Видове набивки за жлези. Изборът на материали, използвани за производството на опаковка на сандъче. Описание на уплътненията на жлезите
ВЛИЯНИЕ НА УПЛОТНИТЕЛИТЕ GRAFLEX ВЪРХУ КОНСТРУКЦИИ НА САТЕНИКАТА НА РОТАЦИОННАТА И БУТАЛНАТА ПОМПА
Авдеев В.В., доктор на техническите науки, професор, ген. директор
Илин Е.Т., д-р, доцент, зам ген. директор по техническата политика
Уланов G.A., главен конструктор
абстрактно. Настоящата работа наблюдава работата на уплътнителя за сапунна кутия на помпата при третиране със силите на околната среда и компресията. Направено е сравнение между взаимодействието на нестандартни уплътнители и уплътнители "Graflex" с уплътнени повърхности. Дадени са препоръки за модификация на сапунката при използване на уплътнители "Графлекс". Ефективността на използване на "Графлекс" е оценена в сравнение с уплътнителите по поръчка.
Най-широко използван в уплътненията на вала центробежни помпиполучиха отдавна познати и прости по дизайн меки опаковки за пълнене. Повечето от произвежданите меки опаковки за пълнене се състоят от влакнеста тъкана подложка, импрегнирана с лубрикантс добавки от антифрикционни вещества (графит, талк и др.).
Херметичността на спълнежната кутия се определя преди всичко от хидравличното съпротивление на уплътнението, предоставено от него на уплътнената работна среда и степента на притискането му към уплътнените части. При реални условия на работа, сълзотворната кутия се влияе, от една страна, от силата на затягане на кутията за пълнене, а от друга страна, от налягането работна среда, което води до пластична деформация на материала и неговото уплътняване, което намалява порьозността и пропускливостта.
В същото време, по време на работа, опаковката на кутията за пълнене се износва, което е придружено от отстраняване на материала извън кутията за пълнене. стягане уплътнение на жлезатав процеса на износване намалява и изисква периодично възстановяване. Износването на опаковъчния материал зависи от редица фактори, основните от които са грапавостта на повърхността на подвижната уплътнена част, вида на движение спрямо опаковката (възвратно-постъпателно или въртеливо), интензивността на движение, контактното налягане на уплътнението на вала, налягането на уплътнената работна среда, агрегатно състояниеи физикохимични свойствасреда за запечатване, силата на вътрешните връзки на опаковъчния материал.
За възстановяване на дадена степен на херметичност се използва затягане на пълнежната кутия. Трудността при възстановяване на херметичността на спълнежната кутия, която е намаляла в резултат на механично износване на опаковката, чрез затягане на спълнежната кутия може да се обясни по следния начин. Тънък слой опаковка в близост до подвижната уплътнителна част е подложен на износване. Поради абразия от подвижната част, порьозността на материала в този тънък слой е по-висока, отколкото в останалия обем на опаковката. Порьозността на този слой може да бъде намалена чрез аксиална компресияи запълване на празнини с материал от основния слой. Запълването на такива кухини с опаковъчния материал зависи до голяма степен от пластичните свойства на материала, характеризиращи се с коефициента на странично налягане (Kb), който определя съотношението на аксиалната сила, приложена към уплътнителния елемент, предавана в радиална посока (за най-традиционно използваните плетени опаковки от AP, AS, APR, AGI Kb = 0,35-0,45). По време на работа, при периодично затягане на пълнежната кутия, пълнежният материал се уплътнява, губи пластичност и способността си да се деформира в аксиална и радиална посока. Поради това трябва да се прилага все повече и повече аксиална сила, за да се осигури уплътняването на монтажа, докато настъпи моментът, в който компресията на спълнятелната кутия вече не осигурява херметичността на монтажа и уплътнението трябва да бъде сменено.
Към гореизложеното трябва да се добави, че аксиалната сила, приложена към уплътнението, намалява значително по дълбочината на пълнежната кутия, поради триенето на пълнежа по стените на камерата и втулката на вала, а също и поради вътрешно триенев самата опаковка, което се получава по време на компресия. От своя страна, силата на триене на набивката върху съпоставящите се повърхности зависи от грапавостта на втулката и стените на кутията за пълнене и следователно разпределението на силите по дълбочината на кутията за пълнене зависи от тези фактори. Тъй като всеки уплътнителен пръстен отслабва силата на затягане на кутията за пълнене поради силите на триене, с увеличаване на дълбочината на кутията за пълнене и броя на монтираните пръстени, силата на натиск на последните пръстени ще намалее. Намаляването на силата на натиск води до факта, че слоевете на набивката в контакт с работната среда не са достатъчно уплътнени, така че средата може да проникне както през порите на самата набивка, така и между стеблото и набивката, което води до снижаване на налягането на сандъчната кутия.
Ориз. един. Качествена характеристикаразпределение на радиалното налягане по дълбочината на уплътнението на жлезата.
Ro - аксиален натиск върху набивката на салаза от страната на притискащата втулка;
ПП - налягане на работната среда;
Рв е налягането, упражнявано от уплътнението върху вала.
Качествено изменение на радиалната сила върху вала по дължината на сайлера, от общото действие на работната среда и въздействието на притискащата втулка е показано на фиг. 1. Както се вижда от фигурата, най-голямо натоварване понасят първите пръстени, които при работа имат износване от 70% от износването на цялото уплътнение на сальника, докато последните пръстени почти не се износват и по същество са излишни. Трябва да се добави, че стръмността на представената характеристика зависи основно от характеристиките на материала (от стойността на коефициента на странично налягане), колкото по-малък е Kb, толкова по-стръмна ще бъде тази крива.
Заедно с коефициента на страничен натиск, дизайнът на пълнежната кутия оказва значително влияние върху натиска на уплътнението, което трябва да бъде уплътнено спрямо втулката на вала.
Ориз. 2. Дизайн на кутия за пълнене с междинен пръстен за фенер за традиционни опаковки.
1. вал на помпата;
2. podsalnikovy бронзов пръстен;
3. стена на сандъчето;
4. бутащ ръкав;
5. пръстен за фенер.
Повечето от съществуващите конструкции на сальники на центробежни помпи са изпълнени със скосявания на крайната страна на спълнежната кутия и на напорната втулка, фиг. 2. Под действието на такъв скос крайните уплътнителни елементи изпитват допълнителна сила (Рrad), притискайки ги към втулката на вала, фиг.3. В резултат на това радиалният ефект на крайните (първи и последни) уплътнителни елементи върху защитната втулка на вала се увеличава и износването им се увеличава допълнително. Повече ▼, и има износване не само на уплътнителния материал, но и на защитната втулка на вала. Оперативната практика е показала наличието характерни зониизносване на втулката на вала в зоната, където са разположени тези пръстени. В резултат на това вече след 0,5-1 година, в зависимост от условията на работа, се налага ремонт или смяна на защитната втулка.
Фиг.3. Схема на преразпределение на предаването на аксиална сила от притискащата втулка със скосяване.
1.-стенна кутия за пълнене; 2.-напорна втулка; Z.-вал на помпата;
Ro - аксиална сила, действаща върху притискащата втулка;
Pa - аксиална сила, предавана от притискащата втулка към уплътнителния пръстен;
Rrad е радиалният компонент на аксиалната сила.
В допълнение, произтичащите от това прекомерни радиални налягания могат да доведат до увеличаване на триенето, локално нагряване на вала и дори кипене на работния флуид и в резултат на това аварийно разрушаване на пълнежната кутия.
В световната практика все повече широко приложениенамерете уплътнения на базата на термично експандиран графит (TEG), експандиран политетрафлуоретилен (PTFE) и техните композитни материали, като се използват подсилващи влакна с висока якост. Един от основните производители на тези продукти в Русия повече от 12 години е НПО УНИХИМТЕК, който произвежда цялата гама уплътнители под търговската марка GRAFLEX.
Основните предимства на новите уплътнителни продукти пред паронит, азбесто-графитни пръстени, азбест и памучни опаковки се определят от факта, че те са приложими в широк спектър от приложения.
(практически неограничен) диапазон от температури и налягания, имат добра свиваемост (20-60%) при натоварване и възстановяване (10-70%) след отстраняването му, еластичност (8-12%), не губят тези свойства с течение на времето - направете не се отпускат и "не стареят", химически са инертни и приложими в почти всяка среда, осигуряват уплътняване на уплътнения възел за дълго време без системно затягане, имат нисък коефициент на триене от 0,02 - 0,12% и висока топлопроводимост.
Наличието на изброените по-горе свойства прави възможно използването на тези материали за уплътняване на подвижни фуги високи скоростиплъзгане (до V= 25m/s) в широк диапазон от температури и налягания.
В момента ЗАО "Унихимтек" произвежда уплътнителни елементи под формата на пръстени (KGN-пръстени с ниска плътност от материал GRAFLEX) и плетени уплътнения (NGF-опаковки, оплетени от материал GRAFLEX) за уплътнителни помпи. Освен това уплътнителните пръстени са изработени от няколко вида, усукани (KGN-V) и издути, различни видове(KGN-SO, KGN-SOP).
Усуканите пръстени се изработват чрез спираловидно навиване на графитна лента, последвано от студено пресоване във форма до определена плътност. В резултат на такова пресоване фолийните слоеве се деформират под формата на гофриране в аксиална посока и са здраво свързани един с друг, осигурявайки херметичност. Плътността на уплътняване на пръстените се определя от параметрите и условията на последваща експлоатация и обикновено е в диапазона ρ=0,9-N,35 g/cm³. Тези пръстени имат висок коефициент на странично налягане (Kb = 0,7-0,85), поради което се използват за осигуряване на уплътнение при ниски стойности на аксиално налягане.
Слоестите пръстени се състоят от редуващи се хоризонтални слоеве графитно фолио, перфорирани от лист (перпендикулярно на оста на пръстена). Пръстенът KGN-SO се изработва чрез послойно полагане и залепване на слоевете заедно. Пръстенът KGN-SOP е изработен от графитно фолио с редуващо се полагане на всеки слой и последващо студено предварително пресоване. Тези пръстени имат висока топлопроводимост в радиална посока λ > 120 W/(m K) и нисък коефициент на странично налягане (Kb=0,1-0,15), поради което се използват за отвеждане на топлина и като дроселиращи пръстени. Поради малката стойност на Kb, остава много малка междина между вала и пръстена по време на компресия, където средният поток се дроселира, което осигурява повече благоприятни условияработа на други пръстени.
Плетените уплътнителни опаковки се изработват под формата на шнур, предимно с квадратно сечение, проходно, многоредово, диагонално тъкане. Тъкаща нишка се получава чрез усукване на лента от графитно фолио. За да придаде здравина на плетената опаковка на етапа на производство на фолио, тя е подсилена с нишки от различен материал(памучен конец, фибростъкло, метална тели други втвърдяващи материали). За разширяване на свойствата на уплътнителния материал, плетените опаковки се използват в комбинация с други материали, по-специално с експандирани флуоропласти, високоякостни влакна - кевлар (SVM). За подобряване на уплътняващите свойства на плетените опаковки, както и за намаляване на техния коефициент на триене и корозионна активност, се използва импрегниране. специални формулировкии лубриканти.
Коефициентът на странично налягане за плетена набивка NHF (Kb=0,5-0,6), в същото време тази набивка има доста висок коефициент на топлопроводимост, сравним с топлопроводимостта на метала на корпуса на помпата.
Разнообразие от технологии за производство на уплътнителни продукти от материала GRAFLEX дава възможност за сглобяване на комплекти опаковки с определени потребителски свойства.
Ориз. Фиг. 4. Схема на уплътнението на сальника на вала на работещи помпи с пълен комплект уплътнителни елементи GRAFLEX.
Дизайнът на уплътнителния механизъм на вала на помпата, проектиран преди това от производителите за традиционни уплътнителни материали (пълнежи от азбест, памук и синтетични материалиС различни видовеимпрегниране) е показано на фиг. 4а. Дълбочината на кутията за пълнене обикновено беше зададена на Голям бройпръстени (6-12 броя), което предопределя създаването на голяма аксиална сила по време на компресия на пълнежната кутия, води до увеличаване на неравномерния натиск върху вала в радиална посока и бързо износване на екстремните уплътнителни елементи. Върху крайните повърхности на долната кутия, пълнежната кутия и междинния фенерен пръстен се правят скоси под ъгъл α=15° спрямо крайната повърхност за подобряване на деформацията на набивката от външния диаметър до вала.
НПО УНИХИМТЕК, въз основа на тестове и експлоатационен опит на такива съединителни кутии, препоръчва използването на плетена опаковка от тип NGF като уплътнител, което гарантира дълготрайна и надеждна работа с минимално изтичане и увеличаване на експлоатационен живот на уплътнението 2-4 или повече пъти, в зависимост от условията на работа. В този случай дизайнът на сглобката на жлезата не се променя. В някои случаи, ако в средата има абразивни частици, е препоръчително външните пръстени да се монтират от опаковка с по-здрави резби, например от кевлар (SVM).
Ако използването на NGF опаковки не дава желаните резултати по отношение на експлоатационния живот, количеството на изтичане на работната среда или налягането на средата е достатъчно високо Рработа > 2 MPa, то това е преди всичко следствие от конструктивни недостатъци в уплътнение на съединителната кутия, което може да бъде компенсирано с помощта на специални пръстени от TRG GRAFLEX. Конфигурационната диаграма на такива възли е показана на фиг. 46. Тази конфигурация осигурява работата на уплътнението практически без течове (скоростта на изтичане е 1-5 капки в минута).
Ориз. 4б. Схема на уплътнение на сальника на вала на работещи помпи с пълен комплект уплътнителни елементи GRAFLEX.
Топлоотвеждащите пръстени осигуряват ефективно топлоотвеждане както поради висока топлопроводимост (в сравнение с уплътненията NGF и пръстените тип B CGN), така и поради високата ефективност на дроселиране на работното налягане и изравняване на радиалното налягане върху вала по дължината на кутията за пълнене, което води до равномерно и по-бавно износване на уплътнението.
За дроселиране на високо налягане на работната среда (2 ÷ 4 MPa), както и за работни среди със значително количество механични примеси, могат да се монтират няколко дроселиращи пръстена отстрани на работната среда. Фигура 4в показва една от възможните конфигурационни схеми за монтажа на жлеза при наличие на пръстен за фенер.
Ориз. 4в. Схема на уплътнение на сальника на вала на работещи помпи с пълен комплект уплътнителни елементи GRAFLEX.
За комплекта за пълнене на вала на помпата, чийто дизайн ще бъде разработен за предназначението на уплътнителни комплекти от TRG GRAFLEX, препоръчваме промените, показани на фиг.5. Крайните повърхности на притискащата втулка и междинния фенерен пръстен са направени перпендикулярно на оста на вала, без скосявания, което прави възможно осигуряването на повече равномерно разпределениерадиален натиск върху вала по дължината на пълнежната кутия. Вместо метални (стоманени, бронзови) subsalyshk пръстени, монтирани за средно дроселиране с минимални хлабини по протежение на вала δ = 0,2 ÷ 0,3 mm, е възможно да се монтира специален дроселиращ пръстен, изработен от Grflex TRG от тип KGN-S. Благодарение на еластичността на материала, ниския коефициент на триене, високата топлопроводимост и износоустойчивостта, дроселиращите пръстени поддържат минимални пролуки за дълго време, което определя изключително високата ефективност на дроселирането на налягането.
Фиг.5. Схема на конструкцията на сълзниковата кутия за използване на уплътнения тип GRAFLEX.
Резултатите от проучванията показват, че за осигуряване на надеждно уплътняване с уплътнителни материали GRAFLEX при налягане на работната среда до Рр ≤ 1 MPa е необходим комплект от 3-5 уплътнителни пръстена и при налягане на работната среда над Рр< 1МПа, целесообразно устанавливать комплект, состоящий из 6 колец.
Освен това, поради така наречения "самовъзстановяващ" ефект, който се състои в това, че при контакт с уплътняващи продукти, изработени от TRG, уплътняващата повърхност се покрива с тънък слойграфит, в резултат на което се запълват микрограпавините, повърхността става по-гладка и се получава по-нататъшен контакт на набивката с графизираната повърхност, в резултат на което коефициентът на триене намалява до k = 0,02-0,05 (сухо триене на TRG върху стомана k = 0,l-0,12). Всичко това спомага за намаляване на износването на опаковката, което води до надеждна херметичност и издръжливост на уплътнението с по-малък брой уплътнителни елементи.
От своя страна, намаляването на броя на уплътнителните елементи намалява размерипомпи, намаляване на разхода на метал на продукта, намаляване на разходите за уплътнителни материали.
| Повече ▼ по-голям ефектпостигнати по време на експлоатация при консуматорите. По-долу са резултатите от оценката на ефективността на използването на материали GRAFLEX в сравнение с традиционните опаковки.
Промяната в цената на материалите за годината, в случай на замяна на традиционните уплътнения на основата на азбест с GRAFLEX, може да се оцени чрез израза:
Където: C asb, C gr - цената съответно на азбестовите пломби и уплътненията GRAFLEX, rub/kg;
G asb, G gr - разход на материал за уплътнение на съединителната кутия от азбест и съответно GRAFLEX, кг;
η asb, η gr - срок на експлоатация на уплътнения от азбест и от материал GRAFLEX, съответно, седмици;
η година е броят на седмиците в една година.
Като пример помислете за промяната в разходите за материали за центробежна помпа, използвана за изпомпване на битум в рафинерията в Сизран, като вземете предвид реални условияуслуги за запечатване.
ΔS=(0,4 150/2,5-0,4 1350/26) 52=168 търкане/година
По този начин, въпреки значително по-високата цена на уплътненията GRAFLEX (С gr = 1350 рубли/кг и С asb = 150 рубли/кг), в резултат на това спестяването на материални разходи на година е 168 рубли на помпа. Но ефективността на новото поколение не свършва дотук.
Високата топлопроводимост на GRAFLEX и ниският коефициент на триене позволяват да се осигури работата на съединителните възли на центробежните помпи без изтичане на изпомпваната среда през уплътненията (в някои случаи има изтичане от 1-5 капки в минута предоставени). Използването на конвенционални опаковки изисква изтичане на малко количество изпомпвана среда (5-20 капки в минута (всъщност дори повече, ако средата не е токсична)), за да се предотврати нагряване на кутията за пълнене, което съответства на средни течове от около 0,5 -1,0 l/h (действителните течове могат да достигнат 3 l/h). За една година (7000-8000 часа) такива течове възлизат на 4 до 8 тона продукт. Икономическият ефект в този случай може да се оцени чрез израза:
където G пот - течове на изпомпваната течност, t/година;
C pr - цената на 1 тон изпомпана течност, rub / t.
Като се вземе предвид цената на петрола - 3000 рубли / тон, ефектът от намаляването на загубите в този случай ще бъде от 1,2 000 рубли / година до 24 000 рубли / година, което е почти 100 пъти по-високо от цената на материалите.
Намаляването на коефициента на триене при използване на уплътнения GRAFLEX с повече от три пъти ви позволява да намалите разходите за енергия за задвижването на помпата. Тези разходи покриват също няколко пъти разходите за закупуване на уплътнителния материал GRAFLEX. За съвременните центробежни помпи механичната ефективност, която отчита загубите на енергия от триене в уплътненията, лагерите и дисковото триене η m = 0,92-0,99. Разходът на енергията, използвана за преодоляване на силите на механичното триене в пълнежната кутия за традиционните опаковки е около α c =50% от общите механични загуби.
В този случай величината на намаляването на консумацията на енергия се счита за включена следния пример: за помпа със задвижваща мощност N e = 100 kW, смяната на традиционното уплътнение на сълзниковата кутия с уплътнение, изработено от материал GRAFLEX, ви позволява да намалите загубите на енергия в пълнителя с 2/3. Ако приемем, че първоначалната механична ефективност на помпата е η m = 0,95, тогава в резултат получаваме следните икономии на енергия:
ΔN E = 2/3 α c N E = 0,667 0,5 0,05 100 = 1,6675 kW
Изглеждаше незначителна сума. Въпреки това, с продължителността на работа на помпата τ=7000 часа годишно, можете да спестите енергия:
E g = 1,6675- 7000 = 11672,5 kW.
При цена на електроенергията от 50 копейки спестяванията ще бъдат S eq.e = 5836 рубли. За сравнение, комплект опаковка на кутия за пълнене за такава помпа струва средно около 500 рубли.
Още по-голям ефект се получава чрез увеличаване на експлоатационния живот на защитната втулка на вала. Експлоатационният опит показва, че при използване на традиционни опаковки, след една година експлоатация е необходима или жлеб, или най-често смяна на защитната втулка. Използването на уплътнения, изработени от материал GRAFLEX, дава възможност за поддържане на производителността на втулката за 3-4 години експлоатация. По този начин спестяванията от увеличаване на живота на защитната втулка с коефициент три ще бъдат:
От w.v. - цената на защитната втулка за тази помпа, руб.;
S p.p. - цена ремонтни работиза смяна на защитната втулка, разтрийте.
Общият икономически ефект ще бъде:
Възвръщаемостта на уплътнителните материали GRAFLEX, както показва експлоатационният опит, не надвишава два до три месеца.
НПО УНИХИМТЕК на базата на експериментални изследванияи пилотна експлоатация, за работа на помпи са разработени и внедрени уплътнителни комплекти от материали GRAFLEX, които гарантират намаляване на изтичането на течности и увеличаване на експлоатационния живот. Въз основа на резултатите от теоретични и експериментални проучвания са разработени препоръки за внасяне на промени в конструкцията на пълнежната кутия на помпата при използване на уплътнителни материали GRAFLEX, които намаляват средните течове, намаляват износването на втулката на вала, разхода на уплътнителен материал и намаляване на оперативните разходи.
ЛИТЕРАТУРА
- Domashnee A.D., Khmelniker V.L. Уплътнения за сальники за арматура на АЕЦ. - М.: Атомшдат, 1980, 112с.
- Кришнек Р. Уплътнителни системи на базата на графит. Химическа и нефтена и газова техника, бр.8, 2000г.
- Ворохов А.М., Гашнин А.С., Додонов Н.Т. Влакнести и комбинирани уплътнения на сандъче. М.: Машиностроение, 1966, 312 с.
- Илин Е.Т. Руски високопроизводителни уплътнения GRAFLEX - Материали от индустриалната среща на главните механици на нефтени рафинерии и нефтохимически предприятия в Русия и ОНД. Кириши, 2002, с. 2 59-266.
AT промишлено производствопо време на работа на различни тръбопроводи неизбежно възникват загуби на изпомпвани течности. За предотвратяване на тези случаи служат множество уплътнения, един от които ще бъде разгледан подробно в тази статия.
Уплътнение на пълнителя на помпата
Съвременното помпено оборудване е завършено голямо количествоелементи. В същото време спецификата на работата изисква да се обърне повишено внимание на нормалното и непрекъснато функциониране на продуктите като цяло. Благодарение на простотата на своя дизайн и лекотата на използване, уплътненията на сапунката на помпата се използват много по-често от другите уплътнителни устройства.
Оперативни изисквания
Работното колело на всички видове помпено оборудване работи благодарение на двигателя. Най-често е електрически. Чрез механичен съединител енергията се предава от вала на двигателя към работното колело, което го привежда в движение. Самият вал се простира извън корпуса на оборудването, което прави черупката непропусклива. Следователно загубата на работна течност е неизбежна.
Ако се използва, може да се избегне изтичане на изпомпваната течност. Използват се следните технологии:
Опаковано (жлезено) уплътнение. Това е пръстен от влакнест материал.
Маншет. За този печат, еластични материаликоито могат да бъдат подсилени за увеличаване на твърдостта. Използва се за монтаж в помпено оборудване с ниска скорост на вала.
Край. Състои се от два пръстена, плътно разположени един до друг на вала. Единият от тях се върти заедно с вала, докато другият остава напълно неподвижен.
прорезен. Второто име е лабиринт. Считан за най-надежден модерен външен видуплътнения. Представен под формата на пръстен от мека сплав. Използва се в многостепенни помпи, където използването на други технологии може значително да повлияе на ефективността.
Освен това има устройства, които не изискват уплътнения, като помпи с магнитно задвижване с мокър ротор.
Описание на уплътненията на жлезите
За осигуряване на херметичност най-често се използват прорезни материали потопяеми помпи. Те нямат специални изисквания за изтичане на течности. Тук дълголетието играе голяма роля.
Уплътнението на уплътненията на помпата се появи почти едновременно с оборудването за изпомпване на течности. Това са своеобразни пръстени, изработени от влакнест материал, които се намират в основата на сандъчето, откъдето идва и името им. Опаковката трябва да се намокри от течността, транспортирана през тръбопроводите. Това е необходимо за охлаждане и смазване на кутията за пълнене. Самото намокряне е изпълнено със загуба на течност. Един час работа на помпата предполага загуба на 1-15 литра вода. Ако опаковката не е намокрена, тогава материалът ще загуби своята полезност и бързо ще „изгори“.
Уплътненията трябва да се обслужват редовно. В същото време компресорите и помпите не могат да се разглобяват, което е едно от съществените предимства на уплътненията. Самообслужването е периодично „издърпване“ на маншета.
Типични вариации на уплътненията за помпено оборудване
Съвременният пазар предлага различни уплътнения за помпи; типичните маслени уплътнения са представени от два основни типа:
Подсилена опаковка с един ръб. Основната цел е да се предотврати загубата на изпомпваната течност.
Маншети, подсилени с прашник и един ръб. Използва се за защита на самата връзка от прах и мръсотия. Също така не позволявайте на течността да напусне транспортната система.
Ако го погледнем, можем да различим маслени уплътнения:
с формован ръб;
с обработен ръб.
В зависимост от вида на използваната гума има такива маншети:
На базата на нитрилен бутадиен каучук. Продуктите се произвеждат от 1, 2 и 3 клас каучук. Сравнително висок праг отрицателна температураработа (съответно -30, -45 и -60 °C).
На базата на флуорокаучук. Суровината е каучук от групи 1 и 2. При изпомпване на минерално или редукторно масло те издържат на температури до 170 ° C.
Изработен от силиконова гума. При производството на каучук се използва изключително 1 група. В крайна сметка Работна температураопаковки -55 °C.
Като правило модерните маншети идват с пружини. Подходящи са за уплътняване на валове с различни диаметри.
Пружината може да бъде доставена отделно от пълнителя, ако е предназначена за работа с вал до 20 мм или повече от 120 мм.
експлоатационни свойства, за кои помпи е по-добре да се използват
По правило маншетите се различават от другите уплътнения по своята гъвкавост и пластичност. Високата устойчивост на износване също е значително предимство на продуктите. Лек удар върху вала разширява сегмента на приложение.
Характеристиките на работата директно зависят от структурата на уплътнителя и състава, който е бил използван в производството. В зависимост от тъкането се различават диагонални (преходни и комбинирани) жлези и еднослойни (което означава структурата на сърцевината). Съставът на маншетите е:
азбест и неазбестови;
сухи и импрегнирани (като импрегниране се използват смеси от мазнини, графит и лепило);
подсилени и неармирани.
Кутиите за пълнене се използват за запечатване на центробежната връзка, а опаковката може да се използва и в бутално оборудване за изпомпване на течни среди. Когато инсталирате продукта, не забравяйте, че помпите с уплътнения на съединителната кутия ще пропускат определено количество течност, споменато по-горе.
Графитно-керамични уплътнения
Това е един от видовете маншети за помпено оборудване. Използването на този тип уплътнение напълно елиминира навлизането на работна течност в двигателя на оборудването. Къде се използват графитно-керамични уплътнения? Няма много водни помпи, които пасват. По правило сегментът на приложение е ограничен само до повърхностни механизми.
Срокът на експлоатация може да достигне 10 години. В същото време си струва да се придържате към него правилна работа помпена станция. Основните изисквания, поставени по време на работа на оборудването:
Без "сухо бягане". Строго е забранено да държите помпата в режим "включено", ако в системата няма течност.
Най-добре е да се изпомпва най-пречистената субстанция. Наличието на примеси съкращава живота на маншета.
Не забравяйте да се придържате към температурния режим.
Предимства на пълнителите за помпи с водно уплътнение
Маншетът на оборудването за изпомпване на вода изглежда като плетена връзка с квадратно сечение. Азбестовата (памучна или ликова) нишка може да има включвания от медна или месингова тел. Помпите с водно уплътнение имат сърцевина от олово. Размер на лентата 5*0,5. Вместо това може да се използва тъкане на 4 оловни жици.
Използват се водни уплътнения, обикновено от смукателната страна. Но е възможно да ги използвате от противоположната страна. Размерът на опаковката е пряко свързан с диаметъра на вала. Максималният брой уплътнителни пръстени е 5.
Как да изберем семеринг
Изборът на уплътнения се извършва според редица характеристики. Без съмнение най-важният въпрос е надеждността. Сред другите важни критерии се взема предвид цената. Допълнителни опциисе вземат предвид при избора на устройства:
брой работни часове;
загуба на течности;
най-доброто преди среща;
разходи, свързани с ремонта.
Освен това изборът на уплътнения за помпи се извършва, като се вземат предвид стандартните размери. Те включват външния и вътрешния диаметър, височината и дебелината на основата.
Какво казват потребителите
Мнозина вече са се сблъскали с инсталирането на маслено уплътнение за едностепенна помпа. Често се отбелязва гъвкавостта на пълнежа. Използването на уплътнения не се ограничава до високоскоростни валове.
Отбелязва се, че уплътнението на съединителната кутия на помпите със смазка на силиконова основа показва по-голяма термична стабилност.
Вариациите с високо съдържание на въглерод значително намаляват коефициента на разширение с повишаване на температурата на изпомпваната течност. А арамидните влакна със специално PTFE импрегниране позволяват на кутията за пълнене да работи в агресивна среда върху химическо производство, CHP и хартиената промишленост.
Уплътненията са предназначени за уплътняване на отвори, през които преминават или се поставят вътре движещи се части на механизмите. Нарушаването на херметичността на всяко правилно сглобено уплътнение на сала се причинява главно от загуба на еластичност на уплътнителните пръстени (маншети) и едностранно износване на триещите се повърхности на частите. При загуба на еластичност, силата, с която пръстенът притиска шийката на вала или се притиска вътрешна повърхностцилиндър, а при едностранно износване се изкривява цилиндричната форма на триещите се повърхности.
Контрол на състоянието и ремонт на части. Състоянието на уплътнителните пръстени и маншетите се проверява чрез рутинна проверка. Във всички случаи при демонтаж на сальниковите уплътнения се сменят филцовите пръстени, опаковката от памук, азбест или конопен шнур или сноп, сгънат от тези материали, независимо от състоянието им. На смяна подлежат и гумени пръстени и маншети и самозатягащи се накрайници, монтирани на труднодостъпни места на механизми. В други случаи гумените части и самозаключващите се уплътнения се сменят само при загуба на еластичност, при наличие на разкъсвания и дефекти по триещите се повърхности, разслояване или омекотяване на гумата.
Сглобяване. Всяко уплътнение на кутията за пълнене работи нормално само ако кутията за пълнене притиска шийката на вала или е притисната към повърхността на цилиндъра равномерно и със същата сила. За да направите това, е необходимо осите на вала, отворите на частта за пълнежната кутия и самата кутия за пълнене да са коаксиални. Освен това изтичането на гърлото на вала, въртящо се в сайлера, трябва да бъде минимално (не повече от 0,05 mm), а триещите се повърхности на вала или цилиндъра трябва да имат гладка повърхност без ръбове.
Уплътнения с филцови пръстени. Материалът и размерите на пръстените на всяка връзка трябва да отговарят на изискванията на чертежа. За придаване на еластичност и намаляване на износването на пръстените се препоръчва накисването им за 5.10 минути със специални съединения, загряти до 120.130 "C. Смес от 75% технически глицерин, 20% натриев сапун и 5% люспест графит може да се използват като такива съединения.или 90% рициново масло, 5% натриев сапун и 5% люспест графит.Пръстените, монтирани в капачките, трябва да прилягат плътно към подрязването на капачката.Трещата повърхност на пръстените трябва да е чиста и равна, без удебеления, вдлъбнатини и подрязвания, пръстенът трябва да е стегнат и дори да притиска подвижна част.
Уплътнения с пръстени за пълнене. Опаковката на кутията за пълнене (като кутия за пълнене на водна помпа) обикновено се състои от отделни пръстени с наклонен разрез. Ставите на съседни пръстени се изместват на 120 или 180°. За ускоряване на процеса на пълнене е желателно да има дорници, с леки удари, на които халките са добре уплътнени. Трябва да се внимава при окончателното затягане на гайките на дюзата. Неравномерното неправилно затягане на гайките често води до нагряване и прекомерно износване на триещите се части на частите.
Уплътнения със самозаключващи се накрайници, гумени пръстени и маншети. В свободно състояние пружината на самозатягащата се жлеза трябва леко да компресира маншета; силата на натиск се регулира чрез промяна на дължината на пружината. Твърде голяма сила, въпреки че увеличава херметичността на връзката, обаче може да причини прегряване и принудително износване на частите. За да се улесни монтажа на гумените части, техните триещи повърхности се смазват с тънък слой грес. За да се постигне по-добро уплътнение, контактните повърхности на гнездото на корпуса и самозатягащата се муфа са покрити с лепило GEN-150V, оловно бяло, уплътнител, шеллак или лепило карбинол.
Основната част от производството на формовани гумени изделия се пада на уплътнителни устройства, от които зависи производителността и надеждността на възлите и механизмите, уплътняването и уплътняването на фуги, шевове и всички видове връзки. Задачата на уплътненията е да предотвратяват или намаляват изтичането на течност или газ в съединенията на машинни части, тръбопроводи и други системи. Консолидациите се случват подвижни, неподвижни, контактни и прорезни. Те могат да имат сложен профил на напречното сечение, за да осигурят херметичност и необходимата скорост на механизма, да намалят нагряването на работния флуид в системата, да предпазят от проникване на чужди вещества в техническо устройствои предотвратяване на външно изтичане на работния флуид. Зависи от химичен състави физични свойствагумените уплътнения могат успешно да работят в голямо разнообразие от условия и се използват във всички индустрии. Подвижните контактни уплътнения включват О-пръстени, яки и други видове специални уплътнения. Например, пръстеновидните уплътнения, произведени в съответствие с GOST 9833-73, са проектирани за надеждна работа в хидравлични системи при налягания до 32 MPa и във фиксирани съединения до 50 MPa. С повече високо наляганеработна течност в системата, се препоръчва използването на гумени маншети.
Видове маншети
Осигурява стегнатост в хидравлични устройствабрадва за машини и възли (GOST 6969–54, TU 38-1051725-86)
Примери за обозначение: Маншет 80x100 GOST 6969-54 - маншет за запечатване на цилиндър с диаметър 100 mm, прът с диаметър 80 mm
Осигурява уплътняване на пролуката между цилиндъра и буталото при налягане от 0,1 до 50 MPa с възвратно-постъпателна скорост не повече от 0,5 m/s при температура от -60C до +200C (GOST 14896-84, GOST 6969-54 ). В зависимост от конструкцията и стойността на действащото налягане се изработват три вида
Примери за обозначение: Маншет 1-20x12-4 GOST 14896-84 - маншет тип 1 за запечатване на цилиндър с диаметър 20 mm, прът с диаметър 12 mm от група 4 гума
Служи за уплътняване на пръти и цилиндри на хидравлични устройства, работещи в минерални масла, масла, пресни и морска вода, водни емулсии при налягания до 63 MPa при температури от -50 до +120°C с възвратно-постъпателна скорост до 3 m/s. Тези маншети са монтирани в комплект с метална опора и притискащи пръстени (GOST 22704-77)
Примери за обозначение: Поддържащ пръстен KO 70x95-2 GOST 22704-пръстен с вътрешен диаметър 70 mm, външен диаметър 95 mm, изработен от каучук група 2
Примери за обозначение: Шеврон маншет M 70x95-2 GOST 22704 - маншет с вътрешен диаметър 70 mm, външен диаметър 95 mm от каучукова група 2
Примери за обозначение: Пръстен за налягане KN 70x95-2 GOST 22704-пръстен с вътрешен диаметър 70 mm, външен диаметър 95 mm, изработен от каучук група 2
Предназначен за уплътняване на цилиндри и пръти на пневматични устройства, работещи при налягане от 0,005 до 1 MPa при температура от -65 до +150 °C със скорост на възвратно-постъпателно движение до 1 m/s (GOST 6678-72). Има два вида - тип 1 (за уплътнение на цилиндъра) и тип 2 (за уплътнение на прът)
Примери за обозначение: Уплътнителен маншет 1-025-3 GOST 6678-72 - маншет тип 1 за цилиндър с диаметър 25 мм от каучук група 3
Примери за обозначение: Уплътнителен маншет 2-010-1 GOST 6678-72 - маншет тип 2 за прът с диаметър 10 мм от каучукова група 1
За уплътняване на въртящи се валоверабота при по-тежки условия на работа в минерално масло, вода, дизелово гориво, при свръхналягане до 0,05 MPa, температури от -60 до +170 (в зависимост от каучуковата група) и скорости на въртене до 40 m/s се използват подсилени гумени маншети (GOST 8752-79). Такива маншети се наричат още жлези. Тези маншети са подсилени с метален пръстен и кръгла пружина. Металът на пръстена е в гумен слой, не реагира с агресивна среда и укрепва общ дизайн, а пружината притиска работния ръб на маншета към вала. Могат да бъдат направени някои видове маншети флуорокаучуки силиконова гума. Това позволява използването на подсилени маншети в широк диапазон от работни параметри при изключителни натоварвания под въздействието на най-агресивните среди.
Правят се два вида:
аз — едноръбови (за предотвратяване на изтичане на запечатаната среда);
II — единична устна с обувка (за предотвратяване на изтичане на уплътняващата среда и за защита от проникване на прах)
Изработват се в два варианта: 1. с обработен ръб (разрез); 2. с формован работен ръб.
Примери за обозначение: Маншет 2.1-60*80-4 GOST 8752–79 - маншет тип 2, версия 1, за вал с диаметър 60 mm с външен диаметър 80 mm, изработен от каучукова група 4
бележки:
- Буквата "C" означава, че пригодността на каучук за уплътняване на тази група медии се определя по споразумение между производителя и клиента;
- Знакът "-" означава, че еластомерът не е приложим за уплътняване в посочената група среди.
Всички Kharprompolimer LLC се произвеждат в съответствие с GOST 8752-79.
Уплътненията са устройства за предотвратяване или намаляване на изтичането на течност през пролуките между частите.
Уплътненията на помпата могат да бъдат разделени на две групи: уплътнения на края на вала (външни) и вътрешни уплътнения на степента. Крайните уплътнения са предназначени да предотвратяват изтичане на изпомпваната течност от помпата и навлизане на въздух в помпата по време на нейната работа с отрицателно налягане на входа (пълнител, крайни уплътнения). Вътрешните уплътнения са предназначени да намалят изпомпваната течност между стъпалата вътре в корпуса на помпата при многостепенните помпи или между корпуса и въртящото се работно колело при едностепенните помпи (прорезни, лабиринтни).
Уплътненията (сальник) са уплътнение на въртящ се вал в точките на изхода му от фиксиран корпус, изработен от мека еластична опаковка. Използването на маслени уплътнения като уплътнителен елемент е едно от най-старите начинизапечатване на подвижната става.
В уплътненията на пълнителя без принудително компресиране жлезна опаковкасе вписват в канали на неподвижните и подвижните части на ставите. Използва се за уплътняване на бутални лагери при ниски скорости на движение и ниско свръхналягане.
Уплътненията на сальника с принудителна компресия са изградени по схема, при която уплътнението се постига чрез притискане на уплътнението към вала в резултат на сила на натиск.
В повечето конструкции на уплътненията на сальника, притискателните втулки и долните кутии са направени с контактна равнина, наклонена към оста на вала, което прави възможно увеличаването на радиалното налягане на уплътняващото налягане върху вала. Въпреки това, прекомерното увеличаване на ъгъла на наклон води до появата на големи напрежения в близост до притискащата втулка, което води до повишено износване на пръстените, които са най-близо до втулката.
Подаването на въздух в работната кухина на помпата се изключва чрез използването на уплътнително устройство с хидравлично уплътнение. Течност под свръхналяганесе захранва към междинен пръстен 2. Може да се захранва от офлайн източникили взети от помпата. По този начин се създава хидравлично уплътнение, което не само предотвратява проникването на външен въздух в помпата, но и предотвратява изтичането на изпомпваната течност от помпата. Хидравличните уплътнителни уплътнения осигуряват добро смазване на уплътнението, намалявайки загубите от триене в монтажа и осигурявайки разсейване на топлината.
Всички уплътнителни устройства, разгледани по-горе, извършват компресията на меката опаковка от страна, противоположна на действието на налягането на изпомпваната течност, т.е. създават максимално радиално налягане на уплътнителния елемент върху вала, където налягането на изпомпваната течност е минимално.
Фигура 9 - Спълнятелна кутия с компресия на опаковката на изпомпваната течност: 1 - вътрешна втулка; 2 - уплътнителен елемент; 3 - лагер; 4 - външна втулка; 5 - вал
Най-добрите условия за уплътняване могат да бъдат постигнати чрез осигуряване на максимално радиално налягане на елемента върху вала, където налягането на изпомпваната течност е максимално. Например уплътнителни устройства, в които опаковката се компресира от налягането на изпомпваната течност. Тъй като площта на маншона под налягане от страната на течността е по-голяма от площта от страната на компресия на опаковката, се генерира напрежение, което надвишава налягането на изпомпваната среда. Такова уплътнение се нарича диференциално.
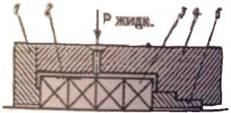
Фигура 10 - Уплътнение на кутията за пълнене с радиално предварително натоварване: 1 - капак; 2 - еластична камера; 3 - уплътнителен елемент; 4 - тяло; 5 - грундбукса.
Равномерно разпределение на уплътняващото налягане върху вала може да се постигне чрез радиална компресия на уплътнението. В уплътнението с радиална компресия на набивката между тялото 4 и уплътняващата набивка 3 има еластична камера 2, в която се подава течност под свръхналягане през отвора. Налягането на течността през еластичната камера се прехвърля равномерно към уплътнителния елемент, запечатвайки връзката.
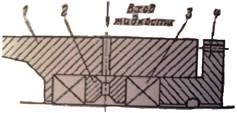
Фигура 11 - Уплътнение на пълнежа с хидравлично уплътнение: 1 - корпус; 2 - междинен пръстен; 3 - уплътнение на жлеза; 4 - маншон за налягане
За да се увеличи издръжливостта на меката опаковка, нейните отделни пръстени са ограничени от шайби, които са изработени от метал или пластмаса. Печатът, така да се каже, е разделен на отделни камери. Уплътнителните пръстени са защитени от преждевременно изтичане на пълнителя, изсъхване и бързо износване, което гарантира повече дългосроченуслуги за запечатване.
Основният елемент на уплътнението на кутията за пълнене е еластична опаковка. Опаковъчният материал трябва да има достатъчно механична силаи еластичност, висока устойчивост на износване, непропускливост и добри антифрикционни свойства. Според GOST 5152-84 има три вида опаковки: плетени, валцувани и пръстеновидни.
Плетените опаковки се подразделят на опаковки за плетене и плетене. За пълнеж се използват памук, коноп, азбест, талк и синтетични конци. В CNS помпи за изпомпване на вода в нефтопомпени образувания се използва опаковка AG - изтъкана от азбестова нишка, импрегнирана с маслен състав с нанасяне на графитен прах, APR-31 - тъкана набивка от азбестова нишка, подсилена с месингова тел и импрегнирана с мастен състав. Срокът на експлоатация на такива опаковки е около 700 часа. Други се прилагат съвременни материалис удължен експлоатационен живот. Графитната опаковка NG-L е изработена от термично експандиран графит, подсилен с лавсанова нишка. Срок на експлоатация до 10000 часа.