Публикации. Сальниковая набивка
Большая часть конструкций трубопроводной арматуры имеет сальниковое устройство для уплотнения подвижного соединения крышка - шпиндель с применением сальниковых набивок. Материалы сальниковых набивок должны обладать высокой упругостью, термостойкостью и химической стойкостью против действия рабочей среды и возможно малым коэффициентом трения. В качестве набивочных в основном применяют хлопчатобумажные и пеньковые материалы, асбестовый шнур, графит, тальк и полимерные материалы (стекловолокно, фторопласт) . Наиболее часто используют асбестовые плетеные шнуры квадратного или круглого сечения, а также скатанные шнуры без плетения или чесаные волокна (пенька и др.). Наиболее целесообразно применение набивки из заранее приготовленных и отформованных колец.
Хлопчатобумажную набивку , сухую или пропитанную, применяют в среде воды, воздуха, нефтепродуктов при давлении до 20МПа и температуре от минус 40 до 100 °С. Пеньковую набивку в сухом или пропитанном виде используют при давлении до 16 МПа и температуре от минус 40 до 100 ºС. Под действием кислот и щелочей, а также при высокой температуре хлопчатобумажная и пеньковая набивки теряют прочность и разрушаются, но они дешевы и доступны. Кольцевые манжеты из хлопчатобумажной ткани в виде прорезиненного материала (вулканизированного и графитизированного) марок МХБ, МЛ, МА используют для пара, воды, воздуха и нефтепродуктов при давлении до 40 МПа и температуре до 100 ºС.
Асбестовую набивку применяют в виде плетеных или специально отформованных шнуров. Асбестовые кольца укладывают последовательно в коробку сальника . Асбестовый шнур, пропитанный смазкой ЦИАТИМ-221, пригоден для температур от минус 50 до 70 ° С и давлений до 20 МПа; асбестовый шнур, пропитанный графитопарафиновой смазкой, - для температур от минус 200 до 50 °С и давлений до 4 Мпа. Применяют также разрезные асбестоалюминиевые кольца марки КРАА для нефтепродуктов. Для температур до 510 °С используют набивку типа "пушенка", состоящую из хлопьев асбеста, перемешанных с чешуйчатым графитом. Верхнее и нижнее кольца сальниковой набивки изготовляют из асбеста, а пространство между ними заполняют "пушенкой".
Резиновые кольца и манжеты в зависимости от марки применяют для воды, масел, нефтепродуктов, кислот, щелочей и при температуре от минус 50 до 140 ºС.
Графитовая набивка . Графит обладает высокой жаростойкостью (свыше 550 °С), химической стойкостью, хорошими антифрикционными свойствами, высокой теплопроводностью. Он не впитывает влагу. При наличии влаги графит образует с некоторыми сталями гальваническую пару и оказывает на них коррозирующее действие, поэтому графитовую набивку устанавливают в сальники арматуры непосредственно перед эксплуатацией, а шпиндель обычно азотируют во избежание износа.
В некоторых случаях используют гидрофобизирующую обработку шнуров из графитовых волокон олигомерными и высокомолекулярными компонентами по растворной или плазмохимической технологии, что позволяет осуществить герметизацию сопряжения и обеспечивает высокую износостойкость пары трения «шток-уплотнение». Уплотнительные комплекты представляют собой набор колец из гидрофобизированного графита, которые сверху и снизу герметизированы шнурами. Кольца имеют геометрические размеры с диаметром в диапазоне от 12 до 360 мм и толщиной в диапазоне от 10 до 25 мм. Позволяют увеличить прочность в 1,2-1,3 раза; термостойкость на 150-200 ºС; износостойкость (по сравнению с базовыми волокнами) в 1,5-2 раза; температуру рабочей среды до 600 ºС, и до 3000 °С - в инертной среде; повысить срок работы без специального обслуживания до 1000 ч.; стойкость к воздействию эксплуатационных сред, в т. ч. концентрированных и разбавленных растворов солей, кислот, щелочей (рис. 1.18).
Рис. 1.18.
Графитовые шнуры и прокладки после гидрофобизующей обработки.
Применяют чешуйчатый графит в виде пасты, очищенной от минеральных и органических примесей. Во избежание утечки через зазор между крышкой и шпинделем, сверху и снизу набивки ставят асбестовые кольца или прослаивают графит кольцами из паронита. Применяют также кольца и полукольца из прессованного графита. Графит используют для набивки и в виде различных мастик: графитоцерезиновая для температур до 80 °С при давлении до 1,6 МПа, асбестографитоцинковая для температур от минус 70 до 150 °С при давлении до 4 МПа.
Полимерная набивка . В качестве набивочных материалов в коррозионных средах используют фторопласт-4 в виде стружки, колец или манжет. Набивки из фторопластовых колец, манжет или стружки, смазанные смесями из графита, парафина и масла, применяют при температуре от минус 250 до 200 °С и давлении до 5 МПа. Фторопласт может выдерживать давления до 30 - 40 МПа при отдельных конструкциях манжет, исключающих ползучесть материала. При малых давлениях вместе с фторопластом применяют дополнительные упругие элементы - резину, пружину, так как фторопласт обладает небольшой упругостью. Для сальниковых набивок используют фторопластовый уплотнительный материал в виде шнура при температуре от минус 60 до 150 °С и давлении до 6,4 МПа.
Терморасширенный графит (ТРГ). В настоящее время в России начали производиться и поставляться уплотнительные элементы из терморасширенного графита для арматуры и фланцевых соединений энергетического оборудования. Данный вид уплотнения на основе терморасширенного графита используется взамен устаревших из металла, паронита и из других асбестосодержащих материалов, что значительно повысило надежность и долговечность этих узлов.
Все конструкторско-технологические работы по изготовлению арматуры обладают высокой степенью новизны (на уровне изобретений) с применением новейших материалов («металлорезины», изделий из любой керамики: карбида кремния, оксида алюминия, циркония, стекла, твердого сплава) и современных технологий (карбонитрирование, диффузионное хромирование, хромонитри-дизация, лазерные термообработка и сварка, наплавки неметаллов, диффузионная пайка разнородных материалов, прецизионная алмазная доводка до оптической плоскости, антикоррозионные покрытия).
Терморасширенный графит - специфический материал со свойствами, присущими графиту, с одной стороны, и с дополнительными свойствами, отличными от электрографита или графитоутольных композиций, применяемых, например, в торцовых уплотнениях. Если добавить к основным свойствам графита упругость и сжимаемость, то вы получите представление о терморасширенном графите, но в первую очередь терморасширенный графит применяется не как конструкционный материал, а как материал для изготовления фланцевых эластичных прокладок, спирально - навитых прокладок, сальниковой набивки с превосходными характеристиками.
Аналогом терморасширенного графита, является широко известный материал графлекс. Однако технология применяемая при изготовлении изделий из терморасширенного графита позволяет существенно снизить себестоимость производства и повысить качество конечного продукта.
Терморасширенный графит - это уплотнительный материал нового поколения. Обладая всеми положительными качествами графита - термостойкостью, химстойкостью, низким коэффициентом трения, терморасширенный графит дополнительно приобретает совершенно новое свойство - пластичность. И это свойство остается присуще ему на весь срок службы.
Ни повышенные температуры, ни термоциклирование, ни время на пластичность графита не влияют. Уплотнения из ТРГ очень надежны и не требуют обслуживания. Асбест с течением времени теряет эластичность, массу и объем и его необходимо время от времени подтягивать, графит лишен этого недостатка. Фторопласт не выдерживает высоких температур и давлений, графит работает при 560°С и 400 атм. Углеродные набивки так же выдерживают большие температуры, но они проницаемы для газов и жидкостей, графит абсолютно непроницаем уже при плотности 1 г/см3. Он предназначен для работы с кислотами и щелочами, нефтью и питьевой водой. Ресурс работы по пути скольжения: асбест - 600 метров; графит - 10 000 метров. Графит очень мягкий, поэтому оказывает минимальное воздействие на шток задвижки и вал насоса.
Графитовые и металло-графитовые фланцевые уплотнения применяются для герметизации арматуры, трубопроводов, теплообменников, компрессоров, сосудов высокого давления, насосных агрегатов и другого технологического оборудования. Уплотнения характеризуются повышенным ресурсом работы, абсолютной экологической чистотой и не подверженностью старению. Возможна работа в агрессивных средах при повышенных температурах. Сальниковые графитовые уплотнения применяются на сальниковых разъемах, преимущественно, с вращательным движением вала, позволяют герметизировать изношенные фланцы. Сальниковые графитовые уплотнения так же характеризуются повышенным ресурсом работы, абсолютной экологической чистотой и не подверженностью старению. Возможна работа в агрессивных средах при повышенных температурах (рис. 1.19 ).
Рис. 1.19.
Сальниковые графитовые уплотнения.
Графитовые фланцевые уплотнения применяются для герметизации арматуры, трубопроводов, теплообменников, компрессоров и другого технологического оборудования. Уплотнения характеризуются повышенным ресурсом работы, абсолютной экологической чистотой и не подверженностью старению. Возможна работа в агрессивных средах при повышенных температурах. Графитовые фланцевые уплотнения применяются на разъемах типа "шип-паз". Применяются при температуре от минус 150 до 550 ºС (воздух), до 3000 °С (инертная среды); при рабочем давлении до 100 МПа; агрессивности среды рН от 0 до 14 (рис. 1.20 ).
Рис. 1.20.
Графитовые фланцевые уплотнения
.
Металло-графитовые фланцевые уплотнения применяются для герметизации трубопроводов, теплообменников, сосудов высокого давления и другого технологического оборудования. Уплотнения характеризуются повышенным ресурсом работы, абсолютной экологической чистотой и не подверженностью старению. Возможна работа в агрессивных средах при повышенных температурах. Металло-графитовые фланцевые уплотнения применяются на любых разъемах, преимущественно типа "гладкий фланец". Применяются при температуре от минус 150 до 200 °С (воздух), до 3000 °С (инертная среды); при рабочем давлении до 200 МПа; агрессивности среды рН от 0 до 14 (рис. 1.21 ).
Рис. 1.21.
Металло-графитовые уплотнения.
Сальниковые графитовые уплотнения применяются на сальниковых разъемах, преимущественно, с вращательным движением вала. Позволяют герметизировать, в том числе изношенные фланцы. Сальниковые графитовые уплотнения характеризуются повышенным ресурсом работы, абсолютной экологической чистотой и не подверженностью старению. Возможна работа в агрессивных средах при повышенных температурах. Применяются при температуре от минус 150 до плюс 550 °С (воздух), до плюс 3000 ºС (инертная среды); при рабочем давлении до 100 МПа; агрессивности среды рН от 0 до 14 (рис. 1.22 ).
Рис. 1.22.
Сальниковые графитовые уплотнения.
Армированный графитовый лист - композитный материал, состоящий из слоев гладкой или перфорированной стали, плакированной графитовой фольгой. Применяется для изготовления армированных прокладок, для герметизации фланцевых соединений арматуры и трубопроводов при температурах от минус 196 °С до 600 °С и давлении до 40 МПа и для двигателей внутреннего сгорания. Производятся однослойными и многослойными с количеством армирующих слоев от 1 до 5.
Уплотнительная лента ГРАФЛЕКС Л-200 . Лента ГРАФЛЕКС Л-200 (ЛК-ЭФ) предназначена для уплотнения статичных фланцевых соединений простой и сложной конфигураций в диапазоне давлений от полного вакуума до 20 МПа, температур от минус 240 °С до 260 °С, кратковременно до 310 °С, в зависимости от типа фланцевого соединения и конкретных условий эксплуатации трубопроводов и оборудования (рис. 1.23 ).
Рис. 1.23.
Уплотнительная лента.
Лента применяется взамен традиционных прокладок из картона, паронита, фторопласта Ф-4, жгута ФУМ и др. в газонефтедобывающеи, газонефтеперерабатывающей, химической, фармацевтической, пищевой промышленности, в тепловой и ядерной энергетике и других отраслях. Наибольшее применение лента получила при герметизации фланцевых соединений теплообменного оборудования (кожухотрубные теплообменники: крышки подогревателей низкого давления, сетевых подогревателей, маслоохладители, воздухоохладители, крышки арматуры, крышки сосудов и аппаратов, люки конденсаторов, напорные резервуары, колонны, испарители и т. д.). Лента из экспандированного фторопласта изготавливается из 100% первичного фторопласта (политетрафторэтилена PTFE) по специальной технологии. В результате обработки фторопласт приобретает направленную специально ориентированную волокнистую структуру. Материал ленты, сохранив все химические характеристики традиционного фторопласта, приобретает новые уникальные физические свойства.
Набивка плетеная «ТМГ» изготавливается из графитовой фольги "Термографенит" (ТМГ), с армированной хлопчатобумажной нитью, стекловолокном или металлической проволокой, в виде плетеного шнура квадратного, круглого, прямоугольного сечения, сквозного плетения с однослойным и многослойным плетением, двухрядного, трехрядного или четырехрядного диагонального плетения. Выпускается с сечением от 3х3 мм до 50x50 мм и плотностью (0,8 - 1,2) г/см3. Предназначена для уплотнения сальниковых камер насосов и арматуры, подвижных и неподвижных соединений разнообразных машин и аппаратов (рис. 1.24 ).
Низкий коэффициент трения и высокая теплопроводность позволяют эксплуатировать центробежные насосы в режиме с минимальным прокапыванием, при использовании теплоотводных колец ТМГ типа С без прокапывания. Применение набивок ТМГ практически исключает механический и коррозионный износ штоков арматуры и валов насосного оборудования. Благодаря этому набивка ТМГ увеличивает срок межремонтной эксплуатации центробежных насосов в 2 - 5 раз, трубопроводной арматуры в 3 - 5 раз в сравнении с асбестовыми и, таким образом, обеспечивает высокую эффективность ее использования.
Рис. 1.24.
Набивка плетеная.
Фольга графитовая «ТМГ». Гибкая графитовая фольга из терморасширенного графита марки "Термографенит" (ТМГ), изготавливаемая по технологии, которая содержит специальные методы очистки, химической и термической обработки природного кристаллического графита с последующей прокаткой без связующих веществ, и внедрена в производство научно - производственным предприятием ООО "ТМСпецмаш" (рис. 1.25 ).
Рис. 1.25.
Фольга графитовая.
Основное применение фольги "ТМГ" - производство сальниковых уплотнений для трубопроводной арматуры, центробежных насосов, прокладок для фланцевых соединений.
Термостойкость на воздухе - 450°С, при обжатии во фланцах - 600°С, в условиях водяного пара - 560°С, в инертной среде - 3000°С. Фольга ТМГ химически и биологически инертна (применяется при рН = 0 - 14), радиационностойкая, нетоксичная, не поддерживает горения, пожаро- и взрывобезопасная, не стареет, имеет антифрикционные свойства, не изнашивает валы и штоки.
Кольца уплотнительные «ТМГ» применяются при уплотнении подвижных и неподвижных соединений трубопроводной арматуры, центробежных, вихревых и поршневых насосов, машин и аппаратов, которые используются в энергетической, нефтехимической, химической, перерабатывающей и других отраслях производства. Использование колец "Термографенит" (ТМГ) увеличивает межремонтный период эксплуатации: регулирующей трубопроводной арматуры в 3 - 5 раз, центробежных насосов в 5 - 12 раз.
Спирально-навитые прокладки "ТМГ" применяются для уплотнения "гладких" фланцевых соединений, типа "выступ-впадина", "шип-паз", арматуры трубопроводов, сосудов, аппаратов, насосов и аналогичного оборудования химической, нефтеперерабатывающей и других отраслей промышленности при температуре рабочей среды от минус 196 °С до 600 °С и давления до 25 МПа.
Спирально-навитая прокладка (СНП) состоит (рис. 1.26 ) из слоев профилированной холоднокатаной коррозионностойкой стальной ленты (2) и ленты наполнителя - гибкой ленты из терморасширенного графита "Термографенит" (3).
Рис. 1.26.
Спирально-навитая прокладка: 1 - внешнее ограничительное кольцо; 2 - стальная
лента;3 - ТМГ лента; 4 - внутреннее ограничительное кольцо;
По форме сечения все типы СНП имеют V-образный профиль. Уплотнение происходит за счет заполнения наполнителем микронеровностей фланцев при обжатии, а металлическая лента выполняет роль упругого каркаса. Благодаря уникальным упруго-пластичным характеристикам ленты "Термографенит", СНП сохраняет уплотнительные свойства при ослаблении затяжки болтов, вибрациях, термическом расширении, пульсации давления в трубопроводах и т. д.
В зависимости от типа фланцевого соединения прокладки оснащаются ограничительными кольцами:
- для фланцев типа "выступ-впадина" применяют внутреннее ограничительное кольцо;
- для "гладких" фланцев - внешнее или/и внутреннее кольца.
Ограничительные кольца предназначены для:
- защиты спирально-навитой части от разрыва рабочим давлением;
- защиты спирально-навитой части от переобжатия во время монтажа;
- центрирования прокладки, поскольку внешний диаметр ограничительного кольца равен внутреннему диаметру кольца, по которому размещаются болты крепления фланца.
Материал внутренних колец - коррозионностойкая сталь, внешних - углеродистая сталь. Материал наполнителя-фольга "Термографенит", толщиной 0,60±0,05 мм, плотностью 1,0 ± 0,08 г/см.
В большинстве устройств трубопроводной арматуры герметичность подвижного соединения «крышка─шпиндель (шток)» обеспечивают, применяя сальник (сальниковое уплотнение). Устройство сальникового уплотнения обязательно включает сальниковую набивку, состоящую из одного или нескольких элементов, изготовленных из упругого, легко деформируемого материала.
Способы изготовления сальниковой набивки
Преимущества сальникового уплотнения ─ невысокая стоимость и легкость замены. Кстати, в большинстве случаев, когда говорят «замена сальника», подразумевают именно замену набивки сальниковой.
Сальниковая набивка может изготавливаться различными способами. Одним из наиболее часто применяемых для заполнения сальниковых камер трубопроводной арматуры уплотнительных материалов являются плетеные набивки. Способы их изготовления ─ однослойное оплетение сердечника, многослойное плетение, сквозное плетение. Наряду с плетенными применяют крученные и скатанные сальниковые набивки. Сальниковая набивка может иметь форму не только шнура (прямоугольного (в т. ч. квадратного) или круглого сечения), но и состоять из одного или нескольких соответствующим образом отформованных колец.
Как работает и какие задачи решает сальниковая набивка
Помещенная в специальную полость (камеру сальникового уплотнения, называемую также коробкой), сальниковая набивка под воздействием регулирующего нагрузку устройства сжимается вдоль оси штока или шпинделя. Сила упругости заставляет составляющие ее элементы (или один элемент) расширяться в перпендикулярном этой оси направлении, заполняя зазор между штоком (шпинделем) и стенками отверстия в крышке. Зазор, заполненный сальниковой набивкой, становится герметичным.
Гарантировать максимально высокую герметичность трубопроводной арматуры в течение всего срока эксплуатации ─ не единственная задача сальникового уплотнения. Очень важно, чтобы ее выполнение сопровождалось как можно меньшим трением в зоне контакта сальниковой набивки с подвижными деталями. Так можно избежать быстрого износа штока (шпинделя) и самого сальника, а также сократить затраты энергии при эксплуатации арматуры, управляемой с использованием механизированного привода.
Выбор материалов, используемых для изготовления сальниковой набивки
В решающей степени функциональные возможности и эффективность сальникового уплотнения определяются свойствами материала сальниковой набивки. Чтобы обеспечить успешное решение стоящих перед сальниковым уплотнением задач, она должна обладать целым спектром качеств, важнейшим среди которых наряду с как можно меньшим коэффициентом трения является даже не одна, а сразу несколько «стойкостей». Химическая стойкость к уплотняемым рабочим средам. Термическая стойкость к воздействию высоких и низких температур. Механическая стойкость к износу и различным механическим воздействиям.
Набивка сальниковых уплотнений может выполняться из различных материалов. Из натуральных волокон (хлопка или лубяных культур), волокон минерального происхождения (пряжа из асбеста), химических волокон, а также минеральных порошков, минеральных масел, полимеров, металлов. Необходимые свойства сальниковой набивки акцентируют, применяя пропитки и наполнители. Конкретный выбор материала для сальниковой набивки определяется химическими и физическими свойствами рабочей среды, ее температурой и давлением, степенью ответственности арматуры, ее конструкцией и рядом других факторов.
Сальниковые набивки из хлопчатобумажных материалов и пеньки
Широкое распространение получили хлопчатобумажные набивки, как плетенные (набивка сальниковая ХБП, пропитанная антифрикционным жировым составом, графитированная), так и прорезиненные скатанные ─ ХБР и ХБРС (дополнительно «снаряжена» резиновым сердечником). «Усиленные» резиной, они используются для газов (воздух, CO2, NH3), пара, воды, минеральных масел. Производятся сухие и пропитанные хлопчатобумажные набивки с лубяным сердечником.
Под прилагательным «пеньковые» (например, сальниковая набивка пеньковая) объединены не только набивки из волокон конопли, но и других лубяных культур ─ джутовых, льняных и т. д. Пример ─ сальниковая набивка марки ПП ─ плетенная из лубяных волокон, пропитанная жировым антифрикционным составом, графитированная.
У давно используемых для герметизации различных технических устройств, включая сальниковые уплотнения трубопроводной арматуры, набивок из растительных волокон есть неоспоримое преимущество ─ невысокая цена. «Расплачиваться» за нее приходится относительно невысокой стойкостью к внешним воздействиям, а, значит, принципиальной невозможностью использования при определенных эксплуатационных режимах или, если эксплуатация и допустима, необходимостью частой замены. При воздействии растворов щелочей, кислот, высоких (свыше 100°C) или низких (ниже минус 40°C) температур они становятся менее прочными и могут полностью разрушиться.
Использование пеньковой набивки, создающей достаточно большое трение, способно привести к износу шпинделей и штоков трубопроводной арматуры в местах набивки, если ее функционирование связано с их частым перемещением.
Не выносят сальниковые набивки из растительных волокон и очень высокого давления. Для хлопчатобумажной его верхняя планка составляет порядка 20 МПа, а для пеньковой ─ даже несколько меньше.
Но для трубопроводной арматуры, когда рабочей средой является вода с температурой до 100°C, сухие или пропитанные сальниковые набивки из растительных волокон ─ вариант вполне приемлемый. При «поддержке» таких материалов, как резина и графит, возможности сальниковых набивок из растительных волокон существенно возрастают. Имеющие различную конфигурацию (сечение) уплотненные в пресс-формах, вулканизированные, цельноскатанные, многослойные, графитированные резинотканевые кольцевые манжеты (МХБ ─ из хлопчатобумажной ткани и МЛ ─ из льняной) можно использовать в среде инертных газов, воздуха, воды (не только питьевой), пара, нефтепродуктов при давлении до 40 МПа (400 кгс/см²).
Набивки сальниковые асбестовые
Набивки сальниковые асбестовые используются для герметизации подвижных соединений трубопроводной арматуры, работающей в нейтральных и агрессивных средах. В зависимости от состава пропитки их применяют в арматуре, управляющей потоками воды, щелочей, нефтепродуктов, газообразными средами, паром.
Производители предлагают широкий ассортимент сальниковых асбестовых набивок. Плетенные ─ марок АГИ, АП-31, АСП-31, АПР, АПР-31, АПРПП, АПРПС, АС, АСП, АСС, АФ-1, АФВ, АФТ, ПАФС; скатанные ─ марок АР (скатанная прорезиненная), АРС (скатанная прорезиненная с резиновым сердечником); крученные, например, АПК-31, пропитанная жировым антифрикционным составом на основе нефтяных экстрактов, графитированная.
Широко распространены сальниковые набивки марок АС ─ асбестовая плетенная сухая и АСС ─ то же, только с сердечником из стеклоровинга. Сердечник из стеклоровинга (жгута из стекловолокна) есть у асбестовых набивок марок АСП и АСП-31. Жировым антифрикционным составом на основе нефтяных экстрактов пропитаны графитированные асбестовые сальниковые набивки АП-31, АСП-31, АПР-31. Для пропитки асбестовых сальниковых набивок также используются суспензии фторопласта (АФ-1) или фторопласта и талька (марка АФТ). Плетеные набивки АПРПС и АПРПП дополнительно усилены латунной проволокой.
Сальниковая набивка из асбеста работоспособна в широком диапазоне температур: от −70 до +300°C.
Асбест не очень хорошо переносит воздействие влаги, но пропитка маслом позволяет повысить его влагостойкость. Для набивки сальников также используется смесь чешуйчатого графита и хлопьев асбеста, удерживаемая в сальниковой камере асбестовыми кольцами. Между асбестовыми кольцами могут устанавливаться графитовые втулки, а сами кольца обильно протираться графитом, обладающим уникальной способностью снижать трение.
Сальниковая набивка графитовая
Для изготовления графитовых сальниковых набивок часто используют т. н. терморасширенный графит (сокращенно ТРГ) ─ модификацию природного графита, состоящую из чистого углерода. Чем чище ТРГ, тем выше его эксплуатационные параметры. Его применение позволяет существенно повысить стойкость сальниковых уплотнений при высоких температурах и давлении. Это следствие уникальных свойств материала ─ высокой термостойкости, химической инертности, упругости, низкий коэффициент трения. Терморасширенный графит ─ экологически чистый материал, сохраняющий стабильность свойств на протяжении длительного времени эксплуатации. Например, сальниковое уплотнение из графита может проработать многие годы без замены материала набивки и не требуя его добавления. Графитовая набивка сальникового уплотнения, пожалуй, наиболее надежная среди всех набивок, работающих при высоких температурах.
Графит применяют для набивки сальников в форме мастик, например, графитоцерезиновой или асбестографитоцинковой. Или в виде порошка, например, в смеси порошков графита и фторопласта. Такое сочетание позволяет обеспечить герметичность сальникового уплотнения и минимальный износ штока и шпинделя.
Из графитовой фольги изготавливают плетеную набивку, армированную хлопчатобумажной нитью, стекловолокном, металлической проволокой. В последнем варианте термостойкость сальниковой набивки увеличивается до более чем 600 градусов Цельсия.
Набивка сальниковая фторопластовая
Важный сегмент сальниковых набивок составляют набивки из фторопласта. Фторопласт, он же политетрафторэтилен (Polytetrafluoroethylene, PTFE) или тефлон (торговая марка), был получен перед самым началом Второй Мировой войны, но в действительно широких масштабах его начали использовать уже после ее окончания. Фторопласт стал одним из знаковых изобретений из числа тех, с которыми ассоциируется понятие «научно-технический прогресс». О фторопласте знают почти все, хотя бы по посуде с антипригарным тефлоновым покрытием. Но это, конечно, всего лишь одна из граней его применения. Фторопласт (PTFE) — эффективный материал для сальниковых уплотнений. Его достоинства: высокая устойчивость ко всему спектру внешних воздействий ─ химических (химическая инертность у фторопласта одна из самых высоких у полимеров), механических, термических. Следствие этого ─ долгий срок службы. Важное достоинство фторопласта ─ низкий коэффициент трения, один из наименьших среди материалов, применяемых для уплотнения, поэтому фторопласт ─ гарантия отличного скольжения штока (шпинделя).
В качестве сальниковой набивки фторопласт обеспечивает герметичность при работе с различными рабочими средами: водой, паром, газом, кислотами, маслом, хладагентами. Благодаря низкой теплопроводности его можно использовать при высоких температурах.
Впрочем, есть некоторые факторы, ограничивающие использование фторопласта в качестве материала сальниковых набивок. При высоких температурах он набухает в жидких фторуглеродах, а даже при комнатной незначительно увеличивает свой объем при контакте с фреонами. Не смачиваясь водой при кратковременном погружении в нее, фторопласт все-таки смачивается при продолжительном, измеряемом десятками суток, контакте с дистилированной водой.
Набивка сальниковая фторопластовая может изготавливаться как из чистого политетрафторэтилена, так и из фторопласта с наполнителями, например, графитонаполненного. Насыщение фторопластовой пряжи графитом с формированием связей между ним и фторопластом на молекулярном уровне позволяет изготавливать сальниковые набивки, обладающие уникальными, еще более ярко выраженными, чем у чистого фторопласта, качествами.
Фторопластовая пряжа может состоять из тонкой крученой ленты или из большого числа скрученных длинных тонких волокон. Во втором случае сальниковая набивка получается более плотной.
Широкое распространение сальниковых уплотнений в трубопроводной арматуре обусловлено целым рядом их достоинств. Наряду с невысокой себестоимостью и технологической функциональностью, значимое место в этом ряду занимает возможность выбора материалов для сальниковых набивок. Благодаря развитию науки и промышленных технологий со временем она только расширяется, а, значит, увеличивается потенциал сальникового уплотнения как конструктивного решения, призванного обеспечить, пожалуй, самое главное качество трубопроводной арматуры ─ герметичность.
INFLUENCE OF GRAFLEX SEALANTS ON THE ROTARY AND PLUNGER PUMP STUFFING BOX CONSTRUCTIONS
Авдеев В.В., д.т.н., профессор, ген. директор
Ильин Е.Т., к.т.н., доцент, зам. ген. директора по технической политике
Уланов Г.А., главный конструктор
Abstract. The present work observes performance of a pump stuffing box sealant under the environmental and compression forces treatment. Comparison was made berween the interaction of custom sealants and "Graflex" sealants with sealed surfaces. Recommendations were given for stuffing box modification under "Graflex" sealants usage. "Graflex" utilization efficiency was estimated in comparison to the custom sealants.
Наиболее широкое распространение в узлах уплотнения валов центробежных насосов получили давно известные и простые по конструкции мягкие сальниковые набивки . Большинство выпускаемых мягких сальниковых набивок состоит из волокнистой сплетенной основы, пропитанной смазочным материалом с добавками антифрикционных веществ (графита, талька и др.).
Герметичность сальника определяется в первую очередь гидравлическим сопротивлением набивки, оказываемым ею уплотняемой рабочей среде и степенью прижатия ее к уплотняемым деталям . В реальных условиях эксплуатации на сальниковую набивку действует, с одной стороны, усилие затяжки сальника, а с другой стороны - давление рабочей среды, в результате чего происходит пластическая деформация материала и его уплотнение, обеспечивающее снижение пористости и проницаемости.
Вместе с тем, в процессе эксплуатации происходит износ сальниковой набивки, сопровождающийся выносом материала за пределы сальниковой камеры. Герметичность сальникового уплотнения в процессе износа снижается и требует периодического восстановления. Износ материала набивки зависит от ряда факторов, главными из которых являются шероховатость поверхности подвижной уплотняемой детали, вид движения относительно набивки (возвратно-поступательный или вращательный), интенсивность движения, контактное давление набивки на вал, давление уплотняемой рабочей среды, агрегатное состояние и физико-химические свойства уплотняемой среды, прочность внутренних связей материала набивки.
Для восстановления заданной степени герметичности применяется подтяжка сальника. Трудность восстановления герметичности сальника, снизившейся в результате механического износа набивки, путем подтяжки сальника можно объяснить следующим образом. Тонкий слой набивки, прилегающий к перемещающейся уплотняемой детали, подвергается износу и разрушению. Вследствие истирания подвижной деталью пористость материала в этом тонком слое более высокая, чем в остальном объеме набивки. Снижение пористости этого слоя можно было бы осуществлять за счет осевого сжатия и заполнения пустот материалом из основного слоя. Заполнение таких пустот материалом набивки в значительной степени зависит от пластических свойств материала, характеризуемых коэффициентом бокового давления (Кб), который определяет долю осевого усилия приложенного к уплотняющему элементу, передаваемую в радиальном направлении (для большинства традиционно применяемых плетеных набивок типа АП, АС, АПР, АГИ Кб=0,35-0,45). В процессе эксплуатации, при периодических подтяжках сальника, материал набивки уплотняется, теряет пластичность и способность к деформации в осевом и радиальном направлениях. Поэтому приходится прилагать все большее осевое усилие, чтобы обеспечить герметизацию узла, пока не наступит момент, когда обжатие сальника уже не обеспечивает герметичности узла и требуется замена уплотнителя.
К сказанному выше следует добавить, что осевое усилие, приложенное к набивке, существенно уменьшается по глубине сальниковой камеры, в связи с трением набивки о стенки камеры и гильзу вала , а также вследствие внутреннего трения в самой набивке, возникающего при сжатии. В свою очередь сила трения набивки о сопрягаемые поверхности зависит от шероховатости гильзы и стенок сальниковой камеры, а значит и распределение усилий по глубине сальниковой камеры зависит от этих факторов. Так как каждое кольцо набивки вследствие сил трения ослабляет усилие затяжки сальника, то по мере увеличения глубины сальниковой камеры и количества устанавливаемых колец, усилие сжатия последних колец будет снижаться. Снижение усилия обжатия приводит к тому, что слои набивки, контактирующие с рабочей средой, оказываются недостаточно уплотненными, поэтому среда может проникать как через поры самой набивки, так и между штоком и набивкой, приводя к разгерметизации сальника.
Рис. 1. Качественная характеристика распределение радиального давления по глубине сальникового уплотнения.
Ро - осевое давление на сальниковую набивку со стороны нажимной втулки;
Рр - давление рабочей среды;
Рв - давление, оказываемое набивкой на вал.
Качественное изменение радиального усилия на вал по длине сальника, от суммарного действия рабочей среды и воздействия нажимной втулки представлено на рис. 1. Как видно из рисунка, наибольшую нагрузку несут первые кольца, которые в эксплуатации имеют износ составляющий 70% износа всего сальникового уплотнения, в тоже время последние кольца почти не изнашиваются и оказываются по существу лишними. Следует добавить, что крутизна представленной характеристики существенным образом зависит от характеристик материала (от величины коэффициента бокового давления), чем меньше Кб, тем круче будет данная кривая.
Наряду с коэффициентом бокового давления, существенное влияние на величину прижима уплотняемой набивки к гильзе вала оказывает конструкция сальниковой камеры.
Рис. 2. Конструкция сальниковой камеры с промежуточным фонарным кольцом для традиционных набивок.
1. вал насоса;
2. подсальниковое бронзовое кольцо;
3. стенка сальниковой камеры;
4. нажимная втулка;
5. фонарное кольцо.
Большинство существующих конструкций сальниковых камер центробежных насосов выполнено со скосами на торцевой стороне сальниковой камеры и на нажимной втулке, рис. 2. Под действием такого скоса крайние уплотняющие элементы испытывают дополнительное усилие (Ррад), прижимающее их к гильзе вала, рис.3. В результате чего увеличивается радиальное воздействие крайних (первого и последнего) уплотнительных элементов на защитную гильзу вала и их износ возрастает в еще большей степени, причем происходит не только износ уплотняющего материала, но и защитной втулки вала. Практика эксплуатации показала наличие характерных зон износа гильзы вала в районе расположении этих колец. В результате, уже через 0,5-1 год, в зависимости от условий эксплуатации, возникает необходимость ремонта или замены защитной гильзы.
Рис.3. Схема перераспределения передачи осевого усилия от нажимной втулки со скосом.
1.-стенка сальниковой камеры; 2.-нажимная втулка; З.-вал насоса;
Ро - осевое усилие, действующее на нажимную втулку;
Ра - осевое усилие, передаваемое нажимной втулкой на уплотнительное кольцо;
Ррад - радиальная составляющая осевого усилия.
Кроме этого, возникающие чрезмерные радиальные давления могут привести к увеличению трения, местному нагреву вала и даже вскипанию рабочей жидкости и, как следствие, аварийному разрушению сальниковой набивки.
В мировой практике все более широкое применение находят уплотнители на основе терморасширенного графита (ТРГ), экспандированного политетрафторэтилена (ПТФЭ) и их композиты, с применением армирующих высокопрочных волокон. Одним из основных производителей данной продукции в России уже более 12-и лет является НПО УНИХИМТЕК, выпускающее весь номенклатурный ряд уплотнителей под торговой маркой ГРАФЛЕКС.
Основные преимущества новых уплотнительных изделий перед паронитом, асбо-графитовыми кольцами, асбестовыми и хлопчатобумажными набивками определяются тем, что они применимы в широком
(практически неограниченном) диапазоне температур и давлений, имеют хорошие показатели сжимаемости (20-60%) под нагрузкой и восстанавливаемости (10-70%) после ее снятия, упругости (8-12%), не теряют этих свойств со временем - не релаксируют и "не стареют", химически инертны и применимы практически в любых средах, обеспечивают герметизацию уплотняемого узла в течение длительного времени без систематических подтяжек, имеют низкий коэффициент трения 0,02 - 0,12% и высокую теплопроводность.
Наличие перечисленных выше свойств позволяет применять эти материалы для уплотнения подвижных соединений при высоких скоростях скольжения (до V= 25м/с) в широком диапазоне температур и давлений.
В настоящее время для уплотнения насосов ЗАО "Унихимтек" производит уплотнительные элементы в виде колец (КГН-кольца низкоплотные из материала ГРАФЛЕКС) и плетеные набивки (НГФ-набивки плетеные из материала ГРАФЛЕКС). Причем уплотнительные сальниковые кольца изготовляются нескольких типов, витые (КГН-В) и слоеные, различного типа (КГН-СО, КГН-СОП).
Витые кольца изготавливаются путем спиральной намотки графитовой ленты с последующим холодным прессованием в пресс-форме до определенной плотности. В результате такого прессования слои фольги деформируются в виде гофра в осевом направлении и прочно соединяются между собой, обеспечивая герметичность. Плотность прессования колец определяется параметрами и условиями последующей эксплуатации и находится обычно в пределах ρ=0,9-Н,35 г/см³. Эти кольца имеют высокий коэффициент бокового давления (Кб=0,7-0,85), поэтому используются для обеспечения герметизации при малых значениях осевого давления.
Слоеные кольца состоят из чередующихся, горизонтальных слоев графитовой фольги, вырубленных из листа (перпендикулярно оси кольца). Кольцо КГН-СО изготавливается послойной укладкой и склейкой слоев между собой. Кольцо КГН-СОП изготовляется из графитовой фольги с поочередной укладкой каждого слоя и последующей холодной подпрессовкой. Эти кольца обладают высокой теплопроводностью в радиальном направлении λ > 120 Вт/(м К) и низким коэффициентом бокового давления (Кб=0,1-0,15), поэтому используются для отвода теплоты и в качестве дросселирующих. Благодаря малому значению Кб, между валом и кольцом при обжатии сохраняется очень малая щель, где происходит дросселирование потока среды, что обеспечивает более благоприятные условия работы остальных колец.
Плетеные уплотнительные набивки изготавливаются в виде шнура, в основном, квадратного сечения, сквозного, многорядного, диагонального плетения. Нить для плетения получают путем скручивания ленты из графитовой фольги. Для придания прочности плетеной набивке на стадии изготовления фольги производят ее армирование нитями из различного материала (хлопчато-бумажной нитью, стекловолокном, металлической проволокой и другими упрочняющими материалами). Для расширения свойств уплотнительного материала применяются плетеные набивки в комбинации с другими материалами, в частности, с экспандированным фторопластом, высокопрочным волокном - "Кевлар" (СВМ). Для повышения уплотнительных свойств плетеных набивок, а также уменьшения их коэффициента трения и коррозионной активности, применяют пропитку специальными составами и смазками.
Коэффициент бокового давления для плетеной набивки НГФ (Кб=0,5-0,6), в то же время эта набивка имеет достаточно высокий коэффициент теплопроводности, сопоставимый с теплопроводностью металла корпуса насоса.
Разнообразие технологии изготовления уплотнительных изделий из материала ГРАФЛЕКС, позволяет набирать комплекты набивок с заданными потребительскими свойствами.
Рис. 4. Схема сальникового уплотнения вала действующих насосов с комплектацией из уплотняющих элементов ГРАФЛЕКС.
Конструкция узла сальникового уплотнения вала насоса ранее спроектированного заводами-изготовителями для традиционных уплотнительных материалов (набивки из асбестосодержащих, хлопчатобумажных и синтетических материалов с различными видами пропитки) приведена на рис.4а. Глубина сальниковой камеры, как правило, устанавливалась для большого количества колец (6-12 штук), что предопределяет создание большого осевого усилия при обжатии сальника, приводит к росту неравномерности давления на вал в радиальном направлении и быстрому износу крайних уплотняющих элементов. На торцевых поверхностях грундбуксы, подсальникового и промежуточного фонарного кольца выполнены скосы под углом α=15° к торцевой поверхности для улучшения деформации набивки от наружного диаметра к валу.
НПО УНИХИМТЕК, на основании испытаний и опыта эксплуатации таких сальниковых узлов рекомендует применение в качестве уплотнителя плетеную набивку типа НГФ, обеспечивающую длительную и надежную эксплуатацию при минимальных протечках, и увеличении срока службы уплотнения в 2-4 и более раз, в зависимости от условий эксплуатации. При этом конструкция сальникового узла не меняется. В ряде случаев, при наличии в среде абразивных частиц, целесообразно крайние кольца устанавливать из набивки с более прочными нитями, например, из кевлара (СВМ).
Если применение набивок НГФ не обеспечивает желаемых результатов по ресурсу работы, величине протечки рабочей среды или давление среды достаточно высокое Рраб > 2МПа, то это в первую очередь является следствием недостатков конструкции узла сальникового уплотнения вала, компенсировать которые можно путем применения специальных колец из ТРГ ГРАФЛЕКС. Схема комплектации таких узлов приведена на рис.46. Такая комплектация обеспечивает работу уплотнения практически без протечек (величина протечки составляет 1-5 капель в минуту).
Рис. 4б. Схема сальникового уплотнения вала действующих насосов с комплектацией из уплотняющих элементов ГРАФЛЕКС.
Теплоотводящие кольца обеспечивают эффективный отвод тепла как за счет высокой теплопроводности (в сравнении с набивками НГФ и кольцами КГН типа В), так и за счет высокой эффективности дросселирования рабочего давления и выравнивания радиального давления на вал по длине сальника, что приводит к равномерному и более медленному износу сальника.
Для дросселирования большого давления рабочей среды (2 ÷ 4 МПа), а также для рабочих сред со значительным количеством механических примесей, может быть установлено подряд несколько дросселирующих колец со стороны рабочей среды. На рис.4в приведена одна из возможных схем комплектации сальникового узла при наличии фонарного кольца.
Рис. 4в. Схема сальникового уплотнения вала действующих насосов с комплектацией из уплотняющих элементов ГРАФЛЕКС.
Для узла сальникового уплотнения вала насоса, конструкция которого будет разрабатываться для целевого применения комплектов уплотнений из ТРГ ГРАФЛЕКС, мы рекомендуем изменения, представленные на рис.5. Торцевые поверхности нажимной втулки и промежуточного фонарного кольца выполняются перпендикулярно оси вала, без скосов, что позволяет обеспечивать более равномерное распределение радиального давления на вал по длине сальника. Взамен металлических (стальных, бронзовых) подсалышковых колец, устанавливаемых для дросселирования среды с минимальными зазорами по валу δ= 0,2 ÷ 0,3 мм, возможна установка специального дросселирующею кольца из ТРГ "Грфлекс" типа КГН-С. За счет упругости материала, низкого коэффициента трения, высокой теплопроводности и износостойкости дросселирующие кольца долго сохраняют минимальные зазоры, что предопределяет чрезвычайно высокую эффективность дросселирования давления.
Рис.5. Схема конструкции сальникового узла для использования уплотнителей типа ГРАФЛЕКС.
Результаты проведенных исследований показали, что для обеспечения надежной герметизации с использованием уплотнительных материалов ГРАФЛЕКС при давлении рабочей среды до Рр ≤ 1 МПа требуется комплект, состоящий из 3-5 уплотняющих колец, а при давлении рабочей среды выше Рр < 1МПа, целесообразно устанавливать комплект, состоящий из 6 колец.
Кроме этого, благодаря так называемому эффекту "самолечения", заключающемуся в том, что при контакте с уплотнительными изделиями из ТРГ, уплотняемая поверхность покрывается тонким слоем графита, в результате чего происходит заполнение микронеровностей, поверхность становится более гладкой и дальнейший контакт набивки происходит с прографиченной поверхностью, в результате чего коэффициент трения снижается до k=0,02-0,05 (сухое трение ТРГ по стали k=0,l-0,12). Все это способствует уменьшению износа набивки, в результате чего обеспечивается надежная герметичность и долговечность работы уплотнения при меньшем числе уплотняющих элементов.
В свою очередь, сокращение числа уплотняющих элементов позволяет уменьшить габаритные размеры насосов, снизить металлоемкость изделия, сократить затраты на уплотняющие материалы.
Еще больший эффект достигается в процессе эксплуатации у потребителей. Ниже приводятся результаты оценки эффективности применения материалов ГРАФЛЕКС по сравнению с традиционными набивками .
Изменение затрат на материалы за год, в случае замены традиционных уплотнений на основе асбеста на ГРАФЛЕКС можно оценить по выражению:
Где: С асб, С гр - цена асбестового уплотнения и уплотнения ГРАФЛЕКС соответственно, руб/кг;
G асб, G гр - расход материала на сальниковое уплотнение из асбеста и ГРАФЛЕКС соответственно, кг;
η асб, η гр - срок службы уплотнений из асбеста и из материала ГРАФЛЕКС, соответственно, недель;
η год - число недель в году.
В качестве примера, рассмотрим изменение затрат на материалы для центробежного насоса, используемого для перекачки битума на Сызранском НПЗ с учетом реальных сроков службы уплотнений.
ΔS=(0.4·150/2.5-0.4·1350/26)·52=168 руб/год
Таким образом, несмотря на значительно более высокую цену уплотнений ГРАФЛЕКС (С гр = 1350 руб/кг, а С асб = 150 руб/кг), в итоге экономия затрат на материал за год составляет 168 рублей на один насос. Но этим эффективность нового поколения не исчерпывается.
Высокая теплопроводность ГРАФЛЕКС и низкий коэффициент трения позволяют обеспечить работу сальниковых узлов центробежных насосов без протечек перекачиваемой среды через уплотнения (в отдельных случаях предусматривается протечка в пределах 1-5 капель в минуту). Применение обычных набивок требует обеспечения протечки небольшого количества перекачиваемой среды (5-20 капель в минуту (реально еще больше, если среда не является ядовитой)) для предотвращения разогрева сальникового узла, что соответствует утечкам среды около 0,5-1,0 л/час (реально протечки могут достигать 3 л/ч). За год (7000-8000 часов) такие утечки составляют от 4 до 8 тонн продукта. Экономический эффект при этом можно оценить по выражению:
где G пот - утечки перекачиваемой жидкости, т/год;
С пр - цена 1тоны перекачиваемой жидкости, руб/т.
С учетом цены нефти - 3 000 руб/т, эффект от сокращения потерь в этом случае составит от 1.2 000 руб/год до 24 000 руб/год, что практически в 100 раз превосходит затраты на материалы.
Снижение коэффициента трения при использовании уплотнений ГРАФЛЕКС более чем в три раза позволяет получить снижение затрат энергии на привод насоса. Эти затраты также в несколько раз перекрывают расходы на приобретение уплотнительного материала ГРАФЛЕКС. Для современных центробежных насосов механический КПД, который учитывает потери энергии от трения в уплотнениях, подшипниках и дискового трения η м =0,92-0,99. Затраты энергии, идущей на преодоление сил механического трения в сальнике, для традиционных набивок составляют около α с =50% от суммарных механических потерь.
Для этого случая величину снижения потребляемой мощности рассмотрим на следующем примере: для насоса, с мощностью привода N Э =100 кВт замена традиционного сальникового уплотнения на уплотнение из материала ГРАФЛЕКС позволяет на 2/3 сократить потери энергии в сальниковом узле. Если предположить, что исходный механический КПД насоса равен η м =0,95, то в результате получим следующую величину экономии мощности:
ΔN Э =2/3·α c ·N Э =0.667·0.5·0.05·100=1,6675кВт
Казалось бы, ничтожная величина. Однако, при продолжительности эксплуатации насоса τ=7000 часов в год, можно получить экономию электроэнергии:
Э г = 1,6675- 7000 = 11672,5кВт.
При цене электроэнергии 50 копеек, экономия составит S эк.э =5836 рублей. Для сравнения комплект сальниковой набивки на такой насос в среднем стоит около 500 рублей.
Еще больший эффект получается от увеличения срока службы защитной гильзы вала. Опыт эксплуатации показал, что при применении традиционных набивок после одного года эксплуатации необходима либо проточка или, чаще всего, замена защитной втулки. Применение набивок из материала ГРАФЛЕКС позволяет сохранять работоспособность втулки в течение 3-4 лет эксплуатации. Таким образом, экономия от увеличения ресурса защитной гильзы в три раза составит:
С з.в. - цена защитной втулки для данного насоса, руб.;
S p.p. - стоимость ремонтных работ по замене защитной втулки, руб.
Суммарный экономический эффект составит:
Окупаемость уплотнительных материалов ГРАФЛЕКС, как показал опыт эксплуатации, не превышает двух-трех месяцев.
НПО УНИХИМТЕК на базе экспериментальных исследований и опытно-промышленной эксплуатации разработаны и внедрены комплекты уплотнений из материалов ГРАФЛЕКС для действующих насосов, обеспечивающих снижение протечек среды и увеличение срока службы. По результатам теоретических и экспериментальных исследований разработаны рекомендации для внесения изменений в конструкцию сальниковой камеры насоса при использовании уплотнительных материалов ГРАФЛЕКС, обеспечивающих снижение протечек среды, уменьшение износа гильзы вала, расхода уплотняющего материала и снижения затрат на эксплуатацию.
ЛИТЕРАТУРА
- Домашнее А.Д., Хмелъникер В.Л. Сальниковые уплотнения арматуры АЭС. - М.: Атомшдат, 1980, 112с.
- Кришнек Р. Уплотнительные системы на основе графита. Химическое и нефтегазовое машиностроение, № 8, 2000.
- Ворохов A.M., Гашнин А.С., Додо-нов Н.Т. Волокнистые и комбинированные сальниковые уплотнения. М.: Машиностроение, 1966, 312 с.
- Ильин Е.Т. Российские высокоэффективные уплотнения ГРАФЛЕКС - Материалы отраслевого совещания главных механиков нефтеперерабатывающих и нефтехимических предприятий России и СНГ. г. Кириши, 2002, С. 2 59-266.
Аппараты для перемешивания жидких сред
1. Бакланов Н.А. Перемешивание жидкостей. Л.-.Химия, 1979. 63с.
2. Богданов В. В. .Христофоров Е.И..Кдоцунг Б. А. Эффективные масообменные смесители. Л.-.Химия, 1989. 224с.
3. Брагинский Л.Н. .Вегачев В.И. .Варабаш В.М. Перемешивание в жидких средах; Физ. основы и инж. методы расчета. Л. Химия, 1984. 336с.
4. Васильцов 3.А. .Ушаков В.Г. Аппараты для перемешивания жидких сред: Справ, пособие. Л.-.Машиностроение, 1989. 271с.
5. Канторович 3. В. Машины химической промьапленности. М.-.Машиностроение, 1965. 415с.
6. Касаткин А. Г. Основные процессы и аппараты химической технологии. М.-. Химия, 1973. 750с.
7. Криворот А. С. Конструкция и основы проектирования машин и аппаратов химической промышленности. Ц.: Машиностроение, 1976. 376с.
8. Леонтьева А. И. Машины и аппараты химической промышленности. Учеб. пособие. Тамбов: ТГТУ, 1991. 4.1. 104с.
9. Машины и аппараты химических производств./Под ред. И. И. Чернобыльского. М.:машиностроение, 1975. 456с.
10. Холланд Ф.А., Чапман Ф.С. Химические реакторы и смесители для жидкофазных процессов: Пер. с англ. М.: Химия, 1974. 208с.
Для создания герметичности между неподвижным корпусом аппарата и вращающимся валом служит уплотнение. В зависимости от физико-химических характеристик и параметров рабочих сред, а также требований производственной санитарии, техники безопасности и пожароопасности аппараты для перемешивания жидких сред комплектуются сальниковыми или торцевыми уплотнениями, гидрозатворами или имеют герметичный привод.
Сальниковое уплотнение состоит из корпуса, грундбуксы, нажимной втулки, сальниковой и стягивающих шпилек (рисунок 27). Уплотнение достигается прижатием сальниковой набивки к вращающемуся валу. Между валом о грундбуксой остается зазор 0,5 - 0,75 мм, а между валом и нажимной втулкой – несколько – больший зазор (1 - 1,5 мм). Эти зазоры устраняют возможность износа вала в указанных местах. Для изготовления грундбуксы и нажимной втулки используется чугун. При отсутствии зазора между валом и грундбуксой последняя должна изготовляться из бронзы.
1 - корпус; 2- нажимная втулка; 3- набивка; 4 - упорное кольцо (грундбукса).
Рисунок 27 - Сальник.
В некоторых случаях сальниковое устройство одновременно является опорой для вала (подшипником скольжения). Тогда зазор между валом и нажимной втулкой делается минимальным, т.е. на посадке скольжения. Нажимная втулка снабжается устройством для подачи и распределения смазки и изготовляется из бронзы или снабжается бронзовым вкладышем.
Cальник (рисунок 28) в середине слоя сальниковой набивки имеет сальниковое кольцо, которое обеспечивает равномерный подвод смазки по всему периметру вала в середину набивки. Для отвода тепла сальник снабжается охлаждающей рубашкой.
1 - корпус; 2- рубашка; 3- нажимная втулка; 4- набивка; 5- смазочное кольцо; 6- упорное кольцо (грундбукса).
Рисунок 28 - сальник со смазывающим кольцом.
В качестве сальниковых набивок чаще всего применяются хлопчатобумажные, пеньковые и асбестовые материалы.
Ниже приведены предельные температуры, при которых могут использоваться набивки.
Таблица 1.2 - Предельные температуры для сальниковых набивок.
Перечисленные набивки могут применяться при давлениях 0,6-4 Мпа в зависимости от температуры и используемого пропитывающего состава. Пропитка служит для улучшения герметизации и снижения коэффициента трения набивки о вал. Для пропитки набивок применяют сало, парафин, битум, графит, жидкое стекло, тавот, вискозин и т.п.
Из указанных выше набивок следует отметить фторопласт. Он имеет малый коэффициент трения, поэтому срок его службы в несколько десятков раз больше, чем у остальных материалов. Этому способствует также его высокая химическая стойкость. Недостатки фторопласта – сравнительно высокая твердость (что требует больших усилий при затяжке сальника) и высокая стоимость. Эти недостатки устраняются в набивке из асбестового шнура, пропитанного фторопластовой суспензией.
При высоких температурах (t > 300° С) используются сухие набивки. Наиболее распространенная сухая набивка марки АГ-50 состоит из 50% графита, 45% длинноволокнистого асбеста и 5% алюминиевой пудры. Утечка уплотняемой среды в сухих набивках происходит вследствие их пористости. Даже при высоких давлениях прессования набивки (30 - 60 МПа) она остается пористой, так как составляющие её компоненты – асбест и графит – являются пористыми телами.
Сальниковые уплотнения применяют в аппаратах, работающих при давлениях до 0,1 МПа и температуре до 70°. Их нельзя применять при вакууме, переработке в аппаратах ядовитых и взрывоопасных сред. Скорость вала – от 5 до 320 об/мин.
Для нормальной работы сальника необходимо, чтобы усилие прижатия нижних слоев к валу равнялось давлению среды. Усилие прижатия набивки к валу действует в радиальном направлении, тогда как поджим набивки нажимной втулкой производится в осевом направлении. Схема работы сальника изображена на рисунке 29. Если бы набивной служила идеальная жидкость, то осевое и радиальное усилие были бы равны (Р х = Р у) во всех её участках. Однако, поскольку набивка является деформируемым твердым телом, то Р х <= Р у и, кроме того, сила прижатия набивки к валу будет изменяться по высоте сальниковой камеры вследствие трения набивки о вал и корпус при её деформации, т.е. при сжатии.
1 - вал; 2 - нажимная втулка; 3- корпус.
Рисунок 29 - Схема распределения усилий в сальнике.
Связь осевого и радиального усилий можно выразить зависимостью:
Величина m зависит от материала набивки, давления и лругих факторов и изменяется в пределах от 1,5 до 5.
Закон изменения осевой силы по высоте сальника можно представить следующим образом:
, (1.40)
Где S=(D-d)/2 ; f=m ТР /m ; m ТР – коэффициент трения набивки о вал и корпус сальника.
В нижней части при у=0 справедливо равенство Р у =Р 0 , а верхней при y=h – равенство Р у =Р 0 ехр(2 f h/S). Величина осевого усилия в верхней части позволяет по площади сечения набивки определить усилие затяга и рассчитать стяжные шпильки.
При совместном решении уравнений (1.39) и (1.40) получим закон изменения радиальной силы по высоте набивки, т.е. силы прижатия набивки к валу:
, (1.41)
Эпюра изменения силы прижатия набивки к валу изображена на рисунке 29. При удалении от нажимной втулки эта сила уменьшается. При большой высоте сальниковой набивки уменьшение радиальной силы будет значительным. Эффективное перераспределение радиальной силы может быть достигнуто в конструкции двойного сальника, однако, двойной сальник применения не находит, так как его эксплуатация очень сложна.
Если бы набивка являлась абсолютно твердым телом, то в противоположность допущению об идеальной жидкости, прижатие набивки к валу должно полностью отсутствовать. Для деформируемого твердого тела усилие прижатия набивки к валу будет составлять некоторую часть от осевого усилия. Увеличение силы прижатия можно достигнуть конструктивным приемом – изготовление колец уплотнительной набивки с конусными поверхностями. Для реальных набивок этот прием широко используется.
Определим мощность, теряемую на трение в сальнике. Для элемента набивки высотой dy сила трения равна:
После подстановки значения Р х из уравнения (1.41) и интегрирования в пределах от 0 до h получаем:
, (1.43)
С учетом f=m тр /m имеем:
, (1.44)
Мощность теряемая на трение, будет равна:
, (1.46)
Коэффициент трения f при вращении вала имеет меньшее значение, чем при неподвижном вале, кроме того, он изменяется при изменении давления. Учесть все это для разнообразных набивок при использовании уравнения (1.45) сложно, поэтому переходят к эмпирической зависимости (1.46), которая для практических расчетов принимает вид:
Таблица 1.3 - Влияние геометрических размеров сальниковой набивки на потери мощности.
Ширина сальниковой набивки S ,мм определяется по диаметру вала:
, (1.48)
Торцевое уплотнение. В этом уплотнении герметичность достигается за счет плотного поджатия по торцевым плоскостям двух деталей – вращающейся и неподвижной. Герметичность в таком соединении может быть достигнута только при высоком качестве обработке прилегающих поверхностей. Неровности 1мкм нарушают нормальную работу торцевого уплотнения. Поверхности трения подвергаются шлифовке и притирке, и имеют высокую чистоту обработки (№ 10 - № 12), они могут быть плоскими, сферическими или конусными. Плоские поверхности применяются чаще, т.к. при доводке легче получить хорошую чистоту поверхности трения, ширина кольцевой поверхности трения не должна быть большой (меньше 6 - 8 мм).
В химической промышленности торцевые уплотнения применяются не только для реакторов, но и для центробежных насосов. Торцевое уплотнение для герметизации аппаратов представлено на рисунке 30. Кольцо 2 получает вращение от вала через водило 4, состоящее из двух половинок, стягивающих вал, и через шпильки 3. Неподвижное кольцо 7 соединено с сильфоном. Тяги 6 с пружиной дают возможность регулировать силу поджатия колец 2 и 7, сильфон 8 позволяет компенсировать биение вала.
1 - корпус; 2 - вращающееся кольцо; 3 - шпилька; 4 - водило; 5 - пружина; 6 - тяга; 7 - неподвижное кольцо; 8 - сильфон.
Рисунок 30 - Торцевое уплотнение.
уплотнение (рисунок 30) работает при давлении 2* 10 3 - 1,6* 10 6 Па, температуре до 250 ° С и частоте вращения до 10 с -1 .
Достоинства – меньшие утечки, чем в сальнике, так как при работе под вакуумом подсос воздуха отсутствует, потери мощности составляют десятые доли потерь мощности на трение в сальнике, не требуется обслуживания, что объясняется большой износостойкостью пары трения (а следовательно, долговечностью) и хорошей работой при биениях вала.
Недостатки – высокая стоимость и сложность ремонта.
Основным узлом торцевого уплотнения является пара трения. Материал, из которого она изготовлена, должен обладать износостойкостью и малым коэффициентом трения. Используются следующие материалы: кислостойкая сталь – одно кольцо; углеграфит, бронза или фторопласт – другое кольцо. Фторопласт применяется только в случае небольших давлений и при невысоких скоростях пары трения, так как он обладает хладотекучестью. По конструкции торцевое уплотнение может быть внутренним и внешним, одинарным и двойным. Уплотнение, изображенное на рисунке 30, является внешним.
У внутреннего уплотнения вращающееся кольцо и нажимные пружины расположены внутри аппарата в рабочей среде. Двойное уплотнение имеет две пары трения и практически представляет собой два последовательных одинарных уплотнения. В двойном уплотнении между двумя парами трения помещается запирающая среда, предотвращающая утечки и отводящая тепло трения.
В химической промышленности наиболее распространенными являются следующие типы торцевых уплотнений: а) двойное торцевое уплотнение типа ТД (левая часть рисунок 31), предназначенное для герметизации валов аппаратов для перемешивания взрывоопасных, токсичных, пожароопасных, ядовитых и подобных им сред при давлениях до 0,6 МПа (тип ТД-6) и при давлениях до 3,2 МПа (тип ТД-32); б) двойное торцевое уплотнение ТДП (правая часть рисунок 31) с встроенным подшипником, предназначенное для герметизации валов аппаратов для перемешивания взрывоопасных, токсичных, ядовитых и подобных им сред; в) торцевое уплотнение типа ТСК, в котором использован сильфон из стали 12Х18Н10Т (рисунок 32), предназначенное для герметизации валов аппаратов для перемешивания взрывоопасных, токсичных и ядовитых сред, находящихся под давлением.
1 - неподвижные уплотнительные кольца; 2 - подвижные уплотнительные кольца; 3 - пружина; 4 - корпус; 5 - встроенный опорный подшипник.
Рисунок 31 - Двойное торцевое уплотнение типа ТД (левая часть рисунка) и типа ТДП (правая часть рисунка).
Данные торцевые уплотнения применяют в аппаратах, работающих при избыточном давлении до 1,6 МПа или остаточном давлении не менее 0,0027 МПа и температуре от -20 до +50 ° С.
Конструкция торцевого уплотнения (рисунок 32.), состоящая из под- вижного кольца 5, закрепленного на валу с помощью водила 2, и неподвижного кольца 6, плотно прижимаемого торцевой поверхностью к неподвижному кольцу пружинами 4 и гайками 3. Неподвижное кольцо 6 соединено болтами 10 с узлом сильфона 7. Корпус 8 закрыт сверху крышкой 1 и прикреплен фланцами и болтами 9 к крышке аппарата.
1 - крышка; 2 - пружина; 3 - подвижное кольцо; 4 - неподвижное кольцо; 5 - сильфон; 6 - корпус; 7 - болт.
Рисунок 32 - Торцевое уплотнение типа ТСК.
Сильфон представляет собой тонкостенную трубку с гофрированной поверхностью.
Смазку трущихся колец и охлаждение производят проточной водой, циркулирующей в полости крышки. Вода, попавшая через уплотнительную поверхность, собирается в нижней части корпуса, называемой уловителем, и выводится через штуцер. Неподвижные и подвижные кольца (пары трения) изготовляют из углеграфита, сталей 12Х18Н10Т, 40Х13, 95Х18, сплавов хостеллой Д или ситаллов.
Рассмотрим работу торцевого уплотнения (рисунок 33).
Рисунок 33 - Движение среды в зазоре между кольцами торцевого уплотнения
Движение среды в зазоре между кольцами в цилиндрических координатах описывается уравнением:
Так как уплотнение имеет осевую симметрию, то и , а поскольку в зазоре давление изменяется только в радиальном направлении, то .
После упрощения уравнение (1.49) примет вид:
, (1.50)
Поскольку ширина поверхности соприкосновения колец в торцевом уплотнении невелика, то можно принять:
Теперь уравнение движения среды запишется следующим образом:
, (1.52)
Исходя из схемы движения среды в зазоре между кольцами, изображенной на рисунке 33, граничные условия для уравнения (1.52):
Интегрирование уравнения (1.52) дает:
, (1.54)
Используя граничные условия (1.53), получаем по уравнению (1.54):
, (1.55)
, (1.56)
из которых находим
; , (1.57)
С учетом постоянных с 1 и с 2 решение примет вид:
, (1.58)
Величина утечки на единице длины уплотнения составит:
, (1.59)
На всем периметре уплотнения величина утечки будет равна:
Преобразуем уравнение (1.60):
, (1.61)
Граничные условия для уравнения (1.61) с использованием схемы движения среды в зазоре пары трения рисунок 33:
После интегрирования получаем:
Отсюда найдем величину утечек среды в торцевом уплотнении:
, (1.64)
Таким образом, на величину утечки наиболее сильное влияние оказывает величина зазора между кольцами торцевого уплотнения. В уравнениях (1.60) и (1.64) эта величина входит в третьей степени, поэтому для нормальной работы уплотнения зазор между кольцами должен быть доведен до минимума. Этого удается достичь шлифовкой и притиркой колец. Величина зазора составляет от долей микрона до нескольких микрон.
В торцевом уплотнении одно из колец вращается, поэтому кроме сил давления и трения на величину утечек оказывает влияние сила инерции. Если угловую скорость вращения среды в зазоре определять как среднюю арифметическую угловых скоростей вращения колец, то уравнение (1.61) с учетом силы инерции примет вид:
, (1.65)
После интегрирования и преобразования величины утечек определятся выражением:
, (1.66)
Таким образом, повышение частоты вращения вала увеличивает утечки при работе аппарата под давлением и уменьшает утечки при работе аппарата под вакуумом.
Гидрозатворы представляют собой уплотнительный узел, предназначенный для предотвращения контакта газовой среды, заполняющей внутреннюю полость аппарата, с атмосферой (рисунок 34). Гидрозатвор состоит из неподвижного цилиндрического корпуса, внутрь которого с зазором d относительно его неподвижных элементов вставлен вращающийся совместно с валом мешалки цилиндрический колпак. При атмосферном давлении в корпусе аппарата и правильно выбранных размерах гидрозатвор надежно предохраняет уплотняемые плотности от взаимного контакта.
1 - корпус; 2 - вращающийся колпак; 3 - кольцо уплотнительное; 4 - неподвижный стакан; 5 - корпус.
Рисунок 34 - Гидрозатвор для аппаратов общего назначения (левая часть рисунка) и для малогабаритных аппаратов (правая часть рисунка).
Манжетные уплотнения применяют в аппаратах, работающих при атмосферном давлении и температуре до 120 0 С. Конструктивно уплотнение представляет собой диск, укрепляемый на болтах над отверстием крышки, в кольцевой проточке диска установлена стандартная манжета, герметизирующая зазор между валом и внутренней поверхностью отверстия диска.
Герметичные электроприводы . Аппараты для перемешивания высокотоксичных, высоко агрессивных или пожароопасных сред обычно комплектуют герметичными электроприводами. Приводы этого типа представляют собой конструкцию, в которой активные элементы ротора и статора электродвигателя защищены от воздействия перемешиваемой среды с помощью специальной изоляции (мокрый статор) или специальных защитных гильз (сухой статор) . Герметичные электроприводы с "мокрым" или "сухим" статором могут быть газозаполненными и жидкостнозаполненными.
В газозазаполненном электроприводе (рисунок 35) ротор, вращающийся в газовой полости, установлен на подшипниках качения. Статорная полость электродвигателя защищена от контакта с парами перемешиваемой среды тонкостенной защитной гильзой 5. В случае необходимости защитная гильза может быть также установлена на роторе 11. В электроприводах по подобного типа подшипники качения обычно смазывают консистентной или обычной смазкой, подаваемой через штуцер 9. Герметичный электропривод на подшипниках качения выполняется обычно газозаполненным. В качестве газа, создающего этот своеобразный буфер, препятствующий контакту перемешивающей среды с подшипниками качения, используется один из компонентов реакционной среды или какой-либо инертный газ.
Жидкостнозаполненный герметичный электропривод (рисунок 36) представляет собой конструкцию, в которой используются гидростатические или гидродинамические опоры скольжения, смазываемые перемешивающей средой, не содержащей твердых взвесей. Между рабочим пространством аппарата и внутренней полостью жидкостнозаполненного электропривода обычно устанавливают торцевое уплотнение, уменьшающее обмен между средами, заполняющими эти полости.
1 - мешалка; 2 - циркуляционная труба; 3 - вал; 4 , 8 - подшипники качения; 5 - защитная гильза; 6 - обмотка статора; 7 - железо статора; 9 - штуцер подвода жидкой смазки; 10 - штуцер подвода инертного газа; 11 - железо ротора.
Рисунок 35 - Аппарат с герметичным приводом перемешивающего устройства.
1 - упорная пята; 2 - центробежный насос, обеспечивающий циркуляцию жидкости в приводе; 3, 8 - опорные подшипники жидкостного трения; 4 - защитная гильза ротора; 5 - защитная гильза статора; 6 - железо статора; 7 - железо ротора; 9 - вал; 10 - мешалка;11 - торцевое уплотнение.
Рисунок 36 - Жидкостнозаполненный герметичный электропривод на подшипниках жидкостного трения.
Вопросы для повторения
1. Уплотнения валов и штоков.
2. Сальник, устройство и принцип действия.
3. Набивки сальника и их выбор.
4. Расчет сальника.
5. Торцевое уплотнение, устройство и принцип действия.
6. Расчет торцевого уплотнения.
7. Гидрозатвор, устройство и принцип действия.
8. Герметичный привод.
В чем заключается набивка сальников?
Сама по себе набивка сальников представляет собой изделия, предназначенные для сальниковых камер. С виду это простой эластичный шнур с квадратным/круглым сечением. Сечение сальников производится из асбестовой нити и др. волокон. Сальники обеспечивают герметизацию как динамичных, так и не динамичных соединений механизма. Набивки сальников отлично взаимодействует с агрессивной средой и с разными температурами. На данный момент сальники представлены разными видами. Различают асбестовые/ неасбестовые набивки.
Перед набивкой сальников поставлена важная задача, а именно герметизация узлов и агрегатов в любой промышленности. Она делится на типы и классы. Каждому типу и классу свойственен определенный уровень эксплуатации. К примеру, набивки с содержанием асбеста используется в нефтяной промышленности, поскольку все нефтеперерабатывающие машины и станки взаимодействуют с химическими нефтяными продуктами, газами, смесями. В тех случаях, когда возникает серьезная ситуацию, для осуществления процесса набивки применяется прессовка, выполняемая специалистами.
Если говорить о набивке сальников типа MC 105, то она включает в себя качественные гибкие графитовые волокна, армированных х/б нитью и пропитанные политетрафторэтиленом. Она используется для того, чтобы уплотнять центробежные и плунжерные насосы. Эта набивка используется в составе горячей воды, в нефтяных продуктах, смазочном и термальном масле и разных органических растворителях.
В ней не происходит утечка между волокнами только благодаря тому, что под образовавшимся давлением выделяется специальная масса, которая предотвращает утечку. Кроме того, набивка отличается пониженным коэффициентом трения. Применяемый графит понижает тепловыделение и потребление электроэнергии в насосах. Помимо прочего, она может самостоятельно смазываться. То есть, в случае изнашивания одного слоя, обнажается второй слой с теми же свойствами, тем самым продлевается срок использования. Поскольку набивка сальников характеризуется теплопроводностью, благодаря которой тепло в камерах рассеивается.
Как видно, этот процесс занимает достаточно времени. Процесс набивки необходим для наполнения сальника и уплотнения того места, откуда выпускаются все движущиеся детали механизма. Этот процесс необходим для того, чтобы втулка сальника вплотную прижималась к набивке и опускалась в гнездо, глубиной в 10-15 мм.
Порой, в жилищно-коммунальном хозяйстве возникают проблемы, связанные с централизованной системой отопления, отрегулировав которую сальники начинают пропускать воду. Если говорить о летнем сезоне, то отопление не поступает, так как его отключают для выполнения ремонтных работ. А так, как многие уезжают из города, то попасть к ним в дома просто невозможно и как следствие отремонтировать сальники тоже невозможно. Если же использовать тот аппарат, который проиллюстрирован на рисунке ниже, то эти же ремонтные работы можно выполнять и зимой, при действующей системе отопления.
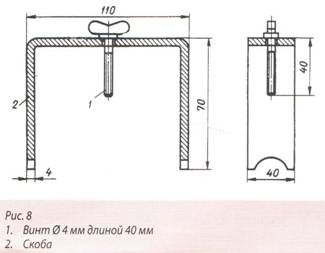
Необходимо создать скобу по образу буквы, толщина пластины которой равно 5 мм, ширина - 40 мм, а длина - 250 мм. В центре просверлите отверстие, концы нужно залить строго по диаметру трубопровода и поставить винт. Так как цилиндр будет прижат к крышке крана, то образуется преграда воды к сальнику. Потом крышку отворачивают и набивают сальником.

Осуществляя набивку центробежных насосов, необходимо использовать хлопчатобумажный шнур, а лучше плетенку, которую сначала нужно промокнуть в теплое цилиндровое масло с небольшим содержанием парафина.
В дополнение ко всему можно воспользоваться плетенкой из чистого длинноволосого льна, который нужно очистить от костры и пропитать составом с содержанием мыла, вазелина, графита.
В уплотнении сальников центробежных насосов применяется про-графический асбест. Для тех предприятий, которые качают нефтяные продукты, применяют иные волокнистые сальниковые набивки с применением медной проволоки.