Сальник уплотнительный. Сальниковое уплотнение насоса. Конструкция сальниковых уплотнений
Сальниковые набивки ещё долго будут широко использоваться из-за своей простоты и низкой стоимости.
Стандарт распространяется на волокнистые и комбинированные сальниковые набивки, применяемые для заполнения сальниковых камер с целью герметизации подвижных и неподвижных соединений различных машин и аппаратов. Стандарт не распространяется на набивки специальных конструкций.
В Таблице 2 Приведены характеристики марок набивок по
В Таблице 3 приведены марки сальниковых набивок в зависимости от области применения.
Большинство набивок, упомянутых в , до сих пор востребованы и пользуются спросом в промышленности.
Сегодня производители уплотнительных материалов предлагают как традиционные набивки, так и более современные материалы, причём упор делается на набивки на основе и различных полимерных материалов (в основном ). Сегодня на рынке широко представлены материалы производства Российских и зарубежных компаний.
Крупнейшие Российские производители:
ОАО «Барнаульский завод Асбестовых Технических Изделий», ОАО «УралАТИ», ОАО "ВАТИ", ЗАО «Унихимтек - Графлекс», ООО «Силур», ЗАО "ТРЭМ Инжиниринг", и др.
Крупнейшие зарубежные производители:
Компании имеющие отношение к данному типу уплотнений:
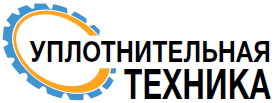
В процессе работы насоса возникают потери жидкости. Как правило, это происходит в месте присоединения его к трубопроводу. Чтобы ее избежать, необходимо использовать сальниковое уплотнение насоса. Именно об этом приспособлении пойдет речь.
Сальниковое уплотнение насоса
На современных центробежных наносах установлены различные конструктивные элементы и детали. При этом необходимо обеспечить нормальное функционирование не только отдельных элементов, но и всего оборудования. Сальниковое уплотнение насоса используется чаще, чем остальные способы. Причиной тому является простота конструкции, а также легкая установка.
Требования к уплотнителю
Бытовые насосы работают благодаря рабочему колесу, которое действует от двигателя. Как правило, он электрический. Вращение рабочего колеса происходит за счет энергии, поступающей от мотора через механическую муфту. Вал двигателя не находится в корпусе. Поэтому его герметичность нарушена. Из-за этого происходят утечки большого количества жидкости. Если использовать сальниковое уплотнение насоса, то проблемы можно избежать. Сегодня используются различные методы:
- Набивное уплотнение. Это круглая конструкция, состоящая из волокнистого материала.
- Манжетное уплотнение. В качестве данного уплотнителя используют материалы, которые хорошо работают на растяжение. Для увеличения жесткости конструкции используют армирование. Такой вид устанавливают на бытовые насосы, где скорость вращения вала имеет низкий показатель.
- Щелевое уплотнение. Оно имеет другое название - лабиринтное. Это самый надежный вид уплотнения. Он представляет собой круглую конструкцию, выполненную из мягкого материала. Данный тип монтируется на многоступенчатых насосах. Если на них устанавливать другие уплотнители, то это приведет к потере производительности агрегата.
- Торцевое сальниковое уплотнение. Этот тип представлен в виде двух колец, которые плотно расположены друг к другу. Первое выполняет вместе с рабочим валом, а второе статично.
Существует такое насосное оборудование, где использование уплотнителя не требуется. Это устройства, содержащие магнитную муфту.
Эксплуатация уплотнителей
Сальниковое уплотнение вала насоса применяется для обеспечения герметичности. Как правило, их используют для погружных типов, так как к ним не предъявляется особых требований по утечке жидкости. В этом случае более важным является длительный срок эксплуатации.
Сальниковые уплотнители появились на рынке вместе с приборами для перекачивания жидкости. Почему они так называются? Уплотнитель имеет круглую форму, состоящую из волокнистого материала. Данная форма изготовлена на сальниковой основе. Волокнистый материал должен постоянно смачиваться при помощи перекачиваемой жидкости. Она выступает не только в качестве смазки, но и как охлаждающий материал. Поэтому потери жидкости все равно не избежать. За один час работы расходуется до 15 л воды. Если не смачивать волокнистый материал, то он быстро сгорит и придется устанавливать новый.
Стоит отметить, что элементы нуждаются в постоянном обслуживании. Замена сальникового уплотнения производится без разбора насоса и двигателя. Это является существенным преимуществом. При этом не нужно вызывать специалиста. Подтягивание манжетов делается самостоятельно.
Конструкция сальниковых уплотнений
На сегодняшний день на рынке представлен широкий выбор сальниковых уплотнителей.
Основными видами являются:
- Армированный материал с одной кромкой. Служит для предотвращения протечек.
- Армированные манжеты с одной кромкой. Данное приспособление используется для защиты сальников от грязи, а также от потери жидкости при перекачке.
Кроме того, кромка может производиться в нескольких исполнениях:
- стандартные;
- с механической обработкой.
Уплотнители также разделяют по виду материала для резины, используемой в манжетах. Среди них выделяют такие материалы:
- Каучук. Из этого материала изготавливаются разные классы резины. Их главным преимуществом является способность выдерживать низкие температуры.
- Фторкаучук. Используется только для резины 1 и 2 классов. Способны выдерживать температуру до 170°С, которая достигается при перекачке вязкого масла.
- Силиконовый. Применяется только для резины 1 класса. Способен выдерживать температуру до -60°С.
Современные манжеты производят вместе с пружиной, которая нужна для уплотнения валов различного диаметра.
Характеристики уплотнительного материала
По сравнению с другими уплотнителями, манжеты отличаются гибкими и пластичными свойствами. Эксплуатационные особенности зависят от вида уплотнительного материала. В зависимости от структуры, они могут иметь диагональные плетения и в виде сердечка. Их состав также отличается, и может быть таким:
- могут содержать асбест;
- быть в сухом или пропитанном виде;
- армированными и неармированными.
Также используются сальниковые уплотнения и При монтаже следует учитывать, что некоторое количество перекачиваемой жидкости будет использоваться для смачивания уплотнителя.
Преимущества сальникового уплотнителя
Итак, манжет, служащий для перекачки жидкости, имеет вид плетеной веревки. Нити изготовлены из асбеста или хлопка. Иногда в них вставляется медная проволока. Середина состоит из свинца. При плетении может использоваться от 4 ниток.
Устанавливаются сальники со стороны всасывания. Однако, их можно монтировать и в других местах. Количество набивки зависит от диаметра вала.
Как подбирается сальник
Перед тем, как приобретать уплотнитель, необходимо рассмотреть ряд характеристик. Первым, и самым главным вопросом является показатель надежности. Еще один важный фактор - стоимость. Среди других критериев рассматривают:
- время эксплуатации;
- удельный показатель потери жидкости;
- срок службы;
- затраты на ремонт или замену.
Выбирать сальниковый уплотнитель необходимо, исходя из типоразмеров. Здесь смотрят на внешний и внутренний диаметр, а также толщину стенок.
Сальниковые уплотнения являются одним из видов уплотнений, которые встречаются наиболее часто. Несмотря на тот факт, что постепенно сальниковые уплотнения вытесняются другими конструкциями, к примеру, теми же торцевыми уплотнениями, сальниковые набивки еще на протяжении многих лет будут широко применяться благодаря своей низкой стоимости и простоте.
Согласно ГОСТ Р 52720-2007 Арматура трубопроводная. Термины и определения. Сальник (сальниковое уплотнение) – это уплотнение подвижных узлов (деталей) относительно окружающей среды, в котором применен уплотнительный элемент с принудительным созданием в нем напряжений, которые необходимы для того, чтобы обеспечить требуемую герметичность.
Конструкция, которую имеет сальниковый узел, является, пожалуй, одной из наиболее древних в уплотнительной технике конструкций. Собственно, название уплотнения – «сальниковое», уходит корнями в те времена, когда в качестве набивки применялись различные растительные волокна (пенька, лен), которые пропитывались животным жиром.
Сальниковые уплотнения используются там, где через крышку механизма или аппарата, либо же через неподвижный корпус проходит шток (вал), который совершает возвратно-поступательные либо вращательные движения. Принцип действия сальникового уплотнения состоит в следующем. На сальниковую набивку (уплотнительный материал), которая помещена в сальниковую камеру, оказывается давление, которое направлено вдоль оси штока (вала). В результате этого, за счет того, что в материале набивки происходит перераспределение усилий, она упирается в поверхность штока и стенки камеры.
Благодаря этому обеспечивается герметичность уплотнения, а также предотвращается проникновение рабочей среды за пределы корпуса арматуры. Особенность данной конструкции состоит в том, что к материалу набивки предъявляется ряд определенных, специфических требований, так как с одной стороны, набивка должна обеспечивать достаточный уровень герметичности на протяжении длительного периода времени, то есть, обладать упругими свойствами и износостойкостью. С другой стороны, она должна иметь с материалом штока минимальный коэффициент трения, чтобы не создавать работе механизма помех.
Понятно, что в одном материале очень непросто добиться сочетания таких противоречивых свойств. По этой причине для сальниковых узлов важную роль играют конструкторские решения, которые обеспечивают их нормальную работу. Помимо требований, которые предъявляются к уплотнительному материалу, определенный ряд требований также предъявляется к материалу и качеству обработки деталей (особенно штока или вала), габаритам, а также к конструкции узла запирания. Также следует заметить, что в отдельных случаях, особенно, когда шток (вал) совершает непрерывные перемещения, для того, чтобы продлить ресурс сальниковых набивок используют охлаждение сальникового узла и (или) смазку.
Таким образом, можно сформулировать ряд требований, которые предъявляются к сальниковым уплотнениям:
- Удобство монтажа;
- Стойкость к воздействию рабочей среды;
- Износоустойчивость;
- Упругость;
- Низкий коэффициент трения.
На сегодняшний день сальниковая набивка обычно имеет вид колец либо шнура из асбестосодержащего или безасбестного (на основе искусственных или натуральных волокон) материала. В более редких случаях в качестве набивки могут использоваться манжетные кольца, исполненные из различных материалов.
Конкретный тип набивки выбирается, исходя из таких параметров, как условия эксплуатации, параметры рабочей среды и конструкция сальникового узла.
Классификацию сальниковых набивок можно провести по ряду параметров. В представленной ниже Таблице 1 вы можете ознакомиться с классификационными признаками сальниковых набивок.
Как можно увидеть в представленной выше таблице, существует большое количество вариантов исполнения сальниковых набивок для получения необходимых свойств, соответствующих условиям эксплуатации сальникового узла.
До сих пор основным нормативным документом в данной области является ГОСТ 5152-84 Набивки сальниковые. Технические условия.
Данный стандарт распространяется на комбинированные и волокнистые сальниковые набивки, которые используются для заполнения сальниковых камер с целью герметизации неподвижных и подвижных соединений различных аппаратов и машин. Данный стандарт не распространяется на сальниковые набивки специальных конструкций.
В Таблице 2 вы можете ознакомиться с характеристиками марок набивок по ГОСТ 5152-84 .
Таблица
2
В Таблице 3 к вашему вниманию представлены марки сальниковых набивок в зависимости от области их применения.
Таблица
3
Основная часть набивок, которые упомянуты в ГОСТ 5152-84, и по сегодняшний день являются востребованными, и пользуются спросом в различных отраслях промышленности.
Сегодня производители различных уплотнительных материалов предлагают как традиционные виды набивок, так и более современные материалы, причем основной упор делается на набивки, сделанные на основе терморасширенного графита (ТРГ) и разнообразных полимерных материалов (в основном это фторопласт). На сегодняшний день на рынке в широком ассортименте предоставлены материалы, произведенные как российскими, так и зарубежными компаниями.
Из крупнейших российских производителей можно упомянуть ЗАО «ТРЭМ Инжиниринг», ООО «Силур», ЗАО «Унихимтек — Графлекс», ОАО «ВАТИ», ООО «Ильма», ОАО «УралАТИ», ОАО «Барнаульский завод Асбестовых Технических Изделий» и другие.
Крупнейшие зарубежные производители:
АВКО, Spetech, Kempchen, ProPACK, Latty, Simrit, GORE.
Ввиду того, что технология, а также спектр материалов для изготовления набивок является достаточно узким, у различных производителей номенклатура является очень близкой. В таблицах 4, 5 и 6 вы можете ознакомиться с набивками, которые выпускаются различными производителями, их параметрами эксплуатации и соответствием между собой. Причем для набивок, исполненных из терморасширенного графита, характерными являются высокие температурные и физико-механические свойства, а для набивок, исполненных из фторопласта – отличная химическая стойкость.
Терморасширенный графит является высокотехнологичным материалом, который получают из обыкновенного графита.
На первом этапе производится окисление исходного кристаллического графита. Окисление сводится к внедрению между слоями кристаллической решетки графита ионов и молекул азотной либо серной кислоты. После этого окисленный графит подвергают термической обработке до 1000 градусов по Цельсию со скоростью 400-600 градусов в секунду. Благодаря тому, что скорость нагрева является чрезвычайно высокой, происходит резкое выделение газообразных продуктов разложения внедренной азотной или серной кислоты из кристаллической решетки графита. В результате этого межслойное расстояние увеличивается приблизительно в триста раз, а объем – в 60-400 раз. Далее осуществляется прокатка полученного терморасширенного графита. Иногда этот материал армируют, добавляют различные присадки и прессуют для получения готовых изделий.
Обладая всеми полюсами графита, такими как низкий коэффициент трения, химическая стойкость, термостойкость, терморасширенный графит приобрел еще одно новое свойство – пластичность. Благодаря этому из него можно формовать изделия без введения какого-либо связующего. Данное свойство присуще терморасширенному графиту на протяжении всего срока его эксплуатации. На пластичность этого материала не оказывают влияния ни время, ни термоциклирование, ни повышение температуры.
В Таблице 4 вашему вниманию представлены наиболее распространенные на сегодняшний день набивки, главным компонентом в которых является терморасширенный графит.
Фторопласт – это материал, который обладает уникальными свойствами, среди которых высокая химическая стойкость, широкий диапазон температур эксплуатации, низкий коэффициент трения. К сожалению, вследствие хладотекучести фторопласта его эксплуатационные характеристики существенно снижаются. Одним из способов, который используют для понижения хладотекучести этого материала, является экспандирование.
Лента или жгут из фторопласта механическим способом экспандируется (вытягивается) в одном или двух направлениях. В результате этого материал приобретает характерную структуру, благодаря которой его свойства меняются.
С набивками из экспандированного фторопласта вы можете ознакомиться Таблице 5.