Zbijanje betonske mešanice. Metode stiskanja betona
Tehnologija postavljanja betonskih konstrukcij vključuje pripravo betonska mešanica in njegovo zbijanje. Obstajajo primeri, ko se pri mešanju raztopine v notranjosti pojavijo votline, ki lahko porušijo strukturo in zmanjšajo njeno gostoto. Zaradi tega se v izdelku pojavijo razpoke, kar lahko na koncu privede do uničenja. betonske konstrukcije. Med postopkom stiskanja strokovnjaki odstranijo zrak iz raztopine, odvečna tekočina, zaradi česar postane bolj gost. Tako je izdelek močnejši in trajnejši.
Zbijanje betona velja za najbolj kritično fazo polaganja. cementne mešanice. Koeficient betona in glavne značilnosti izdelka bodo odvisni od tega, kako natančno bo to dejanje izvedeno. Med postopkom strokovnjaki obdelujejo betonska površina ročno ali z mehanske naprave odstranjevanje votlin. To omogoča enotnost betonska malta, povečati oprijem sestave z drugimi strukturnimi elementi.
Načini
Gradbeniki uporabljajo naslednje vrste naprave za stiskanje mešanice:
- površina (za zgornjo plast cementa);
- globoko (velike betonske konstrukcije);
- zunanji (nameščen pred stiskanjem z roba lesenega opaža ali posode s cementno malto);
- vibracijske platforme (uporabljajo se v specializiranih podjetjih).
Obstajajo različni načini stiskanja cementne malte:
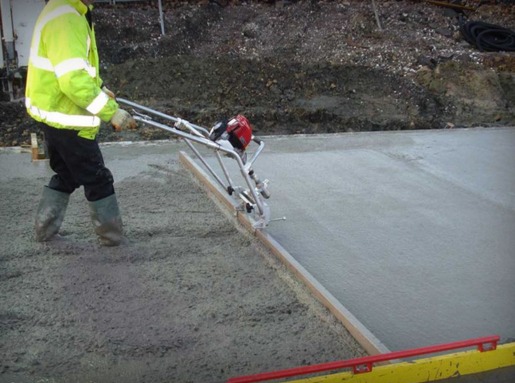
druge metode
Druge metode tesnjenja vključujejo:
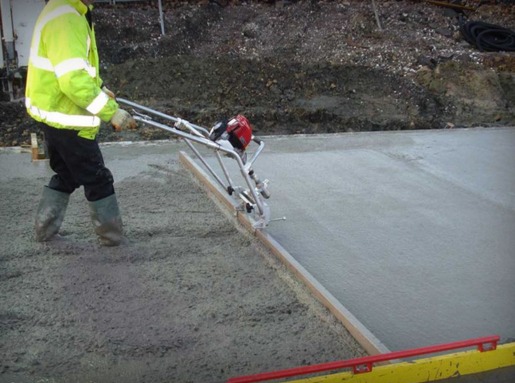
Za cementna sestava je enakomerno zbito, je treba upoštevati naslednja priporočila:
- Pri montaži lesenih opažev je treba posvetiti pozornost varna pritrditev podrobnosti. Na konstrukcijskih elementih ne sme biti nobenih vrzeli (betonska raztopina se lahko iztisne skozi razpoke). Potrebno je, da je opaž poliran in gladek, v drugače pustil bo udrtine na izdelku. Poleg tega se lahko kasneje v telesu konstrukcije tvorijo praznine.
- Detajli lesenih ali vezanih opažev, vključno s klini, morajo biti varno pritrjeni, da se deske ne premikajo.
- Pri vibrokompaktiranju sestave je treba položaj vibracijskega estriha občasno spreminjati, sicer bo raztopina nehomogena, nastale bodo votline.
- Strokovnjaki svetujejo, da ne porabite veliko časa za delo, saj lahko to povzroči razslojevanje, ki se pojavi zaradi dejstva, da se na dnu podrti velik gramoz, na vrhu pa se nabira le cementna malta.
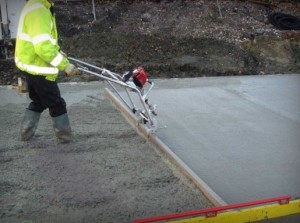
Ker uporaba površinskih vibracijskih naprav ne omogoča vizualnega določanja stopnje gostote, pri izvajanju gradbena dela pogosto uporablja dodatno zdravilo, kar bo pomagalo zagotoviti moč sestave. Da bi to naredili, gradbeniki obstoječi sestavi dodajo raztopino z visoko plastičnostjo. Zaradi tega se poveča tveganje za razslojevanje izdelka. Da bi se izognili takšni pomanjkljivosti, je priporočljivo povečati količino cementa.
Faktor zbijanja
Ocenite kakovost betonska sestava možno z enim pomembno merilo. To je približno o faktorju zbijanja. Koeficient se določi na naslednji način: izračuna se razmerje specifična težnost pripravljena mešanica na vrednost, ki je bila dosežena v odsotnosti zračnih mehurčkov v notranjosti. Torej je sprejemljiva vrednost koeficienta 1. Kazalnik lahko dosežete različne poti zbijanje betona, bo izbira metod neposredno odvisna od sestave, namena in frakcij. Avtomatizirani vibracijski estrihi bistveno povečajo kakovost rešitve.
Od česa je odvisno razmerje?
Ta indikator je določen z granularnostjo sestave, pa tudi z objektom, ki bo betoniran, ne glede na to, ali gre za slepe površine, proge, poti.
ugotovitve
Izkušeni gradbeniki trdijo, da bosta od tega odvisna stabilnost in vzdržljivost konstrukcije. To je treba upoštevati, če želite, da vam izdelek služi več kot eno leto. Pravočasno sprejeti ukrepi bodo pripomogli k nadaljnjemu povečanju zaščite konstrukcije pred poškodbami, prihranili denar pri obnovitvenih delih. Univerzalne vibracijske naprave vam bodo omogočile, da dobite visokokakovosten beton. Pred izvedbo gradbenih del se morate vnaprej posvetovati s strokovnjaki in izbrati potrebno opremo. Ergonomsko oblikovani vibratorji omogočajo gradbincem kompaktiranje cementa v najrazličnejših pogojih.
Za izvedbo majhne količine gradbenih del strokovnjaki priporočajo uporabo, ki tehtajo do pet kilogramov. Za večja dela gradbeniki uporabljajo velika orodja za učinkovito stiskanje betona v proizvodnji z veliko sprednjo stranjo.
Eden od najpomembnejše lastnosti betonska mešanica - sposobnost plastičnega širjenja pod delovanjem lastne mase ali obremenitve, ki se nanjo nanaša. To določa relativno enostavnost izdelave izdelkov najrazličnejšega profila iz betonske mešanice in možnost njene uporabe za zbijanje. različne načine. V tem primeru sta način zbijanja in lastnosti zmesi (njena mobilnost ali fluidnost) tesno povezani. Tako toge nepretočne mešanice zahtevajo močno zbijanje, pri oblikovanju izdelkov iz njih pa je treba uporabiti intenzivno vibracijo ali vibracijo z dodatnim stiskanjem (z obremenitvijo). Obstajajo tudi drugi načini stiskanja trdih mešanic - nabijanje, stiskanje, valjanje.
Mobilne mešanice se enostavno in učinkovito stiskajo z vibracijami. Uporaba stiskalnih (stiskalnih) vrst zbijanja - stiskanja, valjanja, pa tudi nabijanja - je neprimerna za takšne mešanice. Pod vplivom znatnih stiskalnih sil ali pogosto ponavljajočih se udarcev nabijača bo mešanica zlahka iztekla izpod matrice ali pa jo bo nabijal razpršil.
Lite mešanice se lahko stisnejo pod vplivom lastne teže. Da bi povečali učinek zbijanja, so včasih izpostavljeni kratkotrajnim vibracijam.
Tako ga je mogoče razlikovati naslednje načine Utrjevanje betonskih mešanic: vibriranje, stiskanje, valjanje, nabijanje in litje. Najučinkovitejša tako tehnično kot ekonomsko je metoda vibriranja. Uspešno se uporablja tudi v kombinaciji z drugimi metodami.
Mehansko tesnilo - z nabijanjem (vibro-tiskanjem! s stiskanjem (vibro-stiskanjem), z valjanjem (vibro-valjanjem). vesel "NOVIDNOST mehanske metode zbijanje premičnih betonskih mešanic je centrifugiranje, ki se uporablja pri tvorbi votlih cevastih izdelkov. Dobri rezultati pri proizvodnji betona Visoka kvaliteta omogoča sesanje mešanice v procesu njenega mehanskega zbijanja (predvsem z vibracijami), vendar znatno trajanje postopka sesanja znatno zmanjša njen tehnični in ekonomski učinek, zato se ta metoda v tehnologiji montažnih betonov ne uporablja široko.
Na kratko razmislite o bistvu zgornjih metod stiskanja betonskih mešanic.
Vibracija je zbijanje betonske mešanice kot posledica prenosa nanjo pogosto ponavljajočih se prisilnih nihanj, ki se v agregatu izražajo s tresanjem. V vsakem trenutku stresanja so delci betonske mešanice tako rekoč v suspendiranem stanju in njihova povezava z drugimi delci je prekinjena. Z naknadnim delovanjem potisne sile delci pod lastno težo padejo in hkrati zavzamejo ugodnejši položaj, v katerem so lahko manj prizadeti zaradi udarcev. To ustreza stanju njihovega najgostejšega pakiranja med drugimi, kar na koncu vodi do goste betonske mešanice. Drugi razlog za zbijanje betonske mešanice med vibracijami je sposobnost premikanja v začasno tekoče stanje pod delovanjem zunanjih sil, ki se nanjo nanašajo, kar imenujemo tiksotropija. Biti notri tekoče stanje, se betonska mešanica med vibracijami začne širiti, pridobi obliko - j in se stisne pod delovanjem lastne mase. U Tretji razlog za zbijanje določa visoke tehnične lastnosti betona. ,
Visoka stopnja zbijanja betonske mešanice z vibracijami | doseženo z uporabo opreme nizke moči. Na primer, betonske mase s prostornino več kubičnih metrov se stisnejo z vibratorji s pogonsko močjo le 1 ... 1,5 kW.
Sposobnost betonskih mešanic, da pod vplivom vibracij preidejo v začasno tekoče stanje, je odvisna od mobilnosti mešanice in hitrosti gibanja njenih delcev drug glede na drugega. Mobilne mešanice zlahka preidejo v tekoče stanje in zahtevajo visoka hitrost premikanje. Toda s povečanjem togosti (zmanjšanjem mobilnosti) betonska mešanica vse bolj izgublja to lastnost ali zahteva ustrezno povečanje stopnje vibracij, kar pomeni, da so potrebni višji stroški energije za zbijanje.
Hitrost v (cm / s) nihanja med vibracijami je izražena z zmnožkom amplitude A in frekvence n nihanj: u \u003d An
Plošče. Praksa je pokazala, da se mobilne betonske mešanice učinkovito stisnejo z amplitudo nihanja 0,3 ... 0,35 mm,
In trdo - 0,5 ... 0,7 mm.
Na kakovost vibrokompaktacije ne vplivajo samo parametri vibracijskega mehanizma (frekvenca in amplituda), temveč tudi trajanje vibracij. Za vsako betonsko mešanico je glede na njeno gibljivost določeno svoje optimalno trajanje vibrokompaktiranja, do katerega se zmes učinkovito stisne in preko katerega se stroški energije povečajo v veliko večji meri kot se zmes stiska. Nadaljnje zbijanje sploh ne daje povečanja gostote. Poleg tega lahko pretirano dolgotrajne vibracije povzročijo razslojevanje mešanice, njeno ločitev na ločene komponente - cementno malto in velika zrna agregata, kar bo na koncu povzročilo neenakomerno gostoto izdelka po odseku in zmanjšanje trdnosti v ločeni deli njegovega.
Seveda so dolgotrajne vibracije nedonosne tudi z ekonomskega vidika: stroški energije in delovna intenzivnost se povečajo, produktivnost linije za oblikovanje pa se zmanjša.
Intenzivnost vibrokompaktiranja I (cm2/s3), izražena z najkrajšim trajanjem tresljajev, je odvisna tudi od glavnih parametrov delovanja vibracijskega mehanizma - frekvence in amplitude nihanja, ki se izvaja ob upoštevanju njihove medsebojne kombinacije hitrosti in pospeška. nihanja: I = A2 / n3.
Intenzivnost vibrokompaktacije se poveča tudi, če je frekvenca prisilnih tresljajev enaka frekvenci naravnih tresljajev. Zaradi dejstva, da ima betonska mešanica širok razpon velikosti delcev (od nekaj mikrometrov za cement do nekaj centimetrov za grobi agregat) in s tem razlike v pogostosti njihovih naravnih vibracij, bo najbolj intenzivno zbijanje mešanice ko je za način vibracije značilen različne frekvence. Tako se je pojavil predlog za uporabo polifrekvenčnih vibracij.
Te dejavnike je treba upoštevati za tehnično in ekonomsko oceno postopkov oblikovanja izdelkov. Iz navedenega sledi, da se učinkovitost stiskanja povečuje z naraščajočo energijo stiskanja, trajanje stiskanja se skrajša in poveča produktivnost vlivne linije. Tako lahko na podlagi tehnične in ekonomske analize lastnosti betonske mešanice, zmogljivosti kalupne linije izberete moč vibrokompaktnih mehanizmov.
Vibracijsko zbijanje betonske mešanice se izvaja s prenosnimi in stacionarnimi vibracijskimi mehanizmi. Uporaba prenosnih vibratorjev v montažnem betonu je omejena. Uporabljajo se predvsem pri oblikovanju velikih masivnih izdelkov na stojnicah.
V tehnologiji montažnega betona v delujočih tovarnah
V skladu s shemami pretočnega agregata in transporterja se uporabljajo vibracijske ploščadi. Vibracijske platforme odlikuje široka paleta vrst in izvedb vibratorjev - elektromehanskih, elektromagnetnih, pnevmatskih; narava vibracij - harmonična, udarna, kombinirana; oblika tresljajev - krožno usmerjena - navpična, vodoravna; načrtovalne sheme mize - s trdnim zgornjim okvirjem, ki tvori mizo z eno ali dvema vibracijskima gredoma in sestavljen iz ločenih vibracijskih blokov, ki na splošno predstavljajo skupno vibracijsko ravnino, na kateri se nahaja oblika z betonsko mešanico.
Za trdnost pritrditve obrazca na mizo platforme so predvideni posebni mehanizmi - elektromagneti, pnevmatske ali mehanske sponke.
Vibracijska ploščad (slika 11.1) je ravna miza, podprta z vzmetnimi nosilci na fiksnih nosilcih ali okvirju (okvirju). Vzmeti so zasnovane tako, da dušijo tresljaje mize in s tem preprečijo njihov udarec na nosilce, sicer se uničijo. V spodnjem delu je na mizo togo pritrjena vibrirajoča gred z ekscentri, ki se nahajajo na njej. Ko se gred vrti iz elektromotorja, ekscentri vzbujajo tresljaje mize, ki se nato prenesejo na obliko z betonsko mešanico, posledično se stisne. Moč vibracijske platforme je ocenjena z njeno nosilnostjo (masa izdelka skupaj s kalupom), ki je 2...30 ton.
Montažne armiranobetonske tovarne so opremljene z enotnimi vibracijskimi ploščadmi, s frekvenco vrtenja 3000 vrt / min in amplitudo 0,3 ... 0,6 mm. Te vibrirajoče ploščadi dobro kompaktirajo togo betonsko mešanico konstrukcij do 18 m dolžine in do 3,6 m široke.
Pri oblikovanju izdelkov na vibracijskih ploščadih, zlasti iz trdih betonskih mešanic na poroznih agregatih, se za izboljšanje strukture betona uporabljajo uteži - statične,
Vibracijski, pnevmatski, vibropnevmatski. Vrednost teže, odvisno od lastnosti betonske mešanice, je 2 ... 5 kPa.
Pri oblikovanju izdelkov v fiksnih kalupih se betonska mešanica stisne s površinskimi, globinskimi in vgrajenimi vibratorji, ki so pritrjeni na kalup. Pri izdelavi izdelkov v vodoravnih oblikah se uporabljajo toge ali počasi premikajoče se betonske mešanice in pri oblikovanju v navpični obliki
nekatere oblike (v kasetah) uporabljajo mobilne mešanice z obleganjem stožca 8 ... 10 cm.
F Stiskanje je redko uporabljena metoda stiskanja betonske mešanice v tehnologiji montažnih betonov, čeprav je zelo učinkovita v smislu tehničnih kazalnikov, ki vam omogoča, da dobite beton visoke gostote in trdnosti z minimalno porabo cementa (100 ... 150). kg / m3 betona). Preprečujemo izključno širjenje metode stiskanja ekonomski razlogi. Tlak stiskanja, pri katerem se beton začne učinkovito zbijati, je 10 ... 15 MPa in več. Tako je za tesnjenje izdelka za vsak 1 m2 potrebno uporabiti obremenitev, ki je enaka 10 ... 15 MN. Stiskalnice takšne moči se uporabljajo v inženirstvu, na primer za stiskanje ladijskih trupov, vendar se izkaže, da so njihovi stroški tako visoki, da popolnoma odpravijo ekonomska izvedljivost uporaba takšnih stiskalnic.
V tehnologiji montažnih betonov se stiskanje uporablja kot dodatna mehanska obremenitev betonske mešanice med njenimi vibracijami. V tem primeru zahtevana vrednost pritiska stiskanja ne presega 500 ... 1000 Pa. Tehnično se ta tlak doseže pod delovanjem statično uporabljene obremenitve kot posledica prisilnega premikanja posameznih delcev betonske mešanice.
Razlikovati med stiskanjem s ploščatimi in profilnimi žigi. Slednji prenašajo svoj profil betonske mešanice. Tako oblikovano stopnišča, nekatere vrste rebrastih plošč. V slednjem primeru se metoda stiskanja imenuje tudi žigosanje. Najem je vrsta stiskanja. V tem primeru se pritisk stiskanja na betonsko mešanico prenese samo skozi majhno območje valj, kar posledično zmanjša potrebo po stiskanju. Toda tukaj plastične lastnosti betonske mešanice, skladnost njene mase pridobijo poseben pomen. V primeru nezadostne kohezije bo mešanica premaknjena s tlačnim valjem in jo zlomila. Centrifugiranje - zbijanje betonske mešanice Kot posledica delovanja centrifugalnih sil, ki nastanejo v njej med vrtenjem. V ta namen se uporabljajo centrifuge (slika 11.2), ki so cevasti odsek, ki se med stiskanjem vrti do 600 ...
valjanje med vrtenjem, se pritisne na notranjo površino kalupa in hkrati stisne. Zaradi različne gostote trdnih komponent betonske mešanice IN VODE se iz betonske mešanice odstrani do 20 ... 30% vode, kar prispeva k proizvodnji betona visoke gostote.
Metoda centrifugiranja relativno enostavno omogoča pridobivanje izdelkov iz betona visoke gostote, trdnosti (40 ... 60 MPa) in vzdržljivosti. Hkrati je za pridobitev betonske mešanice visoke kohezije potrebna velika količina cementa (400 ... 450 kg / m3), sicer se bo mešanica pod delovanjem centrifugalnih sil razslojila na majhna in velika zrna, ker se bo slednji z veliko silo oprijel površine kalupa. Cevi, daljnovodni drogovi, stojala za svetilke se oblikujejo s centrifugiranjem. Pri sesanju se v betonski mešanici ustvari vakuum do 0,07 ... 0,08 MPa, zrak, ki je vključen v njeno pripravo in polaganje v kalup, pa tudi nekaj vode, pa se iz betonske mešanice odstrani pod delovanjem ta vakuum: izpraznjena mesta zasedajo trdni delci in betonska mešanica pridobi povečano gostoto. Poleg tega prisotnost vakuuma povzroči pritisk na betonsko mešanico z atmosferskim tlakom, ki je enak vrednosti vakuuma. Prispeva tudi k zbijanju betonske mešanice. Sesanje je praviloma kombinirano z vibracijami. V procesu vibriranja betonske mešanice, ki je izpostavljena vakuumu, pride do intenzivnega polnjenja trdnih komponent por, ki nastanejo med vakuumom na mestu. zračni mehurčki in vodo. Vendar ima v tehničnem smislu sesanje pomembno tehnično in ekonomsko pomanjkljivost, in sicer: dolg procesni čas - 1 ... 2 minuti na vsak 1 cm debeline izdelka, odvisno od lastnosti betonske mešanice in velikosti preseka. . Debelina sloja, ki ga je mogoče izpostaviti vakuumu, ne presega 12...15 cm, zato se sesanju izvajajo predvsem masivne konstrukcije, ki dajejo površinski plasti posebno visoko gostoto. V tehnologiji montažnega armiranega betona se sesanje praktično ne uporablja. wj
Zbijanje tal je ena najpomembnejših operacij tehnološki proces erekcijo subgrade in pločnikih.
Tesnilo se izvaja z nanašanjem na površino tal, materialov za gradnjo cest ali njihovih mešanic kratkotrajnih ponavljajočih se ali cikličnih obremenitev. Pod delovanjem teh obremenitev se tla deformirajo. Popolna deformacija je sestavljena iz reverzibilne (elastične), t.j. okrevanje po odstranitvi bremena in nepopravljivo (preostalo).
Pri sorazmerno majhni vrednosti zunanjih obremenitev se nepopravljive deformacije pojavljajo predvsem kot posledica spremembe prostornine tal, kar povzroči njeno zbijanje. Večja (večja) je velikost obremenitev,. večji del nepopravljive deformacije nastane kot posledica spremembe oblike tal, ki se kaže v obliki znatnega posedanja in izbočenja tal na straneh izpod delovnega telesa stroja.
Parametri tesnilnega stroja izbrati je treba tako, da dobimo največjo vrednost nepopravljivih volumetričnih deformacij in ne povzročimo znatnega plastičnega pretoka tal, ki negativno vpliva na proces zbijanja.
Trdnost delcev tal bistveno presega moč vezi med njimi. Torej pečat je možno le zaradi medsebojnega gibanja delcev trdne faze in posledično zmanjšanja poroznosti tal (zmesi), kar je povezano z izpodrivanjem zraka (ali vlage) iz por. Delo, porabljeno za zbijanje, se v glavnem porabi za premagovanje sil vezi in trenja med delci trdne faze. Del se porabi za uničenje trdnih delcev.
Deformacija tal teče v času. Pod delovanjem kratkotrajnih obremenitev je trajanje obremenjenega stanja tal veliko krajše od časa, potrebnega za popoln potek deformacije. Posledično, da bi dobili želeno zbijanje tal stroji potrebujejo večkratno uporabo obremenitve.
Od kakovosti postopka tesnila odvisen je nadaljnji servis podlage in pločnika. Zahteve glede gostote so določene za vsako od teh struktur. stisnjena plasti. Hkrati pa metoda standarda tesnila, zato so zahteve po gostoti običajno izražene s faktorjem zbijanja, t.j. v delcih največje standardne gostote
Glede na vrsto pločnika so sprejete naslednje vrednosti faktorji zbijanja:
1) za ceste z izboljšanimi kapitalnimi in lahkimi pločniki (cementobeton, asfalt beton, črni lomljenec, črni gramoz itd.) v območju 0,95-0,98, medtem ko je zgornja meja priporočljiva za cementnobetonske pločnike;
2) za ceste s prehodnim pločnikom (drobljen kamen, gramoz, žlindra itd.), ki je enak 0,9.
V vdolbinah in ničelnih mestih med gradnjo cest z izboljšanimi premazi - najmanj 0,9.
Stopnja stiskanja je v veliki meri odvisno od vsebnosti vlage v tleh.
Povečanje vlažnosti na določeno vrednost vodi do povečanja gostote. Z naraščajočo vlažnostjo se vedno več volumna por napolni z vodo in zato bo gostota manjša. Stanje tal, katerih pore so popolnoma napolnjene z vodo, bo tako rekoč njena meja. tesnila.
Če je vlažnost stisnjena tla spodaj optimalne vrednosti, je treba uporabiti močnejše stroji za stiskanje ali za vlaženje tal. V primeru, ko je vlažnost večja od optimalne vrednosti, zahtevane gostote ni mogoče doseči, zato je treba zemljo pustiti, da se posuši.
Učinek zunanje obremenitve in vpliv glavnih parametrov strojev na učinkovitost stiskanja lahko ocenimo na naslednji način:
1) za vsako vrsto tal obstaja lastna najugodnejša kontaktna napetost, enaka 0,9-1,0 njene natezne trdnosti, pri kateri je mogoče doseči najboljše rezultate zbijanja;
2) globina stiskanja je odvisna od velikosti kontaktne površine delovnih teles strojev, skozi katere se prenaša pritisk na tla, zato bo pri isti napetosti globina stiskanja večja, večja je prečna velikost kontaktnega območja;
3) učinkovitost zbijanja je ob drugih enakih pogojih odvisna od hitrosti spreminjanja napetostnega stanja tal in trajanja obremenitve, manjša pa je hitrost spremembe napetostnega stanja, višje stopnje tesnila je mogoče dobiti;
4) globina zbijanja tal s stroji pod enakimi pogoji je odvisna od dimenzij delovnega telesa glede na (določeno z najmanjša velikost), stopnja zbitosti pa je odvisna od vrednosti normalnih kontaktnih napetosti.
Zbijanje tal in drugih cestnih gradbenih materialov v telesu nasipa, podlagi pločnika in v samem pločniku izvajajo stroji, katerih delovanje temelji na naslednjih načelih:
a) valjanje - uporaba statični tlak valjanje drugačna oblika delovna površina;
b) nabijanje - s pomočjo dinamičnih udarcev (padajoča bremena z določene višine);
c) vibracije - s posredovanjem vibracijskih gibov tesnilnemu materialu, zaradi česar pride do medsebojnega premikanja in zbijanja trdnih delcev;
d) kombinacija teh metod - valjanje z vibracijami, vibracije z nabijanjem itd.
Kljub razliki v principih delovanja stiskalnih strojev ima postopek stiskanja v vseh primerih veliko skupnega in le pri vibriranju opazimo nekatere posebnosti.
V vseh primerih je vpliv na tla ali materiale delovnih teles strojev povezan z uporabo ciklične obremenitve (Kharhutova tabela, str. 473).
Učinek strojev za zbijanje zemlje je odvisen od pravilne izbire debeline stisnjenega sloja. Pri preveliki debelini plasti ni dosežena zahtevana gostota tal. Če so debeline plasti premajhne, se produktivnost zmanjša in stroški dela se povečajo.
Globina aktivne cone je odvisna od prečnih dimenzij žiga v načrtu, velikosti napetosti, hitrosti spreminjanja napetostnega stanja ter vrste in vlažnosti tal.
Za kategorija:
Stroji za zbijanje tal
Fizikalne osnove procesa zbijanja tal s stroji
Zbijanje tal je eno izmed najbolj pomembnih elementov tehnološki proces montaže podlage avtomobilskega in železnice, jezovi itd. Njihova nadaljnja storitev je odvisna od kakovosti tega procesa. Da bi dosegli zadostno stabilnost, so za vsako od teh struktur določene zahteve glede gostote njihovih tal. Hkrati se kot osnova za ocenjevanje stopnje zbitosti uporablja standardna metoda zbijanja, zato so zahteve po gostoti tal običajno izražene kot faktor zbitosti, to je v deležih največje standardne gostote (bmax). Za zgornje plasti podlaga tla avtoceste zahteve za gostote so visoke - tukaj gostota tal ne sme biti nižja od (0,98-e-1,0) bmax. Za nižje plasti nasipov se lahko zmanjša na 0,956 max. Gostote tal železniških nasipov, odvisno od lokacije obravnavane plasti v nasipih, naj bodo znotraj (0,90-0,98) 6 gaax, gostote tal jezov pa se določijo v vsakem posameznem primeru. Treba je opozoriti, da je doseganje tako visoke gostote, kot je (0,98h-1,0)bmax, povezano s precejšnjimi težavami in ga je mogoče doseči le z prava izbira tako parametri uporabljenih strojev kot tudi način njihovega delovanja. Zbijanje tal je treba izvajati samo s posebnimi stroji, namenjenimi za ta namen. Poskus uporabe zemeljskih strojev za to in kombiniranja tega postopka z odstranjevanjem nasipov je pokazal, da je gostota tal nezadostna in zbijanje neenakomerno, zato lahko ta metoda služi le za predhodno zbijanje tal, kar seveda , olajša delo glavnih strojev.
Vlaga tal igra pomembno vlogo pri zbijanju. Vsaka obremenitev, ki deluje na tla, ima svojo optimalna vlažnost, pri kateri je mogoče z najmanjšo količino mehanskega dela doseči zahtevano gostoto. V primeru nezadostne vlažnosti je za doseganje zahtevane gostote potrebno izvesti številne ukrepe, ki vključujejo na primer zmanjšanje debeline stisnjene plasti. Upoštevati je treba, da zelo suha tla sploh ne moremo doseči zahtevane gostote. Optimalna vlažnost tal W0, ki jo določimo s standardnim načinom zbijanja, ustreza delovanju srednje velikih strojev.
Tla se stisnejo z valjanjem, nabijanjem, vibracijami in vibrotampanjem.
Pri valjanju po tleh se kotali boben ali kolo, na kontaktni površini katerega je določen specifični pritisk (napetost), zaradi česar se razvije nepopravljiva deformacija tal. Na tem principu temelji delovanje vseh valjev. Pri nabijanju tla stisne padajoča masa, ki je bila predhodno dvignjena na določeno višino in ima v trenutku, ko se sreča s površino tal, določeno hitrost. Tako je nabijanje povezano z udarcem delovnega telesa stroja na tla. Pri vibriranju se stiskalna masa nahaja na površini stisnjene plasti (površinski vibratorji) ali znotraj nje (globoki vibratorji). Zaradi posebnega mehanizma se spravi v stanje nihajnega gibanja. del kinetična energija te mase se porabi za vibracije tal, ki so posledica relativnih premikov njenih delcev, kar ima za posledico njihovo gostejše pakiranje. Pri vibriranju ni ločitve mase od stisnjene površine oziroma je zelo nepomembno. Če motnje mase presežejo določeno mejo, se ta loči od površine tal, kar bo povzročilo pogoste udarce mase ob tla. V tem primeru se bo vibracija spremenila v vibrotamping. Ta postopek se od nabijanja razlikuje po visoki pogostosti udarcev. Kljub nizki višini množičnega padca, zaradi razvoja visoke hitrosti gibanja, udarna energija je lahko pomembna.
V vseh primerih je vpliv na tla delovnih teles stroja povezan s ciklično obremenitvijo.
Predpostavlja se, da imajo tla optimalno vsebnost vlage.
Specifični tlaki na kontaktnih površinah delovnih teles strojev z zgoščenimi tlemi ne smejo biti višji od njihovih meja trdnosti, hkrati pa ne smejo biti nizki, saj se sicer zmanjša učinek zbijanja. Najboljši učinek bo dosežen v primerih, ko so specifični tlaki na kontaktnih površinah z delovnimi telesi stiskalnih strojev enaki (0,9-t-1,0) ap (ap - končna trdnost). Izjema od tega pravila so stroji, katerih delovanje delovnih teles temelji na njihovem globokem prodiranju v stisnjeno plast zemlje (odmikalni in rešetkasti valji).
Deformacija in s tem učinek zbijanja sta odvisna tako od hitrosti spreminjanja napetostnega stanja kot od trajanja obremenitve in posledično od števila ponovitev njene uporabe.
Narava interakcije delovnih teles strojev s tlemi kavljev je taka, da jo je mogoče zmanjšati na shemo obremenitve polovice tal s togim okroglim žigom
Učinek delovanja strojev za zbijanje tal je odvisen od tega, kako pravilno je izbrana debelina stisnjenega sloja. Pri preveliki debelini plasti ni dosežena zahtevana gostota tal. Če so debeline plasti premajhne, se produktivnost strojev zmanjša in stroški dela se povečajo.
Profesor N. N. Ivanov je teoretično ugotovil, da je največja globina, do katere še sega delovanje bremena, 3,5 cm (dm-premer žiga). Kasneje je bil ta sklep eksperimentalno potrjen. Znotraj te cone, ki je še vedno podvržena delovanju obremenitve, je treba razlikovati še eno cono, kjer se v procesu zbijanja tal deformacija v globino porazdeli še bolj ali manj enakomerno. To območje lahko imenujemo aktivno, njegova globina pa globina aktivne cone. Ustvarjanje takšne cone olajšujejo množični plastični premiki talnih delcev in agregatov, ki se razvijejo po volumnu tal, ter dejstvo, da je zgoščena plast nameščena na bolj togi podlagi, ki je predhodno zbita tla. Prisotnost toge podlage vodi do koncentracije tlačnih napetosti vzdolž osi zgoščene obremenitve, pa tudi do manjšega globinskega padca napetosti, to je do njihove izravnave.
Pri nekohezivnih tleh je globina jedra 1,2-1,5-krat večja.
Približno 80 % vseh deformacij tal se zgodi znotraj aktivne cone, le 20 % pa se zgodi v volumnu tal, ki se nahaja zunaj tega območja. Zato debelina stisnjenega sloja zemlje ne sme biti večja od globine aktivne cone, sicer ne bo dosežena zahtevana gostota tal.
Optimalna debelina stisnjene plasti zemlje je tesno povezana z globino sredice. Pod optimalno debelino se razume taka debelina, pri kateri je dosežena zahtevana stopnja zbijanja z najmanj mehanskega dela in največjo produktivnostjo stroja. Globina aktivne cone določa zgornjo mejo optimalnih debelin stisnjenih plasti tal. V primerih, ko zahtevana gostota med zbijanjem tal ne presega 0,956max, se lahko optimalna debelina plasti vzame za enako globino sredice. Hkrati se taka gostota doseže razmeroma enostavno in ne zahteva veliko število avtomobilski prehodi.
Najmanjša velikost delovnega telesa stroja v načrtu določa največja vrednost optimalna debelina talnega sloja, torej tako rekoč možnost zbijanja, ki pa se lahko uresniči le, če je napetost na površini tal blizu natezne trdnosti. Pri manjših napetostih se bo optimalna debelina plasti zmanjšala.
Če je zahtevana gostota tal visoka in znaša (0,98-7-1,0) 8max, potem je optimalna debelina plasti enaka polovici globine jedra (H0 = 0,5ftn). To gostoto je mogoče doseči tudi z debelino sloja, ki je enaka globini aktivne cone, vendar je v tem primeru treba število prehodov povečati za faktor 3 v primerjavi s primerom, ko je zahtevana gostota 0,95 bar max. Zato postane zbijanje tal s tako veliko debelino plasti ekonomsko nerentabilno.
Zmanjšanje debeline stisnjene plasti tal v primerjavi z optimalno vrednostjo ob ohranjanju enakih dimenzij delovnega telesa in enake velikosti napetosti, ki se razvije na površini tal, praviloma pomeni preveliko porabo specifičnega dela, t.j. , delo, potrebno za stiskanje enote prostornine tal.
Analiza formule (IV. 1) kaže, da zmanjšanje napetosti na (0,5-7-0,6) op praktično ne vpliva na globino jedra in posledično na optimalna debelina stisnjena plast. Hkrati je treba opozoriti, da vsako zmanjšanje stresa vodi do povečanja zahtevanega števila ponovitev uporabe obremenitve.
Zaradi zbijanja je treba pridobiti ne le zahtevano gostoto tal, temveč tudi njeno trdno strukturo. To je mogoče doseči le z upoštevanjem določenega načina delovanja. Najprej se to nanaša na specifični tlak, ki mora biti blizu končne trdnosti tal, vendar ne sme presegati slednje ne le na koncu zbijanja, temveč v celotnem procesu. Če kršite to pravilo in nemudoma izberete pritisk, ki naj se zgodi šele na koncu procesa zbijanja, ko je zemlja že gosta in močna, se bo pri prvih prehodih struktura uničila, še posebej blizu površine. To bo otežilo nadaljnje oblikovanje gosto in močno strukturo, gostota in trdnost pa bosta na koncu doseženi nižji od tistih, ki jih dobimo s postopnim povečevanjem specifičnega tlaka. Na uničenje strukture na primer kaže močno valovanje pred valji ali kolesi valjev, pa tudi izbočenje tal s strani.
Tako lahko rečemo, da se mora specifični tlak delovnega telesa stroja postopoma povečevati od prehoda do prehoda v primeru valjev ali od udarca do udarca z nabijalci. Ta proces povečanja specifičnega tlaka se do neke mere samodejno izvede s postopnim zmanjševanjem globine tira med valjanjem in časa udarca med zbijanjem. Hkrati se specifični tlaki povečajo za 1,5-2 krat, pri čemer je potrebno, da postanejo 3-4 krat višji. Zato je treba tla stiskati z dvema strojema - lahkim in težkim. Lahka naprava naj služi za predhodno zbijanje, težka pa za končno spravljanje tal do zahtevane gostote. Uporaba predkompaktiranja zmanjša skupno potrebno število prehodov ali udarcev na enem mestu za približno 25 %. Če še upoštevamo, da se na začetku postopka uporabljajo lažja sredstva, potem vse to daje prihranek do 30 % skupnih stroškov stiskanja.
Prehod na zbijanje s težjim strojem ne bi smel povzročiti močno povečanje napetosti na površini tal. Zato je najboljši učinek dosežen, ko bo napetost na površini ob prvem udarcu težjega stroja enaka napetosti, ki ustreza zadnjemu udarcu lažjega stroja. Pri valjanju z valji na pnevmatikah je ta zahteva izpolnjena, ko se predhodno stiskanje izvaja z valjčkom, katerega obremenitev na vsako kolo je 2-krat manjša kot pri glavnem stiskanju, tlak v pnevmatikah pa se zmanjša za 1,5-2 krat. . Pri strojih za nabijanje je mogoče predhodno zbijanje izvajati s strojem, katerega delovno telo tehta polovico manj, ali z istim strojem, ki proizvaja glavno zbijanje, vendar s 4-kratnim zmanjšanjem višine padca delovnega telesa. Med predkompaktiranjem je treba opraviti 30-40 % skupnega zahtevanega števila prehodov.
Predhodno zbijanje se lahko izpusti, če so tla pri gradnji nasipa zbijali zemeljski ali zemeljski stroji do gostote najmanj 0,906 ha, kar nastane na primer pri strgalnikih.
Pri valjanju ima določen vpliv hitrost valjev. Pri različnih hitrostih vožnje je optimalna gostota tal praktično dosežena v enakem številu prehodov. Ta sklep potrjujejo neposredni testi in izhaja iz reoloških lastnosti tal. Tako je bilo v 2. poglavju prikazano, da hitrost spremembe napetostnega stanja praktično vpliva na velikost nepopravljive deformacije le do določenih vrednosti. Hitrosti, ki nastanejo med valjanjem, so že zunaj njihovega vpliva.
Vendar je bilo ugotovljeno, da pri visoke hitrosti gibanju nastane manj trpežna struktura tal, kar je razloženo z nekoliko večjimi strižnimi silami, ki delujejo na tla. Izvedene študije so omogočile razvoj racionalnega režima valjanja pri visokih hitrostih, pri katerem se kakovost zbijanja ne le ne zmanjša, ampak se tudi nekoliko poveča. V tem načinu je treba prvi in zadnja dva prehoda opraviti pri nizki hitrosti (1,5-2,5 km/h), vsi vmesni prehodi pa pri visoki hitrosti (8-10 km/h). V tem načinu se zmogljivost poveča za približno 2-krat. Zasnova valjev mora omogočati zbijanje tal pri razumni hitrosti.
Za Kategorija: - Stroji za zbijanje tal
Vpliv amplitude in frekvence nihanja
Frekvenca nihanja delcev in njihova amplituda sta medsebojno povezani, kar omogoča uporabo v industrijsko okolje različni načini vibracije za mešanice različnih konsistence. Mešanice z frakcijo grobozrnatega agregata vibrirajo z relativno nizko frekvenco (3000-6000 tresljajev na minuto), vendar s precej veliko amplitudo, medtem ko se visokofrekvenčna vibracija uporablja za vibrokompaktiranje drobnozrnatih mešanic - do 20.000 vibracij na minuto. minuto, vendar z majhno amplitudo.
Shema možnosti stiskanja betona: a) globok vibrator; b) paket globokih vibratorjev; c) vibrator s gibljivo gredjo; d) površinski vibrator; e) zunanji vibrator; f) sprememba trdnosti betona glede na čas njegovega zbijanja.
Poleg takih delovnih parametrov vibracijskega mehanizma, kot sta amplituda in frekvenca, na kakovost zbijanja kot posledica vibracij vpliva tudi trajanje samega procesa. Za vse vrste betonskih mešanic, odvisno od njihove tekočnosti, obstaja optimalen čas vibracijsko zbijanje, med katerim se zmes učinkovito stisne in po katerem so stroški energije nesorazmerni z učinkovitostjo nadaljnjega stiskanja. Ker se zbijanje nadaljuje po tem času, na splošno ni opaziti povečanja gostote. Poleg tega obstaja nevarnost, da se bo betonska mešanica začela razslojevati na posamezne sestavine, odvisno od njihovih lastnosti - na primer frakcija grobozrnatega agregata in cementna suspenzija. Kot rezultat, kakovost končnega betonski izdelek se bo zmanjšala zaradi neenakomerne porazdelitve gostote in zmanjšane trdnosti na določenih delih njenih delov.
Dolgotrajne vibracije so ekonomsko nerentabilne, saj so povezane z visokimi stroški energije in mukotrpnostjo celotnega procesa, zaradi česar se produktivnost livarske linije znatno zmanjša.
Sovpadanje frekvence naravnih nihanj delcev raztopine s frekvenco prisilnih vibracij vibrokompaktorja pozitivno vpliva na učinkovitost zbijanja. Toda tukaj morate upoštevati dejstvo, da je mešanica kombinacija različnih frakcij z različne velikosti delci - od mikrometrov do cementna malta do nekaj centimetrov za velik betonski agregat. V skladu s tem največ učinkovita tehnologija zgostitev bo uporaba različnih frekvenc - tako imenovana polifrekvenčna zgostitev, saj je frekvenca naravnih nihanj za delce različne velikosti in masa bo drugačna.
Pri izdelavi študije izvedljivosti je treba upoštevati navedeno – s povečanjem energije stiskanja se poveča učinkovitost stiskanja, kar tudi skrajša trajanje procesa in poveča donosnost.
Vibracijski stroji in vibracijske ploščadi
Vibrokompaktiranje betonske malte se izvaja tako s stacionarnimi kot prenosnimi sredstvi. Uporaba prenosnih sredstev v tehnologiji stiskanja montažnega betona je precej omejena. Njim industrijska uporaba gre predvsem za oblikovanje velikih, težkih izdelkov na stojnicah.
Vibroplatforme se uporabljajo v tovarniški proizvodnji montažnega armiranega betona tistih vrst obratov, ki delujejo po transportnih in pretočno-agregatnih shemah. Obstaja veliko različnih oblikovne značilnosti in vrste vibracijskih ploščadi - elektromagnetne, elektromehanske, pnevmatske. Po naravi vibracij - tolkalne, harmonične, kombinirane. Glede na obliko tresljajev - krožno usmerjeno, vodoravno, navpično. Po načrtovalnih shemah mize - trden zgornji okvir, ki tvori mizo z eno ali več vibracijskimi gredi ali sestavljen iz ločenih vibracijskih blokov, ki kot celota predstavljajo eno vibracijsko površino s kalupom z mešanico, ki se nahaja na njej. Za trdno pritrditev kalupa z malto so na mizi ploščadi predvideni pnevmatski elektromagneti ali mehanske sponke.
Diagram vibrirajoče mize z dimenzijami
Vibracijska ploščad je izdelana v obliki ravne mize, ki je podprta z vzmetnimi nosilci na postelji (okvir) ali na fiksnih nosilcih. Namen vzmeti je blažiti nihajne premike mize in s tem preprečiti njihov vpliv na oporo, kar bi neizogibno vodilo v uničenje. V spodnjem delu je na napravo pritrjena vibrirajoča gred z ekscentri, ki se nahajajo na njeni površini. Gred poganja elektromotor, gibanje ekscentrikov povzroča tresljaje mize, ki se nato prenesejo na maso betona in povzročijo zbijanje betonske mešanice. Moč vibracijske ploščadi se meri z nosilnostjo - maso betonskega izdelka skupaj z obliko - in se giblje od 2 do 30 ton.
Obrati za proizvodnjo montažnega betona so običajno opremljeni z enotnimi vibracijskimi platformami z amplitudo nihanja 0,3-0,6 mm in frekvenco 3000 nihanj na minuto. Takšne ploščadi se dobro spopadajo z zbijanjem konstrukcij z dolžino do 18 m in širino do 3,5 m.
Pri oblikovanju izdelkov na vibrirajočih platformah, še posebej, če se uporabljajo togi na osnovi poroznih agregatov, se uteži običajno uporabljajo za izboljšanje strukture betona.
Če je treba izdelek oblikovati s fiksno obliko, se betonska mešanica stisne s površinskimi, globinskimi in nameščenimi vibratorji, pritrjenimi na obliko. Pri izdelavi izdelkov z uporabo horizontalnih oblik se uporabljajo toge betonske mešanice ali mešanice z nizko tekočnostjo; v navpičnih oblikah (kasete) - mešanice z visoko tekočnostjo in ugrezom stožca 80-100 mm.
Postopek stiskanja
Stiskanje kot metoda stiskanja v proizvodnji izdelki iz armiranega betona se redko uporablja, kljub dejstvu, da je glede na tehnične indikacije zelo učinkovit, saj omogoča pridobivanje betona visoke trdnosti z visoka gostota z zelo nizko porabo cementa (100-150 kg / m 3 betona). Razlogi, ki preprečujejo širjenje te metode, so izključno ekonomske narave. Tlak, pri katerem se beton učinkovito stisne, je 10-15 MPa ali več, to pomeni, da je treba za stiskanje betonskega izdelka uporabiti silo, ki je enaka 10-15 MN (milijonov Newtonov), za vsak 1 m 2. Stiskalnice s takšno močjo se uporabljajo samo v ladjedelništvu za stiskanje ladijskih trupov, njihova cena pa je tako visoka, da pri uporabi popolnoma izključuje ekonomsko donosnost.
centrifugiranje
Med centrifugiranjem se vrteča se zmes stisne ob stiku z notranja površina obrazci. Zaradi postopka centrifugiranja se zaradi različne gostote sestavin betonske raztopine in vode, ki jo vsebuje, iz nje odstrani do 20-30% tekočine, kar povzroči beton visoke trdnosti.
Centrifugiranje olajša pridobivanje izdelkov iz betona visoka gostota, trdnost (40-60 MPa) in vzdržljivost. Ta metoda zahteva zadostno količino cementa, tako da ima končna betonska mešanica visoko kohezivnost (400-450 kg/m 3 ). V nasprotnem primeru bo pod delovanjem centrifugalne sile prišlo do ločitve na več plasti, saj se bodo zrna večje velikosti in mase močneje oprijela roba centrifugalnega kalupa kot zrna manjši. S pomočjo te tehnologije se oblikujejo stojala za svetilke, nosilce daljnovodov ali cevi.
Vakuumska raztopina
Pri uporabi metode evakuacije se ustvari redčenje zraka do tlaka 0,07-0,08 MPa, zaradi česar se odvečni zrak, vključen v raztopino, in odvečna voda odstranita pod vplivom razlik v tlaku. Beton zaseda v tem primeru izpraznjeni prostor, zaradi česar se gostota mešanice poveča. Prisotnost vakuuma ima tudi pritisk na betonsko maso, velikost tega učinka je enaka razliki med vakuumskim tlakom in zračni tlak. Zaradi tega učinka se zmes dodatno stisne.
Kombinacija evakuacije z vibracijami
Postopek evakuacije je zaželeno kombinirati z vibracijami. Med vibriranjem betonske raztopine, ki je izpostavljena vakuumu, trdne komponente mešanice intenzivno zapolnjujejo pore, ki nastanejo namesto zračnih mehurčkov in vodnih kapljic. Vendar ima evakuacija s tehničnega vidika pomembno tehnično in ekonomsko pomanjkljivost - dolgotrajnost postopka, ki glede na velikost reza traja približno 1-2 minuti za vsak 1 cm debeline.
Debelina sloja, ki ga je mogoče evakuirati, ne presega 12-15 cm, zato se konstrukcije velikih velikosti v glavnem evakuirajo, da bi njihov površinski sloj dobil večjo gostoto.