A gépi talajtömörítés folyamatának fizikai alapjai. A felszíni talajtömörítés fizikai módszerei
A rezgés amplitúdójának és frekvenciájának befolyása
A részecskék oszcillációs frekvenciája és amplitúdója egymással összefügg, ami lehetővé teszi ipari körülmények között különböző rezgésmódok alkalmazását különböző konzisztenciájú keverékeknél. A durva szemcsés aggregátumfrakciójú keverékek viszonylag alacsony frekvencián (3000-6000 rezgés percenként), de meglehetősen nagy amplitúdóval rezegnek, míg a nagyfrekvenciás vibrációt finomszemcsés keverékek vibrotömörítésére használják - akár 20 000 rezgés per perc perc, de kis amplitúdóval.
A betontömörítési lehetőségek vázlata: a) mélyvibrátor; b) egy csomag mélyvibrátort; c) rugalmas tengelyű vibrátor; d) felületi vibrátor; e) külső vibrátor; f) a beton szilárdságának változása a tömörítés idejétől függően.
A rezgési mechanizmus olyan működési paraméterei mellett, mint az amplitúdó és a frekvencia, maga a folyamat időtartama is befolyásolja a vibráció következtében létrejövő tömörítés minőségét. Minden típusú betonkeverékhez, folyékonyságától függően, van egy optimális vibrációs tömörítési idő, amely alatt a keverék hatékonyan tömörül, és amely után az energiaköltségek nem állnak arányban a további tömörítés hatékonyságával. Mivel a tömörödés ezen az időn túl is folytatódik, általában nem figyelhető meg a sűrűség növekedése. Ezenkívül fennáll annak a veszélye, hogy a betonkeverék a tulajdonságaiktól függően egyedi komponensekre kezd váladékosodni - például durva szemcséjű adalékanyag-frakcióra és cementiszapra. Ennek eredményeként a betonvégtermék minősége romlik a sűrűség egyenetlen eloszlása és az alkatrészek bizonyos részein a szilárdság csökkenése miatt.
A hosszú távú vibráció gazdaságilag nem kifizetődő, mivel magas energiaköltséggel és a teljes folyamat munkaigényével jár, aminek következtében a formázósor termelékenysége jelentősen csökken.
Az oldat részecskéi természetes rezgésének frekvenciájának egybeesése a vibrokompaktor kényszerrezgéseinek frekvenciájával pozitív hatással van a tömörítés hatékonyságára. De itt figyelembe kell venni azt a tényt, hogy a keverék különböző részecskeméretű frakciók kombinációja - a cementhabarcs mikrométereitől a nagy betonaggregátumokhoz több centiméterig. Ennek megfelelően a leghatékonyabb tömörítési technológia a különböző frekvenciák alkalmazása lesz - az úgynevezett polifrekvenciás tömörítés, mivel a különböző méretű és tömegű részecskék természetes rezgésének gyakorisága eltérő lesz.
A megvalósíthatósági tanulmány elkészítésekor figyelembe kell venni a fentieket - a tömörítési energia növekedésével a tömörítési hatékonyság növekszik, ami egyben csökkenti a folyamat időtartamát és növeli a jövedelmezőséget.
Vibrációs gépek és vibrációs platformok
A betonhabarcs vibrációs tömörítése álló és hordozható eszközökkel történik. A hordozható eszközök alkalmazása az előregyártott betontömörítési technológiában meglehetősen korlátozott. Ipari felhasználásuk főként nagyméretű, nehéz termékek állványokon történő öntésére korlátozódik.
A vibroplatformokat előregyártott vasbeton gyári gyártásához használják olyan típusú üzemekben, amelyek szállítószalagon és áramlási aggregátumokon működnek. A vibrációs platformok tervezési jellemzőinek és típusainak széles választéka létezik - elektromágneses, elektromechanikus, pneumatikus. A rezgések természete szerint - ütős, harmonikus, kombinált. A rezgések formája szerint - körkörös, vízszintes, függőleges. Az asztal tervezési sémái szerint - szilárd felső keret, amely egy vagy több vibrációs tengellyel rendelkező asztalt alkot, vagy különálló vibrációs blokkokból van összeállítva, amelyek összességében egy vibrációs felületet képviselnek egy öntőformával, amelyen keverék található. Az öntőforma habarccsal történő szilárdan rögzítéséhez pneumatikus elektromágnesek vagy mechanikus bilincsek vannak az emelvényasztalon.
Rezgő táblázat diagram méretekkel
A vibrációs platform lapos asztal formájában készül, amelyet rugós támasztékok segítségével az ágyon (kereten) vagy rögzített támaszokon tartanak. A rugók célja, hogy csillapítsák az asztal lengő mozgásait, így megakadályozzák azok becsapódását a támasztékra, ami elkerülhetetlenül tönkremenetelhez vezetne. Az alsó részen egy vibrációs tengely, a felületén található excenterekkel van rögzítve a készülékhez. A tengelyt villanymotor hajtja, az excenterek mozgása az asztal rezgéseit okozza, amelyek azután átkerülnek a beton tömegére és a betonkeverék tömörödését okozzák. A vibrációs platform teljesítményét a teherbírása - a betontermék tömege a formával együtt - mérik, és 2-30 tonna között mozog.
Az előregyártott betont gyártó üzemeket általában 0,3-0,6 mm lengési amplitúdójú, percenkénti 3000 rezgéses frekvenciájú egységes vibrációs platformokkal látják el. Az ilyen platformok jól megbirkóznak a legfeljebb 18 m hosszú és legfeljebb 3,5 m széles szerkezetek tömörítésével.
A vibrációs platformokon történő termékek kialakításakor, különösen, ha porózus adalékanyagon alapuló mereveket használnak, általában súlyokat használnak a beton szerkezetének javítására.
Ha fix formával kell terméket kialakítani, akkor a betonkeveréket a formához rögzített felületi, mélységi és szerelt vibrátorokkal tömörítjük. A vízszintes formákat használó termékek gyártása során merev betonkeverékeket vagy alacsony folyékonyságú keverékeket használnak; függőleges formában (kazettákban) - nagy folyékonyságú keverékek és 80-100 mm-es kúp huzat.
Préselési folyamat
A vasbeton termékek gyártásában a préselést, mint tömörítési módszert ritkán alkalmazzák, annak ellenére, hogy a műszaki adatok szerint nagyon hatékony, mivel lehetővé teszi nagy szilárdságú, nagy sűrűségű beton előállítását nagyon alacsony cement mellett. fogyasztás (100-150 kg / m 3 beton). A módszer elterjedését megakadályozó okok pusztán gazdasági jellegűek. A beton hatékony tömörítésének nyomása 10-15 MPa vagy több, vagyis egy betontermék tömörítéséhez 1 m 2 -enként 10-15 MN (millió Newton) erőt kell kifejteni. Az ilyen teljesítményű préseket csak a hajógyártásban használják hajótestek préselésére, és költségük olyan magas, hogy teljesen kizárja a gazdasági jövedelmezőséget.
centrifugálás
A centrifugálás során a forgó keveréket a forma belső felületéhez tapadva tömörítik. A centrifugálási eljárás eredményeként a betonoldat komponenseinek és a benne lévő víz eltérő sűrűsége miatt a folyadék akár 20-30%-a is eltávolítható belőle, ami nagy szilárdságú betont eredményez.
A centrifugálással könnyen nyerhető nagy sűrűségű, szilárdságú (40-60 MPa) és tartós betontermékekből. Ez a módszer elegendő mennyiségű cementet igényel, hogy a végső betonkeverék nagy kohéziós legyen (400-450 kg/m 3 ). Ellenkező esetben a centrifugális erő hatására több rétegre válik szét, mivel a nagyobb méretű és tömegű szemcsék erősebben nyomódnak a centrifugaforma széléhez, mint a kisebb szemcsék. Ennek a technológiának a segítségével lámpaállványok, elektromos vezetéktartók vagy csövek alakíthatók ki.
Vákuumos oldat
Az evakuálási módszer alkalmazásakor 0,07-0,08 MPa nyomásig légritkítás jön létre, aminek következtében az oldatban részt vevő felesleges levegő és a felesleges víz a nyomáskülönbségek hatására távozik. A beton ebben az esetben elfoglalja a felszabaduló helyet, ami miatt a keverék sűrűsége nő. A vákuum jelenléte nyomó hatással van a betontömegre is, ennek a hatásnak a nagysága megegyezik a vákuumnyomás és a légköri nyomás különbségével. Ennek a hatásnak köszönhetően a keveréket tovább tömörítik.
Az evakuálás és a vibráció kombinációja
Az evakuálási folyamatot előnyösen rezgéssel kombinálják. A vákuumnak kitett betonoldat rezgése során a keverék szilárd komponensei intenzíven kitöltik a légbuborékok és vízcseppek helyén kialakult pórusokat. Technikai szempontból azonban az evakuálásnak van egy jelentős műszaki és gazdasági hátránya - a folyamat hosszú időtartama, amely a vágás méretétől függően körülbelül 1-2 percet vesz igénybe 1 cm vastagságonként.
A kiüríthető réteg vastagsága nem haladja meg a 12-15 cm-t, ezért a nagy méretű szerkezeteket elsősorban azért ürítik ki, hogy a felületi rétegük nagyobb sűrűségű legyen.
Nak nek Kategória:
Talajtömörítő gépek
A gépi talajtömörítés folyamatának fizikai alapja
A talajtömörítés az egyik legfontosabb eleme az út- és vasúti aljzatok, gátak, stb. építési technológiai folyamatának. További szolgáltatásuk e folyamat minőségétől függ. A megfelelő stabilitás elérése érdekében ezen szerkezetek mindegyikénél követelményeket határoznak meg a talaj sűrűségére vonatkozóan. Ugyanakkor a tömörségi fok megállapításánál a szabványos tömörítési módszert veszik alapul, ezért a talajsűrűségre vonatkozó követelményeket általában tömörítési tényezőként, azaz a maximális szabványsűrűség (bmax) töredékében fejezik ki. Az autópályák aljzattalajok felső rétegeinél a sűrűségre vonatkozó követelmények magasak - itt a talaj sűrűsége nem lehet kisebb, mint (0,98-e-1,0) bmax. A töltések alsó rétegeinél 0,956 max. A vasúti töltések talajsűrűsége a vizsgált töltésekben a réteg elhelyezkedésétől függően (0,90-0,98) 6ga-on belül kell, hogy legyen, a gátak talajsűrűsége minden esetben meghatározott. Megjegyzendő, hogy egy ilyen nagy sűrűség elérése, mint a (0,98h-1,0)bmax, jelentős nehézségekkel jár, és csak a használt gépek paramétereinek és működési módjának megfelelő megválasztásával érhető el. Talajtömörítést csak erre a célra tervezett speciális gépekkel szabad végezni. Az erre irányuló földmunkagépek alkalmazására és a töltések eltávolításával való kombinálására tett kísérlet azt mutatta, hogy a talajok sűrűsége nem megfelelő, a tömörítés egyenetlen, ezért ez a módszer csak a talajok előzetes tömörítésére szolgálhat, ami természetesen , megkönnyíti a főgépek munkáját.
A talajnedvesség fontos szerepet játszik a tömörítésben. Minden talajra ható terhelésnek megvan a maga optimális nedvességtartalma, amelynél a legkevesebb gépi munkával érhető el a kívánt sűrűség. Nem megfelelő páratartalom esetén a kívánt sűrűség eléréséhez számos intézkedést kell alkalmazni, amelyek közé tartozik például a tömörített réteg vastagságának csökkentése. Megjegyzendő, hogy a nagyon száraz talajokat egyáltalán nem lehet a kívánt sűrűségre hozni. A szabványos tömörítési módszerrel meghatározott W0 optimális talajnedvesség megfelel a közepes méretű gépek működésének.
A talaj tömörítése hengereléssel, döngöléssel, vibrációval és vibrotampinggal történik.
A talajon gördülve egy dob vagy kerék gördül, melynek érintkezési felületén valamilyen fajlagos nyomás (feszültség) lép fel, ami miatt a talaj visszafordíthatatlan deformációja alakul ki. Az összes görgő működése ezen az elven alapul. Döngöléskor a talajt egy olyan zuhanó tömeg tömöríti, amelyet korábban egy bizonyos magasságba emeltek, és abban a pillanatban, amikor a talajfelszínnel találkozik, meghatározott sebességgel rendelkezik. Így a döngölés a gép munkatestének a talajra való ütközésével jár. Rezgéskor a tömörítő tömeg vagy a tömörített réteg felületén (felületvibrátorok), vagy annak belsejében (mélyvibrátorok) helyezkedik el. Egy speciális mechanizmus hatására rezgőmozgásos állapotba kerül. Ennek a tömegnek a mozgási energiájának egy része a talajrezgésekre fordítódik, amelyeket a részecskék egymáshoz viszonyított elmozdulása okoz, ami sűrűbb tömődést eredményez. Rezgéskor nem válik el a tömeg a tömörített felülettől, vagy nagyon jelentéktelen. Ha a tömeg perturbációi meghaladnak egy bizonyos határt, akkor az elválik a talajfelszíntől, ami a tömeg gyakori talajra csapódásához vezet. Ebben az esetben a vibráció vibronyomtatássá válik. Ez a folyamat az ütközések nagy gyakoriságában különbözik a döngöléstől. A tömeg esésének alacsony magassága ellenére a fejlődő nagy mozgási sebességek miatt az ütközési energia jelentős lehet.
A gép munkatesteinek talajára gyakorolt hatás minden esetben ciklikus terheléssel jár.
Feltételezhető, hogy a talajok optimális nedvességtartalmúak.
A tömörített talajú gépek munkatesteinek érintkezési felületére nehezedő fajlagos nyomás ne legyen nagyobb a szilárdsági határánál, ugyanakkor ne legyen alacsony, mert ellenkező esetben a tömörítési hatás csökken. A legjobb hatást azokban az esetekben érjük el, amikor a tömörítőgépek munkatesteivel érintkező felületeken a fajlagos nyomás egyenlő (0,9-t-1,0) ap (ap - végső szilárdság). Ez alól kivételt képeznek azok a gépek, amelyek munkatesteinek működése a tömörített talajrétegbe való mély behatoláson alapul (bütykös és rácsos hengerek).
Az alakváltozás, és így a tömörítés hatása egyaránt függ a feszültségi állapot változásának sebességétől és a terhelés időtartamától, és ennek következtében az ismétlések számától is.
A gépek munkatestei és a horgok talaja közötti kölcsönhatás jellege olyan, hogy ez a talaj félterének merev kerek bélyeggel való megterhelésére redukálható.
A talajtömörítő gépek működésének hatása attól függ, hogy mennyire helyesen választják meg a tömörített réteg vastagságát. Túl nagy rétegvastagság esetén a szükséges talajsűrűség nem érhető el. Ha túl kicsi a rétegvastagság, csökken a gépek termelékenysége és nő a munka költsége.
N. N. Ivanov professzor elméletileg megállapította, hogy a maximális mélység, amelyre a terhelés hatása még mindig kiterjed, 3,5 cm (a bélyeg dm-es átmérője). Később ezt a következtetést kísérletileg is megerősítették. Ezen a zónán belül, amely még mindig ki van téve a terhelés hatásának, meg kell különböztetni egy másik zónát, ahol a talajtömörödés során a mélységi deformáció még többé-kevésbé egyenletesen oszlik el. Ez a zóna aktívnak nevezhető, mélysége pedig az aktív zóna mélysége. Egy ilyen zóna létrejöttét elősegíti a talajrészecskék és aggregátumok tömeges plasztikus eltolódása, amely a talaj térfogata felett alakul ki, valamint az, hogy a tömörített réteg egy merevebb alapon helyezkedik el, ami a korábban tömörített talaj. A merev alap jelenléte a nyomófeszültségek koncentrálódásához vezet a koncentrált terhelés tengelye mentén, valamint kisebb feszültségeséshez a mélységben, azaz kiegyenlítődésükhöz.
Nem kohéziós talajok esetén a magmélység 1,2-1,5-szer nagyobb.
Az összes talajdeformáció körülbelül 80%-a az aktív zónán belül történik, és csak 20%-a az ezen a zónán kívül eső talajtérfogatban. Ezért a tömörített talajréteg vastagsága nem lehet nagyobb, mint az aktív zóna mélysége, különben nem érhető el a szükséges talajsűrűség.
A tömörített talajréteg optimális vastagsága szorosan összefügg a magmélységgel. Optimális vastagság alatt azt a vastagságot értjük, amelynél a szükséges tömörítési fok a legkisebb mechanikai munkával és a legnagyobb gépi termelékenységgel érhető el. Az aktív zóna mélysége meghatározza a tömörödött talajrétegek optimális vastagságának felső határát. Azokban az esetekben, amikor a talajtömörítés során a szükséges sűrűség nem haladja meg a 0,956max értéket, az optimális rétegvastagság a magmélységgel egyenlőnek vehető. Ugyanakkor az ilyen sűrűség viszonylag könnyen elérhető, és nem igényel nagy számú gépi áthaladást.
A gép munkatestének minimális mérete határozza meg a talajréteg optimális vastagságának maximális értékét, vagyis mintegy tömörödési lehetőségét, amely azonban csak akkor valósulhat meg, ha a talajra nehezedő feszültség talajfelszín közel van a végső szilárdsághoz. Kisebb feszültségeknél az optimális rétegvastagság csökken.
Ha a szükséges talajsűrűség nagy és (0,98-7-1,0) 8max, akkor az optimális rétegvastagság a magmélység felével egyenlő (H0 = 0,5ftn). Ez a sűrűség az aktív zóna mélységével megegyező rétegvastagsággal is elérhető, de ebben az esetben az áthaladások számát 3-szorosára kell növelni ahhoz képest, amikor a szükséges sűrűség max. 0,95 bar. Ezért az ilyen nagy rétegvastagságú talajok tömörítése gazdaságilag veszteségessé válik.
A tömörített talajréteg vastagságának csökkentése az optimális értékhez képest a munkatest azonos méreteinek és a talajfelszínen kialakuló feszültség azonos mértékű megőrzése mellett főszabály szerint túlzott fajlagos munkaráfordítással jár, pl. , az egységnyi talajtérfogat tömörítéséhez szükséges munka.
A (IV. 1) képlet elemzése azt mutatja, hogy a feszültségek (0,5-7-0,6) op-ra való csökkentése gyakorlatilag nem befolyásolja a magmélységet, és ebből következően a tömörített réteg optimális vastagságát. Ugyanakkor meg kell jegyezni, hogy a feszültség bármilyen csökkenése a terhelés alkalmazásának szükséges ismétlésszámának növekedéséhez vezet.
A tömörítés eredményeként nemcsak a talaj kívánt sűrűségét kell elérni, hanem szilárd szerkezetét is. Ez csak egy bizonyos működési mód követésével érhető el. Ez mindenekelőtt a fajlagos nyomásra vonatkozik, amelynek közel kell lennie a talaj végső szilárdságához, de ez utóbbit nem csak a tömörítés végén, hanem a teljes folyamat során sem haladhatja meg. Ha megszegi ezt a szabályt, és azonnal kiválasztja azt a nyomást, amelyet csak a tömörítési folyamat végén kell végrehajtani, amikor a talaj már sűrű és erős, akkor az első menetek során a szerkezet megsemmisül, különösen a felszín közelében. Ez megnehezíti a sűrű és erős szerkezet további kialakítását, és a végül elért sűrűség és szilárdság alacsonyabb lesz, mint a fajlagos nyomás fokozatos növelésével. A szerkezet pusztulását például a hengerek hengerei vagy kerekei előtti erős hullámképződés, illetve a talaj oldalról kidudorodása jelzi.
Így azt mondhatjuk, hogy a gép munkatestének fajlagos nyomása görgők esetén fokozatosan, átjáróról átmenetre, vagy döngölők esetén ütésről fújásra növekedjen. A fajlagos nyomás növelésének ez a folyamata bizonyos mértékig automatikusan megtörténik a gördülés során a pálya mélységének, a tömörítés során az ütközési idő fokozatos csökkentésével. Ugyanakkor a fajlagos nyomások 1,5-2-szeresére nőnek, és szükséges, hogy 3-4-szeresére növekedjenek. Ezért a talajokat két géppel kell tömöríteni - könnyű és nehéz. Könnyű gép az előzetes tömörítésre, egy nehézgép pedig a talaj kívánt sűrűségre hozására szolgáljon. Az előtömörítés alkalmazása körülbelül 25%-kal csökkenti az egy helyen végzett áthaladások vagy ütközések teljes számát. Ha azt is figyelembe vesszük, hogy a folyamat elején könnyebb eszközöket használnak, akkor mindez a tömörítési munka teljes költségének akár 30%-át is megtakarítja.
Nehezebb géppel tömörítésre való átállás nem okozhat éles feszültségnövekedést a talajfelszínen. Ezért a legjobb hatás akkor érhető el, ha a felületre ható feszültség a nehezebb gép első ütközésekor megegyezik a könnyebb gép utolsó ütközésének megfelelő feszültséggel. Pneumatikus gumiabroncsokon görgőkkel történő gördülés esetén ez a követelmény teljesül, ha az előzetes tömörítést henger végzi, amelynek minden egyes kerekére a terhelés kétszer kisebb, mint a fő tömörítésnél, és a gumiabroncs nyomása 1,5-2-szeresére csökken. . A döngölőgépeknél az előtömörítést olyan géppel végezhetjük, amelynek a munkateste fele akkora súlyú, vagy ugyanazzal a géppel, amely a főtömörítést végzi, de a munkatest esési magasságának 4-szeres csökkenésével. Az előtömörítés során az összes szükséges menetszám 30-40%-át kell teljesíteni.
Az előzetes tömörítés mellőzhető, ha a töltés építése során a talajt földmunka- vagy földmunkagépekkel legalább 0,906 ha sűrűségig tömörítették, ami például a kaparómunkák során fordul elő.
Hengerléskor a görgők sebessége bizonyos mértékben befolyásolja. Különböző haladási sebességeknél gyakorlatilag azonos számú menetben érhető el az optimális talajsűrűség. Ezt a következtetést közvetlen vizsgálatok igazolják, és a talajok reológiai tulajdonságaiból következik. Így a 2. részben kimutatták, hogy a feszültségállapot változási sebessége gyakorlatilag csak bizonyos értékekig befolyásolja az irreverzibilis alakváltozás nagyságát. A gördülés során előforduló sebességek már kívül esnek a hatásterületükön.
Ugyanakkor azt tapasztalták, hogy nagy sebességnél kevésbé tartós talajszerkezet alakul ki, ami a talajra ható, valamivel nagyobb nyíróerők magyarázatával magyarázható. Az elvégzett vizsgálatok lehetővé tették egy racionális nagysebességű hengerlési rendszer kialakítását, amelyben a tömörítés minősége nemhogy nem csökken, hanem valamelyest nő is. Ebben az üzemmódban az első és az utolsó két haladást alacsony sebességgel (1,5-2,5 km/h), az összes közbenső haladást pedig nagy sebességgel (8-10 km/h) kell megtenni. Ebben az üzemmódban a teljesítmény körülbelül 2-szeresére nő. A hengerek kialakításának lehetővé kell tennie a talaj ésszerű sebességű tömörítését.
Nak nek Kategória: - Talajtömörítő gépek
A töltésekben a talaj tömörítése különféle típusú hengerek segítségével történik, traktorral együttműködve. Használnak vibrációs döngölőket is, amelyek gyakori oszcillációs mozgásokat adnak át a tömörített talajra, valamint lemez alakú munkatesttel rendelkező döngölőket, amelyek periodikusan esnek a talajra különböző magasságokból.
A tömörítési folyamatot jellemző főbb paramétereket az alkalmazott berendezésektől és a tömörített talaj típusától függően a táblázat tartalmazza. V.5.
Leggyakrabban vontatott hengereket használnak, amelyek közül a pneumatikus görgők a leghatékonyabbak. A talajtömörítést ugyanolyan sorrendben végezzük, mint a feltöltést. A talaj tömörítése a henger egymást követő körkörös behatolásával történik a töltés teljes területén, és minden áttörésnek 0,2 ... 0,3 m-rel át kell fednie az előzőt. Miután befejezte a teljes terület hengerlését, folytassa a következővel: második behatolás
Annak érdekében, hogy a talaj ne omoljon össze a töltés lejtőjének közelében, az első két behatolást a lejtő mentén legalább 1,5 m távolságra kell elvégezni a szélétől. Az ezt követő áttörések 0,5 m-rel a perem felé tolódnak el, és így a töltés szélei gördülnek. Mivel a hengerlést több áttörésben hajtják végre egy pálya mentén, a behatolások első felét kis sebességgel, a másodikat nagyobb sebességgel hajtják végre, mivel a töltés sűrűségének növekedésével a görgő mozgásával szembeni ellenállás jelentősen csökken.
Óránkénti termelékenység, m2/h, tömörítő gépek:
ahol V az átlagos sebesség, m/h; b - az egy menetben tömörített réteg szélessége, m; az előző járat átfedő sávjának a-szélessége, m; Kv - időbeli használati együttható (0,8 - hengereknél és 0,7 - egyéb talajtömörítő gépeknél); n a behatolások száma egy sávon.
A legnehezebb a talaj tömörítése az alapok vagy árkok melléküregeinek feltöltésekor, mivel a munkát szűkös körülmények között végzik. Ezekben az esetekben a talajt az alaptól számított 0,8 m szélességig 15 ... 20 cm-es rétegekkel tömörítik pneumatikus és elektromos döngölőkkel, a felső rétegeket pedig termelékenyebb kis méretű hengerekkel, önmozgó vibrálóval. lemezek stb. (V. 31. kép).
A tömörítési folyamat során ellenőrizni kell az elért talajsűrűséget. Ebből a célból a terepen határozza meg a talaj sűrűségét, amelyet egy 50 ... 100 cm3 térfogatú hengerrel (gyűrűvel) nyernek a töltésekbe fektetett gödrökből.
Ez az ellenőrzési módszer azonban nagyon munkaigényes. A Szojuzdornia által tervezett sűrűségmérőt is használják. Ez az eszköz egy rúdból áll, amelyen egy teher csúszik, amely zuhanáskor (1 J energiával) 1 cm2 (lágy talaj esetén 2 cm2) csúcsba ütközik. A hegy 10 cm-es bemerítéséhez szükséges ütések száma jellemzi a talaj sűrűségét. A gamma-sugárzással áttetsző talajhoz is egy telepítést használnak. Ilyenkor meghatározott távolságra két csövet merítenek a talajba, amelyek közül az egyik radioaktív izotópot, a másik pedig a sugárzás intenzitását mérő kvantumsugárzás-számlálót tartalmaz, amely a két csövet elválasztó talaj sűrűségétől függ.
Talajtömörítés hengerekkel
A hengerlést önjáró és vontatott pneumatikus hengerek végzik. A tömörítési erőt a henger gravitációja és a gördülősíkra (sorra) ható ballasztterhelés (8 MPa-ig) okozó nagy érintkezési feszültségeknek köszönhetjük.
A pneumatikus görgők lehetnek egytengelyesek (10 - 25 tonna súlyúak), kéttengelyes vontatottak (50 tonna súlyig) és félig vontatottak (egy- vagy kéttengelyesek 100 tonnáig). Könnyű hengerekkel a 20-30 cm-es rétegű laza talajok szükséges tömörítése akár 2,5 m munkaszélességgel érhető el A 25-50 tonna súlyú nehéz vontatott pneumatikus hengerek 35-50 cm-es réteggel biztosítják a talajtömörítést 2,5-3,3 m munkaszélességgel a félig vontatott pneumatikus hengerek a leghatékonyabbak, 40 - 50 cm-es réteggel, 2,7 - 2,8 m-es markolatszélességgel biztosítják a kohéziós és nem összefüggő talajok kiváló minőségű tömörítését. ) . A vontatott és önjáró dobgörgők a nagy nyomáseloszlási terület miatt kevésbé hatékonyak, mint a bütykös görgők.
A tömörített talajra nehezedő érintkezési nyomás növelése és a nagy teljesítmény elérése érdekében bütykös vagy rácsos hengereket használnak. A bütykök 200-300 mm hosszú acélprofil csapok, amelyek kerületükön a dobhéjhoz vannak hegesztve. Az ilyen hengereket csak kohéziós talajok tömörítésére használják. A talaj durva kőzetekből történő tömörítésekor bütyök helyett sarok- vagy más acélprofil acélrácsokat hegesztenek a dobok felületére. A bütykös és rácsos hengerek 25-50 cm-es réteggel talajtömörítést biztosítanak, 2,7-3,3 m-es befogási szélességgel, 4-10 menetben a pálya mentén.
Az egyes talajrétegek hengerezését általában spirálgyűrűs minta szerint hajtják végre. A markolat hosszát 250 - 300 m-re feltételezzük.. Kis szélességű markolatokon talajtömörítésnél (a hengerek nehezen forgathatók) elsősorban önjáró dobgörgőket használnak, amelyek oda-vissza mozgásban mozognak.
61. Talajok tömörítése és vibrotömörítése.
A döngöléssel történő talajtömörítés módja a lökésterhelésnek a tömörített talajra való átvitelén alapul. A vibrációs és vibrotamper módszerekkel ellentétben ez a módszer lényegesen nagyobb ütési energiával rendelkezik a munkatest talajjal való ütközésének pillanatában a nagy terhelési sebesség miatt, aminek köszönhetően ez a módszer tömörítést biztosít.
összetartó és nem összefüggő talajok nagy vastagságú rétegekben (gyakorlatilag 2 m-ig). A döngöléssel történő talajtömörítés módszere az ipari építőiparban a legszélesebb körben alkalmazott talajpárnák elhelyezésekor az épületek és építmények alapjai, technológiai berendezések és padlózata alá. Ezt a módszert a süllyedő talajok gödreinek döngölésére is alkalmazzák oszlopos alapok építésénél.
A talajtömörítés kombinált módszere a statikus, vibrációs, vibronyomó és döngölő terhelések talajra gyakorolt hatásának különféle kombinációinak alkalmazásán alapul. Ez a módszer lehetővé teszi minden típusú talaj tömörítését, és főleg sokféle munkához használják.
A vibrációval történő talajtömörítés módja a mechanikai harmonikus rezgések átvitelén alapul a munkatestekről (dobok, kerekek, lemezek, rezgőfejek) a tömörített talajra. A vibrációs módszer felületesre és mélyre oszlik. A talaj felszíni vibrotömörítésének módszerére jellemző, hogy működés közben a tömörítő munkatest a talaj felszínén helyezkedik el, és lengő mozgásokat végezve arra hat. A mélységi módszerrel a tömörítő munkatest üzem közben a talaj belsejében helyezkedik el.
A felületi vibrációs módszer alkalmazást talált nem kohéziós és gyengén kohéziós feltöltőtalajok tömörítésére. A mélyvibrációs módszer hatékonyan alkalmazható homokos talajok, különösen vízzel telített állapotú talajok tömörítésére. A rezgés fő paramétereitől függően, amelyek a rezgések frekvenciája és amplitúdója, a felszíni talajtömörítést szolgáló vibrációs gépek vibro-ütő üzemmódban is működhetnek. Lengésük amplitúdója jóval nagyobb, rezgési frekvenciája kisebb, mint a vibrációs gépeké Ilyenkor a vibrációs gépeket ún.
vibrotamping, a tömörítés módja pedig a vibrotamping. A talaj vibrotampingos tömörítésének módszere az építőiparban, szűk helyeken történő visszatöltések tömörítésekor talált alkalmazásra.
62. Talajok mélytömörítése.
Tömörítés talajkupacokkal, a talaj elmozdulása a radiális tömörítés során a kutak lyukasztása vagy lyukasztása során, majd talajjal való feltöltése és rétegenkénti tömörítés
Mélytömörítési módszerek:
Fizikai
Áztatás
Vízelvezetés (függőleges vízelvezetés)
Mechanikai
Vibrotömörítés
Talajtömörítés cölöpökkel
Talajtömörítés pneumatikus lyukasztókkal
Tömörítés spirális esztrichtel
Tömítés munkatesttel csavaros cölöp formájában
Kombinált
víz + rezgés
(hidrovibrációs tömörítő)
A talaj tömörítésénél gondoskodni kell az optimális nedvességtartalomról, amelynél a legkisebb energiafelhasználás szükséges.
A szekvenciális tömörítéssel a munka sakktábla-mintában történik. Az ütési módszert kutak kialakítására használják. 1 réteg tömörítésének időtartama - 30 mp. 10-15 találattal. Ömlesztett és süllyedő talajokhoz 5-25 m mélységig A felszíni (puffer) réteget tömöríteni kell.
Mélyvibrációs tömörítés - homokos vízzel telített alapokhoz: ömlesztett és hordalékhomok A módszer megvalósítása úgy történik, hogy a vibrációs rudat egymás után a talajba merítjük, miközben a belső üregen keresztül egyidejűleg vizet juttatunk, a vibrációs rúd szükséges bemerítése után a mélyvízellátás leáll, és 4-5 emelés-süllyesztés mellett történik szárazon . Mélytömörítés előáztatással - a talajok deformálhatósága és tömörödése által csökkentett süllyedési tulajdonságok eszközére: lösz, vályog, iszapos talajok magas, legalább 0,2 m / nap szűrési együtthatóval. A tömörítési folyamat a talaj saját tömegének hatására az áztatás során megy végbe, és meglehetősen hosszú, 2-3 hónap. A talajtömörítési idő 3-7 napra történő csökkentése a comflet robbanások miatti további tömörítés alkalmazásával érhető el.
63. Talajtömörítés minőségellenőrzése.
A talajtömörítés minősége a következő legelterjedtebb módszerekkel szabályozható: standard, vágógyűrűs, radioizotópos, szondázás, bélyegzés, viaszolás, lyukas módszer Az egyik vagy másik módszer megválasztása a laboratórium felszereltségétől, a munkavégzés jellegétől függ. szerkezete, a felállítandó töltés térfogata és azok osztálya A tömítések meghatározzák az optimális nedvességtartalmat és a maximális szabványos sűrűséget a SoyuzdorNII készülék segítségével. A töltések talajvázának sűrűségének meghatározására szolgáló gyűrűk vágási módszere a nedves talaj sűrűségének meghatározásán alapul egy 300 ... 400 cm3 kapacitású (d / h = l) fémgyűrű térfogatában, préselve. a tömörödött rétegbe, illetve ennek a talajnak a nedvességtartalma.egyszerűsége miatt a legelfogadhatóbb és elterjedtebb Jelenleg az építőipari gyakorlatban a radioizotópos módszereket alkalmazzák a legszélesebb körben, hiszen a nagy földmunkákon lévő talajterepi laboratóriumokat olyan eszközökkel szerelték fel, amelyek alkalmazza a gammasugárzás és a neutronok elnyelését és szórását A statikus és dinamikus szondázás módszere, mint a talajtömörödés mértékének szabályozásának egyik fajtája töltésekben és feltöltésekben a leghatékonyabb és legegyszerűbb az összes létező szabályozási mód közül A bélyegző bemélyedés módszerrel határozzák meg a talajalapok szilárdságát. Ezt a módszert különösen széles körben alkalmazzák az ipari épületek és alapozások padlója alatti alapok talajtömörödésének minőségének szabályozására A viaszos módszert elsősorban a téli körülmények közötti talajtömörödés szabályozására alkalmazzák rögök A talajba fektetett talaj minősége. a töltéstest akkor tekinthető elfogadhatónak, ha a projektben meghatározottaktól eltérő talajsűrűségű kontrollminták száma nem haladja meg a helyszínen vett összes kontroll minta 10%-át, és a talajváz sűrűsége a telephelyen. a minták nem lehetnek több mint 0,5 g/cm3-rel az előírt (minimális) sűrűség alatt.
64. Talajok zárt fejlesztése punkciós módszerrel.
A szúrás a talaj sugárirányú tömörödése következtében keletkező lyukak kialakulása, amikor egy kúpos hegyű csövet belenyomnak. A bemélyedés hidraulikus emelővel történik. A gödörbe egy hegyes csőkötést helyeznek el, és az emelővel történő igazítás után a rúd löketének hosszára a talajba nyomják. Miután a rúd visszatér eredeti helyzetébe, egy nyomócsövet (ramrod) helyeznek a helyére, és a folyamat megismétlődik. Az első csőcsatlakozó teljes hosszban történő bemélyedésének végén eltávolítják a rácsot, a következő láncszemet leeresztik a gödörbe, amelyet tompahegesztéssel a már földbe zúzotthoz. Ezt követően a hegesztett láncszemet összetörik, és a ciklust elegendő számú alkalommal megismétlik, amíg a szakasz teljes hosszában olyan defekt keletkezik, amely a hagyományos módon nem ásható. Minden ciklusban a cső 150 mm-rel halad előre. Ezt a módszert erősen összenyomható talajokon alkalmazzák, a 100-400 mm átmérőjű csöveknél 3 m-nél mélyebben lyukakat „fúrnak” Enyhén összenyomható talajokon (homok, homokos vályog), a stabilitás biztosítása érdekében. a falaknál a vízszintes erőn kívül keresztirányú és vibrációs hatások alkalmazása szükséges. Ugyanakkor legfeljebb 300 mm átmérőjű lyukakat készítenek.
65. Talaj zárt fejlesztése lyukasztással.
A módszert 500 mm és 1800 mm közötti átmérőjű acélcsövek vagy négyzet (téglalap) keresztmetszetű kollektorok fektetésére alkalmazzák 80 m távolságig A technológia a következő: a csőcsatlakozókat egymás után nyomják a talaj, amelyen belül a talajt csavaros beépítéssel előhívják és eltávolítják. Könnyen erodálódó talajokban az eltávolítás hidromechanikus módszerrel történik (a cső belsejében lévő talajt vízsugárral lemossák, és a pépet szivattyúval kiszivattyúzzák). Gyakran csöveket használnak tokokként a fő csővezetékek elhelyezésére. A vízszintes fúrás módja zárt feltárásban.
A fúrást agyagos talajban 800-1000 mm átmérőjű csővezetékek lefektetésére alkalmazzák 100 m hosszig A cső vége megnövelt átmérőjű vágókoronával van ellátva, a csövet a csőre szerelt motor hajtja. a gödör széle. A cső transzlációs mozgását egy állványemelő jelzi, a hangsúly a gödör hátsó falán van. A csövet belülről kitöltő talaj a lefektetendő csövön keresztül csavaros beépítéssel hidromechanikus módszerrel távolítható el úgy, hogy a cső belsejében lévő talajt vízsugárral kimossuk, majd a pépet szivattyúval kiszivattyúzzuk (könnyen erodálódó helyen talajok) vagy a fogantyújuk meghosszabbításával ellátott sárfogók.
A betonkeverék egyik legfontosabb tulajdonsága, hogy plasztikusan szétterül a saját tömege vagy a rá ható terhelés hatására. Ez határozza meg a legkülönfélébb profilú termékek betonkeverékből történő előállításának viszonylagos egyszerűségét és a különféle módszerek alkalmazásának lehetőségét annak tömörítésére. Ebben az esetben a tömörítés módja és a keverék tulajdonságai (mobilitása vagy folyékonysága) szorosan összefüggenek. Így a merev, nem folyó keverékek erőteljes tömörítést igényelnek, és a belőlük történő termékek kialakításánál intenzív vibrációt vagy vibrációt kell alkalmazni további préseléssel (terheléssel). Vannak más módok is a merev keverékek tömörítésére - tömörítés, préselés, hengerlés.
A mobil keverékek könnyen és hatékonyan tömöríthetők vibrációval. A préselési (préselési) tömörítési módok - préselés, hengerlés, valamint döngölés - alkalmazása nem alkalmas ilyen keverékekre. Jelentős nyomóerők vagy a döngölő gyakran ismétlődő ütései hatására a keverék könnyen kifolyik a szerszám alól, vagy a döngölő kipermetezi.
Az öntött keverékek saját súlyuk hatására tömörödhetnek. A tömörítési hatás fokozása érdekében néha rövid távú vibrációnak vannak kitéve.
Így a betonkeverékek tömörítésének következő módjai különböztethetők meg: vibráció, préselés, hengerlés, döngölés és öntés. Mind műszakilag, mind gazdaságilag a leghatékonyabb a vibrációs módszer. Sikeresen alkalmazzák más módszerekkel kombinálva is.
Mechanikus tömörítés - döngöléssel (vibro-tömörítés! préseléssel (vibro-sajtolás), hengerléssel (vibrohengerlés). örül "A MOZGÓ betonkeverékek tömörítésének mechanikai módszereinek újdonsága a centrifugálás, amelyet üreges cső alakú termékek előállításánál használnak. Jó eredményeket érhetünk el a jó minőségű beton előállításában, ha a keveréket a mechanikai tömörítés során (főleg vibrációval) felszívják, azonban a porszívózás jelentős időtartama jelentősen csökkenti annak műszaki és gazdasági hatását, ezért ez a módszer nem alkalmas széles körben használják az előregyártott betontechnológiában.
Tekintsük röviden a betonkeverékek tömörítésének fenti módszereinek lényegét.
A vibráció a betonkeverék tömörödése, amely gyakran ismétlődő kényszerrezgések átvitelének eredményeként jön létre, amelyek az adalékanyagban rázással fejeződnek ki. A rázás minden pillanatában a betonkeverék részecskéi mintegy szuszpendált állapotban vannak, és kapcsolatuk más részecskékkel megszakad. A nyomóerő ezt követő hatására a saját súlyuk alatt lévő részecskék leesnek, és ezzel egyidejűleg kedvezőbb helyzetet foglalnak el, amelyben kevésbé érhetik őket az ütések. Ez többek között megfelel a legsűrűbb tömítésük állapotának, ami végső soron sűrű betonkeveréket eredményez. A betonkeverék vibráció közbeni tömörödésének második oka az a képesség, hogy a rá ható külső erők hatására átmenetileg folyékony állapotba kerüljön, amit tixotrópiának nevezünk. Folyékony állapotban a betonkeverék vibráció közben terjedni kezd, j alakot vesz fel, és saját tömege hatására tömörödik. У A tömörítés harmadik oka a beton magas műszaki tulajdonságait határozza meg. ,
A betonkeverék nagyfokú tömörítése vibráció hatására | kis teljesítményű berendezésekkel érhető el. Például több köbméter kapacitású betontömegeket tömörítenek vibrátorokkal, amelyek hajtási teljesítménye mindössze 1 ... 1,5 kW.
A betonkeverékek azon képessége, hogy rezgés hatására átmenetileg folyékony állapotba kerüljenek, a keverék mobilitásától és a részecskéi egymáshoz viszonyított mozgási sebességétől függ. A mobil keverékek könnyen folyékony állapotba kerülnek, és alacsony mozgási sebességet igényelnek. De a merevség növekedésével (a mobilitás csökkenésével) a betonkeverék egyre inkább elveszíti ezt a tulajdonságát, vagy ennek megfelelően növelni kell a rezgési sebességet, azaz magasabb energiaköltségekre van szükség a tömörítéshez.
A rezgés közbeni rezgések sebességét v (cm / s) az A amplitúdó és az n rezgési frekvencia szorzata fejezi ki: u \u003d An
Tányérok. A gyakorlat azt mutatja, hogy a mobil betonkeverékek hatékonyan tömöríthetők 0,3 ... 0,35 mm oszcillációs amplitúdóval,
És kemény - 0,5 ... 0,7 mm.
A vibrotömörítés minőségét nemcsak a vibrációs mechanizmus paraméterei (frekvencia és amplitúdó), hanem a rezgés időtartama is befolyásolja. Minden betonkeverékhez, mobilitásától függően, megvan a maga optimális vibrotömörítési időtartama, ameddig a keverék hatékonyan tömörül, és amelyen túl az energiaköltség sokkal nagyobb mértékben nő, mint a keverék tömörítése. A további tömörítés egyáltalán nem eredményez sűrűségnövekedést. Ezenkívül a túlzottan elhúzódó vibráció a keverék delaminációjához, különálló komponensekre - cementhabarcsra és nagy adalékszemcsékre való szétválásához vezethet, ami végső soron a termék egyenetlen sűrűségéhez és az egyes részek szilárdságának csökkenéséhez vezet.
A hosszú távú vibráció természetesen gazdasági szempontból is veszteséges: nőnek az energiaköltségek és a munkaintenzitás, csökken a formázósor termelékenysége.
A vibrotömörítés I intenzitása (cm2/s3) a rezgés legrövidebb időtartamával kifejezve a rezgési mechanizmus működésének fő paramétereitől is függ - a rezgések frekvenciájától és amplitúdójától, amelyeket a sebesség és a gyorsulás kölcsönös kombinációjának figyelembevételével alkalmazunk. oszcillációk: I = A2 / n3.
A vibrotömörítés intenzitása is nő, ha a kényszerrezgések frekvenciája megegyezik a természetes rezgések frekvenciájával. Tekintettel arra, hogy a betonkeverék részecskemérete széles (a cementnél több mikrométertől a durva adalékanyagnál több centiméterig), és ennek megfelelően a természetes rezgések gyakoriságában mutatkozó különbségek, a keverék legintenzívebb tömörítése lesz. amikor a rezgésmódot különböző frekvenciák jellemzik. Tehát volt egy javaslat a többfrekvenciás vibráció használatára.
Ezeket a tényezőket figyelembe kell venni a termék öntési műveleteinek műszaki és gazdasági értékelése során. A fentiekből következik, hogy a tömörítési energia növekedésével nő a tömörítési hatásfok, csökken a tömörítés időtartama és nő a formázósor termelékenysége. Így a betonkeverék tulajdonságainak, a formázósor teljesítményének műszaki-gazdasági elemzése alapján választhatja meg a vibrotömörítő mechanizmusok teljesítményét.
A betonkeverék vibrációs tömörítését hordozható és álló vibrációs mechanizmusok végzik. A hordozható vibrátorok használata előregyártott betonban korlátozott. Főleg nagy méretű, masszív termékek állványokon történő kialakításánál használják őket.
Működő gyárakban az előregyártott beton technológiájában
Az áramlási aggregátum és a szállítószalag sémák szerint vibrációs platformokat használnak. A vibrációs platformokat a vibrátorok sokféle típusa és kialakítása különbözteti meg - elektromechanikus, elektromágneses, pneumatikus; a rezgések természete - harmonikus, sokk, kombinált; rezgések formája - körkörös irányított - függőleges, vízszintes; az asztal tervezési sémái - szilárd felső kerettel, amely egy vagy két vibrációs tengellyel rendelkező asztalt alkot, és külön rezgőblokkokból van összeállítva, általában egy közös vibrációs síkot képvisel, amelyen a betonkeverékkel ellátott forma található.
Az űrlapnak az emelvényasztalhoz való rögzítésének szilárdsága érdekében speciális mechanizmusok állnak rendelkezésre - elektromágnesek, pneumatikus vagy mechanikus bilincsek.
A vibrációs platform (11.1. ábra) egy lapos asztal, amely rugós támasztékokon keresztül rögzített támasztékokon vagy kereten (kereten) van megtámasztva. A rugókat úgy tervezték, hogy csillapítsák az asztal rezgését, és ezáltal megakadályozzák azok becsapódását a támasztékokra, különben tönkremennek. Az alsó részben egy vibrációs tengely, rajta elhelyezett excenterekkel mereven rögzítve van az asztalhoz. Amikor a tengely forog a villanymotorról, az excenterek gerjesztik az asztal rezgéseit, amelyek aztán a betonkeverékkel továbbadódnak a formába, ennek eredményeként az összetömörödik. A vibrációs platform teljesítményét a teherbírása (a termék tömege a formával együtt) becsüli meg, amely 2...30 tonna.
Az előregyártott vasbeton üzemek egységes vibrációs platformokkal vannak felszerelve, 3000 ford./perc forgási frekvenciával és 0,3 ... 0,6 mm amplitúdóval. Ezek a vibrációs platformok akár 18 m hosszú és 3,6 m széles szerkezetek merev betonkeverékeit is jól tömörítik.
Termékek vibrációs platformokon történő alakításakor, különösen merev betonkeverékekből porózus adalékanyagokon, a beton szerkezetének javítása érdekében súlyokat használnak - statikus,
Vibrációs, pneumatikus, vibropneumatikus. A tömeg értéke a betonkeverék tulajdonságaitól függően 2 ... 5 kPa.
A termékek fix formába történő öntésekor a betonkeveréket felületi, mély és szerelt vibrátorokkal tömörítik, amelyeket a formához rögzítenek. A vízszintes formájú termékek gyártása során merev vagy lassan mozgó betonkeverékeket használnak, és függőlegesen öntve
egyes formák (kazettákban) 8 ... 10 cm-es kúpos ostromú mobil keverékeket használnak.
Az F préselés egy ritkán használt módszer a betonkeverékek tömörítésére az előregyártott betontechnológiában, bár a műszaki mutatók szempontjából rendkívül hatékony, lehetővé téve nagy sűrűségű és szilárdságú beton előállítását minimális cementfelhasználással (100 ... 150). kg / m3 beton). A préselési mód elterjedését kizárólag gazdasági okok nehezítik. Az a nyomónyomás, amelynél a beton hatékonyan tömörödni kezd, 10 ... 15 MPa és magasabb. Így a termék 1 m2-enkénti lezárásához 10 ... 15 MN terhelést kell alkalmazni. Ilyen teljesítményű préseket használnak a technológiában, például hajótestek préselésénél, de költségük olyan magasnak bizonyul, hogy teljesen kizárja az ilyen prések gazdasági megvalósíthatóságát.
Az előregyártott betontechnológiában a préselést kiegészítő mechanikai terhelésként alkalmazzák a betonkeverékre annak vibrációja során. Ebben az esetben a préselési nyomás szükséges értéke nem haladja meg az 500 ... 1000 Pa-t. Technikailag ez a nyomás a betonkeverék egyes részecskéinek kényszermozgása következtében statikusan alkalmazott terhelés hatására jön létre.
Különbséget kell tenni a lapos- és profilbélyegekkel történő préselés között. Ez utóbbiak átadják betonkeverék-profiljukat. Így készülnek a lépcsősorok, bizonyos típusú bordás panelek. Ez utóbbi esetben a préselési módszert bélyegzésnek is nevezik. A kölcsönzés a préselés egy fajtája. Ebben az esetben a préselési nyomás a betonkeverékre csak a henger egy kis részén keresztül jut át, ami ennek megfelelően csökkenti a préselés szükségességét. De itt különös jelentőséget kap a betonkeverék plasztikus tulajdonságai, tömegének koherenciája. Nem megfelelő kohézió esetén a keveréket a nyomóhenger eltolja és megtöri. Centrifugálás - a betonkeverék tömörítése A forgás során fellépő centrifugális erők hatására. Erre a célra centrifugákat használnak (11.2. ábra), amelyek egy cső alakú szakasz, amelyet a tömörítés során 600 ...
forgás közben gördül, a forma belső felületéhez nyomódik és egyben tömörödik. A betonkeverék és a VÍZ szilárd összetevőinek eltérő sűrűsége következtében a betonkeverékből akár 20 ... 30% víz távozik, ami hozzájárul a nagy sűrűségű beton előállításához.
A centrifugálási módszer viszonylag könnyen lehetővé teszi nagy sűrűségű, szilárdságú (40 ... 60 MPa) és tartós termékek előállítását betonból. Ugyanakkor a nagy kohéziós betonkeverék előállításához nagy mennyiségű (400 ... 450 kg / m3) cementre van szükség, különben a keverék centrifugális erők hatására kis és nagy szemcsékre rétegződik, mivel ez utóbbiak hajlamosak lesznek nagy erővel a formafelülethez tapadni. Centrifugálással készülnek a csövek, villanyvezeték oszlopok, lámpaállványok. Vákuumozáskor a betonkeverékben akár 0,07 ... 0,08 MPa vákuum keletkezik, és a betonkeverékből az elkészítésében és a formába fektetésében részt vevő levegőt, valamint némi vizet eltávolítanak a betonkeverékből. ez a vákuum: a felszabaduló helyeket szilárd részecskék foglalják el, és a betonkeverék megnövekedett sűrűségűvé válik. Ezenkívül a vákuum jelenléte a vákuumértékkel megegyező légköri nyomású nyomást gyakorol a betonkeverékre. Hozzájárul a betonkeverék tömörödéséhez is. A porszívózást általában vibrációval kombinálják. A vákuumnak kitett betonkeverék vibrálása során a légbuborékok és a víz helyén a vákuumozás során keletkező pórusok szilárd komponensei intenzíven kitöltődnek. Technikai szempontból azonban a porszívózásnak van egy fontos műszaki és gazdasági hátránya, nevezetesen: hosszú folyamatidő - 1 ... 2 perc minden 1 cm-es termékvastagságra, a betonkeverék tulajdonságaitól és a szelvény méretétől függően. . A porszívózható réteg vastagsága nem haladja meg a 12...15 cm-t, ennek eredményeként elsősorban a masszív szerkezeteket vetik alá porszívózásnak, hogy a felületi réteg különösen nagy sűrűségét adja. Az előregyártott vasbeton technológiájában a porszívózást gyakorlatilag nem használják. wj
A betonszerkezetek felállításának technológiája magában foglalja a betonkeverék elkészítését és annak tömörítését. Vannak esetek, amikor az oldat összekeverésekor üregek jelennek meg benne, amelyek megzavarhatják a szerkezetet és csökkenthetik a sűrűségét. Emiatt repedések jelennek meg a termékben, ami végső soron a betonszerkezetek tönkremeneteléhez vezethet. A tömörítési folyamat során a szakemberek eltávolítják az oldatból a levegőt és a felesleges folyadékot, ami miatt az sűrűbbé válik. Így a termék erősebb és tartósabb.
A beton tömörítése a cementkeverékek lerakásának legfontosabb lépése. A beton együtthatója és a termék fő jellemzői attól függnek, hogy milyen gondosan hajtják végre ezt a műveletet. Az eljárás során a szakemberek a betonfelületet manuálisan vagy mechanikus eszközök segítségével dolgozzák fel, eltávolítják az üregeket. Ez lehetővé teszi a betonoldat egységességének elérését, a készítmény tapadásának növelését más szerkezeti elemekkel.
Módokon
Az építők a következő típusú eszközöket használják a keverék tömörítésekor:
- felület (a cement felső rétegéhez);
- mély (nagy betonszerkezetek);
- külső (a tömörítés elé telepítve egy fa zsaluzat vagy cementhabarcsos tartály szélétől);
- vibrációs platformok (szakosodott vállalkozásoknál használják).
A cementhabarcs tömörítésének többféle módja van:
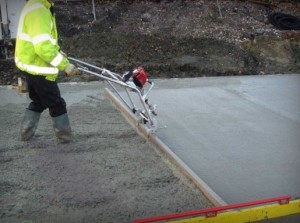
egyéb módszerek
Egyéb tömítési módszerek a következők:
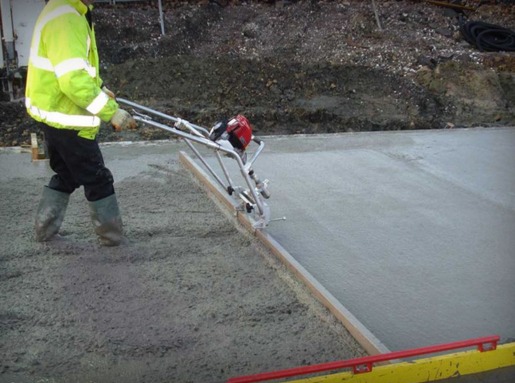
A cement összetételének egyenletes tömörítése érdekében a következő ajánlásokat kell követni:
- A fa zsaluzat beépítése során ügyelni kell az alkatrészek megbízható rögzítésére. A szerkezeti elemeken nem lehetnek hézagok (repedéseken keresztül a betonoldat kinyomható). Szükséges, hogy a zsaluzat polírozott és sima legyen, különben horpadásokat hagy a terméken. Ezenkívül a szerkezet testében ezt követően üregek keletkezhetnek.
- A fa vagy rétegelt lemez zsaluzat részleteit, beleértve az ékeket is, biztonságosan rögzíteni kell, hogy a táblák ne mozduljanak el.
- A kompozíció vibrotömörítésekor a vibrációs esztrich helyzetét időszakonként meg kell változtatni, különben az oldat inhomogén lesz, üregek képződnek.
- A szakértők azt tanácsolják, hogy ne töltsön sok időt a munkával, mert ez rétegvesztést okozhat, ami annak köszönhető, hogy az alján nagy kavicsot ütnek le, és csak a cementhabarcs halmozódik fel a tetején.
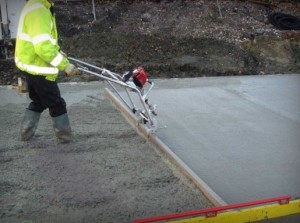
Mivel a felületi vibrációs eszközök használata nem teszi lehetővé a sűrűség fokának vizuális meghatározását, az építési munkák során gyakran használnak kiegészítő szert a kompozíció szilárdságának biztosítására. Ehhez az építők nagy plaszticitású megoldást adnak a meglévő kompozícióhoz. Emiatt megnő a termék delaminációjának kockázata. Az ilyen hátrányok elkerülése érdekében tanácsos növelni a cement mennyiségét.
Tömörítési tényező
A beton összetételének minősége egy fontos kritérium alapján értékelhető. A tömörítési tényezőről van szó. Az együtthatót a következőképpen határozzuk meg: kiszámítjuk a kész keverék fajsúlyának és a belső légbuborékok hiányában kapott érték arányát. Tehát az együttható elfogadható értéke 1. A mutató a beton tömörítésének különböző módjaival érhető el, a módszerek kiválasztása közvetlenül az összetételtől, a céltól és a frakcióktól függ. Az automatizált vibrációs esztrichek jelentősen javítják a megoldás minőségét.
Mitől függ az arány?
Ezt a mutatót a kompozíció részletessége, valamint a betonozandó tárgy határozza meg, legyen szó vak területekről, pályákról vagy utakról.
megállapításait
A tapasztalt építők azt állítják, hogy a szerkezet stabilitása és tartóssága attól függ. Ezt figyelembe kell venni, ha azt szeretné, hogy a termék egy évnél tovább szolgáljon. Az időben megtett intézkedések segítenek tovább növelni a szerkezet védelmét a sérülésekkel szemben, és pénzt takarítanak meg a helyreállítási munkákon. Az univerzális vibrációs eszközök lehetővé teszik, hogy kiváló minőségű betont kapjon. Az építési munkák elvégzése előtt előzetesen konzultálnia kell szakértőkkel, és ki kell választania a szükséges felszerelést. Az ergonómikus kialakítású vibrátorok lehetővé teszik az építők számára a cement tömörítését a legkülönfélébb körülmények között.
Kis mennyiségű építési munka elvégzéséhez a szakemberek legfeljebb öt kilogramm súlyú használatát javasolják. Nagyobb munkákhoz az építők nagy szerszámokat használnak a beton hatékony tömörítésére a nagy előlappal végzett gyártás során.