Физические основы процесса уплотнения грунтов машинами. Физические способы поверхностного уплотнения грунтов
Влияние амплитуды и частоты колебания
Частота колебания частиц и их амплитуда взаимосвязаны, что позволяет применять в промышленных условиях разные режимы вибрирования для смесей разной консистенции. Смеси с крупнозернистой фракцией заполнителя вибрируют при сравнительно невысокой частоте (3000-6000 колебаний в минуту), но довольно большой амплитуде, тогда как при виброуплотнении мелкозернистых смесей используется вибрация высокой частоты – до 20000 колебаний в минуту, но с малой амплитудой.
Схема вариантов уплотнения бетона: а) глубинным вибратором; б) пакетом глубинных вибраторов; в) вибратором с гибким валом; г) поверхностным вибратором; д) наружным вибратором; е) изменение прочности бетона в зависимости от времени его уплотнения.
Кроме таких параметров работы вибромеханизма, как амплитуда и частота, на качество уплотнения в результате вибрации влияет и продолжительность самого процесса. Для всех видов бетонных смесей, в зависимости от их текучести, есть свое оптимальное время уплотнения вибрацией, на протяжении которого смесь эффективно уплотняется и по истечении которого затраты энергии непропорциональны эффективности дальнейшего уплотнения. При продолжении уплотнения сверх этого времени прироста плотности не наблюдается в целом. Более того, существует риск, что бетонная смесь начнет расслаиваться на отдельные компоненты в зависимости от их свойств – например крупнозернистая фракция заполнителя и цементный раствор. В результате качество конечного бетонного изделия будет снижено из-за неравномерного распределения плотности и пониженной прочности в отдельных частях его частях.
Продолжительное вибрирование в экономическом отношении невыгодно, так как связано с большими затратами электроэнергии и трудоемкостью всего процесса, из-за чего производительность формовочной линии существенно снижается.
Позитивно влияет на эффективность уплотнения совпадение частоты собственных колебаний частиц раствора с частотой вынужденных колебаний виброуплотнителя. Но тут нужно принимать во внимание тот факт, что смесь является совокупностью разных фракций с различными размерами частиц – от микрометров для цементного раствора до нескольких сантиметров для крупного бетонного заполнителя. Соответственно, наиболее эффективной технологией уплотнения будет применение разных частот – так называемого поличастотного уплотнения, так как частота собственных колебаний для частиц разного размера и массы будет разной.
При проведении технико-экономической оценки необходимо учитывать вышесказанное – при увеличении энергии уплотнения эффективность уплотнения возрастает, что также снижает продолжительность процесса и повышает рентабельность.
Вибростановки и виброплощадки
Виброуплотнение бетонного раствора производится как стационарными, так и переносными средствами. Использование переносных средств в технологии уплотнения для сборного железобетона довольно ограничено. Их промышленное использование в основном сводится к формованию больших, тяжеловесных изделий на стендах.
Виброплощадки применяются в заводском производстве сборного железобетона тех типов заводов, которые работают по конвейерной и поточно-агрегатной схемам. Существует большое разнообразие конструктивных особенностей и типов виброплощадок – электромагнитные, электромеханические, пневматические. По характеру колебаний – ударные, гармонические, комбинированные. По форме колебаний – круговые направленные, горизонтальные, вертикальные. По конструктивным схемам стола – сплошная верхняя рама, образующая стол с одним или несколькими вибрационными валами или собираемая из отдельных виброблоков, которые в целом представляют собой одну вибрационную поверхность с расположенной на ней формой со смесью. Чтобы прочно закрепить форму с раствором, на столе площадки предусмотрены пневматические электромагниты или механические зажимы.
Схема вибростола с размерами
Виброплощадка исполняется в виде плоского стола, опирающегося посредством пружинных опор на станину (раму) или на неподвижные опоры. Назначение пружин – гасить колебательные движения стола, таким образом не допуская их воздействия на опору, что неизбежно привело бы к разрушению. В нижней части к устройству крепится вибровал с располагающимися на его поверхности эксцентриками. Вал приводится во вращение от электромотора, движение эксцентриков вызывает колебания стола, которые затем передаются массе бетона и вызывают уплотнение бетонной смеси. Мощность виброплощадки измеряется ее грузоподъемностью – массой бетонного изделия, взятого вместе с формой, – и колебается в пределах от 2 до 30 т.
Заводы, производящие сборный железобетон, обычно оборудуются унифицированными вибороплощадками с амплитудой колебаний 0,3-0,6 мм и частотой 3000 колебаний в минуту. Такие площадки хорошо справляются с уплотнением для конструкций с длиной до 18 м и шириной до 3,5 м.
Формируя изделия на виброплощадках, особенно если в расход идут жесткие, основанные на пористых заполнителях, обычно с целью улучшить структуру бетона используются пригрузы.
При необходимости формирования изделия с применением неподвижной формы бетонную смесь уплотняют, используя поверхностные, глубинные и навесные вибраторы, прикрепляемые к форме. При изготовлении изделий с использованием горизонтальных форм используются жесткие бетонные смеси или смеси с малой текучестью; в вертикальных формах (кассетах) – смеси с большой текучестью и осадкой конуса 80-100 мм.
Процесс прессования
Прессование как способ уплотнения при изготовлении железобетонных изделий применяется редко, несмотря на то что по техническим показаниям является весьма эффективным, так как позволяет получить высокопрочный бетон с большой плотностью при очень незначительном расходе цемента (100-150 кг/м 3 бетона). Причины, препятствующие распространению этого способа, носят сугубо экономический характер. Давление, при котором бетон эффективно уплотняется, составляет 10-15 МПа и более, то есть для того чтобы уплотнить изделие из бетона, на каждый 1 м 2 нужно приложить усилие, равное 10-15 МН (миллионов Ньютон). Прессы, обладающие такой мощностью, применяют только в судостроительстве для прессования корпусов кораблей, и их стоимость настолько высока, что полностью исключает экономическую рентабельность при использовании.
Центрифугирование
При центрифугировании вращающаяся смесь уплотняется благодаря прилеганию к внутренней поверхности формы. В результате процесса центрифугирования, из-за различной плотности компонентов бетонного раствора и содержащейся в нем воды из него удаляется до 20-30 % жидкости, благодаря чему получается высокопрочный бетон.
Центрифугирование позволяет легко получить из бетона изделия с высокой плотностью, прочностью (40-60 Мпа) и долговечностью. Для этого метода требуется достаточно много цемента, чтобы конечная бетонная смесь обладала большой связностью (400-450 кг/м 3). В противном случае под действием центробежной силы произойдет разделение на несколько слоев, так как зерна большего размера и массы будут сильнее стремиться прижаться к краю формы центрифуги, нежели зерна меньшего размера. С помощью этой технологии формируют стойки под фонари, опоры линий электропередач или трубы.
Вакуумирование раствора
При использовании метода вакуумирования создают разрежение воздуха до давления в 0,07-0,08 Мпа, благодаря чему лишний воздух, вовлеченный в раствор, и излишки воды удаляются под действием разниц давления. Бетон занимает освободившееся при этом место, благодаря чему плотность смеси возрастает. Присутствие вакуума тоже оказывает прессующее воздействие на бетонную массу, величина этого воздействия равняется разнице между давлением вакуума и атмосферным давлением. Благодаря такому воздействию смесь дополнительно уплотняется.
Сочетание вакуумирования с вибрированием
Процесс вакуумирования предпочитают сочетать с вибрированием. Во время вибрирования бетонного раствора, подверженного вакуумированию, твердые компоненты смеси интенсивно заполняют поры, образовавшиеся на месте пузырьков воздуха и капель воды. Однако у вакуумированния в техническом аспекте есть существенный технико-экономический недостаток – большая продолжительность процесса, который в зависимости от и величины разреза на каждый 1 см толщины занимает около 1-2 мин.
Толщина слоя, поддающегося вакуумированию, не превышает 12-15 см. По этой причине вакуумируют преимущественно конструкции больших размеров с целью придания их поверхностному слою большей плотности.
К атегория:
Машины для уплотнения грунтов
Физические основы процесса уплотнения грунтов машинами
Уплотнение грунтов относится к числу наиболее важных элементов технологического процесса возведения земляного полотна автомобильных и железных дорог, плотин и т. п. От качества выполнения этого процесса зависит дальнейшая их служба. Для получения достаточной устойчивости, для каждого из этих сооружений установлены требования к плотностям их грунтов. При этом в основу оценки степени уплотнения положен метод стандартного уплотнения и потому требования к плотностям грунтов обычно выражены в виде коэффициента уплотнения, т. е. в долях от максимальной стандартной плотности (бтах). Для верхних слоев грунтов земляного полотна автомобильных дорог требования к плотностям высоки - здесь плотность грунта должна быть не ниже (0,98-е-1,0) бтах. Для нижних слоев насыпей она может быть снижена до 0,956тах. Плотности грунтов насыпей железных дорог в зависимости от расположения рассматриваемого слоя в насыпях должны находиться в пределах (0,90ч-0,98) 6гаах, а плотности грунтов плотин устанавливаются в каждом конкретном случае. Следует заметить, что достижение такой высокой плотности как (0,98ч-1,0)бтах связано со значительными трудностями и может быть осуществлено лишь при правильном выборе как параметров применяемых машин, так и режима их работы. Уплотнение грунтов должно производиться только специальными предназначенными для этой цели машинами. Попытка использовать для этого землеройно-транспортные машины и совместить этот процесс с выведением насыпей показала, что плотности грунтов получаются недостаточными и уплотнение неравномерным и потому этот способ может служить только для предварительного уплотнения грунтов, что, конечно, облегчает работу основных машин.
Огромное значение при уплотнении имеет влажность грунтов. Каждой действующей на грунт нагрузке соответствует своя оптимальная влажность, при которой требуемая плотность может быть достигнута при наименьшей затрате механической работы. При недостаточной влажности для Достижения требуемой плотности необходимо применять ряд мер, к числу которых относится, например, снижение толщины уплотняемого слоя. Надо заметить, что очень сухие грунты вообще не могут быть доведены до требуемой плотности. Та оптимальная влажность грунта W0, которая определяется методом стандартного уплотнения, соответствует работе средних машин.
Грунты уплотняю]ся укаткой, трамбованием, вибрацией и вибротрамбованием.
При укатке по грунту перекатывается валец или колесо, на поверхности контакта которых с грунтом имеет место какое-то удельное давление (напряжение), за счет которого и развивается необратимая деформация грунта. На этом принципе основана работа всех катков. При трамбовании грунт уплотняется падающей массой, которая была перед тем поднята на какую-то высоту и в момент встречи с грунтовой поверхностью обладает определенной скоростью. Таким образом, трамбование связано с ударом рабочего органа машины о грунт. При вибрировании уплотняющая масса находится либо на поверхности уплотняемого слоя (поверхностные вибраторы), либо внутри его (глубинные вибраторы). В результате специального механизма она приводится в состояние колебательного движения. Часть кинетической энергии этой массы расходуется на колебание грунта, которое вызывают относительные смещения его частиц, чем достигается их более плотная упаковка. При вибрировании не происходит отрыва массы от уплотняемой поверхности или он весьма незначителен. Если возмущения массы превзойдут определенный предел, то будет иметь место ее отрыв от поверхности грунта, что приведет к частым ударам массы о грунт. В этом случае вибрирование перейдет в вибротрамбование. От трамбования этот процесс отличается высокой частотой ударов. Несмотря на малую высоту падения массы, ввиду развивающихся высоких скоростей движения, энергия удара может быть значительной.
Во всех случаях воздействие на грунт рабочих органов машины связано с приложением к нему циклической нагрузки.
Предполагается, что грунты имеют оптимальные влажности.
Удельные давления на поверхности контактов рабочих органов машин с уплотняемыми грунтами не должны быть выше их пределов прочностей, но вместе с тем они не должны быть и низкими, так как в противном случае снижается эффект уплотнения. Лучший эффект получится в тех случаях, когда удельные давления на поверхности контакта с рабочими органами уплотняющих машин равны (0,9-т-1,0) ар (ар - предел прочности). Исключением из этого правила являются машины, действие рабочих органов которых основано на глубоком проникании их в уплотняемый слой грунта (кулачковые и решетчатые катки).
Деформация, а следовательно, и эффект уплотнения, зависит как от скорости изменения напряженного состояния, так и от продолжительности действия нагрузки, а следовательно, и от числа повторностей ее приложения.
Характер взаимодействия рабочих органов машин с грунтом гаков, что он может быть сведен к схеме нагрузки полупространства грунта жестким круглым штампом
Эффект от работы машин для уплотнения грунтов зависит от того, насколько правильно выбрана толщина уплотняемого слоя. При излишне больших толщинах слоев требуемые плотности грунтов не достигаются. При слишком малых толщинах слоев снижается производительность машин и возрастает стоимость работ.
Профессором Н. Н. Ивановым теоретическим путем установлено, что предельная глубина, на которую еще распространяется действие нагрузки, составляет 3,5сгш (йш-диаметр штампа). Позднее этот вывод получил экспериментальное подтверждение. В пределах этой зоны, на которую еще распространяется действие нагрузки, следует различать еще такую зону, где в процессе уплотнения грунтов деформация по глубине распределяется еще более или менее равномерно. Эту зону можно назвать активной, а ее глубину - глубиной активной зоны. Созданию такой зоны способствуют массовые пластические сдвиги грунтовых частиц и агрегатов, которые развиваются по объему грунта, а также то, что уплотняемый слой расположен на более жестком основании, которым служит ранее уплотненный грунт. Наличие жесткого основания приводит к концентрации сжимающих напряжений по оси сосредоточенной нагрузки, а также к меньшему перепаду напряжений по глубине, т. е. к их выравниванию.
В случае несвязных грунтов глубина активной зоны в 1,2-1,5 раза выше.
В пределах активной зоны реализуется около 80% всей деформации грунта и только 20% ее приходится на объем грунта, расположенный вне этой зоны. Поэтому толщина уплотняемого слоя грунта не может быть больше глубины активной зоны, так как в противном случае не будет достигнута требуемая плотность грунта.
Оптимальная толщина уплотняемого слоя грунта находится в тесной связи с глубиной активной зоны. Под оптимальной понимается такая толщина, при которой требуемая степень уплотнения достигается с наименьшей затратой механической работы и наибольшей производительностью машины. Глубина активной зоны определяет собой верхний предел оптимальных толщин слоев уплотняемого грунта. В тех случаях, когда при уплотнении грунтов необходимая плотность не превышает 0,956тах, оптимальная толщина слоя может быть принята равной глубине активной зоны. При этом такая плотность достигается относительно легко и не требует большого количества проходов машин.
Минимальный размер рабочего органа машины в плане определяет собой максимальное значение оптимальной толщины слоя грунта, т. е. как бы потенциальные возможности уплотнения, которые, однако, могут быть реализованы лишь в том случае, если напряжение на поверхности грунта будет близким к пределу прочности. При меньших значениях напряжений оптимальная толщина слоя снизится.
Если требуемая плотность грунта велика и составляет (0,98-7-1,0) 8тах, то оптимальная толщина слоя равна половине глубины активной зоны (Н0 = 0,5ftn). Эта плотность может быть достигнута и при толщине слоя, равной глубине активной зоны, но при этом число проходов должно быть увеличено в 3 раза по сравнению с тем случаем, когда требуемая плотность равна 0,95бтах. Поэтому уплотнение грунтов при таких больших толщинах слоев становится экономически невыгодным.
Снижение толщины уплотняемого слоя грунта, по сравнению с оптимальной величиной, при сохранении тех же размеров рабочего органа и той же величины развивающегося на поверхности грунта напряжения, как правило, влечет за собой излишнюю затрату удельной работы, т. е. работы, необходимой для уплотнения единицы объема грунта.
Анализ формулы (IV. 1) показывает, что снижение напряжений до (0,5-7-0,6) ор практически не отражается на глубине активной зоны, а следовательно, и на оптимальной толщине уплотняемого слоя. Вместе с тем надо заметить, что всякое снижение напряжений приводит к увеличению необходимого числа повторностей приложения нагрузки.
В результате уплотнения должна быть получена не только требуемая плотность грунта, но и прочная его структура. Это может быть достигнуто лишь при соблюдении определенного режима работы. В первую очередь это относится к удельному давлению, которое должно быть близким к пределу прочности грунта, но не превышать последний не только в конце уплотнения, но и в течение всего процесса. Если нарушить это правило и сразу выбрать то давление, которое должно иметь место лишь в конце процесса уплотнения, когда грунт уже плотен и прочен, то при первых проходах будет происходить разрушение структуры, и особенно вблизи поверхности. Это затруднит дальнейшее формирование плотной и прочной структуры, и достигнутые в конечном итоге плотность и прочность будут ниже тех, которые получаются при постепенном возрастании удельного давления. О разрушении структуры, например, свидетельствует сильное волнообразование перед вальцами или колесами катков, а также выпирание грунта со стороны.
Таким образом, можно сказать, что удельное давление рабочего органа машины должно постепенно повышаться от прохода к проходу в случае катков или от удара к удару при трамбующих машинах. Такой процесс повышения удельного давления до некоторой степени производится автоматически за счет постепенного снижения глубины колеи при укатке и времени удара - при трамбовании. При этом удельные давления возрастают в 1,5-2 раза, а необходимо, чтобы они стали выше в 3-4 раза. Поэтому уплотнять грунты нужно двумя машинами - легкой и тяжелой. Легкая машина должна служить для предварительного уплотнения, а тяжелая - для окончательного доведения грунта до требуемой плотности. Применение предварительного уплотнения снижает примерно на 25% общее потребное число проходов или ударов по одному месту. Если еще учесть, что в начале процесса применяются более легкие средства, то все это дает экономию до 30% от общей стоимости работ по уплотнению.
Переход на уплотнение более тяжелой машиной не должен вызывать резкого повышения напряжения на поверхности грунта. Поэтому лучший эффект достигается в том случае, когда напряжение на поверхности при первом воздействии более тяжелой машины будет равно напряжению, соответствующему последнему воздействию более легкой машины. При укатке катками на пневмошинах это требование удовлетворяется в случае, когда предварительное уплотнение производится катком, нагрузки на каждое колесо которого в 2 раза меньше, чем при основном уплотнении, и давление в шинах снижено в 1,5-2 раза. При трамбующих машинах предварительное уплотнение можно производить машиной, вес рабочего органа которой в два раза меньше, или той же машиной, которой производится и основное уплотнение, но при снижении в 4 раза высоты падения рабочего органа. Во время предварительного уплотнения надо совершить 30-40% общего необходимого числа проходов.
Предварительного уплотнения можно не применять, если грунт в процессе возведения насыпи был уплотнен землеройными или землеройно-транспортными машинами до плотности не ниже 0,906гаах, что имеет место, например, при скреперных работах.
При укатке определенное влияние оказывает скорость движения катков. При разных скоростях движения оптимальная плотность грунта практически достигается за одно и то же количество проходов. Этот вывод подтвержден непосредственными испытаниями и следует из реологических свойств грунтов. Так, в п. 2 было показано, что скорость изменения напряженного состояния практически влияет на величину необратимой деформации лишь до определенных значений. Те скорости, которые имеют место при укатке, уже находятся вне сферы их влияния.
Вместе с тем обнаружено, что при больших скоростях движения формируется менее прочная структура грунта, что объясняется несколько большими действующими на грунт сдвигающими усилиями. Проведенные исследования позволили разработать рациональный скоростной режим укатки, при котором качество уплотнения не только не снижается, но и несколько повышается. При таком режиме первый проход и два последних прохода должны совершаться на малой скорости (1,5-2,5 км/ч), а все промежуточные проходы - на большой скорости (8 - 10 км/ч). При таком режиме производительность повышается примерно в 2 раза. Конструкции катков должны позволять производить уплотнение грунтом на рациональном скоростном режиме.
К атегория: - Машины для уплотнения грунтов
В насыпях уплотняют грунт с помощью различных типов катков, работающих в сцепе с трактором. Применяют также вибротрамбовочные машины, передающие уплотняемому грунту частые колебательные движения, и трамбующие машины с рабочим органом в виде плиты, периодически падающей на грунт с различной высоты.
Основные параметры, характеризующие процесс уплотнения в зависимости от применяемого оборудования и от рода уплотняемого грунта, приведены в табл. V.5.
Чаще всего используют прицепные катки, из которых самыми эффективными являются катки на пневмоходу. Уплотнение грунта ведут в той же последовательности, что и его отсыпку. Грунт уплотняют путем последовательных круговых проходок катка по всей площади насыпи, причем каждая проходка должна перекрывать предыдущую на 0,2...0,3 м. Закончив укатку всей площади за один раз, приступают ко второй проходке
Чтобы грунт не обрушился вблизи откоса насыпи, первые две проходки вдоль откоса ведут на расстоянии не менее 1,5 м от бровки. Последующие проходки смещают на 0,5 м в сторону бровки и таким образом прикатывают края насыпи. Поскольку укатку ведут за несколько проходок по одному следу, первую половину проходок выполняют на малой скорости, а вторую - на более высокой, так как по мере увеличения плотности насыпи сопротивление движению катка значительно снижается.
Часовая производительность, м2/ч, уплотняющих машин:
где V - средняя скорость движения, м/ч; b - ширина уплотняемого за один проход слоя, м; а-ширина полосы перекрытия предыдущего прохода, м; Кв - коэффициент использования по времени (0,8 - для катков и 0,7 - для остальных грунтоуплотняющих машин); п - число проходок по одному следу.
Наиболее трудным является уплотнение грунта при обратной засыпке пазух фундаментов или траншей, так как работы ведут в стесненных условиях. В этих случаях грунт на ширину 0,8 м от фундамента уплотняют Слоями 15...20 см пневматическими и электрическими трамбовками, а верхние слои - более производительными малогабаритными катками, самопередвигающимися виброплитами и др. (рис. V. 31).
В процессе уплотнения необходимо контролировать достигаемую плотность грунта. Для этих целей в полевых условиях определяют плотность грунта, полученного с помощью цилиндра (кольца) объемом 50...100 см3 из шурфов, закладываемых в насыпи.
Однако этот способ контроля весьма трудоемкий. Применяют также плотномер конструкции Союздорнии. Этот прибор состоит из стержня, по которому скользит груз, наносящий при падении удар (энергией 1 Дж) по наконечнику площадью 1 см2 (для слабых грунтов - 2 см2). Число ударов, необходимых для погружения наконечника на 10 см, характеризует плотность грунта. Применяют также установку для просвечивания грунта гамма-лучами. В этом случае в грунт погружают на определенном расстоянии две трубы, в одну из которых закладывают какой-либо радиоактивный изотоп, а в другую - счетчик квантового излучения, измеряющий интенсивность радиации, которая зависит от плотности грунта, разделяющего обе трубы.
Уплотнение грунтов катками
Укатка выполняется самоходными и прицепными катками на пневматическом ходу. Усилие уплотнения достигается за счет высоких контактных напряжений, создаваемых силой тяжести катка и балластного пригруза на плоскости (линии) качения (до 8 МПа).
Пневмоколесные катки могут быть одноосные (массой 10 - 25 т), двухосные прицепные (массой до 50 т) и полуприцепные (одно-или двухосные массой до 100 т). Легкими катками требуемое уплотнение рыхлых грунтов слоем 20 - 30 см достигается при ширине захвата до 2,5 м. Тяжелые прицепные пневмокатки массой 25 - 50 т обеспечивают уплотнение грунта слоем 35 - 50 см при ширине захвата 2,5 - 3,3 м. Применение полуприцепных пневмокатков наиболее эффективно, они обеспечивают качественное уплотнение связных и несвязных грунтов слоем 40 - 50 см при ширине захвата 2,7 - 2,8 м. Все приведенные выше показатели получают за 4 - 12 проходов катка по одному следу (в зависимости от массы катка). Барабанные катки прицепные и самоходные являются менее эффективными по сравнению с кулачковыми в связи с большой площадью распределения давления.
Для повышения контактного давления на уплотняемый грунт и достижения высоких показателей используются кулачковые или решетчатые катки. Кулачки представляют собой стальные профильные штыри длиной 200 - 300 мм, приваренные по окружности к обечайке барабана. Такие катки применяются для уплотнения только связных грунтов. При уплотнении грунтов из крупнообломочных пород вместо кулачков на поверхность барабанов приваривают стальные решетки из уголка или другого стального профиля. Кулачковые и решетчатые катки обеспечивают уплотнение грунтов слоем 25 - 50 см при ширине захвата 2,7 - 3,3 м за 4 - 10 проходов по следу.
Укатка каждого слоя грунта осуществляется, как правило, по спирально-кольцевой схеме. Длина захватки принимается 250 - 300 м. При уплотнении грунтов на захватках малой ширины (затрудняются повороты катков) применяются главным образом самоходные барабанные катки, перемещающиеся по возвратно-поступательной схеме.
61. Трамбование и виброуплотнение грунтов.
Метод уплотнения грунта трамбованием основан на передаче уплотняемому грунту ударных нагрузок. В отличие от вибрационного и вибротрамбующего методов этот метод обладает значительно большей энергией удара за счет высокой скорости приложения нагрузки в момент соударения рабочего органа с грунтом, благодаря чему этот метод обеспечивает уплотнение
связных и несвязных грунтов слоями большой толщины (практически до 2 м). Метод уплотнения грунта трамбованием нашел наиболее широкое применение в промышленном строительстве при устройстве грунтовых подушек под основание фундаментов зданий и сооружений, технологическое оборудование и полы. Этот метод применяется также для вытрамбовывания котлованов в просадочных грунтах при устройстве столбчатых фундаментов.
Комбинированный метод уплотнения грунтов основан на использовании различного сочетания воздействия на грунт статических, вибрационных, вибротрамбующих и трамбующих нагрузок. Этот метод позволяет уплотнять все виды грунтов и применяется, главным образом, при широком фронте работ.
Метод уплотнения грунта вибрированием основан на передаче механических гармонических колебаний от рабочих органов (вальца, колеса, плиты, вибробулавы) на уплотняемый грунт. Метод вибрирования подразделяется на поверхностный и глубинный. Метод поверхностного виброуплотнения грунта характеризуется тем, что во время работы уплотняющий рабочий орган расположен на поверхности грунта и, совершая колебательные движения, воздействует на него. При глубинном методе уплотняющий рабочий орган во время работы находится внутри грунта.
Поверхностный вибрационный метод нашел применение при уплотнении несвязных и малосвязных грунтов обратных засыпок. Глубинный вибрационный метод можно эффективно использовать при уплотнении песчаных грунтов, особенно находящихся в водонасыщенном состоянии. В зависимости от основных параметров вибрации которыми являются частота и амплитуда колебаний, вибрационные машины для поверхностного уплотнения грунта могут работать также в виброударном режиме. Амплитуда их колебаний значительно больше, а частота колебаний меньше, чем у вибрационных машин, В этом случае вибрационные машины называются
вибротрамбующими, а метод уплотнения вибротрамбованием. Метод уплотнения грунтов вибротрамбованием нашел применение в строительстве при уплотнении обратных засыпок в стесненных местах.
62. Глубинное уплотнение грунтов.
Уплотнение грунтовыми сваими, вытеснение грунта при его радиальном уплотнение в процессе продавливания или пробивки скважин и в последствии их заполнение грунтом и послойном уплотнение
Способы глубинного уплотнения:
Физический
Замачивание
Дренированием (вертик. дренаж)
Механический
Виброуплотнение
Уплотнение грунта сваями
Уплотнение грунта пневмопробойниками
Уплотнение спералевидным рабочим органом
Уплотнение рабочим органом в виде винт-сваи
Комбинированное
Вода+ вибрация
(гидро-виброуплотнитель)
При уплотнении грунта необходимо обеспечить оптимальную влажность, при которой требуются наименьшие энергозатраты.
При последовательном уплотнение работы выполняются в шахматном порядке. Для формирования скважин применяется ударный метод. Продолжительность уплотнения 1 слоя- 30 сек. С нанесением 10-15 ударов. Для насыпных и просадочных грунтов на глубину 5-25 м. Поверхностный(буферный) слой стоит доуплотнять.
Глубинное виброуплотнение – для песчаных водонасыщенных оснований:пески насыпные и намывные.Реализация метода осуществляется путем последовательного погружения в грунт виброштанги при одновременной подачи через внутреннюю полость воды, после погружения виброштанги на требуемую глубинную подача воды прекращается и осуществляется в дополнение 4-5 подъема-опускания насуха. Глубинное уплотнение с предварительным замачиванием- для устройства просадочных свойств сниженных деформативностью и уплотнением грунтов: лессов, суглинков, пылеватых грунтов с высоким коэффициентом фильтрации не менее 0,2м/сут. Процесс уплотнения осуществляется под действием собственной массы грунта при замачивании, является достаточно длительным 2-3 месяца. Сокращение сроков уплотнения грунта до 3-7 суток достигается с применением дополнительного уплотнения за счет комуфлетных взрывов.
63. Контроль качества уплотнения грунтов.
Контролировать качество уплотнения грунтов можно следующими наиболее распространенными методами: стандартным, режущими кольцами, радиоизотопными, зондированием, вдавливанием штампа, парафинированием, методом лунок.Выбор того или другого метода зависит от оснащенности лаборатории оборудованием, характера сооружения, объема возводимой насыпи и их классности.Методом стандартного уплотнения определяют оптимальную влажность и максимальную стандартную плотность с помощью прибора СоюздорНИИ. Метод режущих колец при определении плотности скелета грунтов в насыпях основан на определении плотности влажного грунта в объеме металлического кольца вместимостью 300…400 см3 (d/h=l), вдавленного в уплотненный слой, и влажности этого грунта.В условиях полевых лабораторий метод режущих колец из-за простоты является наиболее приемлемым и распространенным.В настоящее время получили наибольшее распространение в строительной практике радиоизотопные методы, так как грунтовые полевые лаборатории на крупных земляных сооружениях были оснащены приборами, в которых используется поглощение и рассеяние гамма-излучения и нейтронов.Метод статического и динамического зондирования как один из видов контроля степени уплотнения грунтов в насыпях и обратных засыпках является наиболее оперативным и простым из всех существующих методов контроля.Метод вдавливания штампа применяют для определения прочности грунтовых оснований. В частности, этот метод широко используют для контроля качества уплотнения грунтов оснований под полы промышленных зданий и под фундаменты.Метод парафинирования применяют преимущественно при контроле за уплотнением грунта в зимних условиях.Метод лунок используют при укладке обратных засыпок из щебенистых крупнообломочных грунтов или из грунта с мерзлыми комьями.Качество уложенного в теле насыпи грунта можно считать допустимым, если число контрольных проб с плотностью грунта, отклоняющейся от заданной проектом, не превышает 10% общего числа контрольных проб, взятых на участке, и плотность скелета грунта в пробах должна быть не более чем на 0,5 г/см3 ниже плотности требуемой (минимальной).
64. Закрытая разработка грунтов способом прокола.
Прокол – это образование отверстий за счет радиального уплотнения грунта при вдавливании в него трубы с коническим наконечником. Вдавливание производят гидравлическим домкратом. В котловане укладывают звено трубы с наконечником и после выверки домкратом вдавливают в грунт на длину хода штока. После возвращения штока в начальное положение вводят на его место нажимной патрубок (шомпол), и процесс повторяется. По окончании вдавливания первого звена трубы на полную длину шомпол убирается, в котлован опускается следующее звено, которое приваривается встык к уже задавленному в грунт. Далее задавливают наваренное звено, и цикл повторяется достаточное количество раз до прокола на всю длину участка, который нельзя копать традиционным образом. За каждый цикл происходит продвижение трубы на 150мм. Этот метод практикуется в хорошо сжимаемых грунтах, отверстия «прокалывают» для труб диаметром от 100 до 400 мм на глубине более 3 м. В мало сжимаемых грунтах (песке, супеси) для обеспечения устойчивости стенок дополнительно к горизонтальному усилию необходимо применять поперечное и вибрационное воздействие. При этом выполняют отверстия диаметром до 300 мм.
65. Закрытая разработка грунта способом продавливания.
Метод применяется для прокладки стальных труб диаметром от500 ммдо1800 мм, либо коллекторов квадратного (прямоугольного) сечения на расстоянии до80 м. Технология следующая: в грунт последовательно вдавливают звенья труб, внутри которых грунт разрабатывается и удаляется посредством шнековой установки. В легко размываемых грунтах удаление производят гидромеханическим методом (струей воды размывают грунт внутри трубы и пульпу откачивают насосом). Часто трубы используют как футляры для размещения в них основных трубопроводов. Способ горизонтального бурения при закрытой разработке грунта.
Бурение применяют для прокладки в глинистых грунтах трубопроводов диаметром от 800 до1000 ммна длину до100 м. Конец трубы снабжается режущей коронкой увеличенного диаметра, труба приводится во вращения от мотора, установленного на бровке котлована. Поступательное движение трубе сообщает реечный домкрат с упором в заднюю стенку котлована. Грунт, заполняющий трубу изнутри, может удаляться через прокладываемую трубу с помощью шнековой установки гидромеханическим методом путем размыва грунта внутри трубы струей воды и последующей откачки пульпы насосом (в легкоразмываемых грунтах) или желонками с наращиванием их рукоятки.
Одно из важнейших свойств бетонной смеси - способность пластически растекаться под действием собственной массы или приложенной к ней нагрузки. Это и определяет сравнительную легкость изготовления из бетонной смеси изделий самого разнообразного профиля и возможность применения для ее уплотнения различных способов. При этом способ уплотнения и свойства смеси (ее подвижность или текучесть) находятся в тесной связи. Так, жесткие нетекучие смеси требуют энергичного уплотнения, и при формовании из них изделий следует применять интенсивную вибрацию или вибрацию с дополнительным прессованием (при - грузом). Возможны также и другие способы уплотнения жестких смесей - трамбование, прессование, прокат.
Подвижные смеси легко и эффективно уплотняются вибрацией. Применение же сжимающих (прессующих) видов уплотнения - прессования, проката, а также и трамбования-для таких смесей непригодно. Под действием значительных прессующих усилий или часто повторяющихся ударов трамбовки смесь будет легко вытекать из-под штампа или разбрызгиваться трамбовкой.
Литые смеси способны уплотняться под действием собственной массы. Для повышения эффекта уплотнения их иногда подвергают кратковременной вибрации.
Таким образом, могут быть выделены следующие способы Уплотнения бетонных смесей: вибрирование, прессование, прокат, трамбование и литье. Наиболее эффективным как в техническом, так и в экономическом отношениях является способ вибрирования. Его успешно применяют также в сочетании с другими способами
Механического уплотнения - трамбованием (вибротрамбование! прессованием (вибропрессование), прокатом (вибропрокат). рад" НОВИДНОСТЬЮ механических способов уплотнения ПОДВИЖНЫХ бетонных смесей является центрифугирование, используемое При формовании полых изделий трубчатого сечения. Хорошие результаты в отношении получения бетона высокого качества дает вакуумирование смеси в процессе ее механического уплотнения (преимущественно вибрированием), однако значительная продолжительность операции вакуумирования существенно снижает ее технико-экономический эффект, и поэтому этот способ мало распространен в технологии сборного железобетона.
Рассмотрим кратко сущность приведенных выше способов уплотнения бетонных смесей.
Вибрирование - уплотнение бетонной смеси в результате передачи ей часто повторяющихся вынужденных колебаний, в совокупности выражающихся встряхиванием. В каждый момент встряхивания частицы бетонной смеси находятся как бы в подвешенном состоянии и нарушается связь их с другими частицами. При последующем действии силы толчка частицы под собственной массой падают и занимают при этом более выгодное положение, при котором на них в меньшей степени могут воздействовать толчки. Это отвечает условию наиболее плотной их упаковки среди других, что в конечном итоге приводит к получению плотной бетонной смеси. Второй причиной уплотнения бетонной смеси при вибрировании является свойство переходить во временно текучее состояние под действием приложенных к ней внешних сил, которое называется тиксотропностью. Будучи в жидком состоянии, бетонная смесь при вибрировании начинает растекаться, приобретая конфигура - j цию формы, и под действием собственной массы уплотняться. У Третья причина уплотнения определяет высокие технические свой - II ства бетона. ,
Высокая степень уплотнения бетонной смеси вибрированием | достигается применением оборудования незначительной мощности. Например, бетонные массивы емкостью несколько кубометров уплотняют вибраторами с мощностью привода всего 1... 1,5 кВт.
Способность бетонных смесей переходить во временно текучее состояние под действием вибрации зависит от подвижности смеси и скорости перемещения при этом частиц ее относительно друг друга. Подвижные смеси легко переходят в текучее состояние и требуют небольшой скорости перемещения. Но с увеличением жесткости (уменьшением подвижности) бетонная смесь все более утрачивает это свойство или требует соответствующего увеличения скорости колебаний, т. е. необходимы более высокие затраты энергии на уплотнение.
Скорость v (см/с) колебаний при вибрировании выражают произведением амплитуды А на частоту п колебаний: и=Ап - При постоянной частоте колебаний вибромеханизма (для большинства виброплощадок равной 3000 кол/мин) изменение скорости колебаний может быть достигнуто изменением величины
Плитуды. Практика показала, что подвижные бетонные смеси ефективно уплотняются при амплитуде колебаний 0,3...0,35 мм,
А жесткие - 0,5...0,7 мм.
На качество виброуплотнения оказывают влияние не только параметры работы вибромеханизма (частота и амплитуда), но также продолжительность вибрирования. Для каждой бетонной смеси в зависимости от ее подвижности существует своя оптимальная продолжительность виброуплотнения, до которой смесь уплотняется эффективно, а сверх которой затраты энергии возрастают в значительно большей степени, чем происходит уплотнение смеси. Дальнейшее уплотнение вообще не дает прироста плотности. Более того, чрезмерно продолжительное вибрирование может привести к расслаиванию смеси, разделению ее на отдельные компоненты - цементный раствор и крупные зерна заполнителя, что в конечном счете приведет к неравномерной плотности изделия по сечению и снижению прочности в отдельных частях его.
Естественно, что продолжительное вибрирование невыгодно и в экономическом отношении: возрастают затраты электроэнергии и трудоемкость, снижается производительность формовочной линии.
Интенсивность И (см2/с3) виброуплотнения, выраженная наименьшей продолжительностью вибрирования, зависит также от основных параметров работы вибромеханизма - частоты и амплитуды колебаний, применяемых с учетом их взаимного сочетания скорости и ускорения колебаний: И = А2/п3.
Интенсивность виброуплотнения также возрастает, если частота вынужденных колебаний оказывается равной частоте собственных колебаний. В связи с тем что бетонная смесь имеет большой диапазон размеров частиц (от нескольких микрометров для цемента до нескольких сантиметров для крупного заполнителя) и соответственно различия в частоте их собственных колебаний, наиболее интенсивное уплотнение смеси будет в том случае, когда режим вибрирования характеризуется различными частотами. Так возникло предложение применять поличастотное вибрирование.
Эти факторы следует учитывать для технико-экономической оценки операций формования изделий. Из сказанного следует, что эффективность уплотнения возрастает с увеличением энергии уплотнения, продолжительность уплотнения при этом снижается и производительность формовочной линии повышается. Таким образом, на основании технико-экономического анализа свойств бетонной смеси, производительности формовочной линии можно выбрать мощность виброуплотняющих механизмов.
Виброуплотнение бетонной смеси производят переносными и стационарными вибромеханизмами. Применение переносных виб - Ромеханизмов в сборного железобетона ограничено. Их используют в основном при формовании крупноразмерных массивных изделий на стендах.
В технологии сборного железобетона на заводах, работающих
По поточно-агрегатной и конвейерной схемам, применяют вибр0 площадки. Виброплощадки отличаются большим разнообразием типов и конструкций вибраторов - электромеханические, электр0 магнитные, пневматические; характером колебаний - гармониче ские, ударные, комбинированные; формой колебаний - круговые направленные - вертикальные, горизонтальные; конструктивными схемами стола - со сплошной верхней рамой, образующей стол с одним или двумя вибрационными валами, и собранные из отдельных виброблоков, в целом представляющих общую вибрационную плоскость, на которой располагается форма с бетонной смесью.
Для прочности крепления формы к столу площадки предусматриваются специальные механизмы - электромагниты пневматические или механические прижимы.
Виброплощадка (рис. 11.1) представляет собой плоский стол, опирающийся через пружинные опоры на неподвижные опоры или раму (станину). Пружины предназначены гасить колебания стола и предупреждать этим их воздействие на опоры, иначе произойдет их разрушение. В нижней части к столу жестко прикреплен вибровал с расположенными на нем эксцентриками. При вращении вала от электромотора эксцентрики возбуждают колебания стола, передающиеся затем форме с бетонной смесью, в результате происходит ее уплотнение. Мощность виброплощадки оценивается ее грузоподъемностью (масса изделия вместе с формой), которая составляет 2...30 т.
Заводы сборного железобетона оборудованы унифицированными виброплощадками, с частотой вращения 3000 кол/мии и амплитудой 0,3...0,6 мм. Эти виброплощадки хорошо уплотняют жесткие бетонные смеси конструкций длиной до 18 м и шириной до 3,6 м.
При формовании изделий на виброплощадках, особенно из жестких бетонных смесей на пористых заполнителях, в целях улучшения структуры бетона используют пригрузы - статический,
Вибрационный, пневматический, вибропневматический. Величина пригруза в зависимости от свойств бетонной смеси составляет 2...5 кПа.
При формовании изделий в неподвижных формах уплотнение бетонной смеси производят с помощью поверхностных, глубинных и навесных вибраторов, которые крепят к форме. При изготовлении изделий в горизонтальных формах применяют жесткие или малоподвижные бетонные смеси, а при формовании в вертикаль-
ньіх формах (в кассетах) применяют подвижные смеси с осадой конуса 8...10 см.
Ф Прессование - редко применяемый способ уплотнения бетонки смеси в технологии сборного железобетона, хотя по техническим показателям отличается большой эффективностью, позволяя получать бетон высокой плотности и прочности при минимальном расходе цемента (100...150 кг/м3 бетона). Распространению способа прессования препятствуют исключительно экономические причины. Прессующее давление, при котором бетон начинает эффективно уплотняться, - 10...15 МПа и выше. Таким образом, для уплотнения изделия на каждый 1 м2 его следует приложить нагрузку, равную 10... 15 МН. Прессы такой мощности в технике применяют, например, для прессования корпусов судов, но стоимость их оказывается столь высокой, что полностью исключает экономическую целесообразность использования таких прессов.
В технологии сборного железобетона прессование используют как дополнительное приложение к бетонной смеси механической нагрузки при ее вибрировании. В этом случае потребная величина прессующего давления не выходит за пределы 500... 1000 Па. Технически такого давления достигают под действием статически приложенной нагрузки в результате принудительного перемещения отдельных частиц бетонной смеси.
Различают прессование штампами плоскими и профильными. Последние передают свой профиль бетонной смеси. Так формуют лестничные марши, некоторые виды ребристых панелей. В последнем случае способ прессования называют еще штампованием. Прокат является разновидностью прессования. В этом случае прессующее давление передается бетонной смеси только через небольшую площадь катка, что соответственно сокращает потребность в давлении прессования. Но здесь особую значимость приобретают пластические свойства бетонной смеси, связность ее массы. При недостаточной связности будет происходить сдвиг смеси прессующим валком и разрыв ее. Центрифугирование - уплотнение бетонной смеси В результате действия центробежных сил, возникающих в ней при вращении. Для этой цели применяют центрифуги (рис. 11.2), представляющие собой форму трубчатого сечения, которой в процессе уплотнения сообщается вращение до 600... 1000 мин^". Загруженная в форму бетонная смесь (обязательно подвижной консистенции) " под действием Центробежных сил, разви
вающихся при вращении, прижимается к внутренней повепх ности формы и уплотняется при этом. В результате различной плотности твердых компонентов бетонной смеси И ВОДЫ из бетоц ной смеси удаляется до 20...30% воды, что способствует получению бетона высокой плотности.
Способ центрифугирования сравнительно легко позволяет получать изделия из бетона высокой плотности, прочности (40...60 МПа) и долговечности. При этом для получения бетонной смеси высокой связности требуется большое количество цемента (400...450 кг/м3), иначе произойдет расслоение смеси под действием центробежных сил на мелкие и крупные зерна так как последние с большой силой будут стремиться прижаться К поверхности формы. Способом центрифугирования формуют трубы, опоры линий электропередач, стойки под светильники. При вакуумировании в бетонной смеси создается разрежение до 0,07...0,08 МПа и воздух, вовлеченный при ее приготовлении и укладке в форму, а также немного воды удаляется из бетонной смеси под действием этого разрежения: освободившиеся при этом места занимают твердые частицы и бетонная смесь приобретает повышенную плотность. Кроме того, наличие вакуума вызывает прессующее действие на бетонную смесь атмосферного давления, равного величине вакуума. Это также способствует уплотнению бетонной смеси. Вакуумирование сочетается, как правило, с вибрированием. В процессе вибрирования бетонной смеси, подвергнутой вакуумированию, происходит интенсивное заполнение твердыми компонентами пор, образовавшихся при вакуумировании на месте воздушных пузырьков и воды. Однако вакуумирование в техническом отношении имеет важный технико-экономический недостаток, а именно: большую продолжительность процесса - 1...2мин на каждый 1см толщины изделия в зависимости от свойств бетонной смеси и величины сечения. Толщина слоя, которая может быть подвергнута вакуумированию, не превышает 12... 15 см. Вследствие этого вакуумированию подвергают преимущественно массивные конструкции для придания поверхностному слою их особо высокой плотности. В технологии сборного железобетона вакуумирование практически не находит применения. wj
Технология возведения конструкций из бетона подразумевает приготовление бетонной смеси и ее уплотнение. Есть случаи, когда при замешивании раствора внутри появляются полости, которые могут нарушить структуру, снизить ее плотность. Из-за этого в изделии появляются трещины, что в конечном итоге способно привести к разрушению бетонных конструкций. В процессе уплотнения специалисты удаляют из раствора воздух, лишнюю жидкость, за счет чего он становится более плотным. Таким образом, изделие получается более прочным и долговечным.
Уплотнение бетона считается самым ответственным этапом укладки цементных смесей. От того, насколько тщательно будет выполнено это действие, будут зависеть коэффициент бетона и основные характеристики изделия. В ходе процедуры специалисты обрабатывают бетонную поверхность вручную или при помощи механических устройств, удаляя полости. Это позволяет добиться однородности бетонного раствора, увеличить сцепление состава с другими элементами конструкции.
Способы
Строители используют следующие виды устройств при уплотнении смеси:
- поверхностные (для верхнего слоя цемента);
- глубинные (крупные бетонные конструкции);
- наружные (устанавливаются перед уплотнением с краю деревянной опалубки или емкости с цементным раствором);
- виброплощадки (применяются на специализированных предприятиях).
Существует разные способы уплотнить цементный раствор:
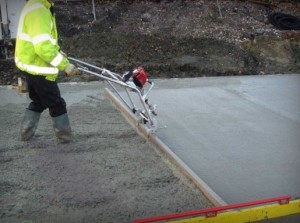
Другие способы
К другим методам уплотнения относятся:
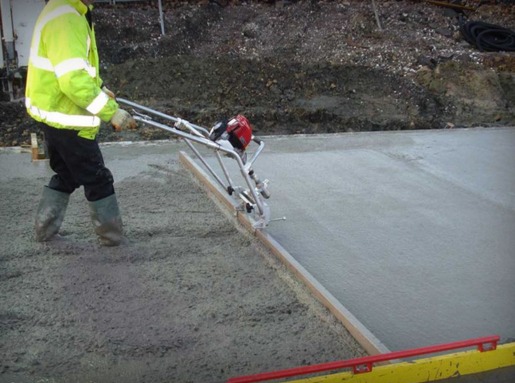
Чтобы цементный состав был равномерно уплотнен, необходимо придерживаться следующих рекомендаций:
- Во время установки деревянной опалубки следует обратить внимание на надежную фиксацию деталей. На элементах конструкции не должно быть щелей (раствор бетона может выдавливаться через трещины). Необходимо, что опалубка быта отшлифованной и гладкой, в противном случае она будет оставлять вмятины на изделии. К тому же впоследствии в теле конструкции могут образоваться пустоты.
- Детали деревянной или фанерной опалубки, в том числе клинья, должны надежно фиксироваться, чтобы не произошло смещение досок.
- При виброуплотнении состава следует периодически менять положение виброрейки, иначе раствор будет неоднородным, образуются полости.
- Специалисты советуют не тратить много времени на работы, поскольку это способно вызвать расслоение, которое появляется по причине того, что крупный щебень сбивается внизу, а наверху скапливается только раствор цемента.
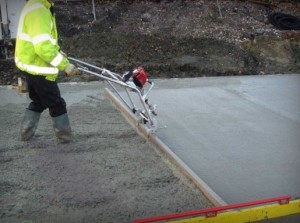
Поскольку использование поверхностных вибрирующих устройств не позволяет визуально определить степень плотности, при выполнении строительных работ часто применяют дополнительное средство, которое поможет гарантировать прочность состава. Для этого строители добавляют к имеющемуся составу раствор с высокой пластичностью. По этой причине возрастает риск расслаивания изделия. Чтобы избежать такого недостатка, советуют увеличить количество цемента.
Коэффициент уплотнения
Оценить качество бетонного состава можно при помощи одного важного критерия. Речь идет о коэффициенте уплотнения. Коэффициент определяется следующим образом: высчитывается соотношение удельной массы готовой смеси к значению, которое было получено при отсутствии пузырей воздуха внутри. Так, допустимым значением коэффициента считается 1. Достичь показателя можно разными способами уплотнения бетона, выбор методов будет зависеть непосредственно от состава, назначения и фракций. Автоматизированные виброрейки значительно увеличивают качество раствора.
От чего зависит коэффициент?
Этот показатель определяется зернистостью состава, а также объектом, который будет бетонироваться, будь то отмостки, трассы, дорожки.
Выводы
Опытные строители утверждают, что от будет зависеть устойчивость и долговечность конструкции. Это необходимо учитывать, если вы хотите, чтобы изделие прослужило вам не один год. Вовремя принятые меры помогут дополнительно повысить защиту конструкции от повреждений, сэкономить средства на реставрационных работах. Универсальные вибрационные устройства позволят получить высококачественный бетон. Перед выполнением строительных работ нужно заблаговременно проконсультироваться со специалистами и подобрать необходимое оборудование. Эргономичные виброустройства позволяют строителям уплотнять цемент в самых разных условиях.
Для выполнения небольшого объема строительных работ профессионалы рекомендуют пользоваться , весом до пяти килограммов. Для более масштабных работ строители применяют большие инструменты, позволяющие эффективно уплотнять бетон на производстве при большом фронте .