहले एक निश्चित ऊंचाई तक उठाया जाता था और मिट्टी की सतह से मिलने के समय इसकी एक निश्चित गति होती है। इस प्रकार, संघनन जमीन पर मशीन के काम करने वाले हिस्से के प्रभाव से जुड़ा हुआ है। कंपन करते समय, संकुचित द्रव्यमान या तो संकुचित परत की सतह (सतह वाइब्रेटर) पर होता है या उसके अंदर (गहराई वाइब्रेटर) होता है। एक विशेष तंत्र के परिणामस्वरूप, इसे दोलन गति की स्थिति में लाया जाता है। इस द्रव्यमान की गतिज ऊर्जा का एक हिस्सा मिट्टी के कंपन पर खर्च होता है, जो इसके कणों के सापेक्ष विस्थापन का कारण बनता है, जिससे उनकी सघन पैकिंग प्राप्त होती है। कंपन करने पर, सघन सतह से द्रव्यमान का पृथक्करण नहीं होता है या यह बहुत ही नगण्य होता है। यदि द्रव्यमान की गड़बड़ी एक निश्चित सीमा से अधिक हो जाती है, तो यह जमीन की सतह से अलग हो जाएगा, जिससे द्रव्यमान का जमीन पर बार-बार प्रभाव पड़ेगा। इस स्थिति में, कंपन कंपन रैमिंग में बदल जाएगा। यह प्रक्रिया संघनन से प्रभावों की उच्च आवृत्ति में भिन्न होती है। द्रव्यमान के गिरने की कम ऊंचाई के बावजूद, गति की बढ़ती गति के कारण, प्रभाव ऊर्जा महत्वपूर्ण हो सकती है।
सभी मामलों में, मशीन के कामकाजी भागों की मिट्टी पर प्रभाव उस पर चक्रीय भार के अनुप्रयोग से जुड़ा होता है।
यह माना जाता है कि मिट्टी में नमी की मात्रा इष्टतम है।
मिट्टी को संकुचित करने वाली मशीनों के कामकाजी भागों की संपर्क सतहों पर विशिष्ट दबाव उनकी ताकत सीमा से अधिक नहीं होना चाहिए, लेकिन साथ ही वे कम भी नहीं होने चाहिए, अन्यथा संघनन प्रभाव कम हो जाता है। सबसे अच्छा प्रभाव उन मामलों में प्राप्त होगा जहां संघनन मशीनों के कामकाजी निकायों के साथ संपर्क की सतह पर विशिष्ट दबाव (0.9-टी-1.0) एपी (एपी तन्य शक्ति है) के बराबर है। इस नियम का अपवाद ऐसी मशीनें हैं जिनके काम करने वाले हिस्से सघन मिट्टी की परत (कैम और जाली रोलर्स) में उनकी गहरी पैठ के आधार पर काम करते हैं।
विरूपण, और इसलिए संघनन प्रभाव, तनाव की स्थिति में परिवर्तन की दर और भार की अवधि, और इसलिए इसके अनुप्रयोग की पुनरावृत्ति की संख्या दोनों पर निर्भर करता है।
जमीन के साथ मशीनों के काम करने वाले हिस्सों की परस्पर क्रिया की प्रकृति ऐसी है कि इसे कठोर गोल मोहर के साथ मिट्टी के आधे स्थान को लोड करने की योजना तक कम किया जा सकता है
मृदा संघनन मशीनों का प्रभाव इस बात पर निर्भर करता है कि संकुचित परत की मोटाई कितनी सही ढंग से चुनी गई है। यदि परत की मोटाई अत्यधिक बड़ी है, तो आवश्यक मिट्टी घनत्व प्राप्त नहीं हो पाता है। यदि परत की मोटाई बहुत छोटी है, तो मशीन की उत्पादकता कम हो जाती है और काम की लागत बढ़ जाती है।
प्रोफेसर एन.एन. इवानोव ने सैद्धांतिक रूप से स्थापित किया कि अधिकतम गहराई जिस पर भार अभी भी लागू होता है वह 3.5 डीजीएसएच (स्टांप का व्यास) है। बाद में, इस निष्कर्ष को प्रायोगिक पुष्टि मिली। इस क्षेत्र के भीतर, जो अभी भी भार के अधीन है, किसी को एक ऐसे क्षेत्र को भी अलग करना चाहिए, जहां मिट्टी के संघनन के दौरान, गहराई में विरूपण कमोबेश समान रूप से वितरित होता है। इस क्षेत्र को सक्रिय कहा जा सकता है, और इसकी गहराई - सक्रिय क्षेत्र की गहराई। इस तरह के क्षेत्र का निर्माण मिट्टी के कणों और समुच्चय के बड़े पैमाने पर प्लास्टिक बदलाव से होता है जो मिट्टी की पूरी मात्रा में विकसित होते हैं, साथ ही इस तथ्य से भी कि संकुचित परत अधिक कठोर आधार पर स्थित होती है, जो पहले से संकुचित मिट्टी है . एक कठोर आधार की उपस्थिति संकेंद्रित भार की धुरी के साथ संपीड़ित तनावों की एकाग्रता की ओर ले जाती है, साथ ही गहराई के साथ तनावों में कम अंतर, यानी उनके बराबर होने की ओर ले जाती है।
असंबद्ध मिट्टी के मामले में, सक्रिय क्षेत्र की गहराई 1.2-1.5 गुना अधिक है।
कुल मिट्टी विरूपण का लगभग 80% सक्रिय क्षेत्र के भीतर होता है, और इसका केवल 20% इस क्षेत्र के बाहर स्थित मिट्टी की मात्रा में होता है। इसलिए, सघन मिट्टी की परत की मोटाई सक्रिय क्षेत्र की गहराई से अधिक नहीं हो सकती, अन्यथा आवश्यक मिट्टी का घनत्व प्राप्त नहीं किया जा सकेगा।
संकुचित मिट्टी की परत की इष्टतम मोटाई सक्रिय क्षेत्र की गहराई से निकटता से संबंधित है। इष्टतम से तात्पर्य उस मोटाई से है जिस पर कम से कम यांत्रिक कार्य और उच्चतम मशीन उत्पादकता के साथ संघनन की आवश्यक डिग्री हासिल की जाती है। सक्रिय क्षेत्र की गहराई सघन मिट्टी की परतों की इष्टतम मोटाई की ऊपरी सीमा निर्धारित करती है। ऐसे मामलों में, जहां मिट्टी के संघनन के दौरान, आवश्यक घनत्व 0.956mach से अधिक नहीं होता है, इष्टतम परत की मोटाई सक्रिय क्षेत्र की गहराई के बराबर ली जा सकती है। इसके अलावा, ऐसा घनत्व अपेक्षाकृत आसानी से प्राप्त किया जाता है और इसके लिए बड़ी संख्या में मशीन पास की आवश्यकता नहीं होती है।
योजना में मशीन के कामकाजी निकाय का न्यूनतम आकार मिट्टी की परत की इष्टतम मोटाई का अधिकतम मूल्य निर्धारित करता है, यानी, संभावित संघनन क्षमताएं, जो, हालांकि, केवल तभी महसूस की जा सकती हैं जब मिट्टी पर तनाव हो सतह तन्य शक्ति के करीब है. कम तनाव मूल्यों पर, इष्टतम परत की मोटाई कम हो जाएगी।
यदि आवश्यक मिट्टी का घनत्व अधिक है और इसकी मात्रा (0.98-7-1.0) 8max है, तो इष्टतम परत की मोटाई सक्रिय क्षेत्र की आधी गहराई (H0 = 0.5ftn) के बराबर है। यह घनत्व सक्रिय क्षेत्र की गहराई के बराबर परत की मोटाई के साथ प्राप्त किया जा सकता है, लेकिन इस मामले में आवश्यक घनत्व 0.95 btah होने पर मामले की तुलना में पास की संख्या 3 गुना बढ़नी चाहिए। इसलिए, इतनी बड़ी परत मोटाई के साथ मिट्टी का संघनन आर्थिक रूप से लाभहीन हो जाता है।
कार्यशील निकाय के समान आयामों और मिट्टी की सतह पर विकसित होने वाले तनाव के समान परिमाण को बनाए रखते हुए, इष्टतम मूल्य की तुलना में संकुचित मिट्टी की परत की मोटाई को कम करना, एक नियम के रूप में, विशिष्ट कार्य के अत्यधिक व्यय को शामिल करता है, अर्थात, मिट्टी की इकाई मात्रा को संकुचित करने के लिए आवश्यक कार्य।
सूत्र (IV. 1) के विश्लेषण से पता चलता है कि तनाव में (0.5-7-0.6) ऑप की कमी का व्यावहारिक रूप से सक्रिय क्षेत्र की गहराई पर कोई प्रभाव नहीं पड़ता है, और परिणामस्वरूप, संकुचित परत की इष्टतम मोटाई पर। साथ ही, यह ध्यान दिया जाना चाहिए कि तनाव में किसी भी कमी से लोड अनुप्रयोग की पुनरावृत्ति की आवश्यक संख्या में वृद्धि होती है।
संघनन के परिणामस्वरूप न केवल आवश्यक मिट्टी का घनत्व प्राप्त होना चाहिए, बल्कि इसकी मजबूत संरचना भी प्राप्त होनी चाहिए। यह केवल तभी हासिल किया जा सकता है जब एक निश्चित ऑपरेटिंग मोड का पालन किया जाए। सबसे पहले, यह विशिष्ट दबाव से संबंधित है, जो मिट्टी की ताकत की सीमा के करीब होना चाहिए, लेकिन बाद वाले से अधिक नहीं होना चाहिए, न केवल संघनन के अंत में, बल्कि पूरी प्रक्रिया के दौरान। यदि आप इस नियम को तोड़ते हैं और तुरंत उस दबाव का चयन करते हैं जो केवल संघनन प्रक्रिया के अंत में होना चाहिए, जब मिट्टी पहले से ही घनी और मजबूत हो, तो पहले पास के दौरान संरचना नष्ट हो जाएगी, खासकर सतह के पास। इससे घनी और मजबूत संरचना बनाना मुश्किल हो जाएगा, और अंततः प्राप्त घनत्व और ताकत विशिष्ट दबाव में क्रमिक वृद्धि के साथ प्राप्त घनत्व और ताकत से कम होगी। उदाहरण के लिए, संरचना का विनाश, रोलर या रोलर पहियों के सामने मजबूत लहर गठन के साथ-साथ किनारे से मिट्टी के उभार से प्रमाणित होता है।
इस प्रकार, हम कह सकते हैं कि मशीन के कामकाजी हिस्से का विशिष्ट दबाव धीरे-धीरे रोलर्स के मामले में पास-दर-पास या टैंपिंग मशीनों के मामले में झटका दर झटका तक बढ़ना चाहिए। रोलिंग के दौरान रट की गहराई और संघनन के दौरान प्रभाव के समय को धीरे-धीरे कम करके विशिष्ट दबाव बढ़ाने की यह प्रक्रिया कुछ हद तक स्वचालित रूप से की जाती है। इस मामले में, विशिष्ट दबाव 1.5-2 गुना बढ़ जाता है, और यह आवश्यक है कि वे 3-4 गुना अधिक हो जाएं। इसलिए, मिट्टी का संघनन दो मशीनों - हल्की और भारी - का उपयोग करके किया जाना चाहिए। प्रारंभिक संघनन के लिए एक हल्की मशीन का उपयोग किया जाना चाहिए, और अंततः मिट्टी को आवश्यक घनत्व में लाने के लिए एक भारी मशीन का उपयोग किया जाना चाहिए। पूर्व-संघनन के उपयोग से प्रति स्थान आवश्यक पासों या प्रभावों की कुल संख्या लगभग 25% कम हो जाती है। यदि हम यह भी ध्यान में रखें कि प्रक्रिया की शुरुआत में हल्के साधनों का उपयोग किया जाता है, तो इस सबके परिणामस्वरूप संघनन कार्य की कुल लागत का 30% तक की बचत होती है।
भारी मशीन से संघनन पर स्विच करने से मिट्टी की सतह पर तनाव में तेज वृद्धि नहीं होनी चाहिए। इसलिए, सबसे अच्छा प्रभाव तब प्राप्त होता है जब किसी भारी मशीन के पहले प्रभाव के दौरान सतह पर तनाव एक हल्की मशीन के अंतिम प्रभाव के अनुरूप तनाव के बराबर होता है। वायवीय टायरों पर रोलर्स के साथ रोल करते समय, यह आवश्यकता उस स्थिति में पूरी होती है जब प्रारंभिक संघनन एक रोलर द्वारा किया जाता है, जिसके प्रत्येक पहिये पर भार मुख्य संघनन की तुलना में 2 गुना कम होता है, और टायर का दबाव 1.5- कम हो जाता है। 2 बार। टैंपिंग मशीनों के साथ, प्रारंभिक संघनन एक ऐसी मशीन के साथ किया जा सकता है जिसके काम करने वाले तत्व का वजन आधा होता है, या उसी मशीन के साथ जो मुख्य संघनन करती है, लेकिन काम करने वाले तत्व की ड्रॉप ऊंचाई में 4 गुना कमी के साथ। पूर्व-संघनन के दौरान, पासों की कुल आवश्यक संख्या का 30-40% पूरा किया जाना चाहिए।
यदि तटबंध के निर्माण के दौरान मिट्टी को अर्थमूविंग या अर्थमूविंग मशीनों द्वारा कम से कम 0.906 हेक्टेयर के घनत्व तक संकुचित किया गया था, तो प्रारंभिक संघनन का उपयोग नहीं किया जा सकता है, जो उदाहरण के लिए, स्क्रैपर कार्य के दौरान होता है।
रोल करते समय, रोलर्स की गति पर एक निश्चित प्रभाव पड़ता है। अलग-अलग गति पर, इष्टतम मिट्टी का घनत्व व्यावहारिक रूप से समान संख्या में पासों में प्राप्त किया जाता है। इस निष्कर्ष की पुष्टि प्रत्यक्ष परीक्षणों से होती है और यह मिट्टी के रियोलॉजिकल गुणों से प्राप्त होता है। इस प्रकार, पैराग्राफ 2 में यह दिखाया गया कि तनाव की स्थिति में परिवर्तन की दर व्यावहारिक रूप से केवल कुछ मूल्यों तक अपरिवर्तनीय विरूपण की मात्रा को प्रभावित करती है। रोलिंग के दौरान जो गति होती है वह पहले से ही उनके प्रभाव क्षेत्र से बाहर होती है।
उसी समय, यह पाया गया कि उच्च गति गति पर, एक कम मजबूत मिट्टी की संरचना बनती है, जिसे मिट्टी पर कार्य करने वाले थोड़े अधिक कतरनी बलों द्वारा समझाया जाता है। किए गए शोध से रोलिंग के लिए एक तर्कसंगत गति व्यवस्था विकसित करना संभव हो गया, जिसमें संघनन की गुणवत्ता न केवल कम होती है, बल्कि थोड़ी बढ़ भी जाती है। इस मोड में, पहला पास और आखिरी दो पास कम गति (1.5-2.5 किमी/घंटा) पर किए जाने चाहिए, और सभी मध्यवर्ती पास उच्च गति (8-10 किमी/घंटा) पर होने चाहिए। इस विधा से उत्पादकता लगभग 2 गुना बढ़ जाती है। रोलर्स के डिज़ाइन को तर्कसंगत गति से मिट्टी के संघनन की अनुमति देनी चाहिए।
कोश्रेणी:- मृदा संघनन मशीनें
तटबंधों में, ट्रैक्टर के साथ मिलकर काम करने वाले विभिन्न प्रकार के रोलर्स का उपयोग करके मिट्टी को दबाया जाता है। वाइब्रेटरी टैंपिंग मशीनों का भी उपयोग किया जाता है, जो संकुचित होने वाली मिट्टी में बार-बार होने वाले दोलन संबंधी आंदोलनों को संचारित करती हैं, और प्लेट के रूप में काम करने वाली बॉडी वाली टैंपिंग मशीनें जो समय-समय पर विभिन्न ऊंचाइयों से मिट्टी पर गिरती हैं।
संघनन प्रक्रिया को दर्शाने वाले मुख्य पैरामीटर, उपयोग किए गए उपकरण और संघनन की जाने वाली मिट्टी के प्रकार के आधार पर, तालिका में दिए गए हैं। वि.5.
ट्रेल्ड रोलर्स का सबसे अधिक उपयोग किया जाता है, जिनमें से वायवीय रोलर्स सबसे प्रभावी होते हैं। मिट्टी का संघनन उसके भरने के क्रम में ही किया जाता है। तटबंध के पूरे क्षेत्र पर रोलर के क्रमिक गोलाकार प्रवेश द्वारा मिट्टी को संकुचित किया जाता है, और प्रत्येक प्रवेश को पिछले वाले को 0.2...0.3 मीटर तक ओवरलैप करना चाहिए। एक समय में पूरे क्षेत्र को रोल करने के बाद, आगे बढ़ें दूसरी पैठ
तटबंध के ढलान के पास मिट्टी को ढहने से रोकने के लिए, ढलान के साथ पहले दो प्रवेश किनारे से कम से कम 1.5 मीटर की दूरी पर किए जाते हैं। इसके बाद के छेदों को किनारे की ओर 0.5 मीटर स्थानांतरित कर दिया जाता है और इस प्रकार तटबंध के किनारों को घुमा दिया जाता है। चूंकि रोलिंग एक ट्रैक के साथ कई पासों में की जाती है, पास का पहला भाग कम गति पर किया जाता है, और दूसरा उच्च गति पर, क्योंकि जैसे-जैसे तटबंध का घनत्व बढ़ता है, रोलर की गति का प्रतिरोध कम हो जाता है उल्लेखनीय रूप से.
कॉम्पैक्टिंग मशीनों की प्रति घंटा उत्पादकता, एम2/घंटा:
जहां V औसत गति है, मी/घंटा; बी - एक पास में संकुचित परत की चौड़ाई, मी; ए-पिछले मार्ग की ओवरलैप पट्टी की चौड़ाई, मी; केवी - समय उपयोग कारक (0.8 - रोलर्स के लिए और 0.7 - अन्य मिट्टी कॉम्पैक्टिंग मशीनों के लिए); n एक ट्रैक पर गुजरने की संख्या है।
नींव या खाइयों के साइनस को भरते समय मिट्टी को जमाना सबसे कठिन काम है, क्योंकि काम तंग परिस्थितियों में किया जाता है। इन मामलों में, नींव से 0.8 मीटर की चौड़ाई तक की मिट्टी को वायवीय और इलेक्ट्रिक टैम्पर्स के साथ 15...20 सेमी की परतों में जमाया जाता है, और ऊपरी परतों को अधिक उत्पादक छोटे आकार के रोलर्स, स्व-चालित कंपन के साथ जमाया जाता है। प्लेटें, आदि (चित्र वी. 31)।
संघनन प्रक्रिया के दौरान, प्राप्त मिट्टी के घनत्व को नियंत्रित करना आवश्यक है। इन उद्देश्यों के लिए, खेत में, तटबंधों में रखे गए गड्ढों से 50...100 सेमी3 की मात्रा वाले एक सिलेंडर (रिंग) का उपयोग करके मिट्टी का घनत्व निर्धारित किया जाता है।
हालाँकि, यह नियंत्रण विधि बहुत श्रम-गहन है। सोयुजडोरनिया द्वारा डिज़ाइन किए गए घनत्व मीटर का भी उपयोग किया जाता है। इस उपकरण में एक छड़ होती है जिसके साथ एक भार फिसलता है, जो गिरने पर 1 सेमी2 (नरम मिट्टी के लिए - 2 सेमी2) के क्षेत्र के साथ एक टिप पर एक झटका (1 जे की ऊर्जा के साथ) देता है। टिप को 10 सेमी तक डुबाने के लिए आवश्यक प्रहारों की संख्या मिट्टी के घनत्व को दर्शाती है। गामा किरणों से मिट्टी को रोशन करने के लिए एक इंस्टॉलेशन का भी उपयोग किया जाता है। इस मामले में, दो पाइपों को एक निश्चित दूरी पर जमीन में डुबोया जाता है, जिनमें से एक में एक रेडियोधर्मी आइसोटोप रखा जाता है, और दूसरे में - एक क्वांटम विकिरण काउंटर जो विकिरण की तीव्रता को मापता है, जो मिट्टी के घनत्व पर निर्भर करता है। दोनों पाइपों को अलग करना।
रोलर्स के साथ मिट्टी का संघनन
स्व-चालित और ट्रैल्ड वायवीय रोलर्स का उपयोग करके रोलिंग की जाती है। संघनन बल रोलर के गुरुत्वाकर्षण और रोलिंग विमान (लाइन) पर गिट्टी भार (8 एमपीए तक) द्वारा बनाए गए उच्च संपर्क तनाव के कारण प्राप्त होता है।
वायवीय रोलर्स सिंगल-एक्सल (वजन 10 - 25 टन), टू-एक्सल ट्रैल्ड (वजन 50 टन तक) और सेमी-ट्रेलर (एक या दो-एक्सल वजन 100 टन तक) हो सकते हैं। हल्के रोलर्स के साथ, 20 - 30 सेमी की परत के साथ ढीली मिट्टी का आवश्यक संघनन 2.5 मीटर तक की कार्यशील चौड़ाई के साथ प्राप्त किया जाता है। 25 - 50 टन वजन वाले भारी ट्रेल्ड वायवीय रोलर्स 35 - 50 सेमी की परत के साथ मिट्टी का संघनन प्रदान करते हैं। 2.5 - 3.3 मीटर की कार्यशील चौड़ाई के साथ। अर्ध-ट्रेलर वायवीय रोलर्स का उपयोग सबसे प्रभावी है; वे 2.7 - 2.8 मीटर की कार्यशील चौड़ाई के साथ 40 - 50 सेमी की परत के साथ एकजुट और गैर-संबद्ध मिट्टी का उच्च गुणवत्ता वाला संघनन प्रदान करते हैं। उपरोक्त सभी संकेतक एक ट्रैक पर रोलर के 4-12 बार गुजरने पर (रोलर के वजन के आधार पर) प्राप्त होते हैं। दबाव वितरण के बड़े क्षेत्र के कारण ट्रैल्ड और स्व-चालित ड्रम रोलर्स कैम रोलर्स की तुलना में कम कुशल होते हैं।
सघन मिट्टी पर संपर्क दबाव बढ़ाने और उच्च प्रदर्शन प्राप्त करने के लिए पैड या जाली रोलर्स का उपयोग किया जाता है। कैम 200 - 300 मिमी लंबे स्टील प्रोफ़ाइल पिन हैं, जो ड्रम खोल की परिधि के चारों ओर वेल्डेड हैं। ऐसे रोलर्स का उपयोग केवल एकजुट मिट्टी को संकुचित करने के लिए किया जाता है। मोटे दाने वाली चट्टानों से मिट्टी जमा करते समय, कैम के बजाय, एक कोण या अन्य स्टील प्रोफ़ाइल से स्टील झंझरी को ड्रम की सतह पर वेल्ड किया जाता है। कैम और जाली रोलर्स ट्रैक के साथ 4 - 10 पासों में 2.7 - 3.3 मीटर की कामकाजी चौड़ाई के साथ 25 - 50 सेमी की परत के साथ मिट्टी का संघनन प्रदान करते हैं।
मिट्टी की प्रत्येक परत की रोलिंग, एक नियम के रूप में, सर्पिल-रिंग पैटर्न के अनुसार की जाती है। ग्रिपर की लंबाई 250 - 300 मीटर मानी जाती है। छोटी चौड़ाई (रोलर घुमाव कठिन होते हैं) के ग्रिपर पर मिट्टी को जमाते समय, स्व-चालित ड्रम रोलर्स का मुख्य रूप से उपयोग किया जाता है, जो एक प्रत्यागामी पैटर्न में चलते हैं।
61. मिट्टी का संघनन और कंपन संघनन।
टैंपिंग द्वारा मिट्टी संघनन की विधि संघनन की जा रही मिट्टी में आघात भार के स्थानांतरण पर आधारित है। कंपन और कंपन टैंपिंग विधियों के विपरीत, इस विधि में मिट्टी के साथ काम करने वाले शरीर के प्रभाव के समय भार के अनुप्रयोग की उच्च गति के कारण काफी अधिक प्रभाव ऊर्जा होती है, जिसके कारण यह विधि संघनन सुनिश्चित करती है।
अत्यधिक मोटाई (लगभग 2 मीटर तक) की परतों में एकजुट और गैर-संबद्ध मिट्टी। इमारतों और संरचनाओं, तकनीकी उपकरणों और फर्शों की नींव के नीचे मिट्टी के कुशन का निर्माण करते समय टैम्पिंग द्वारा मिट्टी को संघनित करने की विधि का औद्योगिक निर्माण में सबसे व्यापक उपयोग पाया गया है। इस विधि का उपयोग स्तंभ नींव का निर्माण करते समय धंसने वाली मिट्टी में गड्ढों को संकुचित करने के लिए भी किया जाता है।
मृदा संघनन की संयुक्त विधि मिट्टी पर स्थैतिक, कंपन, कंपन और टैम्पिंग भार के विभिन्न संयोजनों के उपयोग पर आधारित है। यह विधि सभी प्रकार की मिट्टी को संकुचित करना संभव बनाती है और इसका उपयोग मुख्य रूप से व्यापक कार्यों के लिए किया जाता है।
कंपन द्वारा मिट्टी के संघनन की विधि काम करने वाले हिस्सों (ड्रम, पहिया, प्लेट, कंपन सिर) से यांत्रिक हार्मोनिक कंपन के संचरण पर आधारित होती है, जो कि संकुचित होने वाली मिट्टी तक होती है। कंपन विधि को सतही और गहरे में विभाजित किया गया है। मिट्टी की सतह कंपन संघनन की विधि इस तथ्य से विशेषता है कि ऑपरेशन के दौरान संघनन कार्य तत्व मिट्टी की सतह पर स्थित होता है और, दोलनशील गति करते हुए, उस पर कार्य करता है। गहरी विधि के साथ, ऑपरेशन के दौरान कॉम्पैक्टिंग कार्य तत्व मिट्टी के अंदर स्थित होता है।
सतह कंपन विधि का उपयोग गैर-संसंजक और खराब रूप से संयोजित बैकफ़िल मिट्टी के संघनन में किया गया है। गहरी कंपन विधि का उपयोग रेतीली मिट्टी, विशेष रूप से जल-संतृप्त अवस्था में, को संकुचित करने के लिए प्रभावी ढंग से किया जा सकता है। कंपन के मुख्य मापदंडों के आधार पर, जो कंपन की आवृत्ति और आयाम हैं, मिट्टी की सतह संघनन के लिए कंपन मशीनें कंपन-प्रभाव मोड में भी काम कर सकती हैं। उनके दोलनों का आयाम बहुत अधिक है, और दोलन आवृत्ति कंपन मशीनों की तुलना में कम है। इस मामले में, कंपन मशीनों को कहा जाता है
वाइब्रोटैम्पिंग, और संघनन विधि वाइब्रोटैम्पिंग है। कंपायमान रैमिंग द्वारा मिट्टी संघनन की विधि का उपयोग सीमित स्थानों में बैकफ़िल को संकुचित करने के लिए निर्माण में किया गया है।
62. गहरी मिट्टी का संघनन।
मिट्टी के ढेर के साथ संघनन, कुओं को छेदने या छिद्रित करने की प्रक्रिया में रेडियल संघनन के दौरान मिट्टी का विस्थापन और बाद में उन्हें मिट्टी से भरना और परत-दर-परत संघनन
गहरी संघनन विधियाँ:
भौतिक
डुबाना
जल निकासी (ऊर्ध्वाधर जल निकासी)
यांत्रिक
कंपन संघनन
ढेर से मिट्टी का संघनन
वायवीय छिद्रों से मिट्टी को संकुचित करना
सर्पिल आकार की कार्यशील बॉडी से सील करें
स्क्रू-पाइल के रूप में कार्यशील निकाय के साथ संघनन
संयुक्त
जल+कंपन
(हाइड्रोलिक कंपन कम्पेक्टर)
मिट्टी को संकुचित करते समय, इष्टतम आर्द्रता सुनिश्चित करना आवश्यक है, जिसके लिए कम से कम ऊर्जा खपत की आवश्यकता होती है।
अनुक्रमिक संघनन के साथ, कार्य क्रमबद्ध तरीके से किया जाता है। कुएं बनाने के लिए पर्कशन विधि का उपयोग किया जाता है। 1 परत के संघनन की अवधि 30 सेकंड है। 10-15 वार के साथ. 5-25 मीटर की गहराई तक थोक और अवतल मिट्टी के लिए, सतह (बफर) परत को अतिरिक्त रूप से संकुचित किया जाना चाहिए।
गहरे कंपन संघनन - रेतीले जल-संतृप्त आधारों के लिए: थोक और जलोढ़ रेत। इस विधि को क्रमिक रूप से एक कंपन वाली छड़ को मिट्टी में डुबो कर लागू किया जाता है, साथ ही साथ आंतरिक गुहा के माध्यम से पानी की आपूर्ति की जाती है, कंपन वाली छड़ को आवश्यक गहराई तक डुबोने के बाद, पानी आपूर्ति बंद हो जाती है और 4-5 बार उठाने और कम करने के अलावा सूखा किया जाता है। प्रारंभिक भिगोने के साथ गहरा संघनन - विकृति और संघनन द्वारा कम की गई मिट्टी के उप-विभाजन गुणों को बनाने के लिए: कम से कम 0.2 मीटर / दिन के उच्च निस्पंदन गुणांक के साथ दोमट, दोमट, गादयुक्त मिट्टी। संघनन प्रक्रिया भिगोने पर मिट्टी के अपने द्रव्यमान के प्रभाव में की जाती है, और काफी लंबी होती है - 2-3 महीने। कॉमिटलेट विस्फोटों के कारण अतिरिक्त संघनन के उपयोग से मिट्टी संघनन के लिए आवश्यक समय को 3-7 दिनों तक कम किया जा सकता है।
63. मृदा संघनन का गुणवत्ता नियंत्रण।
आप निम्नलिखित सबसे सामान्य तरीकों का उपयोग करके मिट्टी संघनन की गुणवत्ता को नियंत्रित कर सकते हैं: मानक, काटने के छल्ले, रेडियोआइसोटोप, जांच, एक मोहर दबाना, वैक्सिंग, छेद विधि। एक या किसी अन्य विधि का चुनाव प्रयोगशाला के उपकरण, की प्रकृति पर निर्भर करता है संरचना, बनाए जा रहे तटबंध की मात्रा और उनकी कक्षा। मानक विधि सील सोयुजडोरएनआईआई डिवाइस का उपयोग करके इष्टतम आर्द्रता और अधिकतम मानक घनत्व निर्धारित करती है। तटबंधों में मिट्टी के कंकाल के घनत्व को निर्धारित करने के लिए कटिंग रिंग विधि 300...400 सेमी3 (डी/एच=एल) की क्षमता वाली धातु की अंगूठी की मात्रा में गीली मिट्टी के घनत्व को निर्धारित करने पर आधारित है। संकुचित परत, और इस मिट्टी की नमी सामग्री। क्षेत्र प्रयोगशाला स्थितियों में, कटिंग रिंग विधि अपनी सादगी के कारण, यह सबसे स्वीकार्य और व्यापक है। वर्तमान में, रेडियोआइसोटोप विधियां निर्माण अभ्यास में सबसे व्यापक हैं, क्योंकि मिट्टी क्षेत्र प्रयोगशालाएं बड़ी मिट्टी की संरचनाएं ऐसे उपकरणों से सुसज्जित थीं जो गामा विकिरण और न्यूट्रॉन के अवशोषण और बिखरने का उपयोग करती थीं। तटबंधों और बैकफ़िल में मिट्टी के संघनन की डिग्री की निगरानी के प्रकारों में से एक के रूप में स्थैतिक और गतिशील जांच की विधि सबसे कुशल और सरल है मौजूदा नियंत्रण विधियाँ। स्टाम्प इंडेंटेशन विधि का उपयोग मिट्टी की नींव की ताकत निर्धारित करने के लिए किया जाता है। विशेष रूप से, इस विधि का उपयोग व्यापक रूप से औद्योगिक भवनों के फर्श और नींव के नीचे नींव की मिट्टी के संघनन की गुणवत्ता को नियंत्रित करने के लिए किया जाता है। वैक्सिंग विधि का उपयोग मुख्य रूप से सर्दियों की परिस्थितियों में मिट्टी के संघनन को नियंत्रित करने के लिए किया जाता है। छेद विधि का उपयोग बैकफ़िल बिछाते समय किया जाता है कुचली हुई मोटे मिट्टी या जमी हुई मिट्टी के ढेलों वाली मिट्टी से। तटबंध के शरीर में रखी मिट्टी की गुणवत्ता को स्वीकार्य माना जा सकता है यदि परियोजना द्वारा निर्दिष्ट मिट्टी के घनत्व से विचलन वाले नियंत्रण नमूनों की संख्या 10% से अधिक न हो। साइट पर लिए गए नियंत्रण नमूनों की कुल संख्या, और नमूनों में मिट्टी के कंकाल का घनत्व आवश्यक (न्यूनतम) घनत्व से 0.5 ग्राम/सेमी3 से अधिक नहीं होना चाहिए।
64. पंचर विधि से मिट्टी का बंद विकास।
जब शंक्वाकार टिप वाले पाइप को इसमें दबाया जाता है तो मिट्टी के रेडियल संघनन के कारण छिद्रों का बनना पंचर कहलाता है। दबाव हाइड्रोलिक जैक का उपयोग करके किया जाता है। टिप के साथ पाइप का एक खंड गड्ढे में रखा जाता है और, संरेखण के बाद, इसे रॉड स्ट्रोक की लंबाई तक जैक के साथ जमीन में दबाया जाता है। रॉड अपनी प्रारंभिक स्थिति में लौटने के बाद, उसके स्थान पर एक दबाव पाइप (रैमरोड) डाला जाता है, और प्रक्रिया दोहराई जाती है। पहले पाइप लिंक को उसकी पूरी लंबाई तक दबाने के बाद, रैमरोड को हटा दिया जाता है, अगले लिंक को गड्ढे में उतारा जाता है, जिसे पहले से ही जमीन में दबाए गए लिंक से बट वेल्ड किया जाता है। इसके बाद, वेल्डेड लिंक को नीचे दबाया जाता है, और चक्र को पर्याप्त संख्या में दोहराया जाता है जब तक कि उस क्षेत्र की पूरी लंबाई के साथ एक पंचर नहीं बनाया जाता है जिसे पारंपरिक तरीके से खोदा नहीं जा सकता है। प्रत्येक चक्र के लिए, पाइप 150 मिमी आगे बढ़ता है। इस विधि का अभ्यास अत्यधिक संपीड़ित मिट्टी में किया जाता है; क्षैतिज बल के अलावा, 3 मीटर से अधिक की गहराई पर 100 से 400 मिमी के व्यास वाले पाइपों के लिए छेद "छेदा" जाता है। खराब संपीड़ित मिट्टी (रेत, रेतीली दोमट) में , दीवारों की स्थिरता सुनिश्चित करने के लिए अनुप्रस्थ और कंपन प्रभाव लागू करना आवश्यक है। इस मामले में, 300 मिमी तक के व्यास वाले छेद बनाए जाते हैं।
65. पुशिंग विधि से मिट्टी का बंद विकास।
इस विधि का उपयोग 500 मिमी से 1800 मिमी के व्यास वाले स्टील पाइप या 80 मीटर तक की दूरी पर वर्गाकार (आयताकार) क्रॉस-सेक्शन वाले कलेक्टरों को बिछाने के लिए किया जाता है। तकनीक इस प्रकार है: पाइप लिंक को क्रमिक रूप से दबाया जाता है ज़मीन, जिसके अंदर मिट्टी विकसित की जाती है और बरमा का उपयोग करके हटा दी जाती है। आसानी से मिटने वाली मिट्टी में, हाइड्रोमैकेनिकल विधि का उपयोग करके निष्कासन किया जाता है (पाइप के अंदर की मिट्टी को पानी की धारा के साथ मिटा दिया जाता है और गूदे को पंप से बाहर निकाल दिया जाता है)। पाइपों का उपयोग अक्सर मुख्य पाइपलाइनों को रखने के लिए केस के रूप में किया जाता है। बंद मिट्टी के विकास के लिए क्षैतिज ड्रिलिंग की विधि।
ड्रिलिंग का उपयोग चिकनी मिट्टी में 100 मीटर तक की लंबाई के लिए 800 से 1000 मिमी व्यास वाली पाइपलाइन बिछाने के लिए किया जाता है। पाइप का अंत बढ़े हुए व्यास के कटिंग बिट से सुसज्जित होता है, पाइप को एक मोटर द्वारा घुमाया जाता है गड्ढे के किनारे पर स्थापित किया गया। पाइप को आगे की ओर गति एक रैक जैक द्वारा गड्ढे की पिछली दीवार पर जोर देकर दी जाती है। पाइप के अंदर से भरने वाली मिट्टी को पानी की धारा के साथ पाइप के अंदर की मिट्टी को नष्ट करके और फिर एक पंप के साथ लुगदी को पंप करके (आसानी से मिटने वाली मिट्टी में) हाइड्रोमैकेनिकल विधि का उपयोग करके स्क्रू इंस्टॉलेशन का उपयोग करके बिछाई जा रही पाइप के माध्यम से हटाया जा सकता है। ) या उनके हैंडल में एक्सटेंशन वाले बेलर।
कंक्रीट मिश्रण के सबसे महत्वपूर्ण गुणों में से एक अपने स्वयं के द्रव्यमान या उस पर लागू भार के प्रभाव में प्लास्टिक रूप से फैलने की क्षमता है। यह कंक्रीट मिश्रण से विभिन्न प्रकार के प्रोफाइल के उत्पादों के निर्माण की तुलनात्मक आसानी और इसके संघनन के लिए विभिन्न तरीकों का उपयोग करने की संभावना को निर्धारित करता है। इस मामले में, संघनन की विधि और मिश्रण के गुण (इसकी गतिशीलता या तरलता) बारीकी से संबंधित हैं। इस प्रकार, कठोर गैर-बहने वाले मिश्रणों को जोरदार संघनन की आवश्यकता होती है, और जब उनसे उत्पादों को ढाला जाता है, तो अतिरिक्त दबाव (भार के साथ) के साथ तीव्र कंपन या कंपन का उपयोग किया जाना चाहिए। कठोर मिश्रण को संघनित करने की अन्य विधियाँ भी संभव हैं - संघनन, दबाव, रोलिंग।
गतिशील मिश्रण कंपन द्वारा आसानी से और प्रभावी ढंग से संकुचित होते हैं। संपीड़न (दबाने) प्रकार के संघनन का उपयोग - दबाना, रोल करना, साथ ही टैंपिंग - ऐसे मिश्रण के लिए अनुपयुक्त है। महत्वपूर्ण दबाव बलों के प्रभाव में या छेड़छाड़ के बार-बार दोहराए जाने वाले प्रभावों के तहत, मिश्रण आसानी से डाई के नीचे से बाहर निकल जाएगा या छेड़छाड़ से अलग हो जाएगा।
कास्ट मिश्रण अपने स्वयं के द्रव्यमान के प्रभाव में संघनन करने में सक्षम होते हैं। संघनन प्रभाव को बढ़ाने के लिए, उन्हें कभी-कभी अल्पकालिक कंपन के अधीन किया जाता है।
इस प्रकार, कंक्रीट मिश्रण को संकुचित करने की निम्नलिखित विधियों को प्रतिष्ठित किया जा सकता है: कंपन करना, दबाना, रोल करना, संकुचित करना और ढलाई करना। तकनीकी और आर्थिक दृष्टि से सबसे प्रभावी विधि कंपन विधि है। इसे अन्य विधियों के साथ संयोजन में भी सफलतापूर्वक प्रयोग किया जाता है
मैकेनिकल कॉम्पैक्शन - रैमिंग (कंपन रैमिंग! प्रेसिंग (वाइब्रेटिंग प्रेसिंग), रोलिंग (वाइब्रेटिंग रोलिंग)। रेड" मोबाइल कंक्रीट मिश्रण को कॉम्पैक्ट करने के लिए मैकेनिकल तरीकों की एक नवीनता सेंट्रीफ्यूजेशन है, जिसका उपयोग खोखले ट्यूबलर उत्पादों के मोल्डिंग में किया जाता है। प्राप्त करने के मामले में अच्छे परिणाम उच्च गुणवत्ता वाले कंक्रीट को इसके यांत्रिक संघनन (मुख्य रूप से कंपन द्वारा) की प्रक्रिया के दौरान मिश्रण की निकासी द्वारा प्राप्त किया जाता है, हालांकि, निकासी ऑपरेशन की महत्वपूर्ण अवधि इसके तकनीकी और आर्थिक प्रभाव को काफी कम कर देती है, और इसलिए इस विधि का व्यापक रूप से प्रीकास्ट में उपयोग नहीं किया जाता है। ठोस प्रौद्योगिकी.
आइए कंक्रीट मिश्रण को जमा करने की उपरोक्त विधियों के सार पर संक्षेप में विचार करें।
कंपन एक ठोस मिश्रण का संघनन है जो बार-बार होने वाले मजबूर कंपन के संचरण के परिणामस्वरूप होता है, जिसे सामूहिक रूप से झटकों द्वारा व्यक्त किया जाता है। हिलाने के प्रत्येक क्षण में, कंक्रीट मिश्रण के कण मानो निलंबित अवस्था में होते हैं और अन्य कणों के साथ उनका संबंध टूट जाता है। धक्का देने वाले बल की बाद की कार्रवाई के साथ, कण अपने स्वयं के द्रव्यमान के अंतर्गत आते हैं और अधिक लाभप्रद स्थिति पर कब्जा कर लेते हैं जिसमें वे झटके से कम प्रभावित हो सकते हैं। यह दूसरों के बीच उनकी सबसे सघन पैकिंग की स्थिति को पूरा करता है, जो अंततः एक सघन कंक्रीट मिश्रण प्राप्त करने की ओर ले जाता है। कंपन करने पर कंक्रीट मिश्रण के संघनन का दूसरा कारण उस पर लागू बाहरी बलों के प्रभाव में अस्थायी रूप से द्रव अवस्था में जाने का गुण है, जिसे थिक्सोट्रॉपी कहा जाता है। तरल अवस्था में होने के कारण, कंक्रीट मिश्रण, कंपन करते समय, फैलने लगता है, एक आकार विन्यास प्राप्त करता है, और अपने स्वयं के द्रव्यमान के प्रभाव में संकुचित हो जाता है। संघनन का तीसरा कारण कंक्रीट के उच्च तकनीकी गुणों को निर्धारित करता है। ,
कंपन द्वारा कंक्रीट मिश्रण के संघनन की उच्च डिग्री | कम-शक्ति वाले उपकरणों का उपयोग करके प्राप्त किया गया। उदाहरण के लिए, कई घन मीटर की क्षमता वाले कंक्रीट द्रव्यमान को केवल 1...1.5 किलोवाट की ड्राइव शक्ति वाले वाइब्रेटर के साथ संकुचित किया जाता है।
कंपन के प्रभाव में कंक्रीट मिश्रण को अस्थायी रूप से तरल अवस्था में बदलने की क्षमता मिश्रण की गतिशीलता और उस गति पर निर्भर करती है जिस पर इसके कण एक दूसरे के सापेक्ष चलते हैं। मोबाइल मिश्रण आसानी से तरल अवस्था में बदल जाते हैं और उन्हें कम गति की आवश्यकता होती है। लेकिन बढ़ती कठोरता (गतिशीलता में कमी) के साथ, कंक्रीट मिश्रण तेजी से इस संपत्ति को खो देता है या कंपन गति में इसी वृद्धि की आवश्यकता होती है, यानी, संघनन के लिए उच्च ऊर्जा लागत की आवश्यकता होती है।
कंपन के दौरान दोलनों की गति v (सेमी/सेकंड) को आयाम ए और दोलनों की आवृत्ति n के गुणनफल द्वारा व्यक्त किया जाता है: u = An - कंपन तंत्र के दोलनों की एक निरंतर आवृत्ति पर (अधिकांश कंपन प्लेटफार्मों के लिए 3000 के बराबर) kol/min), मान को बदलकर दोलन गति में परिवर्तन प्राप्त किया जा सकता है
प्लेटें। अभ्यास से पता चला है कि गतिशील कंक्रीट मिश्रण 0.3...0.35 मिमी के कंपन आयाम के साथ प्रभावी ढंग से संकुचित होते हैं,
और कठोर वाले - 0.5...0.7 मिमी.
कंपन संघनन की गुणवत्ता न केवल कंपन तंत्र (आवृत्ति और आयाम) के ऑपरेटिंग मापदंडों से प्रभावित होती है, बल्कि कंपन की अवधि से भी प्रभावित होती है। प्रत्येक कंक्रीट मिश्रण के लिए, उसकी गतिशीलता के आधार पर, कंपन संघनन की अपनी इष्टतम अवधि होती है, जब तक कि मिश्रण प्रभावी ढंग से संकुचित हो जाता है, और जिसके बाद ऊर्जा लागत मिश्रण के संघनन की तुलना में बहुत अधिक हद तक बढ़ जाती है। आगे संघनन से घनत्व बिल्कुल भी नहीं बढ़ता है। इसके अलावा, अत्यधिक लंबे समय तक कंपन से मिश्रण का प्रदूषण हो सकता है, इसे अलग-अलग घटकों में विभाजित किया जा सकता है - सीमेंट मोर्टार और भराव के बड़े दाने, जो अंततः क्रॉस-सेक्शन में उत्पाद के असमान घनत्व और व्यक्तिगत भागों में ताकत में कमी का कारण बनेंगे। इसका.
स्वाभाविक रूप से, लंबे समय तक कंपन आर्थिक दृष्टिकोण से भी लाभहीन है: ऊर्जा लागत और श्रम तीव्रता में वृद्धि होती है, और मोल्डिंग लाइन की उत्पादकता कम हो जाती है।
कंपन संघनन की तीव्रता I (cm2/s3), जो कंपन की सबसे छोटी अवधि द्वारा व्यक्त की जाती है, कंपन तंत्र के मुख्य ऑपरेटिंग मापदंडों पर भी निर्भर करती है - कंपन की आवृत्ति और आयाम, गति और त्वरण के उनके पारस्परिक संयोजन को ध्यान में रखते हुए उपयोग किया जाता है। कंपन की: I = A2/n3.
यदि मजबूर कंपन की आवृत्ति प्राकृतिक कंपन की आवृत्ति के बराबर हो तो कंपन संघनन की तीव्रता भी बढ़ जाती है। इस तथ्य के कारण कि कंक्रीट मिश्रण में कण आकार की एक विस्तृत श्रृंखला होती है (सीमेंट के लिए कई माइक्रोमीटर से लेकर मोटे समुच्चय के लिए कई सेंटीमीटर तक) और, तदनुसार, अपने स्वयं के कंपन की आवृत्ति में अंतर, मिश्रण का सबसे तीव्र संघनन होगा उस स्थिति में जब कंपन मोड को विभिन्न आवृत्तियों की विशेषता होती है। इस प्रकार बहु-आवृत्ति कंपन का उपयोग करने का प्रस्ताव सामने आया।
उत्पाद मोल्डिंग संचालन के तकनीकी और आर्थिक मूल्यांकन के लिए इन कारकों को ध्यान में रखा जाना चाहिए। ऊपर से यह निष्कर्ष निकलता है कि संघनन ऊर्जा बढ़ने के साथ संघनन दक्षता बढ़ती है, संघनन अवधि कम होती है और मोल्डिंग लाइन की उत्पादकता बढ़ती है। इस प्रकार, कंक्रीट मिश्रण के गुणों और मोल्डिंग लाइन की उत्पादकता के तकनीकी और आर्थिक विश्लेषण के आधार पर, कंपन संघनन तंत्र की शक्ति का चयन करना संभव है।
कंक्रीट मिश्रण का कंपन संघनन पोर्टेबल और स्थिर कंपन तंत्र का उपयोग करके किया जाता है। प्रीकास्ट प्रबलित कंक्रीट में पोर्टेबल कंपन तंत्र का उपयोग सीमित है। इनका उपयोग मुख्य रूप से स्टैंड पर बड़े आकार के विशाल उत्पादों को ढालते समय किया जाता है।
संचालित कारखानों में प्रीकास्ट कंक्रीट प्रौद्योगिकी में
प्रवाह-इकाई और कन्वेयर योजनाओं के अनुसार, कंपन प्लेटफार्मों का उपयोग किया जाता है। वाइब्रेटिंग प्लेटफ़ॉर्म वाइब्रेटर के विभिन्न प्रकारों और डिज़ाइनों द्वारा प्रतिष्ठित होते हैं - इलेक्ट्रोमैकेनिकल, इलेक्ट्रोमैग्नेटिक, वायवीय; कंपन की प्रकृति - हार्मोनिक, पर्कशन, संयुक्त; कंपन रूप - वृत्ताकार दिशात्मक - ऊर्ध्वाधर, क्षैतिज; टेबल डिज़ाइन आरेख - एक ठोस ऊपरी फ्रेम के साथ एक या दो कंपन शाफ्ट के साथ एक टेबल बनाते हैं, और अलग-अलग कंपन ब्लॉकों से इकट्ठे होते हैं, जो आम तौर पर एक सामान्य कंपन विमान का प्रतिनिधित्व करते हैं जिस पर कंक्रीट मिश्रण के साथ फॉर्म स्थित होता है।
प्लेटफ़ॉर्म टेबल पर फॉर्म को सुरक्षित रूप से जकड़ने के लिए, विशेष तंत्र प्रदान किए जाते हैं - विद्युत चुम्बक, वायवीय या यांत्रिक क्लैंप।
कंपन प्लेटफ़ॉर्म (चित्र 11.1) एक सपाट टेबल है जो स्प्रिंग सपोर्ट के माध्यम से स्थिर समर्थन या एक फ्रेम (बिस्तर) पर समर्थित है। स्प्रिंग्स को टेबल के कंपन को कम करने के लिए डिज़ाइन किया गया है और इस तरह समर्थन पर उनके प्रभाव को रोका जा सकता है, अन्यथा वे नष्ट हो जाएंगे। निचले हिस्से में, उस पर स्थित एक्सेन्ट्रिक्स के साथ एक कंपन शाफ्ट कठोरता से मेज से जुड़ा हुआ है। जब शाफ्ट एक इलेक्ट्रिक मोटर से घूमता है, तो एक्सेन्ट्रिक्स टेबल के कंपन को उत्तेजित करते हैं, जो फिर कंक्रीट मिश्रण के साथ फॉर्म में प्रेषित होते हैं, जिसके परिणामस्वरूप इसका संघनन होता है। एक कंपन प्लेटफ़ॉर्म की शक्ति का अनुमान उसकी भार क्षमता (आकार के साथ उत्पाद का वजन) से लगाया जाता है, जो 2...30 टन है।
पूर्वनिर्मित प्रबलित कंक्रीट कारखाने 3000 आरपीएम की घूर्णन गति और 0.3...0.6 मिमी के आयाम के साथ मानकीकृत कंपन प्लेटफार्मों से सुसज्जित हैं। ये कंपन करने वाले प्लेटफ़ॉर्म 18 मीटर तक लंबे और 3.6 मीटर तक चौड़े ढांचे के कठोर कंक्रीट मिश्रण को कॉम्पैक्ट करने में अच्छे हैं।
कंपन प्लेटफार्मों पर उत्पादों को ढालते समय, विशेष रूप से झरझरा समुच्चय पर कठोर कंक्रीट मिश्रण से, कंक्रीट की संरचना में सुधार करने के लिए, वजन का उपयोग किया जाता है - स्थैतिक,
कंपन, वायवीय, कंपन-वायवीय। कंक्रीट मिश्रण के गुणों के आधार पर भार का परिमाण 2...5 kPa है।
स्थिर सांचों में उत्पादों को ढालते समय, कंक्रीट मिश्रण को सतह, गहरे और लगे हुए वाइब्रेटर का उपयोग करके संकुचित किया जाता है, जो सांचे से जुड़े होते हैं। क्षैतिज रूप में उत्पादों का निर्माण करते समय, कठोर या कम गति वाले कंक्रीट मिश्रण का उपयोग किया जाता है, और लंबवत रूप से ढालते समय,
नए रूपों में (कैसेट में), 8...10 सेमी के शंकु ड्राफ्ट के साथ मोबाइल मिश्रण का उपयोग किया जाता है।
एफ प्रेसिंग प्रीफैब्रिकेटेड प्रबलित कंक्रीट तकनीक में कंक्रीट मिश्रण को कॉम्पैक्ट करने की शायद ही कभी इस्तेमाल की जाने वाली विधि है, हालांकि तकनीकी संकेतकों के संदर्भ में यह अत्यधिक कुशल है, जिससे न्यूनतम सीमेंट खपत (100...150 किलोग्राम) के साथ उच्च घनत्व और ताकत वाले कंक्रीट का उत्पादन संभव हो जाता है। /m3 कंक्रीट का)। दबाव विधि का प्रसार केवल आर्थिक कारणों से बाधित है। जिस दबाव पर कंक्रीट प्रभावी रूप से संकुचित होना शुरू होता है वह 10...15 एमपीए और अधिक होता है। इस प्रकार, उत्पाद को संकुचित करने के लिए, इसके प्रत्येक 1 एम2 पर 10...15 एमएन का भार लगाया जाना चाहिए। ऐसी शक्ति के प्रेस का उपयोग प्रौद्योगिकी में किया जाता है, उदाहरण के लिए, जहाज के पतवार को दबाने के लिए, लेकिन उनकी लागत इतनी अधिक हो जाती है कि यह ऐसे प्रेस के उपयोग की आर्थिक व्यवहार्यता को पूरी तरह से बाहर कर देती है।
प्रीकास्ट कंक्रीट तकनीक में, कंक्रीट मिश्रण के कंपन होने पर उस पर यांत्रिक भार के अतिरिक्त अनुप्रयोग के रूप में दबाने का उपयोग किया जाता है। इस मामले में, दबाने वाले दबाव का आवश्यक मान 500...1000 Pa से अधिक नहीं होता है। तकनीकी रूप से, कंक्रीट मिश्रण के व्यक्तिगत कणों के मजबूर आंदोलन के परिणामस्वरूप स्थिर रूप से लागू भार के प्रभाव में ऐसा दबाव प्राप्त होता है।
फ्लैट और प्रोफाइल स्टैम्प से दबाने में अंतर है। उत्तरार्द्ध अपनी प्रोफ़ाइल को कंक्रीट मिश्रण में स्थानांतरित करते हैं। इस प्रकार सीढ़ियों की उड़ानें और कुछ प्रकार के रिब्ड पैनल बनते हैं। बाद वाले मामले में, दबाने की विधि को स्टैम्पिंग भी कहा जाता है। रोलिंग एक प्रकार का दबाव है। इस मामले में, संघनन दबाव केवल रोलर के एक छोटे से क्षेत्र के माध्यम से कंक्रीट मिश्रण में प्रेषित होता है, जिसके परिणामस्वरूप संघनन दबाव की आवश्यकता कम हो जाती है। लेकिन यहां कंक्रीट मिश्रण के प्लास्टिक गुण और उसके द्रव्यमान की सुसंगतता विशेष महत्व प्राप्त करती है। यदि अपर्याप्त सामंजस्य है, तो मिश्रण दबाने वाले रोलर द्वारा स्थानांतरित हो जाएगा और टूट जाएगा। सेंट्रीफ्यूजेशन - घूर्णन के दौरान उत्पन्न होने वाले केन्द्रापसारक बलों की कार्रवाई के परिणामस्वरूप कंक्रीट मिश्रण का संघनन। इस उद्देश्य के लिए, सेंट्रीफ्यूज का उपयोग किया जाता है (चित्र 11.2), जो ट्यूबलर अनुभाग का एक रूप है, जो संघनन प्रक्रिया के दौरान 600...1000 मिनट^" तक घूमता है। कंक्रीट मिश्रण को सांचे में लोड किया जाता है (आवश्यक रूप से एक का) मोबाइल स्थिरता) "केन्द्रापसारक बलों के प्रभाव में विकसित होती है
रोटेशन के दौरान गठित, मोल्ड की आंतरिक सतह के खिलाफ दबाया जाता है और एक ही समय में कॉम्पैक्ट किया जाता है। कंक्रीट मिश्रण और पानी के ठोस घटकों के विभिन्न घनत्वों के परिणामस्वरूप, कंक्रीट मिश्रण से 20...30% तक पानी निकाल दिया जाता है, जो उच्च घनत्व वाले कंक्रीट के उत्पादन में योगदान देता है।
सेंट्रीफ्यूजेशन विधि उच्च घनत्व, ताकत (40...60 एमपीए) और स्थायित्व के कंक्रीट उत्पाद प्राप्त करना अपेक्षाकृत आसान बनाती है। साथ ही, उच्च सामंजस्य का कंक्रीट मिश्रण प्राप्त करने के लिए, बड़ी मात्रा में सीमेंट (400...450 किग्रा/एम3) की आवश्यकता होती है, अन्यथा मिश्रण केन्द्रापसारक बलों के प्रभाव में छोटे और बड़े दानों में अलग हो जाएगा, क्योंकि बाद वाला बड़ी ताकत से फॉर्म की सतह पर दबाव डालेगा। सेंट्रीफ्यूजेशन विधि का उपयोग पाइप, पावर लाइन सपोर्ट और लैंप स्टैंड बनाने के लिए किया जाता है। वैक्यूमिंग करते समय, कंक्रीट मिश्रण में 0.07...0.08 एमपीए तक का वैक्यूम बनाया जाता है और इसकी तैयारी और सांचे में रखने के दौरान हवा अंदर चली जाती है, और इस वैक्यूम के प्रभाव में कंक्रीट मिश्रण से कुछ पानी निकाल दिया जाता है: खाली जगह पर ठोस कण कब्जा कर लेते हैं और कंक्रीट मिश्रण अधिक घनत्व प्राप्त कर लेता है। इसके अलावा, वैक्यूम की उपस्थिति वैक्यूम के परिमाण के बराबर वायुमंडलीय दबाव के कंक्रीट मिश्रण पर दबाव प्रभाव का कारण बनती है। यह कंक्रीट मिश्रण को सघन करने में भी मदद करता है। वैक्यूमिंग को आमतौर पर कंपन के साथ जोड़ा जाता है। वैक्यूम के अधीन कंक्रीट मिश्रण को कंपन करने की प्रक्रिया में, हवा के बुलबुले और पानी के स्थान पर वैक्यूमिंग के दौरान बने छिद्र ठोस घटकों से तीव्रता से भर जाते हैं। हालाँकि, तकनीकी दृष्टिकोण से निकासी में एक महत्वपूर्ण तकनीकी और आर्थिक नुकसान है, अर्थात्: प्रक्रिया की लंबी अवधि - उत्पाद की मोटाई के प्रत्येक 1 सेमी के लिए 1...2 मिनट, कंक्रीट मिश्रण के गुणों पर निर्भर करता है और क्रॉस-सेक्शन का आकार. जिस परत को निर्वात के अधीन किया जा सकता है उसकी मोटाई 12...15 सेमी से अधिक नहीं होती है। परिणामस्वरूप, सतह परत को विशेष रूप से उच्च घनत्व प्रदान करने के लिए मुख्य रूप से विशाल संरचनाओं को निर्वात के अधीन किया जाता है। प्रीकास्ट कंक्रीट तकनीक में वैक्यूमिंग का व्यावहारिक रूप से उपयोग नहीं किया जाता है। wj
कंक्रीट संरचनाएं खड़ी करने की तकनीक में कंक्रीट मिश्रण तैयार करना और उसे जमाना शामिल है। ऐसे मामले होते हैं, जब किसी घोल को मिलाते समय अंदर गुहाएं दिखाई देती हैं, जो संरचना को बाधित कर सकती हैं और इसके घनत्व को कम कर सकती हैं। इसके कारण, उत्पाद में दरारें दिखाई देती हैं, जो अंततः कंक्रीट संरचनाओं के विनाश का कारण बन सकती हैं। संघनन प्रक्रिया के दौरान विशेषज्ञ घोल से हवा और अतिरिक्त तरल निकाल देते हैं, जिससे यह और अधिक घना हो जाता है। इस प्रकार, उत्पाद अधिक मजबूत और टिकाऊ होता है।
सीमेंट मिश्रण बिछाने में कंक्रीट का संघनन सबसे महत्वपूर्ण चरण माना जाता है। उत्पाद का ठोस गुणांक और मुख्य विशेषताएं इस बात पर निर्भर करेंगी कि यह क्रिया कितनी सावधानी से की जाती है। प्रक्रिया के दौरान, विशेषज्ञ कंक्रीट की सतह को मैन्युअल रूप से या यांत्रिक उपकरणों का उपयोग करके, गुहाओं को हटाकर संसाधित करते हैं। इससे कंक्रीट समाधान की एकरूपता प्राप्त करना और अन्य संरचनात्मक तत्वों के साथ संरचना के आसंजन को बढ़ाना संभव हो जाता है।
तरीकों
मिश्रण को संकुचित करते समय बिल्डर्स निम्नलिखित प्रकार के उपकरणों का उपयोग करते हैं:
- सतह (सीमेंट की ऊपरी परत के लिए);
- गहरी (बड़ी कंक्रीट संरचनाएं);
- बाहरी (लकड़ी के फॉर्मवर्क के किनारे या सीमेंट मोर्टार के साथ एक कंटेनर पर संघनन से पहले स्थापित);
- कंपन प्लेटफ़ॉर्म (विशेष उद्यमों में प्रयुक्त)।
सीमेंट मोर्टार को संकुचित करने के विभिन्न तरीके हैं:
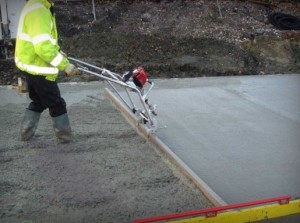
अन्य तरीके
अन्य संघनन विधियों में शामिल हैं:
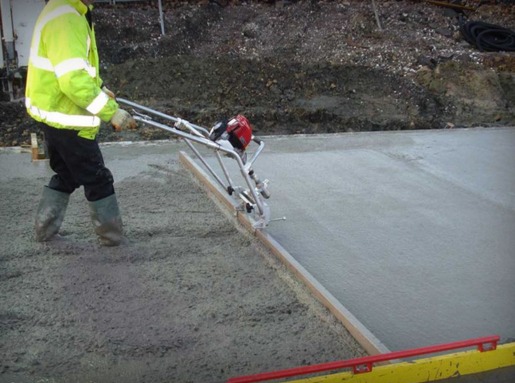
यह सुनिश्चित करने के लिए कि सीमेंट संरचना समान रूप से संकुचित है, निम्नलिखित सिफारिशों का पालन किया जाना चाहिए:
- लकड़ी के फॉर्मवर्क को स्थापित करते समय, आपको भागों के विश्वसनीय निर्धारण पर ध्यान देना चाहिए। संरचनात्मक तत्वों पर कोई अंतराल नहीं होना चाहिए (दरारों के माध्यम से कंक्रीट समाधान को निचोड़ा जा सकता है)। यह आवश्यक है कि फॉर्मवर्क पॉलिश और चिकना हो, अन्यथा यह उत्पाद पर डेंट छोड़ देगा। इसके अलावा, संरचना के शरीर में बाद में रिक्तियां बन सकती हैं।
- बोर्डों को हिलने से रोकने के लिए वेजेज सहित लकड़ी या प्लाईवुड फॉर्मवर्क के हिस्सों को सुरक्षित रूप से तय किया जाना चाहिए।
- रचना को कंपन करते समय, आपको समय-समय पर कंपन करने वाले पेंच की स्थिति को बदलना चाहिए, अन्यथा समाधान अमानवीय होगा और गुहाएं बन जाएंगी।
- विशेषज्ञ काम पर बहुत अधिक समय बर्बाद न करने की सलाह देते हैं, क्योंकि इससे प्रदूषण हो सकता है, जो इस तथ्य के कारण प्रकट होता है कि बड़े कुचले हुए पत्थर को नीचे गिरा दिया जाता है, और शीर्ष पर केवल सीमेंट मोर्टार जमा हो जाता है।
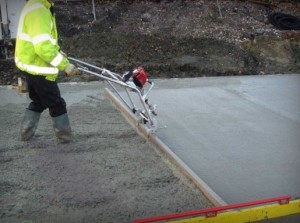
चूंकि सतह कंपन उपकरणों का उपयोग घनत्व की डिग्री के दृश्य निर्धारण की अनुमति नहीं देता है, इसलिए निर्माण कार्य के दौरान संरचना की ताकत सुनिश्चित करने में मदद के लिए अक्सर एक अतिरिक्त साधन का उपयोग किया जाता है। ऐसा करने के लिए, बिल्डर्स मौजूदा संरचना में उच्च प्लास्टिसिटी वाला समाधान जोड़ते हैं। इस कारण उत्पाद के खराब होने का खतरा बढ़ जाता है। ऐसी कमी से बचने के लिए सीमेंट की मात्रा बढ़ाने की सिफारिश की जाती है।
संघनन कारक
एक महत्वपूर्ण मानदंड का उपयोग करके किसी ठोस संरचना की गुणवत्ता का आकलन किया जा सकता है। हम संघनन गुणांक के बारे में बात कर रहे हैं। गुणांक निम्नानुसार निर्धारित किया जाता है: तैयार मिश्रण के विशिष्ट गुरुत्व के अनुपात की गणना उस मूल्य से की जाती है जो अंदर हवा के बुलबुले की अनुपस्थिति में प्राप्त किया गया था। इस प्रकार, गुणांक का स्वीकार्य मान 1 माना जाता है। यह सूचक कंक्रीट संघनन के विभिन्न तरीकों का उपयोग करके प्राप्त किया जा सकता है; विधियों का चुनाव सीधे संरचना, उद्देश्य और अंशों पर निर्भर करेगा। स्वचालित कंपन वाले पेंच समाधान की गुणवत्ता में उल्लेखनीय वृद्धि करते हैं।
गुणांक किस पर निर्भर करता है?
यह संकेतक संरचना के दाने के आकार के साथ-साथ उस वस्तु से निर्धारित होता है जिसे कंक्रीट किया जाएगा, चाहे वह अंधा क्षेत्र, मार्ग, रास्ते हों।
निष्कर्ष
अनुभवी बिल्डरों का दावा है कि संरचना की स्थिरता और स्थायित्व इस पर निर्भर करेगा। यदि आप चाहते हैं कि उत्पाद एक वर्ष से अधिक समय तक आपकी सेवा करे तो इसे ध्यान में रखा जाना चाहिए। समय पर किए गए उपायों से संरचना की क्षति से सुरक्षा को और बढ़ाने में मदद मिलेगी और बहाली कार्य पर पैसे की बचत होगी। सार्वभौमिक कंपन उपकरण उच्च गुणवत्ता वाले कंक्रीट का उत्पादन करेंगे। निर्माण कार्य करने से पहले, आपको पहले से विशेषज्ञों से परामर्श करना होगा और आवश्यक उपकरण का चयन करना होगा। एर्गोनोमिक वाइब्रेटिंग डिवाइस निर्माण श्रमिकों को विभिन्न स्थितियों में सीमेंट को कॉम्पैक्ट करने की अनुमति देते हैं।
थोड़ी मात्रा में निर्माण कार्य करने के लिए, पेशेवर पाँच किलोग्राम तक वजन वाले का उपयोग करने की सलाह देते हैं। बड़े पैमाने पर काम के लिए, बिल्डर बड़े उपकरणों का उपयोग करते हैं जो उन्हें बड़े मोर्चे पर उत्पादन में कंक्रीट को प्रभावी ढंग से कॉम्पैक्ट करने की अनुमति देते हैं।