Fizični temelji procesa strojnega zbijanja tal. Fizikalne metode površinskega zbijanja tal
Vpliv amplitude in frekvence nihanja
Frekvenca nihanja delcev in njihova amplituda sta medsebojno povezani, kar omogoča uporabo različnih načinov vibracij v industrijskih pogojih za mešanice različnih konsistence. Mešanice z frakcijo grobozrnatega agregata vibrirajo z relativno nizko frekvenco (3000-6000 tresljajev na minuto), vendar s precej veliko amplitudo, medtem ko se visokofrekvenčna vibracija uporablja za vibrokompaktiranje drobnozrnatih mešanic - do 20.000 vibracij na minuto. minuto, vendar z majhno amplitudo.
Shema možnosti stiskanja betona: a) globok vibrator; b) paket globokih vibratorjev; c) vibrator s gibljivo gredjo; d) površinski vibrator; e) zunanji vibrator; f) sprememba trdnosti betona glede na čas njegovega zbijanja.
Poleg takih delovnih parametrov vibracijskega mehanizma, kot sta amplituda in frekvenca, na kakovost zbijanja kot posledica vibracij vpliva tudi trajanje samega procesa. Za vse vrste betonskih zmesi, odvisno od njihove tekočnosti, obstaja optimalen čas zbijanja z vibracijami, v katerem se mešanica učinkovito stisne in po katerem so stroški energije nesorazmerni z učinkovitostjo nadaljnjega zbijanja. Ker se zbijanje nadaljuje po tem času, na splošno ni opaziti povečanja gostote. Poleg tega obstaja nevarnost, da se bo betonska mešanica začela razslojevati na posamezne sestavine, odvisno od njihovih lastnosti - na primer frakcija grobozrnatega agregata in cementna suspenzija. Posledično se bo kakovost končnega betonskega izdelka zmanjšala zaradi neenakomerne porazdelitve gostote in zmanjšane trdnosti na določenih delih njegovih delov.
Dolgotrajne vibracije so ekonomsko nerentabilne, saj so povezane z visokimi stroški energije in mukotrpnostjo celotnega procesa, zaradi česar se produktivnost livarske linije znatno zmanjša.
Sovpadanje frekvence naravnih nihanj delcev raztopine s frekvenco prisilnih vibracij vibrokompaktorja pozitivno vpliva na učinkovitost zbijanja. Toda tukaj je treba upoštevati dejstvo, da je mešanica kombinacija različnih frakcij z različnimi velikostmi delcev - od mikrometrov za cementno malto do nekaj centimetrov za velike betonske agregate. V skladu s tem bo najučinkovitejša tehnologija stiskanja uporaba različnih frekvenc - tako imenovano polifrekvenčno zbijanje, saj bo frekvenca naravnih nihanj za delce različnih velikosti in mas različna.
Pri izdelavi študije izvedljivosti je treba upoštevati navedeno – s povečanjem energije stiskanja se poveča učinkovitost stiskanja, kar tudi skrajša trajanje procesa in poveča donosnost.
Vibracijski stroji in vibracijske ploščadi
Vibrokompaktiranje betonske malte se izvaja tako s stacionarnimi kot prenosnimi sredstvi. Uporaba prenosnih sredstev v tehnologiji stiskanja montažnega betona je precej omejena. Njihova industrijska uporaba je v glavnem omejena na oblikovanje velikih, težkih izdelkov na stojnicah.
Vibroplatforme se uporabljajo v tovarniški proizvodnji montažnega armiranega betona tistih vrst obratov, ki delujejo po transportnih in pretočnih agregatih. Obstaja veliko različnih oblikovnih značilnosti in vrst vibracijskih platform - elektromagnetnih, elektromehanskih, pnevmatskih. Po naravi vibracij - tolkalne, harmonične, kombinirane. Glede na obliko tresljajev - krožno usmerjeno, vodoravno, navpično. Po načrtovalnih shemah mize - trden zgornji okvir, ki tvori mizo z eno ali več vibracijskimi gredmi ali sestavljeni iz ločenih vibracijskih blokov, ki kot celota predstavljajo eno vibracijsko površino s kalupom z mešanico, ki se nahaja na njej. Za trdno pritrditev kalupa z malto so na mizi ploščadi predvideni pnevmatski elektromagneti ali mehanske sponke.
Diagram vibrirajoče mize z dimenzijami
Vibracijska ploščad je izdelana v obliki ravne mize, ki je podprta z vzmetnimi nosilci na postelji (okvir) ali na fiksnih nosilcih. Namen vzmeti je blažiti nihajne premike mize in s tem preprečiti njihov vpliv na oporo, kar bi neizogibno vodilo v uničenje. V spodnjem delu je na napravo pritrjena vibrirajoča gred z ekscentri, ki se nahajajo na njeni površini. Gred poganja elektromotor, gibanje ekscentrikov povzroča tresljaje mize, ki se nato prenesejo na maso betona in povzročijo zbijanje betonske mešanice. Moč vibracijske ploščadi se meri z nosilnostjo - maso betonskega izdelka skupaj z obliko - in se giblje od 2 do 30 ton.
Obrati za proizvodnjo montažnega betona so običajno opremljeni z enotnimi vibracijskimi platformami z amplitudo nihanja 0,3-0,6 mm in frekvenco 3000 nihanj na minuto. Takšne ploščadi se dobro spopadajo z zbijanjem konstrukcij z dolžino do 18 m in širino do 3,5 m.
Pri oblikovanju izdelkov na vibrirajočih platformah, še posebej, če se uporabljajo togi na osnovi poroznih agregatov, se uteži običajno uporabljajo za izboljšanje strukture betona.
Če je treba izdelek oblikovati s fiksno obliko, se betonska mešanica stisne s površinskimi, globinskimi in nameščenimi vibratorji, pritrjenimi na obliko. Pri izdelavi izdelkov z uporabo horizontalnih oblik se uporabljajo toge betonske mešanice ali mešanice z nizko tekočnostjo; v navpičnih oblikah (kasete) - mešanice z visoko tekočnostjo in ugrezom stožca 80-100 mm.
Postopek stiskanja
Stiskanje kot metoda zbijanja pri izdelavi armiranobetonskih izdelkov se redko uporablja, kljub dejstvu, da je po tehničnih indikacijah zelo učinkovito, saj omogoča pridobivanje betona visoke trdnosti z visoko gostoto pri zelo nizki ceni cementa. poraba (100-150 kg / m 3 betona). Razlogi, ki preprečujejo širjenje te metode, so izključno ekonomske narave. Tlak, pri katerem se beton učinkovito stisne, je 10-15 MPa ali več, to pomeni, da je treba za stiskanje betonskega izdelka uporabiti silo, ki je enaka 10-15 MN (milijonov Newtonov), za vsak 1 m 2. Stiskalnice s takšno močjo se uporabljajo samo v ladjedelništvu za stiskanje ladijskih trupov, njihova cena pa je tako visoka, da pri uporabi popolnoma izključuje ekonomsko donosnost.
centrifugiranje
Med centrifugiranjem se vrteča se zmes stisne z oprijemom na notranjo površino kalupa. Zaradi postopka centrifugiranja se zaradi različne gostote sestavin betonske raztopine in vode, ki jo vsebuje, iz nje odstrani do 20-30% tekočine, kar povzroči beton visoke trdnosti.
Centrifugiranje omogoča enostavno pridobivanje iz betonskih izdelkov z visoko gostoto, trdnostjo (40-60 MPa) in vzdržljivostjo. Ta metoda zahteva zadostno količino cementa, tako da ima končna betonska mešanica visoko kohezivnost (400-450 kg/m 3 ). V nasprotnem primeru bo pod delovanjem centrifugalne sile prišlo do ločitve na več plasti, saj bodo zrna večje velikosti in mase bolj pritisnjena ob rob centrifugalnega kalupa kot zrna manjše velikosti. S pomočjo te tehnologije se oblikujejo stojala za svetilke, nosilce daljnovodov ali cevi.
Vakuumska raztopina
Pri uporabi metode evakuacije se ustvari redčenje zraka do tlaka 0,07-0,08 MPa, zaradi česar se odvečni zrak, vključen v raztopino, in odvečna voda odstranita pod vplivom tlačnih razlik. Beton zaseda v tem primeru izpraznjeni prostor, zaradi česar se gostota mešanice poveča. Prisotnost vakuuma ima tudi pritisk na betonsko maso, velikost tega učinka je enaka razliki med vakuumskim in atmosferskim tlakom. Zaradi tega učinka se zmes dodatno stisne.
Kombinacija evakuacije z vibracijami
Postopek evakuacije je zaželeno kombinirati z vibracijami. Med vibriranjem betonske raztopine, ki je izpostavljena vakuumu, trdne komponente mešanice intenzivno zapolnjujejo pore, ki nastanejo namesto zračnih mehurčkov in vodnih kapljic. Vendar ima evakuacija s tehničnega vidika pomembno tehnično in ekonomsko pomanjkljivost - dolgotrajnost postopka, ki glede na velikost reza traja približno 1-2 minuti za vsak 1 cm debeline.
Debelina sloja, ki ga je mogoče evakuirati, ne presega 12-15 cm, zato se konstrukcije velikih velikosti v glavnem evakuirajo, da bi njihov površinski sloj dobil večjo gostoto.
Za kategorija:
Stroji za zbijanje tal
Fizikalne osnove procesa zbijanja tal s stroji
Zbijanje tal je eden najpomembnejših elementov tehnološkega procesa gradnje podlag za ceste in železnice, jezov ipd. Od kakovosti tega procesa je odvisno njihovo nadaljnje servisiranje. Da bi dosegli zadostno stabilnost, so za vsako od teh struktur določene zahteve glede gostote njihovih tal. Hkrati se kot osnova za ocenjevanje stopnje zbitosti uporablja standardna metoda zbijanja, zato so zahteve po gostoti tal običajno izražene kot faktor zbitosti, to je v deležih največje standardne gostote (bmax). Za zgornje plasti podlage avtocest so zahteve po gostotah visoke - tukaj gostota tal ne sme biti nižja od (0,98-e-1,0) bmax. Za nižje plasti nasipov se lahko zmanjša na 0,956max. Gostote tal železniških nasipov, odvisno od lege plasti v obravnavanih nasipih, naj bodo znotraj (0,90-0,98) 6ga, gostote tal jezov pa se določijo v vsakem posameznem primeru. Opozoriti je treba, da je doseganje tako visoke gostote, kot je (0,98h-1,0)bmax, povezano s precejšnjimi težavami in ga je mogoče doseči le s pravilno izbiro tako parametrov uporabljenih strojev kot njihovega načina delovanja. Zbijanje tal je treba izvajati samo s posebnimi stroji, namenjenimi za ta namen. Poskus uporabe zemeljskih strojev za to in kombiniranja tega postopka z odstranjevanjem nasipov je pokazal, da je gostota tal nezadostna in zbijanje neenakomerno, zato lahko ta metoda služi le za predhodno zbijanje tal, kar seveda , olajša delo glavnih strojev.
Vlaga tal igra pomembno vlogo pri zbijanju. Vsaka obremenitev, ki deluje na tla, ima svojo optimalno vsebnost vlage, pri kateri je z najmanj mehanskim delom mogoče doseči zahtevano gostoto. V primeru nezadostne vlažnosti je za doseganje zahtevane gostote potrebno izvesti številne ukrepe, ki vključujejo na primer zmanjšanje debeline stisnjene plasti. Upoštevati je treba, da zelo suha tla sploh ne moremo doseči zahtevane gostote. Optimalna vlažnost tal W0, ki jo določimo s standardnim načinom zbijanja, ustreza delovanju srednje velikih strojev.
Tla se stisnejo z valjanjem, nabijanjem, vibracijami in vibrotampanjem.
Pri valjanju po tleh se kotali boben ali kolo, na kontaktni površini katerega je določen specifični pritisk (napetost), zaradi česar se razvije nepopravljiva deformacija tal. Na tem principu temelji delovanje vseh valjev. Pri nabijanju tla stisne padajoča masa, ki je bila predhodno dvignjena na določeno višino in v trenutku, ko se sreča s površino tal, ima določeno hitrost. Tako je nabijanje povezano z udarcem delovnega telesa stroja na tla. Pri vibriranju se stiskalna masa nahaja na površini stisnjene plasti (površinski vibratorji) ali znotraj nje (globoki vibratorji). Zaradi posebnega mehanizma se spravi v stanje nihajnega gibanja. Del kinetične energije te mase se porabi za vibracije tal, ki so posledica relativnih premikov njenih delcev, kar ima za posledico njihovo gostejše pakiranje. Pri vibriranju ni ločitve mase od stisnjene površine oziroma je zelo nepomembno. Če motnje mase presežejo določeno mejo, se ta loči od površine tal, kar bo povzročilo pogoste udarce mase ob tla. V tem primeru se bo vibracija spremenila v vibrotamping. Ta postopek se od nabijanja razlikuje po visoki pogostosti udarcev. Kljub nizki višini padca mase je zaradi razvijajočih se velikih hitrosti gibanja lahko udarna energija pomembna.
V vseh primerih je vpliv na tla delovnih teles stroja povezan s ciklično obremenitvijo.
Predpostavlja se, da imajo tla optimalno vsebnost vlage.
Specifični tlaki na kontaktnih površinah delovnih teles strojev z zgoščenimi tlemi ne smejo biti višji od njihovih meja trdnosti, hkrati pa ne smejo biti nizki, saj se sicer zmanjša učinek zbijanja. Najboljši učinek bo dosežen v primerih, ko so specifični tlaki na kontaktni površini z delovnimi telesi stiskalnih strojev (0,9-t-1,0) ap (ap je natezna trdnost). Izjema od tega pravila so stroji, katerih delovanje delovnih teles temelji na njihovem globokem prodiranju v stisnjeno plast zemlje (odmikalni in rešetkasti valji).
Deformacija in s tem učinek zbijanja sta odvisna tako od hitrosti spreminjanja napetostnega stanja kot od trajanja obremenitve in posledično od števila ponovitev njene uporabe.
Narava interakcije delovnih teles strojev s tlemi kavljev je taka, da jo je mogoče zmanjšati na shemo obremenitve polovice tal s togim okroglim žigom
Učinek delovanja strojev za zbijanje tal je odvisen od tega, kako pravilno je izbrana debelina stisnjenega sloja. Pri preveliki debelini plasti ni dosežena zahtevana gostota tal. Če so debeline plasti premajhne, se produktivnost strojev zmanjša in stroški dela se povečajo.
Profesor N. N. Ivanov je teoretično ugotovil, da je največja globina, do katere še sega delovanje bremena, 3,5 cm (dm-premer žiga). Kasneje je bil ta sklep eksperimentalno potrjen. Znotraj te cone, ki je še vedno podvržena delovanju obremenitve, je treba razlikovati še eno cono, kjer se v procesu zbijanja tal deformacija v globino porazdeli še bolj ali manj enakomerno. To območje lahko imenujemo aktivno, njegova globina pa globina aktivne cone. Ustvarjanje takšne cone olajšujejo množični plastični premiki talnih delcev in agregatov, ki se razvijejo po volumnu tal, ter dejstvo, da je zgoščena plast nameščena na bolj togi podlagi, ki je predhodno zbita tla. Prisotnost toge podlage vodi do koncentracije tlačnih napetosti vzdolž osi zgoščene obremenitve, pa tudi do manjšega globinskega padca napetosti, to je do njihove izravnave.
Pri nekohezivnih tleh je globina jedra 1,2-1,5-krat večja.
Približno 80 % vseh deformacij tal se zgodi znotraj aktivne cone, le 20 % pa se zgodi v volumnu tal, ki se nahaja zunaj tega območja. Zato debelina stisnjenega sloja zemlje ne sme biti večja od globine aktivne cone, sicer ne bo dosežena zahtevana gostota tal.
Optimalna debelina stisnjene plasti zemlje je tesno povezana z globino sredice. Pod optimalno debelino se razume taka debelina, pri kateri je dosežena zahtevana stopnja zbijanja z najmanj mehanskega dela in največjo produktivnostjo stroja. Globina aktivne cone določa zgornjo mejo optimalnih debelin stisnjenih plasti tal. V primerih, ko zahtevana gostota med zbijanjem tal ne presega 0,956max, se lahko optimalna debelina plasti vzame za enako globino sredice. Hkrati se taka gostota doseže relativno enostavno in ne zahteva velikega števila strojnih prehodov.
Najmanjša velikost delovnega telesa stroja v smislu določa največjo vrednost optimalne debeline talnega sloja, torej tako rekoč potenciala zbijanja, ki pa ga je mogoče uresničiti le, če je obremenitev na površina tal je blizu končne trdnosti. Pri manjših napetostih se bo optimalna debelina plasti zmanjšala.
Če je zahtevana gostota tal visoka in znaša (0,98-7-1,0) 8max, potem je optimalna debelina plasti enaka polovici globine jedra (H0 = 0,5ftn). To gostoto je mogoče doseči tudi z debelino sloja, ki je enaka globini aktivne cone, vendar je v tem primeru treba število prehodov povečati za faktor 3 v primerjavi s primerom, ko je zahtevana gostota 0,95 bar max. Zato postane zbijanje tal s tako veliko debelino plasti ekonomsko nerentabilno.
Zmanjšanje debeline stisnjene plasti tal v primerjavi z optimalno vrednostjo ob ohranjanju enakih dimenzij delovnega telesa in enake velikosti napetosti, ki se razvije na površini tal, praviloma pomeni preveliko porabo specifičnega dela, t.j. , delo, potrebno za stiskanje enote prostornine tal.
Analiza formule (IV. 1) kaže, da zmanjšanje napetosti na (0,5-7-0,6) op praktično ne vpliva na globino sredice in posledično na optimalno debelino stisnjenega sloja. Hkrati je treba opozoriti, da vsako zmanjšanje stresa vodi do povečanja zahtevanega števila ponovitev uporabe obremenitve.
Zaradi zbijanja je treba pridobiti ne le zahtevano gostoto tal, temveč tudi njeno trdno strukturo. To je mogoče doseči le z upoštevanjem določenega načina delovanja. Najprej se to nanaša na specifični tlak, ki mora biti blizu končne trdnosti tal, vendar ne sme presegati slednje ne le na koncu zbijanja, temveč v celotnem procesu. Če kršite to pravilo in nemudoma izberete pritisk, ki naj se zgodi šele na koncu procesa zbijanja, ko je zemlja že gosta in močna, se bo pri prvih prehodih struktura uničila, še posebej blizu površine. To bo otežilo nadaljnje oblikovanje goste in močne strukture, končno dosežena gostota in trdnost pa bosta nižji od tistih, ki jih dobimo s postopnim povečevanjem specifičnega tlaka. Na uničenje strukture na primer kaže močno valovanje pred valji ali kolesi valjev, pa tudi izbočenje tal s strani.
Tako lahko rečemo, da se mora specifični tlak delovnega telesa stroja postopoma povečevati od prehoda do prehoda v primeru valjev ali od udarca do udarca z nabijalci. Ta proces do neke mere povečanja specifičnega tlaka poteka samodejno zaradi postopnega zmanjševanja globine koloteka med valjanjem in časa udarca med zbijanjem. Hkrati se specifični tlaki povečajo za 1,5-2 krat, pri čemer je potrebno, da postanejo 3-4 krat višji. Zato je treba tla stiskati z dvema strojema - lahkim in težkim. Lahka naprava naj služi za predhodno zbijanje, težka pa za končno spravljanje tal do zahtevane gostote. Uporaba predkompaktiranja zmanjša skupno potrebno število prehodov ali udarcev na enem mestu za približno 25 %. Če še upoštevamo, da se na začetku postopka uporabljajo lažja sredstva, potem vse to daje prihranek do 30 % skupnih stroškov stiskanja.
Prehod na zbijanje s težjim strojem ne sme povzročiti močnega povečanja obremenitve na površini tal. Zato je najboljši učinek dosežen, ko bo napetost na površini ob prvem udarcu težjega stroja enaka napetosti, ki ustreza zadnjemu udarcu lažjega stroja. Pri valjanju z valji na pnevmatikah je ta zahteva izpolnjena, ko se predhodno stiskanje izvaja z valjčkom, katerega obremenitev na vsako kolo je 2-krat manjša kot pri glavnem stiskanju, tlak v pnevmatikah pa se zmanjša za 1,5-2 krat. . Pri strojih za nabijanje je mogoče predhodno zbijanje izvajati s strojem, katerega delovno telo tehta polovico manj, ali z istim strojem, ki proizvaja glavno zbijanje, vendar s 4-kratnim zmanjšanjem višine padca delovnega telesa. Med predkompaktiranjem je treba opraviti 30-40 % skupnega zahtevanega števila prehodov.
Predhodno zbijanje se lahko izpusti, če so tla pri gradnji nasipa zbijali zemeljski ali zemeljski stroji do gostote najmanj 0,906 ha, kar nastane na primer pri strgalnikih.
Pri valjanju ima določen vpliv hitrost valjev. Pri različnih hitrostih vožnje je optimalna gostota tal praktično dosežena v enakem številu prehodov. Ta sklep potrjujejo neposredni testi in izhaja iz reoloških lastnosti tal. Tako je bilo v 2. razdelku prikazano, da hitrost spremembe napetostnega stanja praktično vpliva na velikost nepopravljive deformacije le do določenih vrednosti. Hitrosti, ki nastanejo med valjanjem, so že zunaj njihovega vpliva.
Hkrati je bilo ugotovljeno, da pri velikih hitrostih nastane manj obstojna struktura tal, kar je razloženo z nekoliko večjimi strižnimi silami, ki delujejo na tla. Opravljene študije so omogočile razvoj racionalnega režima valjanja pri visokih hitrostih, pri katerem se kakovost zbijanja ne le ne zmanjša, ampak se tudi nekoliko poveča. V tem načinu je treba prvi in zadnja dva prehoda opraviti pri nizki hitrosti (1,5-2,5 km/h), vse vmesne prehode pa pri visoki hitrosti (8-10 km/h). V tem načinu se zmogljivost poveča za približno 2-krat. Zasnova valjev mora omogočati zbijanje tal pri razumni hitrosti.
Za Kategorija: - Stroji za zbijanje tal
V nasipih se tla stisnejo s pomočjo različnih vrst valjev, ki delujejo v povezavi s traktorjem. Uporabljajo se tudi vibracijski nabijalci, ki prenašajo pogosta nihajna gibanja na zbito zemljo, in nabijalniki z delovnim telesom v obliki plošče, ki občasno padajo na tla z različnih višin.
Glavni parametri, ki označujejo proces zbijanja, odvisno od uporabljene opreme in vrste stisnjenih tal, so navedeni v tabeli. V.5.
Najpogosteje se uporabljajo vlečni valji, od katerih so najučinkovitejši pnevmatski valji. Zbijanje tal se izvaja v enakem zaporedju kot njegovo polnjenje. Tla se stisnejo z zaporednimi krožnimi prodori valja po celotnem območju nasipa, pri čemer mora vsak preboj prekrivati prejšnjega za 0,2 ... 0,3 m. Ko končate z valjanjem celotne površine naenkrat, nadaljujte do drugi prodor
Da se tla ne zrušijo v bližini pobočja nasipa, se prva dva prodora po pobočju izvedeta na razdalji najmanj 1,5 m od roba. Naknadni preboji se premaknejo za 0,5 m proti robu in tako robovi nasipa valjajo. Ker se valjanje izvaja v več prebojih vzdolž enega tira, se prva polovica prebojev izvaja z nizko hitrostjo, druga pa z višjo hitrostjo, saj se s povečanjem gostote nasipa poveča upor proti gibanju valja. znatno zmanjša.
Urna produktivnost, m2/h, stiskalni stroji:
kjer je V povprečna hitrost, m/h; b - širina plasti, stisnjene v enem prehodu, m; a-širina prekrivajočega se pasu prejšnjega prehoda, m; Kv - koeficient porabe skozi čas (0,8 - za valjčke in 0,7 - za druge stroje za stiskanje tal); n je število penetracij v enem tiru.
Najtežje je zbijanje tal pri zasipanju sinusov temeljev ali jarkov, saj se dela izvajajo v utesnjenih razmerah. V teh primerih se tla do širine 0,8 m od temelja stisnejo s plastmi 15 ... 20 cm s pnevmatskimi in električnimi nabijalci, zgornje plasti pa se stisnejo z bolj produktivnimi majhnimi valji, ki se premikajo z vibriranjem. plošče itd. (slika V. 31).
Med postopkom zbijanja je treba nadzorovati doseženo gostoto tal. Za te namene na terenu določite gostoto tal, pridobljene z jeklenko (obročem) s prostornino 50 ... 100 cm3 iz jam, položenih v nasipe.
Vendar je ta metoda nadzora zelo naporna. Uporablja se tudi merilnik gostote, ki ga je zasnoval Soyuzdornia. Ta naprava je sestavljena iz palice, po kateri drsi tovor, ki pri padcu udari (z energijo 1 J) na konico s površino 1 cm2 (za mehka tla - 2 cm2). Število udarcev, potrebnih za potopitev konice za 10 cm, označuje gostoto tal. Inštalacija se uporablja tudi za prosojna tla z gama žarki. V tem primeru sta na določeni razdalji v zemljo potopljeni dve cevi, od katerih ena vsebuje radioaktivni izotop, druga pa kvantni števec sevanja, ki meri jakost sevanja, ki je odvisna od gostote zemlje, ki ločuje obe cevi.
Zbijanje tal z valji
Valjanje se izvaja s samohodnimi in vlečenimi pnevmatskimi valji. Sila stiskanja je dosežena zaradi visokih kontaktnih napetosti, ki nastanejo zaradi teže valja in balastne obremenitve na kotalni ravnini (liniji) (do 8 MPa).
Pnevmatski valjarji so lahko enoosni (teža 10 - 25 ton), dvoosni vlečni (težki do 50 ton) in pol vlečeni (eno- ali dvoosni do 100 ton). Z lahkimi valjarji dosežemo zahtevano zbijanje rahlih tal s plastjo 20–30 cm z delovno širino do 2,5 m. Težki vlečni pnevmatski valjarji, težki 25–50 ton, zagotavljajo zbijanje tal s plastjo 35–50 cm. z delovno širino 2,5–3,3 m so najbolj učinkoviti polvlečeni pnevmatski valji, ki zagotavljajo kakovostno zbijanje kohezivnih in nekohezivnih tal s plastjo 40–50 cm s širino oprijema 2,7–2,8 m.) . Vlečni in samohodni bobnasti valji so zaradi velikega območja porazdelitve tlaka manj učinkoviti kot odmični valji.
Za povečanje kontaktnega pritiska na stisnjeno zemljo in doseganje visoke zmogljivosti se uporabljajo odmikalni ali rešetkasti valji. Odmikači so jekleni profilni zatiči dolžine 200 - 300 mm, privarjeni po obodu na lupino bobna. Takšni valji se uporabljajo za stiskanje samo kohezivnih tal. Pri stiskanju tal iz grobih kamnin so namesto odmikačev na površino bobnov privarjene jeklene rešetke iz vogala ali drugega jeklenega profila. Odmikalni in rešetkasti valji zagotavljajo zbijanje tal s plastjo 25 - 50 cm s širino zajema 2,7 - 3,3 m v 4 - 10 prehodih vzdolž proge.
Valjanje vsake plasti zemlje se praviloma izvaja po vzorcu spiralnega obroča. Dolžina oprijema je predpostavljena 250 - 300 m. Pri stiskanju tal na oprimkih majhne širine (valje je težko obračati) se uporabljajo predvsem bobnasti valji z lastnim pogonom, ki se gibljejo v vzajemnem vzorcu.
61. Zbijanje in vibrozbijanje tal.
Metoda zbijanja tal z nabijanjem temelji na prenosu udarnih obremenitev na stisnjeno zemljo. Za razliko od vibracijskih in vibrotampernih metod ima ta metoda bistveno večjo udarno energijo zaradi visoke hitrosti uporabe obremenitve v trenutku udarca delovnega telesa ob tla, zaradi česar ta metoda zagotavlja zbijanje.
kohezivna in nekohezivna tla v plasteh velike debeline (praktično do 2 m). Metoda zbijanja tal z nabijanjem je našla najširšo uporabo v industrijski gradnji pri urejanju talnih blazin pod podlago temeljev stavb in objektov, tehnološke opreme in tal. Ta metoda se uporablja tudi za zabijanje jam v pogrezajočih se tleh pri gradnji stebričnih temeljev.
Kombinirana metoda zbijanja tal temelji na uporabi različnih kombinacij statičnih, vibracijskih, vibronabijalnih in nabijajočih obremenitev na tla. Ta metoda omogoča zbijanje vseh vrst tal in se uporablja predvsem za širok spekter del.
Metoda zbijanja tal z vibracijami temelji na prenosu mehanskih harmoničnih nihanj z delovnih teles (bobnov, koles, plošč, vibracijskih glav) na stisnjeno zemljo. Metoda vibracij je razdeljena na površinsko in globoko. Za metodo površinskega vibrokompaktiranja tal je značilno, da se stiskalno delovno telo med delovanjem nahaja na površini tal in z nihajnimi gibi deluje nanjo. Pri globinski metodi se delovno telo stiskanja med delovanjem nahaja znotraj tal.
Metoda površinske vibracije je našla uporabo pri zbijanju nekohezivnih in šibko kohezivnih nasipnih tal. Metoda globokih vibracij se lahko učinkovito uporablja pri zbijanju peščenih tal, zlasti tistih, ki so v vodo nasičenem stanju. Glede na glavne parametre tresljajev, ki so frekvenca in amplituda nihanja, lahko vibracijski stroji za površinsko zbijanje tal delujejo tudi v vibroudarnem načinu. Amplituda njihovih nihanj je veliko večja, frekvenca nihanja pa manjša kot pri vibracijskih strojih.V tem primeru se vibracijski stroji imenujejo
vibrotamping, metoda zbijanja pa je vibrotamping. Metoda zbijanja tal z vibrotampanjem je našla uporabo v gradbeništvu pri zbijanju zasipov na utesnjenih mestih.
62. Globoko zbijanje tal.
Zbijanje talnih pilotov, premik tal med radialnim zbijanjem v procesu prebijanja ali prebijanja vodnjakov in naknadnega polnjenja z zemljo in zbijanje plast za plastjo
Metode globokega zbijanja:
fizično
Namočite
Drenaža (navpična drenaža)
Mehanski
Vibrokompaktacija
Zbijanje tal s piloti
Zbijanje tal s pnevmatskimi udarci
Zbijanje s spiralnim estrihom
Tesnjenje z delovnim telesom v obliki vijačnega kupa
Kombinirano
voda + vibracije
(hidro-vibracijski kompaktor)
Pri zbijanju tal je treba zagotoviti optimalno vlago, ki zahteva najmanjšo porabo energije.
Z zaporednim zbijanjem se delo izvaja v vzorcu šahovnice. Udarna metoda se uporablja za oblikovanje vrtin. Trajanje zbijanja 1 plasti - 30 sek. Z 10-15 zadetki. Za razsuta in pogrezna tla do globine 5-25 m. Površinsko (odbojno) plast je treba stisniti.
Globoko vibracijsko zbijanje - za peščene z vodo nasičene podlage: nasipni in aluvialni pesek Izvedba metode se izvaja z zaporednim potopitvijo vibrirne palice v tla ob hkratnem dovajanju vode skozi notranjo votlino, po potopitvi vibrirne palice do zahtevane vrednosti. globoka oskrba z vodo se ustavi in se izvaja poleg 4-5 dvigovanje-spuščanje suhega . Globoko zbijanje s predhodnim namakanjem - za pripravo lastnosti posedanja, zmanjšanih zaradi deformabilnosti in zbijanja tal: les, ilovica, meljasta tla z visokim filtracijskim koeficientom najmanj 0,2 m / dan. Postopek zbijanja poteka pod vplivom lastne mase tal med namakanjem in je precej dolg 2-3 mesece. Skrajšanje časa zbijanja tal na 3-7 dni je doseženo z uporabo dodatnega zbijanja zaradi eksplozije komflet.
63. Kontrola kakovosti zbitosti tal.
Kakovost zbijanja tal je mogoče nadzorovati z naslednjimi najpogostejšimi metodami: standard, rezalni obročki, radioizotop, sondiranje, žigosanje, voskanje, metoda lukenj Izbira ene ali druge metode je odvisna od opremljenosti laboratorija, narave laboratorija. strukturo, prostornino nasipa, ki se postavlja, in njihov razred tesnila določajo optimalno vsebnost vlage in največjo standardno gostoto z napravo SoyuzdorNII. Metoda rezanja obročev pri določanju gostote skeleta tal v nasipih temelji na določanju gostote mokre zemlje v prostornini kovinskega obroča s prostornino 300 ... 400 cm3 (d / h = l), stisnjenega v zgoščeno plast in vsebnost vlage v tej zemlji je zaradi svoje preprostosti najbolj sprejemljiva in razširjena Trenutno se v gradbeni praksi najbolj uporabljajo radioizotopske metode, saj so bili terenski laboratoriji na velikih zemeljskih delih opremljeni z napravami, ki uporabljajo absorpcijo in razpršitev gama sevanja in nevtronov Metoda statičnega in dinamičnega sondiranja kot ena od vrst kontrole stopnje zbitosti tal v nasipih in nasutjih je najučinkovitejša in enostavna od vseh obstoječih metod nadzora. Metoda se uporablja za določanje trdnosti temeljev tal. Zlasti se ta metoda široko uporablja za nadzor kakovosti zbitosti tal temeljev pod tlemi industrijskih zgradb in temeljev.Voskanje se uporablja predvsem za nadzor zbitosti tal v zimskih razmerah.kmode.Kakovost tal položene v telo nasipa se lahko šteje za sprejemljivo, če število kontrolnih vzorcev z gostoto tal, ki odstopa od tiste, ki je določena v projektu, ne presega 10 % skupnega števila kontrolnih vzorcev, odvzetih na lokaciji, in gostota skeleta tal v vzorci ne smejo biti za več kot 0,5 g/cm3 pod zahtevano gostoto (najmanj).
64. Zaprt razvoj tal s prebodno metodo.
Punkcija je nastanek lukenj zaradi radialnega zbijanja tal, ko se vanjo pritisne cev s stožčastim vrhom. Vdolbina je narejena s hidravlično dvigalko. V jamo se položi cevni člen s konico in se po poravnavi z dvigalom vtisne v tla za dolžino hoda palice. Ko se palica vrne v prvotni položaj, se na svoje mesto vstavi tlačna cev (ramrod) in postopek se ponovi. Na koncu vdolbine prvega cevnega člena po celotni dolžini odstranimo naramnico, v jamo spustimo naslednji člen, ki je sočelno privarjen na že zdrobljenega v zemljo. Nato se zvarjeni člen zdrobi in cikel se ponovi zadostno število krat, dokler ni preluk po celotni dolžini odseka, ki ga ni mogoče izkopati na tradicionalen način. Za vsak cikel se cev premakne za 150 mm. Ta metoda se izvaja v zelo stisljivih tleh, za cevi s premerom od 100 do 400 mm na globini več kot 3 m "preluknjamo" luknje. V rahlo stisljivih tleh (pesek, peščena ilovica), da se zagotovi stabilnost sten je poleg horizontalne sile potrebno uporabiti prečne in vibracijske učinke. Hkrati se naredijo luknje s premerom do 300 mm.
65. Zaprt razvoj tal s prebijanjem.
Metoda se uporablja za polaganje jeklenih cevi s premerom od 500 mm do 1800 mm ali kolektorjev kvadratnega (pravokotnega) preseka na razdalji do 80 m. Tehnologija je naslednja: cevni členi se zaporedno vtisnejo v tla, znotraj katere se zemlja razvije in odstrani s pomočjo vijačne namestitve. V zlahka erodiranih tleh se odstranjevanje izvaja s hidromehansko metodo (tla znotraj cevi se spere s curkom vode in celuloza se izčrpa s črpalko). Pogosto se cevi uporabljajo kot ohišja za postavitev glavnih cevovodov v njih. Metoda vodoravnega vrtanja v zaprtem izkopu.
Vrtanje se uporablja za polaganje cevovodov v glinenih tleh s premerom od 800 do 1000 mm v dolžini do 100 m. Konec cevi je opremljen z rezalno krono povečanega premera, cev poganja motor, nameščen na rob jame. O translacijskem gibanju cevi poroča regalna dvigalka s poudarkom na zadnji steni jame. Zemljo, ki polni cev od znotraj, je mogoče odstraniti skozi cev, ki jo polagamo, z vijačno montažo po hidromehanski metodi, tako da speremo zemljo v notranjosti cevi s curkom vode in nato celulozo izčrpamo s črpalko (v zlahka erodiranih prsti) ali balirke s podaljškom ročaja.
Ena najpomembnejših lastnosti betonske mešanice je sposobnost plastičnega širjenja pod vplivom lastne mase ali obremenitve, ki se nanjo nanaša. To določa relativno enostavnost izdelave izdelkov najrazličnejšega profila iz betonske mešanice in možnost uporabe različnih metod za njeno zbijanje. V tem primeru sta način zbijanja in lastnosti zmesi (njena mobilnost ali fluidnost) tesno povezani. Tako toge nepretočne mešanice zahtevajo močno zbijanje, pri oblikovanju izdelkov iz njih pa je treba uporabiti intenzivno vibracijo ali vibracijo z dodatnim stiskanjem (z obremenitvijo). Obstajajo tudi drugi načini stiskanja trdih mešanic - nabijanje, stiskanje, valjanje.
Mobilne mešanice se enostavno in učinkovito stiskajo z vibracijami. Uporaba stiskalnih (stiskalnih) vrst zbijanja - stiskanja, valjanja, pa tudi nabijanja - je neprimerna za takšne mešanice. Pod vplivom znatnih stiskalnih sil ali pogosto ponavljajočih se udarcev nabijača bo mešanica zlahka iztekla izpod matrice ali pa jo bo nabijal razpršil.
Lite mešanice se lahko stisnejo pod vplivom lastne teže. Da bi povečali učinek zbijanja, so včasih izpostavljeni kratkotrajnim vibracijam.
Tako lahko ločimo naslednje metode stiskanja betonskih mešanic: vibriranje, stiskanje, valjanje, nabijanje in litje. Najučinkovitejša tako tehnično kot ekonomsko je metoda vibriranja. Uspešno se uporablja tudi v kombinaciji z drugimi metodami.
Mehansko zbijanje - z nabijanjem (vibro-tamping! s stiskanjem (vibro-pressing), valjanje (vibro-valjanje). vesel "Novost mehanskih metod stiskanja PREMIKLJIVIH betonskih mešanic je centrifugiranje, ki se uporablja pri oblikovanju votlih cevastih izdelkov Dobre rezultate pri pridobivanju visokokakovostnega betona dosežemo z vakuumiranjem mešanice v procesu njenega mehanskega zbijanja (predvsem z vibracijami), vendar znatno trajanje postopka sesanja znatno zmanjša njegov tehnični in ekonomski učinek, zato ta metoda ni se pogosto uporablja v tehnologiji montažnih betonov.
Na kratko razmislite o bistvu zgornjih metod stiskanja betonskih mešanic.
Vibracija je zbijanje betonske mešanice kot posledica prenosa nanjo pogosto ponavljajočih se prisilnih tresljajev, ki se v agregatu izražajo s tresanjem. V vsakem trenutku stresanja so delci betonske mešanice tako rekoč v suspendiranem stanju in njihova povezava z drugimi delci je prekinjena. Z naknadnim delovanjem potisne sile delci pod lastno težo padejo in hkrati zavzamejo ugodnejši položaj, v katerem so lahko manj prizadeti zaradi udarcev. To ustreza stanju njihovega najgostejšega pakiranja med drugimi, kar na koncu vodi do goste betonske mešanice. Drugi razlog za zbijanje betonske mešanice med vibracijami je sposobnost premikanja v začasno tekoče stanje pod delovanjem zunanjih sil, ki se nanjo nanašajo, kar imenujemo tiksotropija. Ker je v tekočem stanju, se betonska zmes med vibracijami začne širiti, pridobi obliko - j in se stisne pod delovanjem lastne mase. U Tretji razlog za zbijanje določa visoke tehnične lastnosti betona. ,
Visoka stopnja zbijanja betonske mešanice z vibracijami | doseženo z uporabo opreme nizke moči. Na primer, betonske mase s prostornino več kubičnih metrov se stisnejo z vibratorji s pogonsko močjo le 1 ... 1,5 kW.
Sposobnost betonskih mešanic, da pod vplivom vibracij preidejo v začasno tekoče stanje, je odvisna od mobilnosti mešanice in hitrosti gibanja njenih delcev drug glede na drugega. Mobilne mešanice zlahka preidejo v tekoče stanje in zahtevajo nizko hitrost gibanja. Toda s povečanjem togosti (zmanjšanjem mobilnosti) betonska mešanica vse bolj izgublja to lastnost ali zahteva ustrezno povečanje stopnje vibracij, kar pomeni, da so potrebni višji stroški energije za zbijanje.
Hitrost v (cm / s) nihanja med vibracijami je izražena z zmnožkom amplitude A in frekvence n nihanj: u \u003d An
Plošče. Praksa je pokazala, da se mobilne betonske mešanice učinkovito stisnejo z amplitudo nihanja 0,3 ... 0,35 mm,
In trdo - 0,5 ... 0,7 mm.
Na kakovost vibrokompaktacije ne vplivajo samo parametri vibracijskega mehanizma (frekvenca in amplituda), temveč tudi trajanje vibracij. Za vsako betonsko mešanico je glede na njeno gibljivost določeno svoje optimalno trajanje vibrokompaktiranja, do katerega se zmes učinkovito stisne in preko katerega se stroški energije povečajo v veliko večji meri kot se zmes stiska. Nadaljnje zbijanje sploh ne daje povečanja gostote. Poleg tega lahko prekomerno dolgotrajne vibracije povzročijo razslojevanje mešanice, njeno ločitev na ločene komponente - cementno malto in velika zrna agregata, kar bo na koncu povzročilo neenakomerno gostoto izdelka po odseku in zmanjšanje trdnosti v njegovih posameznih delih.
Seveda so dolgotrajne vibracije nedonosne tudi z ekonomskega vidika: stroški energije in delovna intenzivnost se povečajo, produktivnost linije za oblikovanje pa se zmanjša.
Intenzivnost vibrokompaktiranja I (cm2/s3), izražena z najkrajšim trajanjem tresljajev, je odvisna tudi od glavnih parametrov delovanja vibracijskega mehanizma - frekvence in amplitude nihanja, ki se izvaja ob upoštevanju njihove medsebojne kombinacije hitrosti in pospeška. nihanja: I = A2 / n3.
Intenzivnost vibrokompaktacije se poveča tudi, če je frekvenca prisilnih tresljajev enaka frekvenci naravnih vibracij. Zaradi dejstva, da ima betonska mešanica širok razpon velikosti delcev (od nekaj mikrometrov za cement do nekaj centimetrov za grobi agregat) in s tem razlike v pogostosti njihovih naravnih vibracij, bo najbolj intenzivno zbijanje mešanice ko je za način vibracije značilne različne frekvence. Tako se je pojavil predlog za uporabo polifrekvenčnih vibracij.
Te dejavnike je treba upoštevati za tehnično in ekonomsko oceno postopkov oblikovanja izdelkov. Iz zgoraj navedenega sledi, da se učinkovitost stiskanja povečuje s povečanjem energije stiskanja, trajanje stiskanja se skrajša in poveča produktivnost livarske linije. Tako lahko na podlagi tehnične in ekonomske analize lastnosti betonske mešanice, zmogljivosti kalupne linije izberete moč vibrokompaktnih mehanizmov.
Vibracijsko zbijanje betonske mešanice se izvaja s prenosnimi in stacionarnimi vibracijskimi mehanizmi. Uporaba prenosnih vibratorjev v montažnem betonu je omejena. Uporabljajo se predvsem pri oblikovanju velikih masivnih izdelkov na stojnicah.
V tehnologiji montažnega betona v delujočih tovarnah
V skladu s shemami pretočnega agregata in transporterja se uporabljajo vibracijske ploščadi. Vibracijske platforme odlikuje široka paleta vrst in izvedb vibratorjev - elektromehanskih, elektromagnetnih, pnevmatskih; narava vibracij - harmonična, udarna, kombinirana; oblika tresljajev - krožno usmerjena - navpična, vodoravna; načrtovalne sheme mize - s trdnim zgornjim okvirjem, ki tvori mizo z eno ali dvema vibracijskima gredoma in sestavljen iz ločenih vibracijskih blokov, ki na splošno predstavljajo skupno vibracijsko ravnino, na kateri se nahaja oblika z betonsko mešanico.
Za trdnost pritrditve obrazca na mizo platforme so predvideni posebni mehanizmi - elektromagneti, pnevmatske ali mehanske sponke.
Vibracijska ploščad (slika 11.1) je ravna miza, podprta z vzmetnimi nosilci na fiksnih nosilcih ali okvirju (okvirju). Vzmeti so zasnovane tako, da dušijo tresljaje mize in s tem preprečijo njihov udarec na nosilce, sicer se uničijo. V spodnjem delu je na mizo togo pritrjena vibrirajoča gred z ekscentri, ki se nahajajo na njej. Ko se gred vrti iz elektromotorja, ekscentri vzbujajo tresljaje mize, ki se nato prenesejo na obliko z betonsko mešanico, posledično se stisne. Moč vibracijske platforme je ocenjena z njeno nosilnostjo (masa izdelka skupaj s kalupom), ki je 2...30 ton.
Montažne armiranobetonske tovarne so opremljene z enotnimi vibracijskimi ploščadmi, s frekvenco vrtenja 3000 vrt / min in amplitudo 0,3 ... 0,6 mm. Te vibrirajoče ploščadi dobro kompaktirajo togo betonsko mešanico konstrukcij do 18 m dolžine in do 3,6 m široke.
Pri oblikovanju izdelkov na vibracijskih ploščadih, zlasti iz trdih betonskih mešanic na poroznih agregatih, se za izboljšanje strukture betona uporabljajo uteži - statične,
Vibracijski, pnevmatski, vibropnevmatski. Vrednost teže, odvisno od lastnosti betonske mešanice, je 2 ... 5 kPa.
Pri oblikovanju izdelkov v fiksnih kalupih se betonska mešanica stisne s površinskimi, globinskimi in vgrajenimi vibratorji, ki so pritrjeni na kalup. Pri izdelavi izdelkov v vodoravnih oblikah se uporabljajo toge ali počasi premikajoče se betonske mešanice in pri oblikovanju v navpični obliki
nekatere oblike (v kasetah) uporabljajo mobilne mešanice z obleganjem stožca 8 ... 10 cm.
F Stiskanje je redko uporabljena metoda stiskanja betonske mešanice v tehnologiji montažnih betonov, čeprav je zelo učinkovita v smislu tehničnih kazalnikov, ki vam omogoča, da dobite beton visoke gostote in trdnosti z minimalno porabo cementa (100 ... 150). kg / m3 betona). Širjenje metode stiskanja ovirajo izključno ekonomski razlogi. Tlak stiskanja, pri katerem se beton začne učinkovito zbijati, je 10 ... 15 MPa in več. Tako je za tesnjenje izdelka za vsak 1 m2 potrebno uporabiti obremenitev, ki je enaka 10 ... 15 MN. Stiskalnice takšne moči se uporabljajo v tehnologiji, na primer za stiskanje ladijskih trupov, vendar se izkaže, da so njihovi stroški tako visoki, da popolnoma izključujejo ekonomsko izvedljivost uporabe takšnih stiskalnic.
V tehnologiji montažnih betonov se stiskanje uporablja kot dodatna mehanska obremenitev betonske mešanice med njenimi vibracijami. V tem primeru zahtevana vrednost pritiska stiskanja ne presega 500 ... 1000 Pa. Tehnično se ta tlak doseže pod delovanjem statično uporabljene obremenitve kot posledica prisilnega premikanja posameznih delcev betonske mešanice.
Razlikovati med stiskanjem s ploščatimi in profilnimi žigi. Slednji prenašajo svoj profil betonske mešanice. Tako so oblikovane stopnice, nekatere vrste rebrastih plošč. V slednjem primeru se metoda stiskanja imenuje tudi žigosanje. Najem je vrsta stiskanja. V tem primeru se pritisk stiskanja prenese na betonsko mešanico le skozi majhno površino valja, kar ustrezno zmanjša potrebo po stiskanju. Toda tukaj plastične lastnosti betonske mešanice, skladnost njene mase pridobijo poseben pomen. V primeru nezadostne kohezije bo mešanica premaknjena s tlačnim valjem in jo zlomila. Centrifugiranje - zbijanje betonske mešanice Kot posledica delovanja centrifugalnih sil, ki nastanejo v njej med vrtenjem. V ta namen se uporabljajo centrifuge (slika 11.2), ki so cevasti odsek, ki se med stiskanjem vrti do 600 ...
valjanje med vrtenjem, se pritisne na notranjo površino kalupa in hkrati stisne. Zaradi različne gostote trdnih komponent betonske mešanice IN VODE se iz betonske mešanice odstrani do 20 ... 30% vode, kar prispeva k proizvodnji betona visoke gostote.
Metoda centrifugiranja relativno enostavno omogoča pridobivanje izdelkov iz betona visoke gostote, trdnosti (40 ... 60 MPa) in vzdržljivosti. Hkrati je za pridobitev betonske mešanice visoke kohezije potrebna velika količina cementa (400 ... 450 kg / m3), sicer se bo mešanica pod delovanjem centrifugalnih sil razslojila na majhna in velika zrna, ker se bo slednji z veliko silo oprijel površine kalupa. Cevi, daljnovodni drogovi, stojala za svetilke se oblikujejo s centrifugiranjem. Pri sesanju se v betonski mešanici ustvari vakuum do 0,07 ... 0,08 MPa, zrak, ki je vključen v njeno pripravo in polaganje v obliko, pa tudi nekaj vode, pa se iz betonske mešanice odstrani pod delovanjem ta vakuum: izpraznjena mesta zasedajo trdni delci in betonska mešanica pridobi povečano gostoto. Poleg tega prisotnost vakuuma povzroči pritisk na betonsko mešanico z atmosferskim tlakom, ki je enak vrednosti vakuuma. Prispeva tudi k zbijanju betonske mešanice. Sesanje je praviloma kombinirano z vibracijami. V procesu vibriranja betonske mešanice, ki je izpostavljena vakuumu, se namesto zračnih mehurčkov in vode intenzivno zapolnjujejo trdne komponente por, ki nastanejo med sesanjem. Vendar ima v tehničnem smislu sesanje pomembno tehnično in ekonomsko pomanjkljivost, in sicer: dolg procesni čas - 1 ... 2 minuti na vsak 1 cm debeline izdelka, odvisno od lastnosti betonske mešanice in velikosti preseka. . Debelina sloja, ki ga je mogoče izpostaviti vakuumu, ne presega 12...15 cm, zato se sesanju izvajajo predvsem masivne konstrukcije, ki dajejo površinski plasti posebno visoko gostoto. V tehnologiji montažnega armiranega betona se sesanje praktično ne uporablja. wj
Tehnologija gradnje betonskih konstrukcij vključuje pripravo betonske mešanice in njeno zbijanje. Obstajajo primeri, ko se pri mešanju raztopine v notranjosti pojavijo votline, ki lahko porušijo strukturo in zmanjšajo njeno gostoto. Zaradi tega se v izdelku pojavijo razpoke, kar lahko na koncu privede do uničenja betonskih konstrukcij. Med postopkom zbijanja strokovnjaki odstranijo zrak in odvečno tekočino iz raztopine, zaradi česar postane gostejša. Tako je izdelek močnejši in trajnejši.
Zbijanje betona velja za najpomembnejši korak pri polaganju cementnih mešanic. Koeficient betona in glavne značilnosti izdelka bodo odvisni od tega, kako natančno bo to dejanje izvedeno. Med postopkom strokovnjaki obdelajo betonsko površino ročno ali s pomočjo mehanskih naprav, pri čemer odstranijo votline. To vam omogoča, da dosežete enotnost betonske raztopine, povečate oprijem sestave na druge strukturne elemente.
Načini
Gradbeniki pri stiskanju mešanice uporabljajo naslednje vrste naprav:
- površina (za zgornjo plast cementa);
- globoko (velike betonske konstrukcije);
- zunanji (nameščen pred stiskanjem z roba lesenega opaža ali posode s cementno malto);
- vibracijske platforme (uporabljajo se v specializiranih podjetjih).
Obstajajo različni načini stiskanja cementne malte:
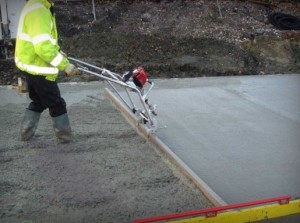
druge metode
Druge metode tesnjenja vključujejo:
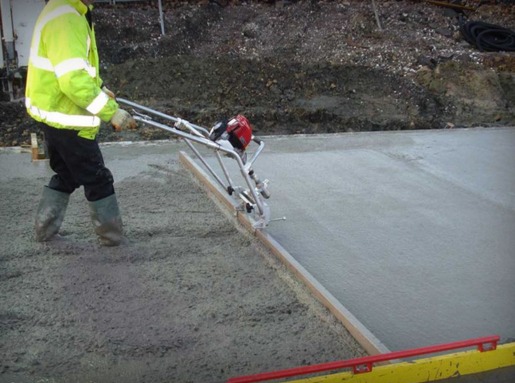
Da bi bila cementna sestava enakomerno zbita, je treba upoštevati naslednja priporočila:
- Pri montaži lesenih opažev je treba paziti na zanesljivo pritrditev delov. Na konstrukcijskih elementih ne sme biti nobenih vrzeli (betonska raztopina se lahko iztisne skozi razpoke). Potrebno je, da je opaž poliran in gladek, sicer bo na izdelku pustil udrtine. Poleg tega se lahko kasneje v telesu konstrukcije tvorijo praznine.
- Detajli lesenih ali vezanih opažev, vključno s klini, morajo biti varno pritrjeni, da se deske ne premikajo.
- Pri vibrokompaktiranju sestave je treba položaj vibracijskega estriha občasno spreminjati, sicer bo raztopina nehomogena, nastale bodo votline.
- Strokovnjaki svetujejo, da ne porabite veliko časa za delo, saj lahko to povzroči razslojevanje, ki se pojavi zaradi dejstva, da se na dnu podrti velik gramoz, na vrhu pa se nabira le cementna malta.
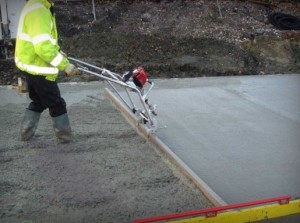
Ker uporaba površinskih vibracijskih naprav ne omogoča vizualnega določanja stopnje gostote, se pri gradbenih delih pogosto uporablja dodatno sredstvo, ki pomaga zagotoviti trdnost sestave. Da bi to naredili, gradbeniki obstoječi sestavi dodajo raztopino z visoko plastičnostjo. Zaradi tega se poveča tveganje za razslojevanje izdelka. Da bi se izognili takšni pomanjkljivosti, je priporočljivo povečati količino cementa.
Faktor zbijanja
Kakovost betonske sestave je mogoče oceniti z enim pomembnim merilom. Gre za faktor stiskanja. Koeficient se določi na naslednji način: izračuna se razmerje med specifično težo končne mešanice in vrednostjo, ki je bila dobljena brez zračnih mehurčkov v notranjosti. Torej je sprejemljiva vrednost koeficienta 1. Kazalnik je mogoče doseči z različnimi načini zbijanja betona, izbira metod bo neposredno odvisna od sestave, namena in frakcij. Avtomatizirani vibracijski estrihi bistveno povečajo kakovost rešitve.
Od česa je odvisno razmerje?
Ta indikator je določen z granularnostjo sestave, pa tudi z objektom, ki bo betoniran, ne glede na to, ali gre za slepe površine, proge, poti.
ugotovitve
Izkušeni gradbeniki trdijo, da bosta od tega odvisna stabilnost in vzdržljivost konstrukcije. To je treba upoštevati, če želite, da vam izdelek služi več kot eno leto. Pravočasno sprejeti ukrepi bodo pripomogli k nadaljnjemu povečanju zaščite konstrukcije pred poškodbami, prihranili denar pri obnovitvenih delih. Univerzalne vibracijske naprave vam bodo omogočile, da dobite visokokakovosten beton. Pred izvedbo gradbenih del se morate vnaprej posvetovati s strokovnjaki in izbrati potrebno opremo. Ergonomsko oblikovani vibratorji omogočajo gradbincem kompaktiranje cementa v najrazličnejših pogojih.
Za izvedbo majhne količine gradbenih del strokovnjaki priporočajo uporabo, ki tehtajo do pet kilogramov. Za večja dela gradbeniki uporabljajo velika orodja za učinkovito stiskanje betona v proizvodnji z veliko sprednjo stranjo.